An Overview Of High Volume Injection Molding From Plastic Injection Molding Companies Near Me
An Overview Of High Volume Injection Molding From Plastic Injection Molding Companies Near Me
Explore the benefits, processes, and applications of high volume injection molding, a method used for efficient and cost-effective manufacturing. Discover how this process can help businesses produce high-quality plastic parts.
In the competitive manufacturing landscape, efficiency and cost-effectiveness play crucial roles in determining the success of businesses. One manufacturing technique that addresses these needs is high volume injection molding. This blog post will explore the world of high volume injection molding, its definition, advantages, process, key considerations, and real-life case studies. By the end, you’ll gain a comprehensive understanding of this manufacturing method and its potential applications.
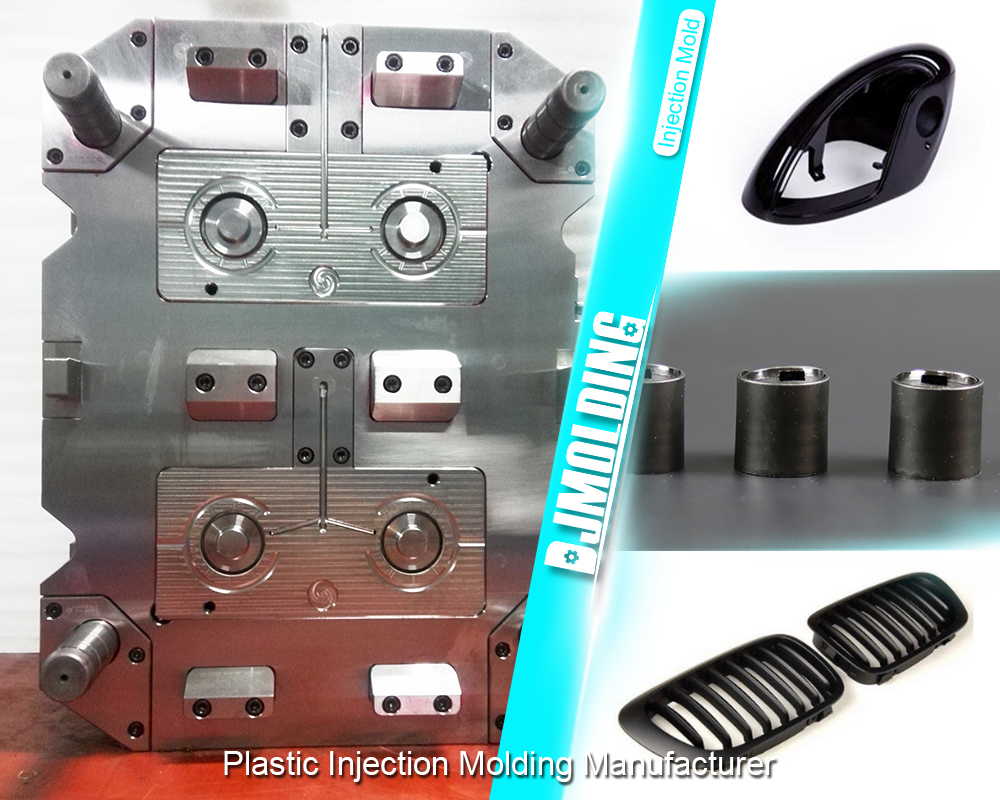
What is High Volume Injection Molding?
Definition and Overview:
High volume injection molding is a manufacturing process that involves injecting molten plastic into a mold cavity at high pressure to create complex and precise plastic parts. It is particularly suitable for large-scale production due to its ability to produce high quantities of identical parts quickly.
Advantages of High Volume Injection Molding
High volume injection molding offers several advantages, including:
- Cost Efficiency: Using mass production techniques significantly decreases the cost per part, making it economically viable for large production runs.
- Scalability: The process can be easily scaled up or down to meet changing production demands.
- Consistent and High-Quality Output: Precise molds and automated processes ensure consistent quality and dimensional accuracy in each part produced.
- Time and Resource Savings: High volume injection molding reduces production cycle times, minimizes material waste, and requires less labor than alternative manufacturing methods.
- Versatile Applications: It finds applications across various industries, from automotive and electronics to consumer goods and medical devices.
Key Factors for Successful Implementation
Businesses must consider factors such as: to ensure the successful implementation of high volume injection molding.
- Material Selection: Choosing the suitable plastic material based on desired properties, part requirements, and compatibility with the injection molding process.
- Mold Design and Preparation: Designing molds that withstand high pressures and temperatures while ensuring optimal part quality and manufacturability.
- Injection Molding Machine Setup: Proper machine setup, including temperature, anxiety, and cycle time optimization, to achieve consistent and efficient production.
- Injection Molding Process Steps: Understanding the sequence of steps involved, from plastic material melting to part ejection, to ensure smooth and accurate output.
The Process of High Volume Injection Molding:
Mold Design and Preparation
The mold design phase involves creating a precise mold cavity based on part specifications and considering material flow, cooling, and ejection factors. Manufacturers typically use steel or aluminum alloys to make molds for durability.
Material Selection
Appropriate plastic material is critical to achieving desired part characteristics, such as strength, flexibility, heat resistance, or appearance. Factors like cost, availability, and environmental considerations also come into play.
Injection Molding Machine Setup
Operators define the injection molding parameters during machine setup, including temperature, pressure, and injection speed. These settings ensure the molten plastic is injected into the mold cavity accurately and efficiently.
Injection Molding Process Steps
The injection molding process consists of several steps, including clamping the mold, injecting the molten plastic, cooling and solidification, mold opening, and part ejection. Each step requires precision and synchronization to produce high-quality parts.
Benefits and Applications of High Volume Injection Molding:
Cost Efficiency and Scalability
High volume injection molding enables businesses to achieve significant cost savings through economies of scale, making it an attractive option for large production runs.
Consistent and High-Quality Output
With automated processes and stringent quality control measures, high volume injection molding ensures consistent and high-quality output. Each part produced maintains dimensional accuracy and meets the required specifications, leading to customer satisfaction and reduced rework or rejection rates.
Time and Resource Savings
By utilizing high volume injection molding, businesses can optimize production cycle times and reduce overall manufacturing lead times. The automated nature of the process minimizes the need for manual intervention, saving labor costs. Additionally, the process allows for efficient material usage, minimizing material waste.
Versatile Applications in Various Industries
High volume injection molding finds applications across a wide range of industries. Automotive manufacturers use this process to produce bumpers, dashboards, and interior trims. The electronics industry utilizes it to create enclosures, connectors, and housings. This manufacturing method can also benefit consumer goods, including toys, packaging, and household appliances. Furthermore, medical device manufacturers rely on high volume injection molding to produce components like syringes, surgical instruments, and device casings.
Key Considerations for High Volume Injection Molding:
Material Selection and Compatibility
Choosing the suitable plastic material is crucial for the success of high volume injection molding. When considering microelectronics adhesives, it is vital to consider factors such as material properties, compatibility with the molding process, and cost. Material testing and ensuring compatibility between the material and mold are essential steps in achieving desired part quality.
Tooling and Mold Design Optimization
Optimizing tooling and mold design is essential to maximize production efficiency and part quality. Gate design, cooling channels, and parting line placement require careful consideration. Mold maintenance and regular inspection are crucial for prolonging the mold’s lifespan and ensuring consistent production.
Quality Control and Inspection
Implementing rigorous quality control measures throughout the production process is crucial. Regular inspections, dimensional checks, and functional testing help identify any defects or variations in parts. Implementing statistical process control techniques can aid in monitoring and improving process capability.
Sustainability and Environmental Impact
As sustainability becomes a key consideration for businesses, high volume injection molding offers certain advantages. Minimizing material waste through efficient design and optimized production processes reduces environmental impact. Additionally, selecting eco-friendly materials and implementing recycling programs contribute to sustainable manufacturing practices.
Case Studies and Success Stories
Highlighting real-life examples of successful high volume injection molding projects can demonstrate the effectiveness of this manufacturing method. Case studies can showcase how businesses have achieved cost savings, improved production efficiency, and delivered high-quality products using high volume injection molding.
Future Trends and Innovations in High Volume Injection Molding
Advances in Materials and Additives
Ongoing research and development in plastic materials and additives are expanding the capabilities of high volume injection molding. Materials with improved properties, such as enhanced strength or heat resistance, are being introduced, broadening the range of applications for this manufacturing method.
Automation and Robotics Integration
Automation and robotics are revolutionizing the high volume injection molding process. Automated systems can handle tasks such as mold loading, part ejection, and quality inspection, leading to increased production efficiency, reduced labor costs, and improved overall productivity.
Industry 4.0 and Smart Manufacturing
Integrating digital technologies and data analytics in high volume injection molding drives the industry toward intelligent manufacturing. Real-time monitoring of production parameters, predictive maintenance, and process optimization through data analysis contribute to improved efficiency, reduced downtime, and enhanced product quality.
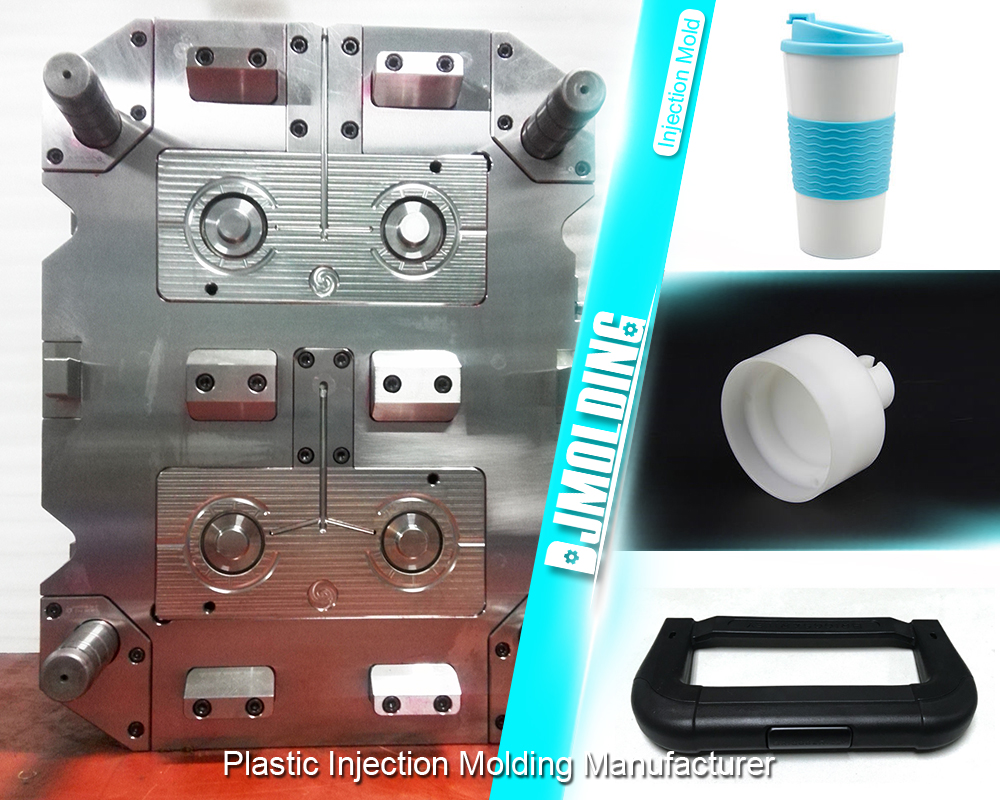
Conclusion
High volume injection molding offers businesses an efficient and cost-effective manufacturing solution for producing large quantities of high-quality plastic parts. The advantages of this process, such as cost efficiency, consistent output, time savings, and versatile applications, make it a valuable option across various industries. Businesses can fully harness the potential of high volume injection molding by considering key factors, optimizing tooling and design, implementing quality control measures, and staying abreast of future trends and innovations. As manufacturing requirements evolve and customer demands increase, this technique provides a competitive edge in efficiency, quality, and scalability.
For more about an overview of high volume injection molding from plastic injection molding companies near me,you can pay a visit to Djmolding at https://www.djmolding.com/high-volume-injection-molding/ for more info.