An engineer’s guide to low volume injection molding from low volume injection molding manufacturers
An engineer’s guide to low volume injection molding from low volume injection molding manufacturers
Low-volume injection molding is a quick and effective method for creating plastic parts in quantities ranging from 100 to 10,000 units. This process is often utilized to manufacture prototypes of established part designs that need actual testing.
Additionally, low-volume injection molding serves as a link between initial prototyping and the large-scale production of hundreds of thousands of parts, making sure there is a smooth transition in the production process.
The best companies use steel molds instead of aluminum for low-volume injection molding. These soft or semi-hardened steel tools are more affordable compared to the hardened steel molds used in high-volume molding. Furthermore, these steel molds can be prepared in under two weeks, reducing lead times for shorter injection molding processes.
An important aspect of low-volume steel molds is their ability to produce intricate parts with excellent injection molding quality. Unlike low-volume rapid injection molding using 3D-printed molds, steel molds have a longer lifespan and can create parts with precise tolerances and intricate details.
This article explores the process of low-volume injection molding and discusses its suitability for prototyping or production purposes. It also provides insight into designing parts specifically for low-volume injection molding, details the manufacturing of injection molds, and delves into other related topics.
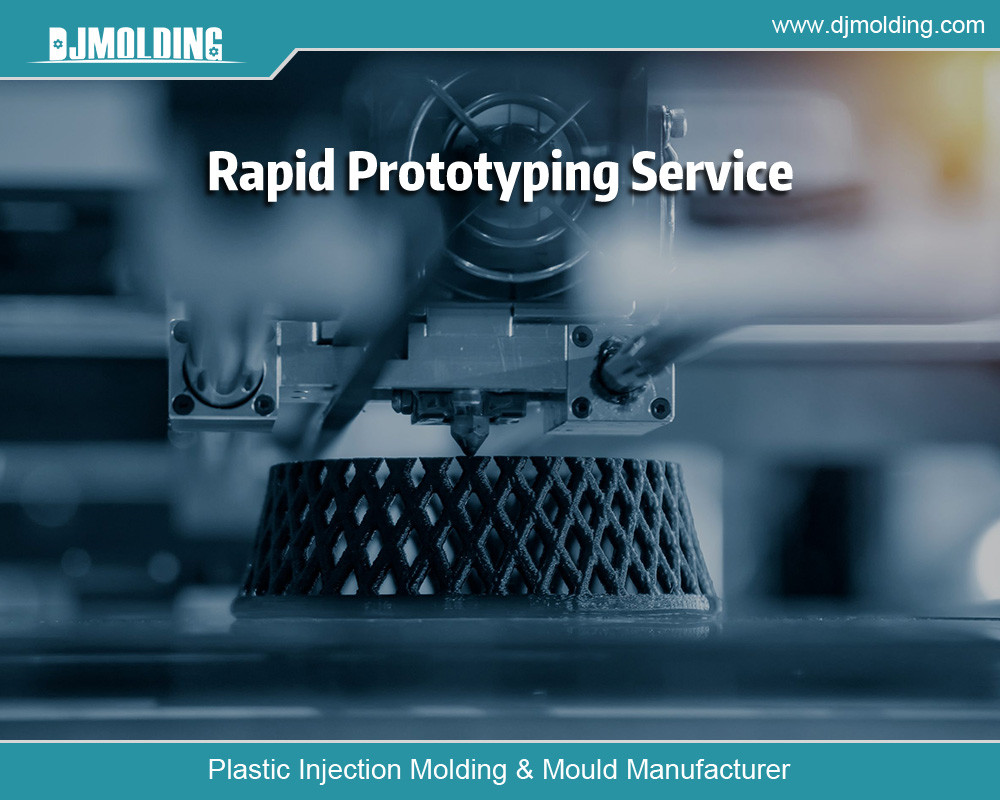
Explaining Low-Volume Injection Molding
The process of low-volume plastic injection molding starts with pouring plastic pellets or granules into a hopper connected to a smaller injection molding machine. These machines are designed for quicker changeovers due to their smaller size and are equipped to handle smaller production runs efficiently.
Once the plastic materials enter the hopper, they are dispensed into a barrel where they are heated and transformed into a liquid state. A large reciprocating screw guides the molten material towards the barrel’s edge while increasing the injection molding pressure and temperature.
Just like in high-volume injection molding, maintaining the correct temperature and pressure is crucial to prevent defects in the injection molding process.
Mold Filling
As pressure and material accumulate in the barrel, a ram moves the screw toward the injection mold, pushing out a “shot” of plastic into channels called “runners” within the mold. The molten plastic flows from the runners through gates and into the mold cavity, where it solidifies.
How To Eject Parts
Upon completion of the injection molding process, the mold is opened, and the part is ejected using ejector pins connected to the mold core. Sometimes, additional mechanisms like hand loads, sliders, or lifters are required for part ejection. Sliders aid in releasing external undercuts on a part’s surface, while lifters help with internal undercuts.
Hand loads are a more economical option compared to sliders or lifters, although they contribute to injection molding expenses. Each hand load needs to be removed and then reinstated in the tool for the following molding cycle.
Despite the added costs, hand loads are viable for low-volume injection molding projects, especially for prototyping or production purposes. These ejection mechanisms can also accommodate intricate part designs such as threads.
Processing The Parts After Ejection
When the injection molding is complete, other processing steps may be necessary. For instance, excess plastic material might seep out between the mold’s core and cavity at the parting line. While some flash is normal, excessive flash must be removed to maintain part surface quality. Skilled injection molding operators can minimize flash occurrence.
Clamping pressure plays a crucial role in keeping the injection mold closed securely. Inadequate pressure can lead to premature mold opening and the formation of flash. However, it is equally important for the injection mold to withstand the clamping pressure exerted by the molding machine. Typically, the smaller equipment used in low-volume injection molding operates at a lower clamping pressure compared to high-volume machines.
When is Low Volume Injection Molding Appropriate?
Low-volume injection molding is ideal for both prototyping and production purposes, making it a valuable option for those new to the field or with established designs. It is essential to understand the synergy between 3D printing and plastic injection molding in order to determine the appropriate use of these complementary techniques.
For projects in their initial stages requiring fewer than 100 parts, 3D printing is a suitable choice. Nevertheless, as design maturity, part quantities, and testing needs evolve, transitioning from 3D printing to prototype injection molding becomes a prudent decision.
Various stages of design maturity, including proof-of-concept, works-like, looks-like prototypes, are defining factors in the choice between these manufacturing methods.
Occasionally, early-stage prototypes are unsuitable for injection molding due to low quantities or evolving part designs. Rapid prototyping may result in significant changes, making it challenging to justify the expense of tooling when spread across only a few parts. Besides, substantial design alterations can lead to extensive tooling modifications, increasing injection molding costs and project timelines.
Prototypes with well-developed designs usually necessitate fewer tooling adjustments. Designers may require pre-production prototypes in quantities that warrant the investment in an injection mold. Moreover, depending on project specifics and testing needs, injected molded prototypes may be essential for conducting initial article inspections.
Short-Run Productions
In low-volume production, an injection molder can detect and address tooling-related issues that may necessitate part design modifications. They can refine machine settings and process parameters before committing to pricier high-volume injection molds.
While modeling software can predict possible problems, low-volume injection molding provides tangible parts for assessment in real-world applications.
Some Design Rules for Injection Molding
The choice of injection molding material dictates the acceptable range of wall thicknesses for your part design. Steer clear of extremely thick walls as they increase material usage and prolong the injection molding cycle, adding to project expenses. On the other hand, overly thin walls can trap air and lead to short shots, resulting in incomplete parts.
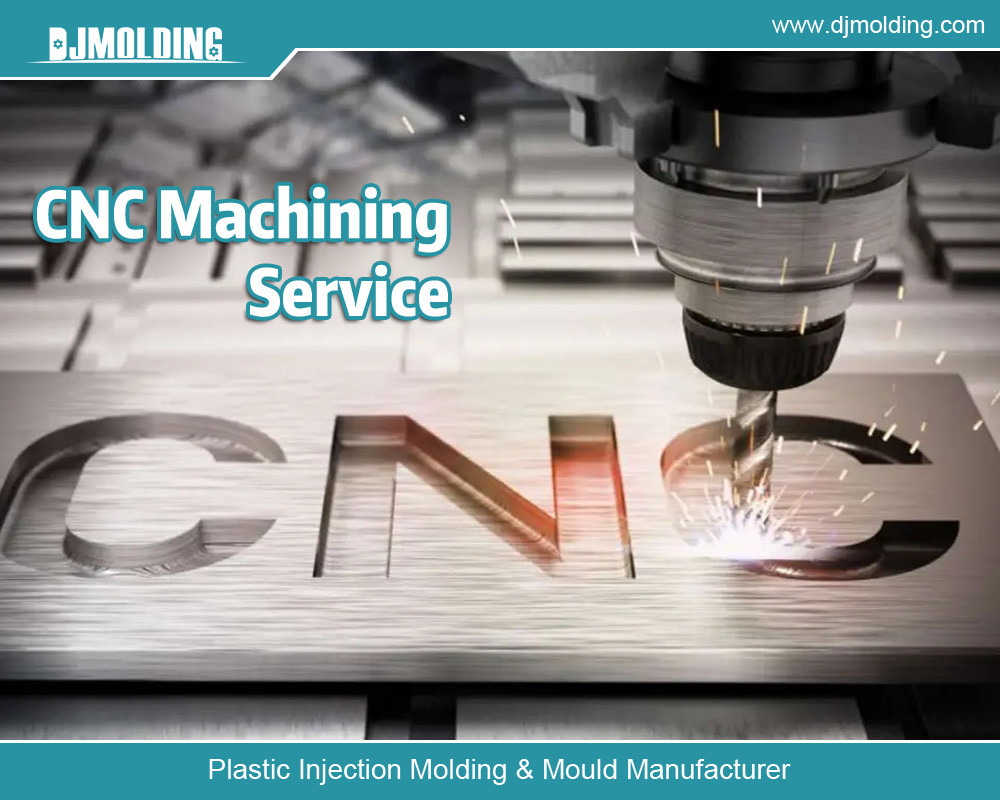
Final Thoughts
If you require intricate injection molded parts at incredibly fast speeds, sign up for a free account with any of the best companies that specialize in low volume injection molding, and upload your part drawing. You will receive expert feedback and a detailed quote response. Get started today!
For more about an engineer’s guide to low volume injection molding from low volume injection molding manufacturers,you can pay a visit to Djmolding at https://www.djmolding.com/low-volume-injection-molding/ for more info.