ABS Injection Molding: Comprehensive Guide To Techniques, Benefits, And Applications
ABS Injection Molding: Comprehensive Guide To Techniques, Benefits, And Applications
Acrylonitrile Butadiene Styrene (ABS) is a popular thermoplastic polymer recognized for its durability, high impact resistance, and ease of fabrication. Its properties make it a preferred material in the automotive and electronics industries. ABS injection molding, specifically, is one of the most efficient and versatile manufacturing processes for producing a vast range of parts with high precision. This article covers the intricacies of ABS injection molding, including the process, techniques, advantages, challenges, and applications.
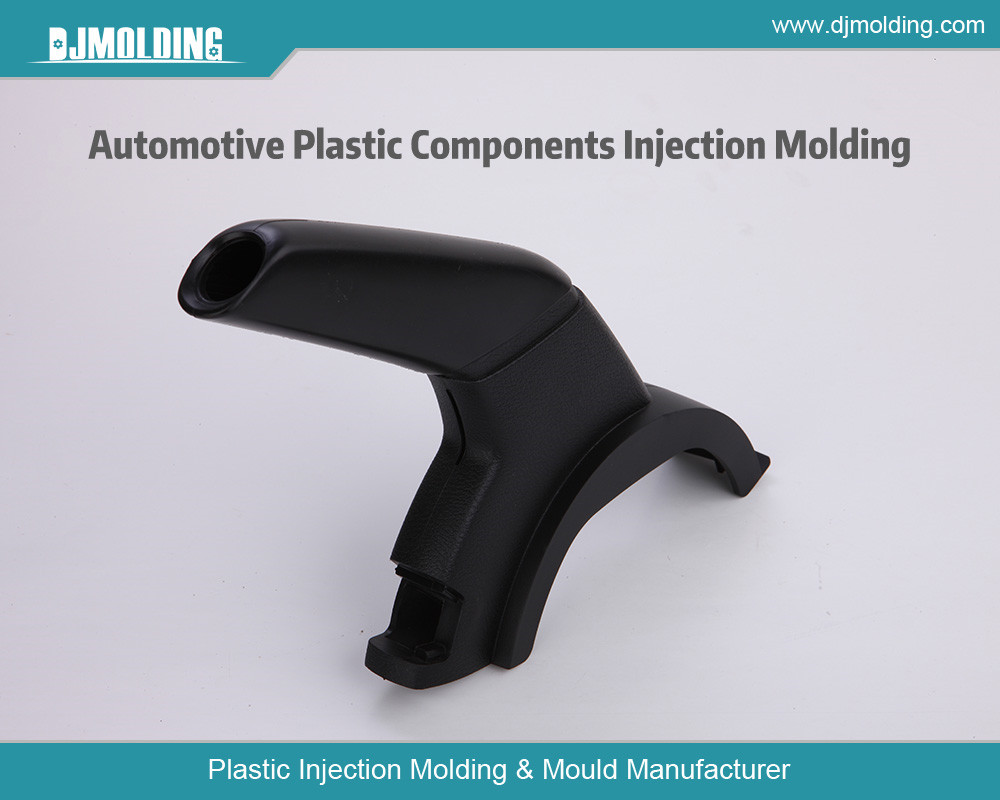
Introduction to ABS Injection Molding
What is ABS?
ABS is a copolymer made from acrylonitrile, butadiene, and styrene. Each component provides unique benefits:
- Acrylonitrile enhances resistance to chemicals and heat.
- Butadiene provides toughness and impact resistance.
- Styrene gives the material rigidity and ease of processing.
These properties make ABS suitable for various products, including automotive parts, household items, toys, and consumer electronics.
Why Injection Molding for ABS?
Injection molding is a manufacturing process in which molten plastic is injected into a mold cavity to create a product of a specific shape and design. ABS is an ideal candidate for this process due to its thermoplastic nature, meaning it can be melted, shaped, and solidified repeatedly without degrading. This recyclability makes ABS injection molding cost-effective, especially for high-volume production runs.
The ABS Injection Molding Process
The ABS injection molding process involves several critical stages for achieving optimal results. Here’s a breakdown of the steps:
Step 1: Material Preparation
Before the ABS material is fed into the injection molding machine, it undergoes drying to remove any moisture. Even small amounts of water can lead to issues like hydrolysis, which can degrade the polymer during the molding process and affect the finished part’s quality.
Step 2: Melting and Plasticizing
ABS pellets are loaded into the injection molding machine’s hopper, which transports them to the barrel. Inside the barrel, a rotating screw pushes the pellets toward the heating zones, where they are melted and plasticized to a uniform consistency. The temperature settings usually range between 200°C to 250°C, optimized to ensure proper melting without causing degradation.
Step 3: Injection
Once the ABS material reaches the desired molten state, it is injected into the mold cavity. Injection pressure is controlled to ensure the material fills every nook of the cavity, achieving a precise shape. For ABS, typical injection pressures range from 75 to 125 MPa, depending on part design and mold complexity.
Step 4: Cooling and Solidification
After filling the mold, the molten ABS begins to cool and solidify. Cooling is crucial as it directly affects part accuracy, surface finish, and shrinkage. The mold often has cooling channels that facilitate efficient heat transfer, minimizing cycle time.
Step 5: Ejection
Once the part has cooled sufficiently, the mold opens, and the molded part is ejected using ejector pins or a plate mechanism. Care is taken to remove the part without damage, as ABS can be prone to surface scratching or marring during ejection.
Critical Parameters and Techniques in ABS Injection Molding
Temperature Control
Temperature control is vital throughout the ABS injection molding process. Overheating can lead to burning, yellowing, or degradation of the material. Conversely, underheating can cause incomplete filling or surface defects. The main temperature parameters include:
- Barrel temperature (200-250°C): For melting ABS without decomposition.
- Mold temperature (50-70°C): To ensure smooth surface finish and dimensional accuracy.
Injection Pressure and Speed
Proper injection pressure and speed ensure the mold is filled quickly and thoroughly. High injection pressure can help fill complex molds, but excessive pressure might induce stress and warping in the final part. ABS injection speeds are generally moderate to avoid issues like jetting and flow marks.
Cooling Time Optimization
Efficient cooling is essential for reducing cycle time and enhancing productivity. ABS has a moderate cooling rate, and designers often use optimized cooling channels to dissipate heat and minimize part deformation evenly. Cooling time varies based on part thickness but constitutes a significant portion of the overall cycle time.
Shrinkage Control
ABS has relatively low shrinkage compared to other plastics, around 0.4% to 0.9%. However, uneven cooling or inadequate mold design can lead to warping or sink marks. Proper mold design, consistent cooling, and controlled processing parameters help minimize these effects.
Benefits of ABS Injection Molding
Cost-Effectiveness
ABS injection molding is economical for high-volume production. The material’s reusability, coupled with high cycle efficiency, reduces the per-part cost, making it suitable for mass production.
High Impact and Heat Resistance
ABS offers excellent impact resistance, making it ideal for parts that withstand mechanical stress. Additionally, it has good heat resistance, allowing ABS products to function well in temperatures up to 100°C without significant degradation.
Excellent Surface Finish
ABS has a naturally high gloss, making it suitable for products requiring aesthetic appeal, such as consumer electronics and automotive interiors. The material also responds well to various finishing techniques, such as painting, plating, and screen printing.
Good Machinability and Recyclability
ABS is easy to machine and can be post-processed using standard techniques, such as drilling or threading. It can also be recycled by grinding and re-melting, minimizing waste and promoting environmental sustainability.
Challenges in ABS Injection Molding
Moisture Sensitivity
ABS is highly sensitive to moisture, which can lead to hydrolysis and material degradation during the molding process. Proper drying before molding (typically for 2-4 hours at 80°C) is necessary to prevent defects like splay marks and weak parts.
Shrinkage and Warping
Despite its relatively low shrinkage rate, ABS can still be prone to warping or shrinkage in complex mold designs. Mold design considerations, such as uniform wall thickness and optimized cooling channels, are critical in controlling these issues.
Surface Defects
Depending on mold design, pressure, and temperature settings, ABS parts can suffer from surface defects, including weld lines, flow marks, and sink marks. Adjustments in injection speed, pressure, and gate location can help mitigate these problems, though achieving the desired finish may involve trial and error.
Environmental Sensitivity
ABS is less resistant to UV exposure and may turn yellow or degrade when exposed to sunlight for prolonged periods. This limits its outdoor applications unless it is UV-stabilized through additives.
Applications of ABS Injection Molding
ABS injection molding is widely used across industries due to its versatility and durability. Here are some typical applications:
Automotive Industry
ABS parts are popular in the automotive sector and used in dashboards, interior trim, grilles, and bumpers. The material’s impact resistance and ease of fabrication make it ideal for components that must withstand stress and frequent use.
Consumer Electronics
Many electronic products, including laptop housings, mobile phone cases, and remote controls, are made from ABS due to their excellent surface finish and aesthetic appeal. It also offers good electrical insulation, making it a safe choice for electronic components.
Household Appliances
ABS is frequently used in small household appliances like vacuum cleaners, coffee makers, and microwave oven components. Its resistance to heat and ease of cleaning are valuable in this sector.
Toys
One of ABS’s most famous applications is in toy manufacturing, notably in LEGO bricks. The material’s rigidity, color retention, and child-safe properties make it a go-to choice for toys and recreational products.
Medical Devices
ABS injection molding is commonly used to create non-sterile components for medical devices, such as casings for diagnostic tools and housings for portable medical equipment. However, ABS is not usually selected for sterile environments unless specially treated.
Innovations and Trends in ABS Injection Molding
Sustainable Manufacturing
With an increasing focus on environmental responsibility, manufacturers are seeking ways to recycle ABS and reduce waste. Innovations in recycling technology allow ABS scrap to be reprocessed for new applications while incorporating bio-based ABS alternatives, which are also being explored.
Advanced Mold Design Software
Modern software enables precise mold filling, cooling, and warpage simulation, allowing engineers to optimize molds for ABS parts before production. This minimizes trial-and-error in mold design, improving efficiency and reducing costs.
Additive Manufacturing Integration
Manufacturers sometimes combine injection molding with 3D printing for prototyping and low-volume production. This hybrid approach allows for faster design validation and iteration, making it possible to refine ABS molds more quickly and cost-effectively.
Improved Surface Finishes
Advancements in mold texture and finishing techniques have expanded the surface finishes available for ABS products. New technologies allow for textures ranging from matte to glossy, expanding ABS’s aesthetic applications.
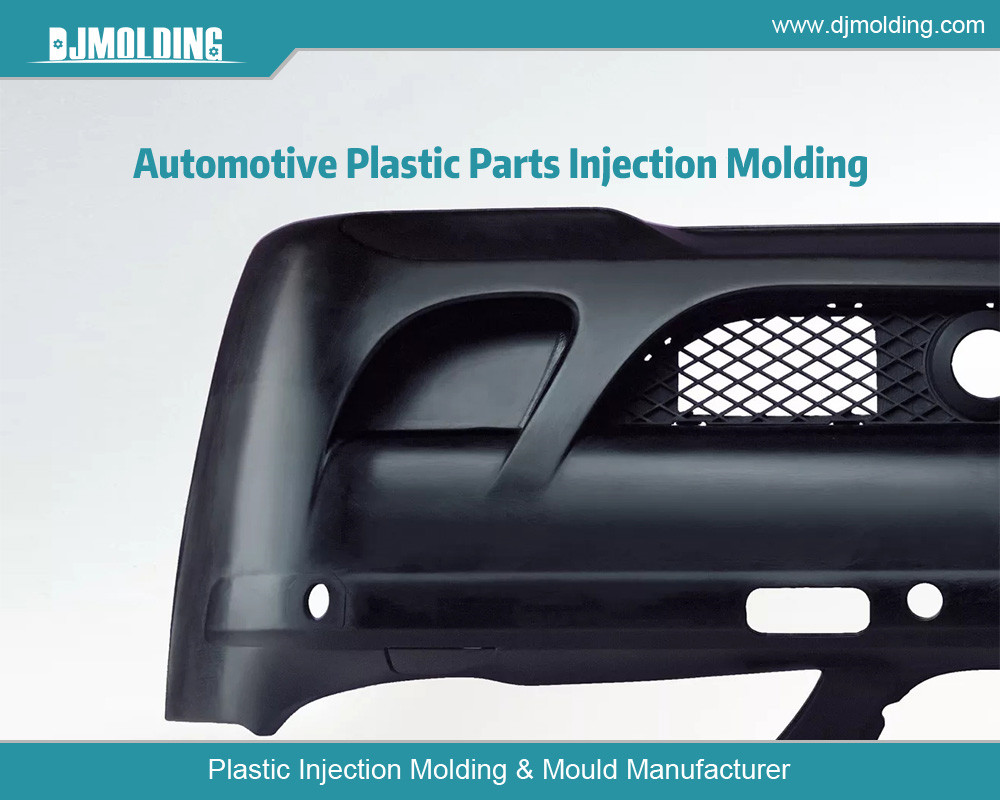
Conclusion
ABS injection molding is a flexible, reliable, cost-effective method for producing durable plastic parts. With its unique balance of strength, impact resistance, and ease of manufacturing, ABS suits applications across industries, from automotive to electronics and household goods. Despite its limitations—such as sensitivity to moisture and UV—proper handling and processing make ABS a highly adaptable material in modern manufacturing. As advancements in technology and sustainable practices continue, ABS injection molding is poised to play an even more significant role in the future of mass manufacturing.
For more about abs injection molding: comprehensive guide to techniques, benefits, and applications, you can pay a visit to Djmolding at https://www.djmolding.com/nylon-vs-abs-injection-molding-whats-their-difference/ for more info.