A Simple Guide To Injection Mold Gate Design
A Simple Guide To Injection Mold Gate Design
Injection molding is a widely used manufacturing process for producing plastic parts by injecting molten material into a mold. One of the critical aspects of this process is the design of the gate, which is the channel through which the molten plastic enters the mold cavity. Proper gate design is essential for ensuring the final product’s quality, strength, and appearance. This article provides a comprehensive guide to injection mold gate design, covering the types of gates, their placement, size considerations, and best practices.
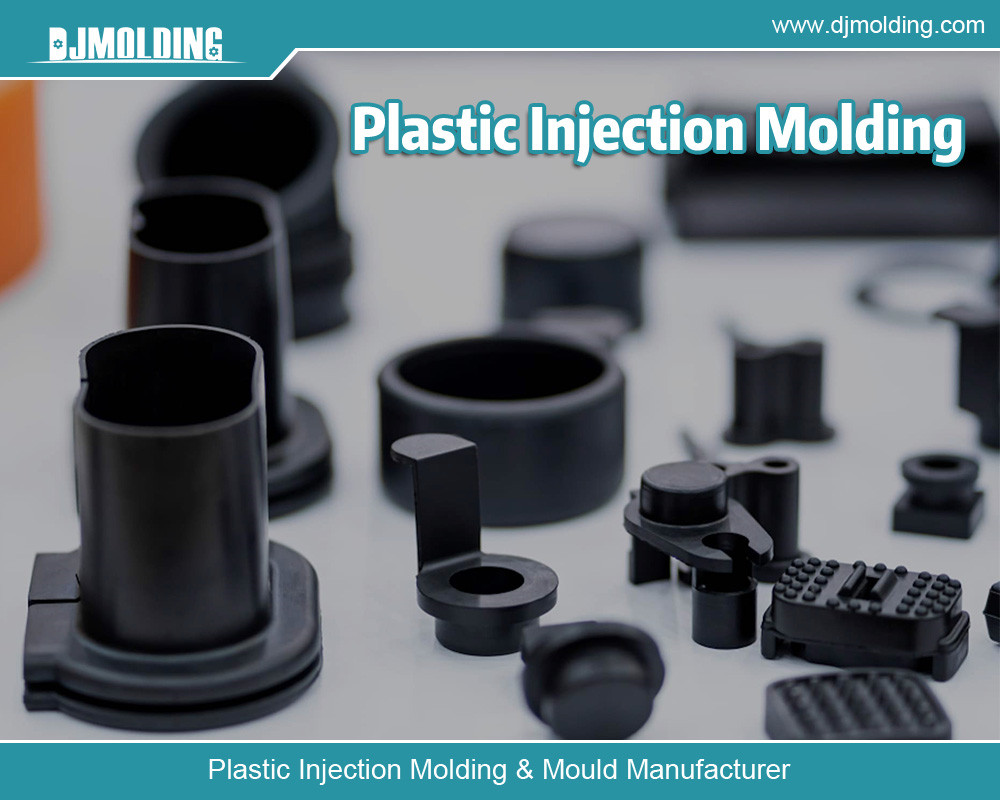
Introduction to Injection Mold Gate Design
Injection mold gate design plays a crucial role in the success of the molding process. The gate is the last section of the runner system, where molten plastic transitions from the runner into the mold cavity. The design and placement of the gate affect the flow of the plastic, the cooling rate, and, ultimately, the quality of the molded part.
Importance of Gate Design
The gate design impacts several critical aspects of the injection molding process, including:
- Flow Characteristics: The gate determines how the molten plastic flows into the mold, affecting the filling pattern and the occurrence of defects like weld lines and air traps.
- Pressure Distribution: A well-designed gate helps maintain uniform pressure throughout the mold cavity, ensuring consistent part quality.
- Cooling and Solidification: The gate size and location influence the cooling rate and solidification of the plastic, impacting the final part’s mechanical properties and appearance.
- Ease of Removal: The gate design affects the ease of removing the part from the mold and the appearance of the gate mark on the finished product.
Types of Injection Mold Gates
Several types of gates are used in injection molding, each with its advantages and applications. The choice of gate type depends on factors such as the part geometry, material, and production requirements.
Edge Gate
Edge gates, also known as side gates, are located on the mold’s parting line and direct the molten plastic into the side of the cavity. This type of gate is simple to design and easy to machine. It is suitable for most general-purpose applications and offers reasonable control over the filling pattern.
Advantages:
- Easy to design and machine
- Suitable for a wide range of part geometries
- Reasonable control over filling pattern
Disadvantages:
- It may leave a noticeable gate mark
- Not ideal for high-pressure applications
Submarine Gate
Submarine or tunnel gates are located below the parting line and direct the plastic flow through a small tunnel. This gate type is often used for parts that require a clean surface finish, as the gate mark is less visible.
Advantages:
- Minimal gate mark
- Suitable for automated ejection systems
- Reduces post-molding finishing operations
Disadvantages:
- More complex to design and machine
- Not suitable for very thick or high-pressure applications
Pin Gate
Pin gates are small, cylindrical gates typically used in multi-cavity molds. They are located at the center of the part and direct the plastic flow in a radial pattern. Pin gates are commonly used for small parts and offer reasonable control over the filling process.
Advantages:
- Minimal gate mark
- Suitable for multi-cavity molds
- Reasonable filling control for small parts
Disadvantages:
- Limited to small parts
- It may require additional post-molding finishing
Hot Runner Gate
Hot runner gates use a heated manifold system to keep the plastic molten until it reaches the cavity. This type of gate is used for high-volume production and reduces material waste by eliminating the need for runners.
Advantages:
- Reduces material waste
- Suitable for high-volume production
- Improved part quality and consistency
Disadvantages:
- Higher initial cost and maintenance
- Complex design and setup
Diaphragm Gate
Diaphragm gates are used for cylindrical or tubular parts, directing the plastic flow from the inside of the part outward. This gate type ensures even filling and is ideal for parts that require a high level of concentricity.
Advantages:
- Ensures even filling for cylindrical parts
- Good control over concentricity
Disadvantages:
- Limited to specific part geometries
- More complex design and machining
Gate Placement Considerations
The placement of the gate is a critical factor in injection mold design. Proper gate placement ensures optimal plastic flow, minimizes defects, and improves the overall quality of the part.
Flow Path and Fill Time
The gate should be placed to ensure a balanced flow path and uniform fill time across the mold cavity. This helps prevent air traps, weld lines, and uneven shrinkage. The flow path should be as short and direct as possible to reduce pressure drop and ensure efficient filling.
Gate Location and Part Strength
The gate location can affect the part’s mechanical properties. Gates placed in high-stress, high-stress, or load areas can lead to weak spots and potential failure points. It is essential to place the gate in a location that does not compromise the part’s structural integrity.
Aesthetic Considerations
Gate marks can affect the appearance of the final product. For parts where aesthetics are essential, the gate should be placed in a less visible location or can be easily removed or finished. Submarine and hot runner gates are often preferred for their minimal gate marks.
Ejection and Post-Processing
The gate placement should facilitate the part’s easy ejection from the mold. Difficulty removing gates can lead to defects and damage to the part. The gate location should also minimize the need for post-processing and finishing operations.
Gate Size and Shape Considerations
The size and shape of the gate are:
- Crucial factors that influence the flow rate.
- Pressure drop.
- Cooling time of the injection molding process.
Proper sizing ensures efficient filling and minimizes defects.
Gate Size
The gate size should be optimized to balance the flow rate and pressure drop. A too small gate can restrict plastic flow, leading to incomplete filling and defects. Conversely, a gate that is too large can cause excessive pressure drop and increase the risk of flash.
Factors Influencing Gate Size:
- Part volume and thickness
- Material viscosity and flow characteristics
- Required fill time and injection pressure
- Cooling rate and solidification time
Gate Shape
The shape of the gate affects the flow characteristics and cooling rate. Common gate shapes include rectangular, circular, and trapezoidal. Each shape has its advantages and is chosen based on the specific requirements of the part and material.
Rectangular Gates:
- Provide a wide flow path
- Suitable for parts with high fill rates
- Can be more prone to gate marks
Circular Gates:
- Offer a uniform flow pattern
- Ideal for small parts and pin gates
- Provide reasonable control over the fill rate
Trapezoidal Gates:
- Combine the benefits of rectangular and circular gates
- Provide a balanced flow and minimal gatemarks
- Suitable for a wide range of applications
Best Practices for Injection Mold Gate Design
Designing an effective gate system requires careful consideration of various factors. Here are some best practices to ensure optimal gate design and improve the quality of the molded parts.
Simulate the Flow
Using simulation software to model the plastic flow can help identify potential issues and optimize gate design. Simulation tools can predict the flow pattern, fill time, and possible defects, allowing designers to make informed decisions and avoid costly errors.
Consider the Material
Different materials have unique flow characteristics and cooling rates. The gate design should be tailored to the specific material being used. Consult material data sheets and work with suppliers to determine the optimal gate size and placement.
Optimize Cooling
The gate design influences the part’s cooling rate. Ensuring uniform cooling can prevent issues such as warping and shrinkage. The gate should be designed to allow even cooling across the entire part.
Minimize Gate Marks
For parts where aesthetics are important, choosing gate types and placements that minimize gate marks is essential. Submarine and hot runner gates are often preferred for their minimal visible marks.
Plan for Ejection
The gate design should facilitate easy ejection of the part from the mold. Consider the parting line and ejection system when designing the gate to ensure smooth removal and minimize damage to the part.
Collaborate with Mold Makers
Working closely with mold makers can provide valuable insights into the manufacturability and practicality of the gate design. Mold makers can offer recommendations based on their experience and expertise, helping optimize the production design.
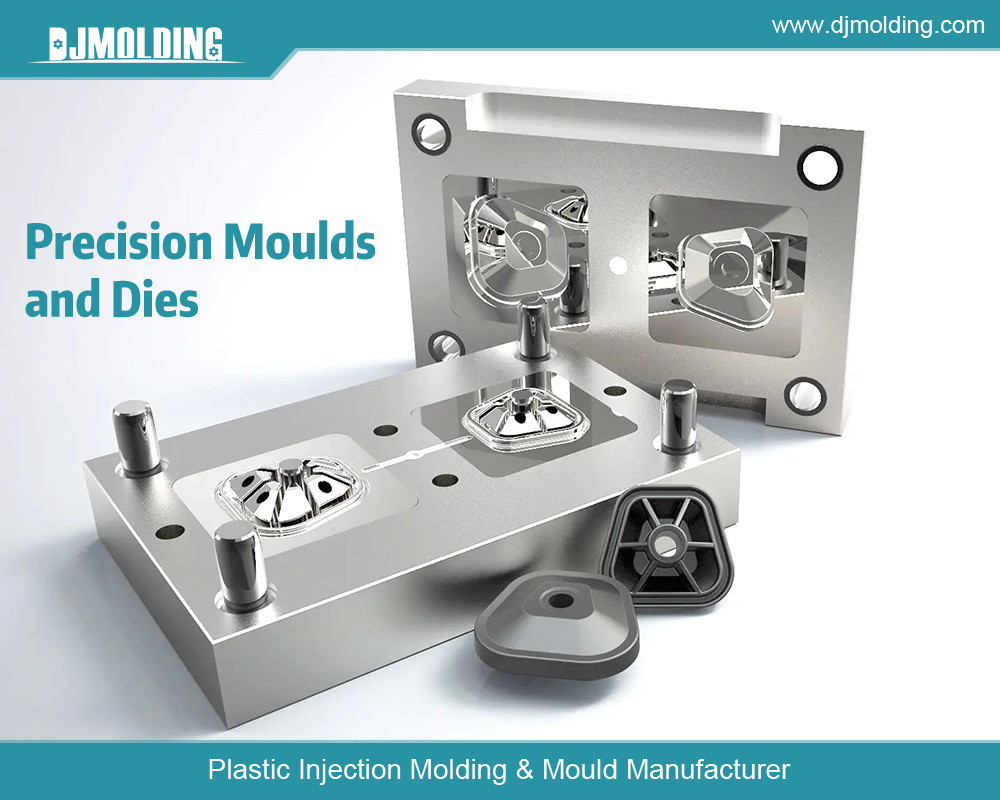
Conclusion
Injection mold gate design is a critical aspect of the injection molding process, influencing the plastic flow, cooling rate, and overall quality of the molded part. By understanding the different types of gates, their placement considerations, and best design practices, manufacturers can optimize their gate systems to produce high-quality, defect-free parts. Effective gate design can be achieved through careful planning, simulation, and collaboration with experts, improving efficiency and product performance in the injection molding process.
For more about a simple guide to injection mold gate design,you can pay a visit to Djmolding at https://www.djmolding.com/injection-mould-design/ for more info.