A Full Guide Of Mold Flow Analysis In Injection Molding
A Full Guide Of Mold Flow Analysis In Injection Molding
Injection molding is a widely utilized manufacturing process for creating intricate geometries and high-precision parts. Central to the efficiency and quality of this process is Mold Flow Analysis (MFA). This simulation tool helps predict the behavior of molten material as it flows into a mold cavity. This guide will delve into the fundamental aspects of MFA, its importance, and its application in optimizing injection molding processes.
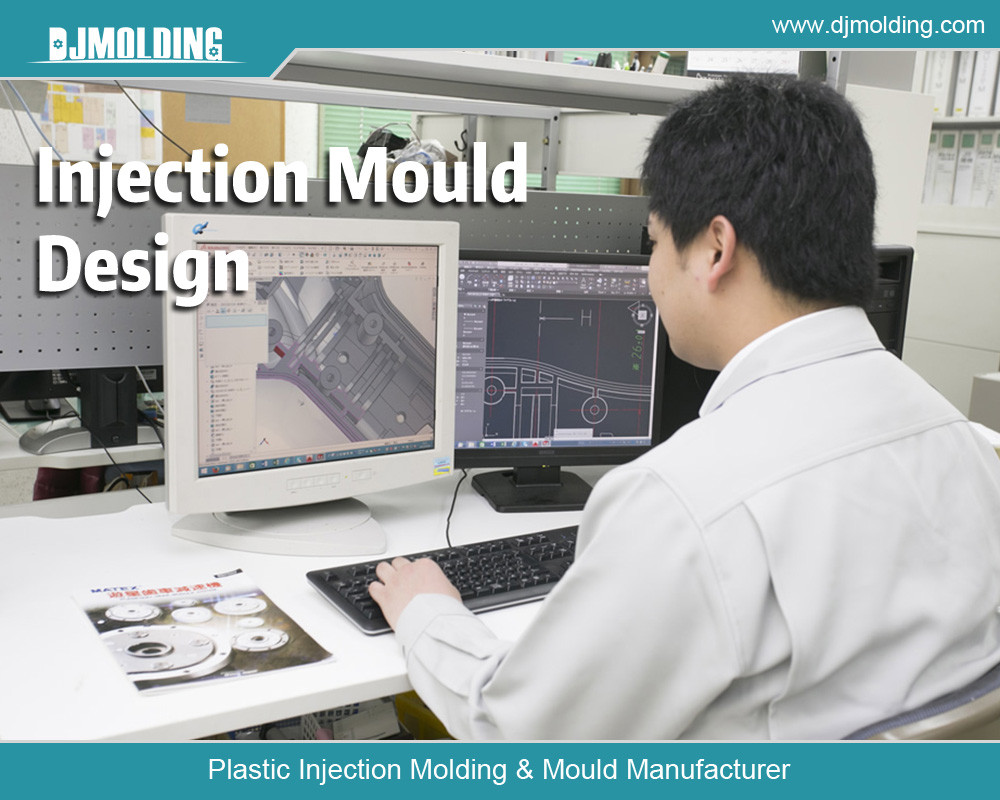
1. Introduction to Mold Flow Analysis
Mold Flow Analysis is a computational tool used to simulate the injection molding process of plastic components. It helps manufacturers predict how molten plastic will fill a mold, solidify, and behave during and after molding. By providing insights into potential issues, MFA enables engineers to optimize mold designs, reduce production costs, and improve product quality.
1.1 Purpose and Benefits
The primary purpose of Mold Flow Analysis is to ensure that the molding process produces defect-free parts consistently. Its benefits include:
- Improved Design Quality: Engineers can identify and rectify design flaws before physical production by simulating plastic flow.
- Reduced Lead Time: MFA allows for virtual testing and adjustments, significantly shortening the time required for mold development.
- Cost Efficiency: Manufacturers can avoid costly rework and material wastage by predicting potential issues early.
2. The Mold Flow Analysis Process
The Mold Flow Analysis process involves several key steps, each crucial for achieving accurate and valuable results. This section outlines these steps in detail.
2.1 Data Preparation
Before running a simulation, accurate data is essential. This includes:
- Material Properties: Information about the plastic material’s behavior, such as viscosity, density, and thermal properties.
- Geometry of the Part: The 3D model of the component to be molded.
- Mold Design: Details of the mold cavity, including gate locations, runner systems, and cooling channels.
2.2 Meshing
Meshing involves dividing the 3D model into more minor, manageable mesh elements. This step is crucial for accurate simulation as it affects the resolution and precision of the results. A finer mesh provides more detailed results but requires more computational power.
2.3 Simulation Setup
In this step, the parameters for the simulation are defined, including:
- Injection Conditions: Parameters such as injection pressure, temperature, and speed.
- Cooling Conditions: Information about the cooling system and its efficiency.
- Boundary Conditions: Constraints and interactions between the mold and the material.
2.4 Running the Simulation
Once the setup is complete, the simulation is run. The software calculates the behavior of the molten plastic as it flows through the mold, considering factors like flow front, temperature distribution, and pressure changes.
2.5 Analyzing Results
After the simulation, the results are analyzed to identify potential issues such as:
- Air Traps: Areas where air is trapped, which can cause defects.
- Flow Fronts: The path the molten plastic takes can reveal potential filling problems.
- Cooling Inefficiencies: Areas where cooling is inadequate, leading to uneven solidification.
3. Common Issues Identified by Mold Flow Analysis
Mold Flow Analysis helps identify and address several common issues that can arise during the injection molding process.
3.1 Air Traps
Air traps occur when air is trapped in the mold cavity, preventing the complete filling of the part. This can lead to defects such as voids or incomplete parts. MFA helps locate air traps and optimize venting systems to prevent them.
3.2 Weld Lines
Weld lines are where two flow fronts meet. They can weaken the part and affect its appearance. Mold Flow Analysis can help adjust the gate locations or modify the mold design to minimize weld lines.
3.3 Sink Marks
Sink marks are depressions on the surface of a part caused by uneven cooling or inadequate packing pressure. MFA allows engineers to analyze the cooling process and adjust parameters to reduce or eliminate sink marks.
3.4 Warping
Warping occurs when a part distorts after cooling, often due to uneven cooling or internal stresses. Mold flow analysis helps identify the causes of warping and provides solutions to minimize it.
4. Applications of Mold Flow Analysis
Mold Flow Analysis is widely used in various industries to improve the quality and efficiency of injection molding processes. Here are some of its critical applications:
4.1 Automotive Industry
MFA designs and optimizes parts such as dashboards, bumpers, and interior components in the automotive industry. It helps ensure that parts meet stringent quality and performance standards while reducing material costs and production time.
4.2 Consumer Goods
Mold Flow Analysis helps design products with complex shapes and fine details for consumer goods, such as electronic housings, toys, and kitchenware. It ensures that these products are manufactured with high precision and minimal defects.
4.3 Medical Devices
In the medical device industry, MFA is crucial for designing parts that require high precision and reliability, such as syringes, surgical instruments, and diagnostic equipment. The analysis helps ensure these parts meet stringent regulatory requirements and function effectively.
4.4 Packaging
In packaging, Mold Flow Analysis optimizes the design of containers and bottles, ensuring that they are both functional and cost-effective. It helps reduce material usage and improve the overall design of the packaging.
5.Best Practices for Mold Flow Analysis
Following best practices is essential to achieve the best results with Mold Flow Analysis. Here are some key recommendations:
5.1 Use Accurate Material Data
Ensure that the material data used in the simulation is accurate and up-to-date. This includes properties such as viscosity, thermal conductivity, and shrinkage. Accurate material data is critical for obtaining reliable simulation results.
5.2 Refine the Mesh Appropriately
Choose an appropriate mesh size based on the complexity of the part and the desired level of detail. A finer mesh provides more accurate results but requires more computational resources. Balance the need for detail with the available computing power.
5.3 Validate Results with Physical Testing
While Mold Flow Analysis is a powerful tool, validating simulation results with physical testing is always beneficial. Conducting mold trials and comparing results with the simulation helps ensure that the analysis accurately reflects real-world conditions.
5.4 Continuously Update and Improve Models
Simulation models are continuously updated and refined to incorporate the latest information as new materials, technologies, and processes emerge. This helps in maintaining the accuracy and relevance of the analysis.
5.5 Collaborate with Experienced Engineers
Working with experienced engineers skilled in Mold Flow Analysis can significantly improve the quality of the analysis. Their expertise in interpreting results and making informed decisions can enhance the effectiveness of the simulation.
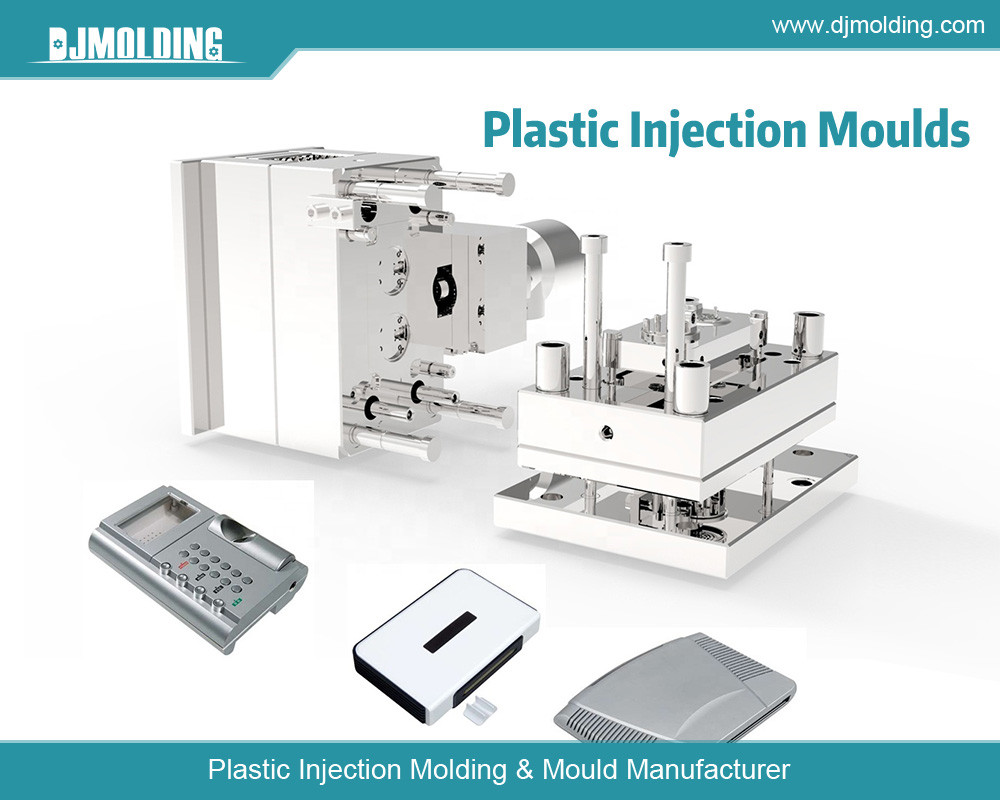
Conclusion
Mold Flow Analysis is an invaluable tool in injection molding, offering significant benefits in quality, efficiency, and cost savings. MFA helps engineers and manufacturers optimize mold designs and production processes by simulating molten plastic behavior and identifying potential issues. Understanding the process, recognizing everyday matters, and applying best practices are crucial to leveraging the full potential of Mold Flow Analysis. As technology advances, MFA will continue to play a vital role in developing high-quality, efficient, cost-effective molded parts across various industries.
For more about a full guide of mold flow analysis in injection molding, you can pay a visit to Djmolding at https://www.djmolding.com/molding-service/ for more info.