A Comprehensive Guide Of Injection Molding Troubleshooting
A Comprehensive Guide Of Injection Molding Troubleshooting
Injection molding is a widely used manufacturing process for producing parts by injecting molten material into a mold. While this technique is efficient and allows for high-volume production, it can present various challenges. Troubleshooting injection molding issues is crucial for maintaining quality and efficiency. This article delves into common problems encountered during injection molding, offering insights and practical solutions.
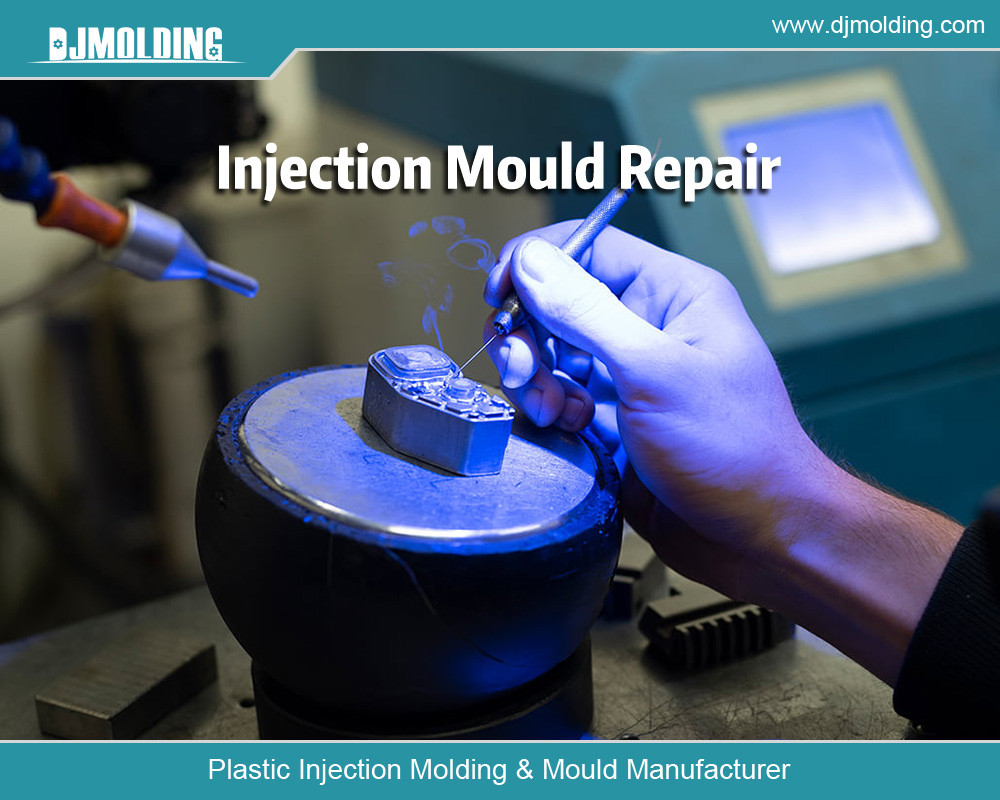
Understanding Injection Molding
What is Injection Molding?
Injection molding is a process used to create parts by forcing molten material into a mold. This method is prevalent for producing plastic components but can also be applied to metals and ceramics. The basic steps of injection molding include:
- Melting the material
- Injecting it into a mold
- Allowing it to cool and solidify
- Removing the finished part from the mold
Advantages of Injection Molding
- High Efficiency: Capable of producing large quantities of parts quickly.
- Complex Shapes: Allows for intricate designs that are difficult to achieve through other methods.
- Material Versatility: Compatible with various materials, including thermoplastics, thermosets, and metals.
- Cost-Effective: Reduces waste and lowers the cost per unit in large production runs.
Common Injection Molding Problems
Despite its advantages, injection molding can encounter several issues. Understanding these problems is the first step toward effective troubleshooting.
1. Defects in Molded Parts
Defects in molded parts can manifest in various forms, including:
- Short Shots: Incomplete filling of the mold.
- Warpage: Deformation of the part after cooling.
- Surface Imperfections: Includes blemishes, scratches, or rough textures.
2. Machine-Related Issues
Problems can also arise from the injection molding machine itself:
- Inconsistent Injection Pressure: This can lead to variations in part quality.
- Temperature Fluctuations: Affect the viscosity of the molten material.
- Clogged Nozzles: Can disrupt the flow of material into the mold.
3. Material-Related Challenges
The choice and condition of the material can significantly impact the injection molding process:
- Moisture Content: Excess moisture can lead to steam generation during molding, causing defects.
- Material Degradation: Prolonged exposure to heat can degrade certain materials.
- Incompatibility: Mixing incompatible materials can lead to poor adhesion and defects.
Injection Molding Troubleshooting Techniques
Troubleshooting is essential to identify and resolve issues effectively. Here are some techniques:
1. Diagnosing Common Issues
Short Shots
- Causes: Insufficient injection pressure, material not heated enough, mold blockage.
- Solutions: Increase injection pressure, check heating elements, and clear blockages.
Warpage
- Causes: Uneven cooling, improper mold design, or material selection.
- Solutions: Optimize cooling channels, select appropriate materials, and adjust mold design.
Surface Imperfections
- Causes: Contaminated material, worn mold surfaces, or inadequate venting.
- Solutions: Use clean materials, maintain mold surfaces, and improve venting.
2. Adjusting Machine Settings
Adjusting the settings on the injection molding machine can often resolve issues:
- Injection Speed: Increasing speed can help fill the mold more effectively.
- Cooling Time: Extending cooling time can help reduce warpage and improve surface finish.
- Back Pressure: Adjusting back pressure can enhance the consistency of the melt.
3. Material Management
Proper management of materials is crucial for quality:
- Drying Materials: Ensure materials are adequately dried to remove moisture.
- Regular Testing: Implement regular testing of materials for quality assurance.
- Proper Storage: Store materials in airtight containers to prevent contamination.
Preventive Measures for Injection Molding
Prevention is often more effective than troubleshooting. Here are some preventive measures to consider:
1. Routine Maintenance
Regular maintenance of machinery and molds can prevent many issues:
- Inspection: Conduct routine inspections of molds and machines.
- Cleaning: Regularly clean nozzles, screws, and molds to avoid contamination.
- Lubrication: Keep moving parts well-lubricated to ensure smooth operation.
2. Training and Development
Investing in workforce training can significantly reduce errors:
- Skill Development: Provide ongoing training for machine operators.
- Process Understanding: Ensure all staff understand the injection molding process and its potential challenges.
3. Material Selection
Choosing the suitable material is essential:
- Compatibility: Ensure materials are compatible with the mold and process.
- Performance Characteristics: Select materials based on the specific requirements of the final product.
Advanced Troubleshooting Techniques for Injection Molding
While basic troubleshooting methods can resolve many common issues in injection molding, more complex problems may require advanced techniques. These approaches involve a deeper understanding of the process and often integrate technology and analytics. Below, we explore some advanced troubleshooting techniques that can enhance the efficiency and quality of injection molding operations.
1. Data Analysis and Process Monitoring
Utilizing data analytics can significantly improve the troubleshooting process. Operators can identify trends and anomalies by collecting and analyzing data from the injection molding machine.
- Real-Time Monitoring: Implement real-time sensors to monitor critical parameters such as pressure, temperature, and flow rate. This allows for immediate detection of deviations from set standards.
- Data Logging: Maintain logs of machine settings, cycle times, and defect rates to identify patterns over time. Analyzing historical data can help pinpoint recurring issues.
- Statistical Process Control (SPC): Use statistical methods to monitor and control the injection molding process, ensuring it operates at its full potential.
2. Root Cause Analysis (RCA)
When problems persist despite initial troubleshooting efforts, conducting a thorough Root Cause Analysis (RCA) is essential.
Whys Technique: Ask “why” repeatedly (typically five times) to drill down to the underlying cause of an issue. For example:
- Why was the part warped? (The cooling time was insufficient.)
- Why was the cooling time insufficient? (The cooling system was not functioning correctly.)
- Continue this process until the fundamental cause is reached.
Fishbone Diagram: Use this visual tool to categorize potential causes of problems. This helps in systematically identifying issues related to:
- Material
- Machine
- Method
- Environment
- Measurement
3. Advanced Simulation Software
Employing advanced simulation software can aid in understanding and predicting problems before they occur.
Finite Element Analysis (FEA): FEA simulates how a part behaves under different conditions, helping identify potential areas of weakness or defects.
Mold Flow Analysis: Use Mold Flow Analysis software to simulate the injection process, allowing for optimization of design and parameters. This can help:
- Predict short shots and air traps
- Optimize gate locations
- Reduce cycle times
4. Implementing Design for Manufacturability (DFM)
Designing parts with manufacturability in mind can prevent many common injection molding issues.
- Simplified Geometries: Design makes it easier to mold parts, reducing the risk of defects.
- Draft Angles: Ensure that parts have appropriate draft angles for easier ejection from the mold.
- Uniform Wall Thickness: Design parts with uniform wall thickness to minimize warpage and sink marks.
5. Collaborative Problem Solving
Engaging all stakeholders in the troubleshooting process can lead to more effective solutions.
- Cross-Functional Teams: Form teams that include engineers, machine operators, and quality control personnel to address problems collaboratively.
- Feedback Loops: Establish mechanisms for operators to report issues and suggest improvements. This encourages a culture of continuous improvement.
- Training Workshops: Conduct workshops where team members share experiences and learn from each other’s challenges and solutions.
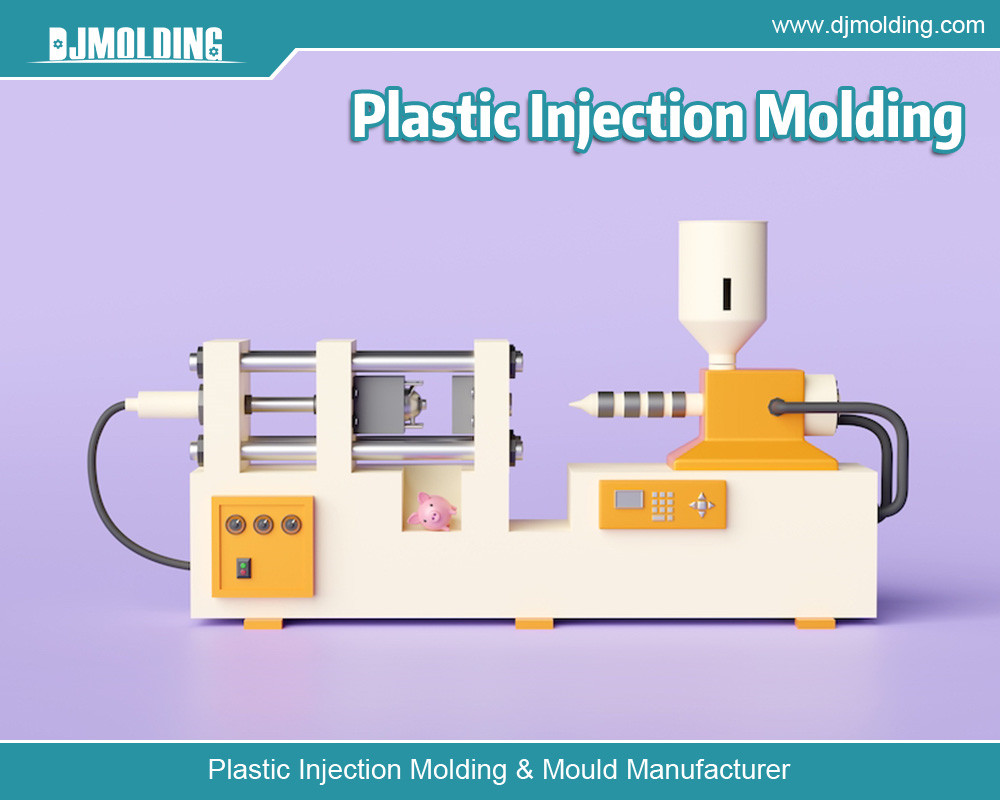
Conclusion
Injection molding is a powerful manufacturing technique with the potential for high efficiency and quality. However, it is not without its challenges. Understanding common issues and employing effective troubleshooting techniques can significantly enhance the process. By implementing preventive measures, such as routine maintenance and proper material management, manufacturers can mitigate problems before they occur. Continuous improvement and training are essential to staying ahead in the dynamic world of injection molding, ensuring both product quality and operational efficiency.
For more about a comprehensive guide of injection molding troubleshooting, you can pay a visit to Djmoldign at https://www.djmolding.com/ for more info.