Plastic Injection Molding Services
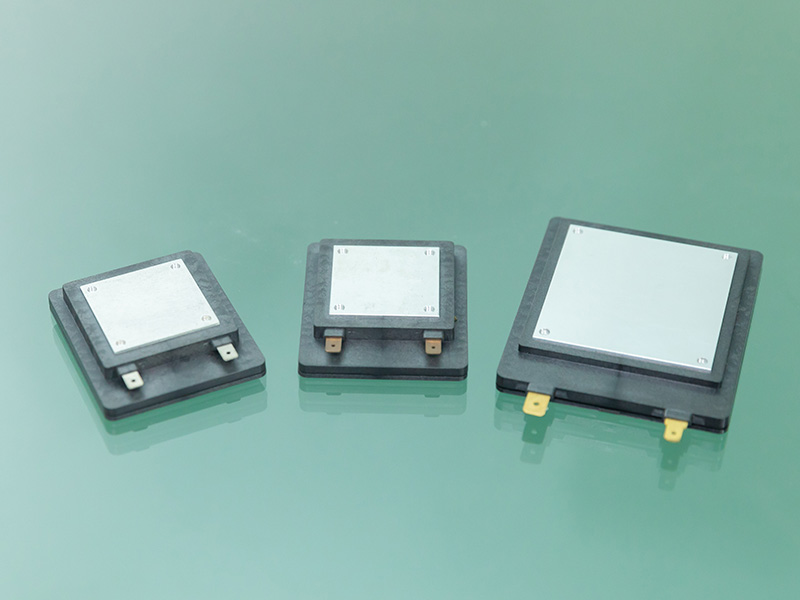
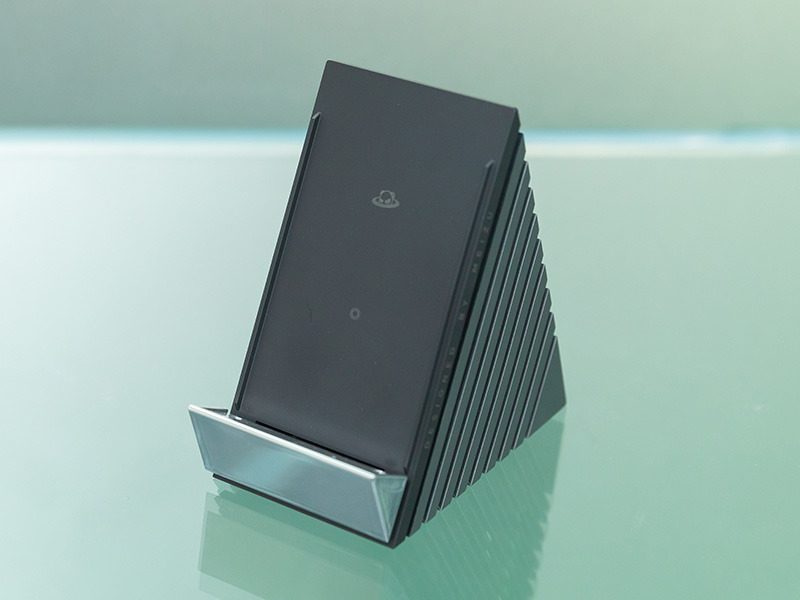
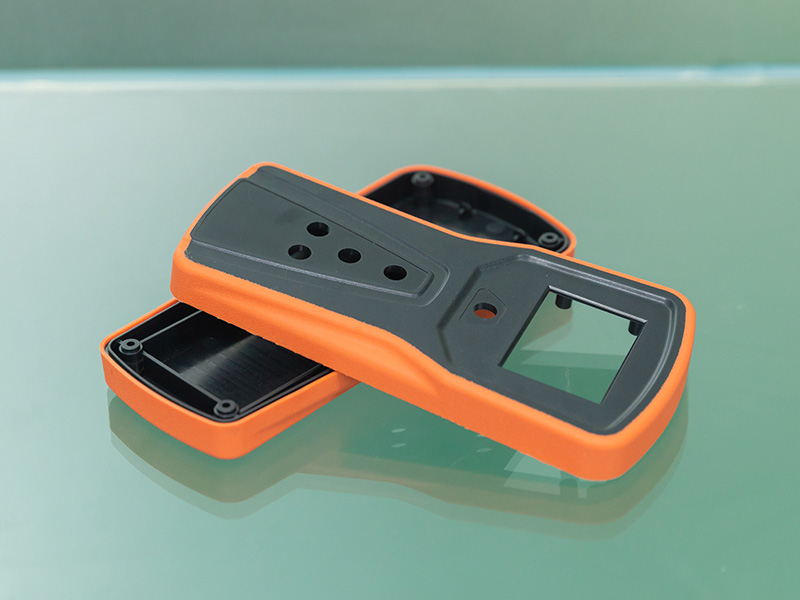
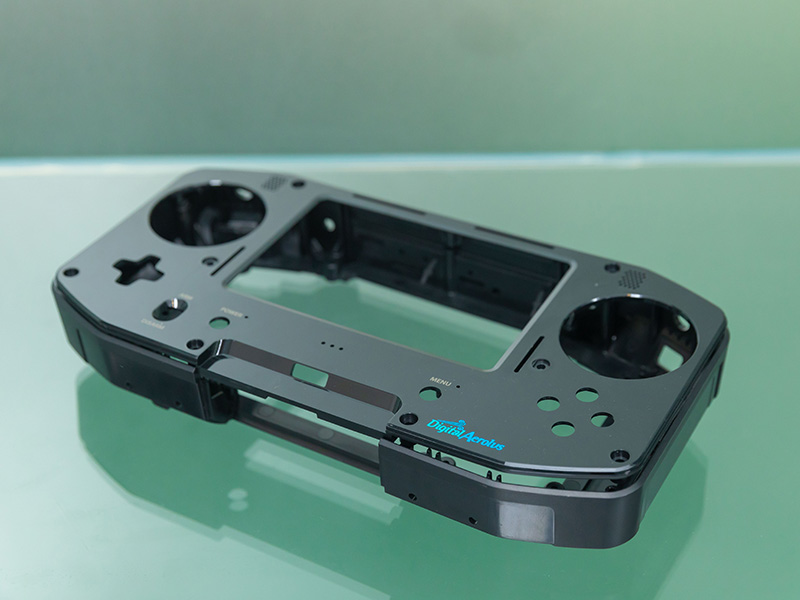
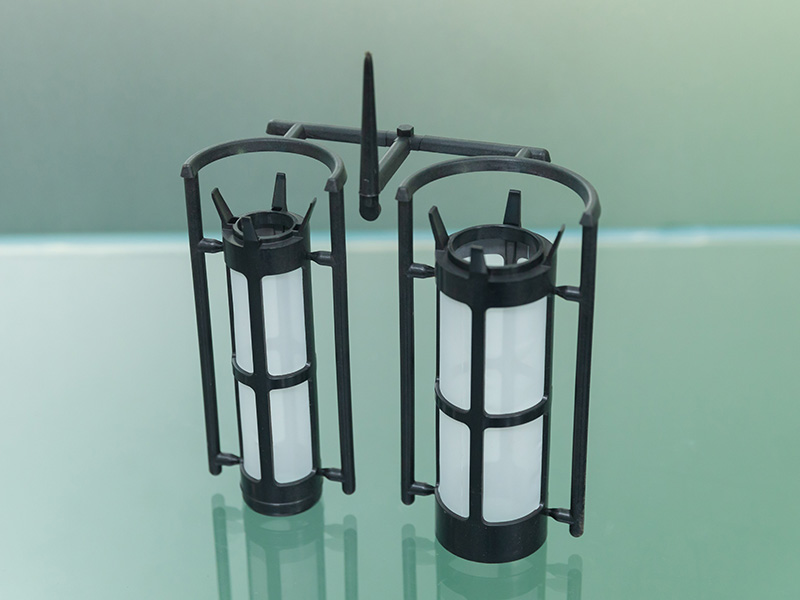
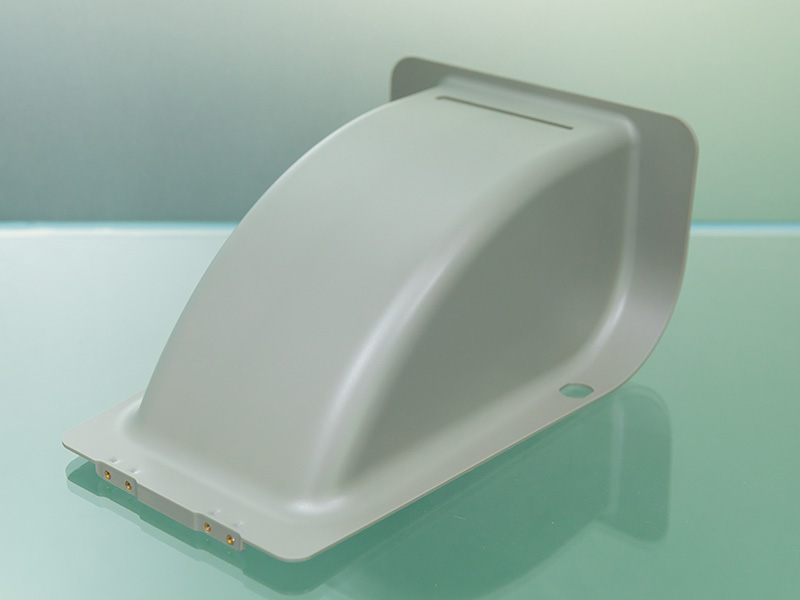
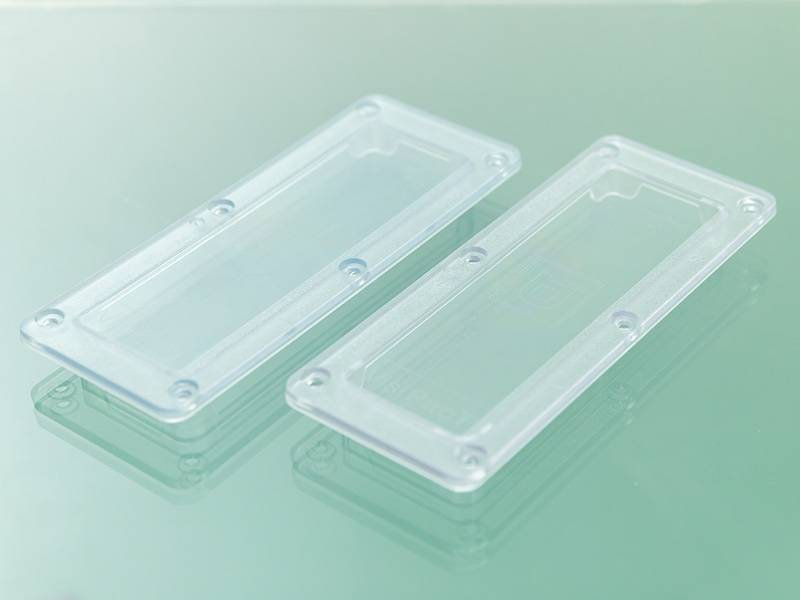
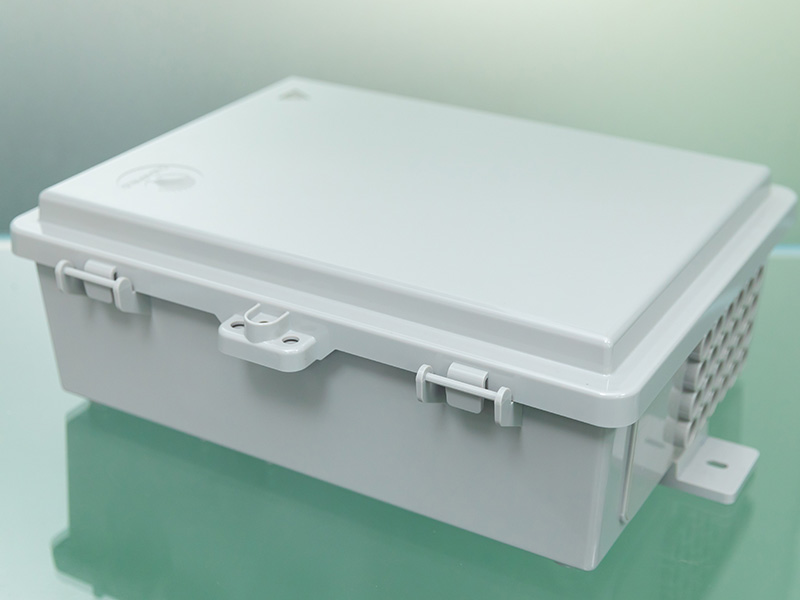
Plastic injection molding is the process of filling a mold tool with liquid plastic resin under great pressure. The tool may comprise a single cavity or hundreds of cavities in order to make indefinite numbers of parts.
There are many advantages to plastic injection molding. These include the ability to make large volumes of parts quickly, high surface quality, many resins to choose from, color flexibility, and durable tooling that can last for years.
* Thousands of resins to choose from
* Economies of scale
* Stable and repeatable
* Excellent surface quality
* Overmolding for more design options
* Multi-cavity and family tools
Plastic injection molding is a manufacturing process that involves melting plastic pellets and injecting them into a mold cavity to create a three-dimensional object. This process begins with many products, from small precision parts to significant automotive components. Plastic injection molding offers many advantages over other manufacturing processes, including high production rates, design flexibility, and cost-effectiveness. This guide will look in-depth at plastic injection molding and explore its various applications, benefits, and limitations
Custom Plastic Injection Molding
Plastic parts are made as per your specifications and are not supplied to any other customer. These could be engineering parts, caps, packaging items, medical parts etc.
Liquid Silicone Rubber(LSR) Injection Molding
Injection molding of Liquid Silicone Rubber (LSR) is a process used to produce pliable, durable parts in high volumes. During the process, several components are necessary: an injector, a metering unit, a supply drum, a mixer, a nozzle, and a mold clamp, among others.
Rapid prototyping is the process of developing prototypes for products as fast as possible. Prototyping is an integral part of product development. It’s where design teams create an experimental product to apply their ideas.
It is the process of developing prototypes as fast as possible to emulate a final product design. It is a series of techniques used to model a scale prototype of a physical component or an assembly using CAD data.
CNC stands for computer numerical control, which is a technology to control the machining tools automatically by applying a microcomputer that is attached to the tool. CNCs machines would operate according to the coded programmed instructions, such as the movement of the machines, the feed rate of materials, the speed, and so on. There is no need for operators to control the machine manually, thus, CNC helps to improve the efficiency and precision to a large extent.
Automotive Plastic Components Injection Molding
High automotive performance demands parts that handle it all. Plastics perform from the engine to the chassis; throughout the interior to the exterior. Today’s automotive plastics make up approximately 50% of the volume of a new light vehicle but less than 10% of its weight.
We have developed moulds and having regular production of Automotive Plastic Parts which supply for automotive industry. We have coperated with several well known auto manufacturers.
Recycled Plastic Injeciton Molding
Recycled plastics refer to plastic materials that are repurposed. It can come from other plastic products or waste that results from the plastic injection moulding process. These recycled materials can be of any type or colour, and when you use them to manufacture products via injection moulding, there is no loss in quality.
At DJmolding, our on-demand, low-volume production offering with injection molding—which uses aluminum tooling—is a fast, cost-effective way to produce hundreds of thousands of end-use molded parts.
Low Volume Manufacturing Service
Small businesses often need help finding affordable manufacturing solutions that can produce low volumes of products without incurring high costs. Small businesses with limited resources often need to overcome a significant barrier due to the cost-effectiveness requirement of creating large quantities in traditional manufacturing methods. However, with the emergence of low volume manufacturing services, small businesses can now produce small products at a fraction of the cost of conventional manufacturing methods. This article will explore the benefits of low volume manufacturing services and how they can help small businesses stay competitive.
With over thousands of plastic injection molding and plastic manufacturing facilities to choose from all over the word, what are one of the top qualities that make a molding company stand out? When choosing a provider, many factors should be taken into consideration; including capabilities, quality assurance, company reputation, cost, and delivery time. Finding the right plastic injection molder to fit your needs may seem time-consuming but determining your low and high-volume requirements first and how they may shift over time, will help to narrow down your options.
Thermoplastic Injection Molding
Thermoplastic injection molding is a popular manufacturing process used to create various plastic parts for multiple industries. This process involves melting plastic pellets and injecting them into a mold to produce a three-dimensional shape. Thermoplastic injection molding is highly efficient and cost-effective for producing large volumes of high-quality plastic parts with tight tolerances. This comprehensive guide will explore the various aspects of thermoplastic injection molding, including its advantages and disadvantages, the types of thermoplastics used, the injection molding process, design considerations, and much more.
Insert injection molding is a widely used manufacturing process in producing complex plastic parts with embedded components. This technique involves inserting metal or plastic parts into the mold cavity before the injection molding process. The molten material then flows around the inserted element, creating a solid bond between the two materials. Insert injection molding offers several advantages, including improved design flexibility, reduced assembly time, and enhanced part functionality. This comprehensive guide will explore the different techniques, benefits, and applications of insert injection molding.
Overmolding is a manufacturing process in which a substrate or a base component is combined with one or more materials to create a final product with improved functionality, durability, and aesthetics. This process has gained popularity in recent years due to its ability to enhance the quality and performance of products while reducing costs and simplifying the assembly process. Overmolding finds applications in various industries, such as automotive, electronics, medical devices, and consumer products. To comprehensively understand this process, this article will delve into the multiple aspects of overmolding, including its techniques, materials, and applications.
Two-color injection molding, or two-shot injection molding, is a manufacturing process used to produce plastic parts with two different colors or materials. This process involves injecting two other materials into a single mold to create a role with a two-tone finish or different functional properties. Two-color injection molding has many applications in various industries, including automotive, medical, and consumer products. This article will delve into the details of two-color injection molding, its advantages, limitations, and applications.
On Demand Manufacturing Service
In today’s fast-paced world, the demand for efficiency and flexibility in manufacturing has surged. Enter on-demand manufacturing services, a revolutionary approach reshaping traditional production paradigms. This article dives deep into the concept, advantages, applications, and prospects of on-demand manufacturing services, shedding light on how they transform industries worldwide.
To know more about DJmolding plastic products and services, please contact us with Email: info@djmolding.com