Short Shot Injection Molding: A Comprehensive Overview
Short Shot Injection Molding: A Comprehensive Overview
Short shot injection molding is a crucial technique in the manufacturing industry, particularly in producing high-quality plastic components. This process involves injecting a measured amount of molten plastic into a mold, which solidifies to form the desired shape. However, what happens when not enough material is injected? The result is a short shot a common issue that can lead to production delays and increased costs. This article delves into the intricacies of short shot injection molding, examining its causes, effects, and mitigation strategies, while highlighting its importance in the broader context of injection molding processes.
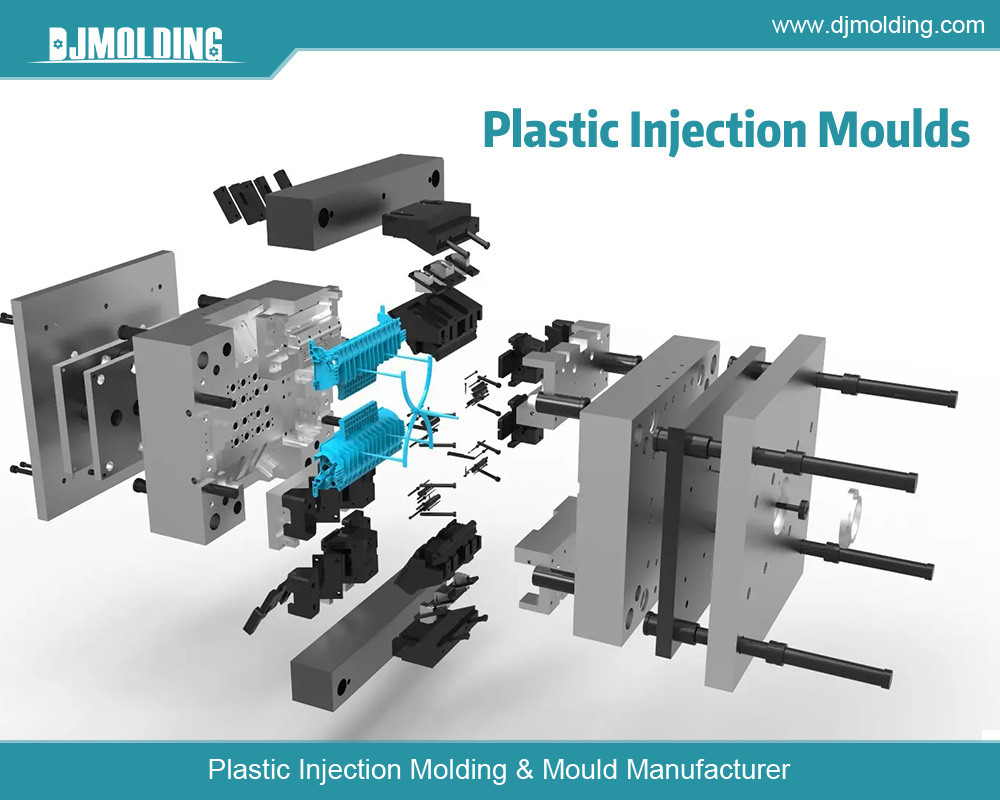
Understanding Injection Molding
What is Injection Molding?
Injection molding is a manufacturing process used to create parts by injecting molten material into a mold. The process involves several key steps:
- Heating the Material: Plastic pellets are heated until they melt.
- Injecting the Material: The molten plastic is injected into a mold under high pressure.
- Cooling: The material is allowed to cool and solidify in the mold.
- Ejecting: Once cooled, the solidified part is ejected from the mold.
Applications of Injection Molding
Injection molding is widely used in various industries, including:
- Automotive: Producing interior and exterior parts.
- Consumer Goods: Manufacturing toys, containers, and household items.
- Medical Devices: Creating precise components for healthcare applications.
- Electronics: Making casings and components for devices.
The Concept of Short Shots
Definition and Causes
A short shot occurs when an incomplete part is produced due to insufficient material injected into the mold. This can arise from several factors, including:
- Insufficient Injection Pressure: There is not enough force to fill the mold.
- Material Flow Issues: Problems with the viscosity of the plastic or its temperature can impede flow.
- Mold Design Flaws: Inadequate venting or gating systems can restrict material flow.
- Machine Malfunctions: Problems with the injection molding machine can lead to short shots.
Identifying Short Shots
Identifying a short shot can be straightforward, as it usually results in visible defects in the final product. Key indicators include:
- Incomplete filling of the mold.
- Surface irregularities.
- Dimensional inaccuracies.
Effects of Short Shots on Production
Quality Concerns
Short shots can significantly compromise the quality of the produced parts. Potential impacts include:
- Weakened Structural Integrity: Parts may not withstand intended loads.
- Aesthetic Defects: Visible flaws can affect marketability.
- Functional Limitations: Parts may not perform as designed.
Economic Implications
The economic ramifications of short shots can be substantial. Considerations include:
- Increased Waste: Short-shot parts often need to be scrapped or reworked.
- Production Delays: Re-running molds to correct short shots can lead to delays in the production schedule.
- Higher Costs: The need for additional material, labor, and time increases overall production costs.
Mitigating Short Shots
Design Considerations
To prevent short shots, careful attention must be paid to the design phase:
- Mold Design: Ensure the mold is adequately designed with appropriate gating and venting.
- Part Design: Optimize the part’s geometry to promote a uniform material flow.
Process Optimization
Implementing process improvements can also reduce the incidence of short shots:
- Adjusting Injection Parameters: Fine-tune injection pressure, speed, and temperature settings.
- Material Selection: Choose materials with the appropriate flow characteristics for the application.
Maintenance and Training
Regular maintenance and operator training can help mitigate issues:
- Machine Maintenance: Keep injection molding machines in good working condition to prevent malfunctions.
- Operator Training: Ensure that operators understand the implications of short shots and how to avoid them.
Advanced Techniques in Injection Molding
Simulation Software
Utilizing advanced simulation software can predict potential short shots before production begins:
- Flow Analysis: Assess how the molten material will flow through the mold.
- Thermal Analysis: Evaluate cooling rates and potential hotspots.
Alternative Molding Techniques
Exploring alternative molding techniques may also provide solutions:
- Gas-Assisted Injection Molding: Reduces the material required, lowering the risk of short shots.
- Multi-Shot Molding: Allows injecting different materials in one cycle, enhancing part integrity.
Critical Strategies for Preventing Short Shots
Preventing short shots in injection molding is essential for maintaining quality, reducing waste, and ensuring efficient production. Here are some key strategies that manufacturers can implement to minimize the risk of short shots:
1. Comprehensive Mold Design
Effective mold design is crucial to prevent short shots. Here are some considerations:
Gating Systems: Ensure that the gates are appropriately sized and located to allow for uniform flow of the molten material. Common types of gates include:
- Edge Gates: Positioned along the parting line.
- Submarine Gates: Located below the mold surface, reducing the visibility of gate marks.
- Hot Runner Systems: Minimize material waste and maintain consistent flow temperature.
Venting: Proper venting is essential to allow air to escape from the mold cavity. Key points include:
- Vent Location: Place vents at the highest points of the mold.
- Vent Size: Use adequate vent widths to allow for effective airflow.
Mold Geometry: Design molds with consistent wall thickness to prevent flow disruptions. Consider:
- Draft Angles: Implement draft angles to ease part ejection and ensure complete filling.
- Rib and Boss Design: Avoid excessively thick sections that trap air and impede flow.
2. Process Parameter Optimization
Fine-tuning injection molding parameters can significantly reduce the likelihood of short shots. Essential parameters to adjust include:
- Injection Pressure: Increase pressure to ensure the molten material fills the mold cavity.
- Injection Speed: Control the speed of injection to allow the material to flow smoothly without causing turbulence.
Temperature Control: Maintain optimal material temperature to ensure it flows easily. This includes:
- Melt Temperature: Ensure that the melt temperature is within the recommended range for the material used.
- Cooling Temperature: Adjust cooling temperatures to promote uniform solidification.
3. Material Selection and Preparation
Choosing the suitable material and preparing it properly can significantly impact flow characteristics:
Material Properties: Select materials with suitable flow properties for the specific part design. Consider:
- Viscosity: Lower viscosity materials flow better and fill molds more completely.
- Additives: Use additives to enhance flow, if necessary.
Drying and Conditioning: Properly dry materials before processing to prevent moisture-related flow issues.
4. Regular Maintenance and Calibration
Maintaining equipment and regularly calibrating machinery can prevent mechanical issues that contribute to short shots:
- Machine Calibration: Ensure injection molding machines are calibrated correctly for pressure, speed, and temperature settings.
- Routine Maintenance: Schedule regular maintenance checks to identify and address potential issues before they lead to production problems.
5. Training and Best Practices
Investing in operator training and implementing best practices can help mitigate the risk of short shots:
Operator Training: Provide comprehensive training for operators on:
- Machine Operation: Ensure they understand how to adjust settings effectively.
- Identifying Issues: Train them to recognize early signs of short shots and take corrective actions.
Standard Operating Procedures: Develop and implement standard operating procedures that outline best practices for setup, operation, and troubleshooting.
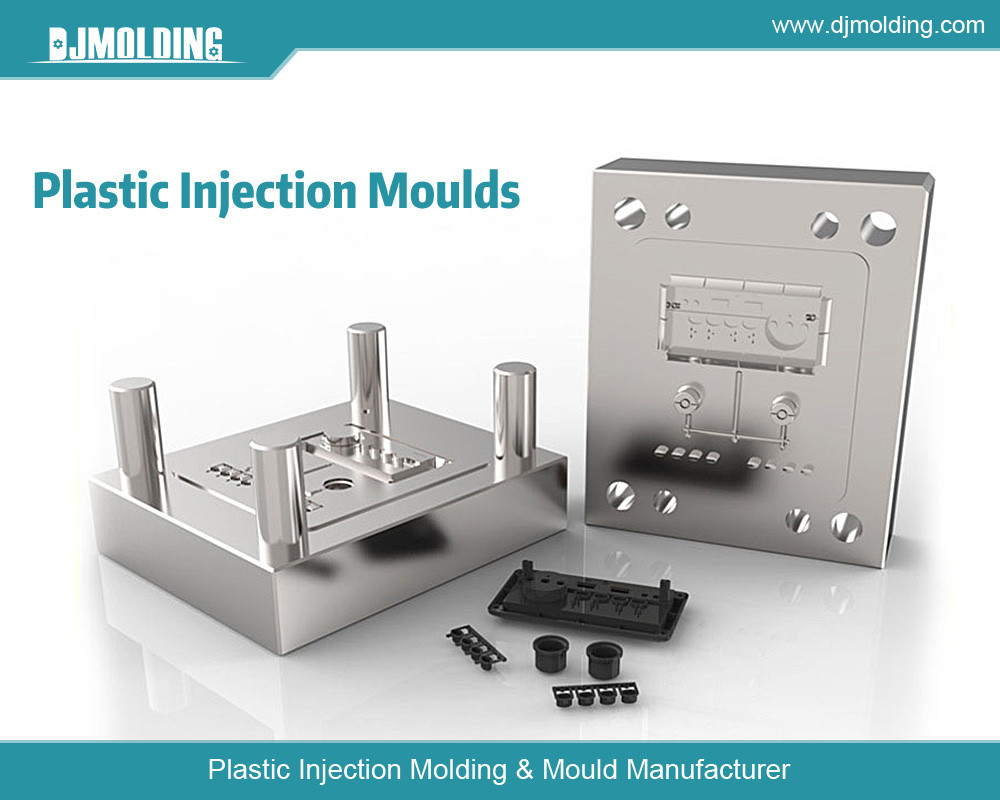
Conclusion
Short shot injection molding represents a critical challenge within the broader field of injection molding. Understanding its causes, effects, and prevention strategies is essential for manufacturers aiming to efficiently produce high-quality, reliable parts. By optimizing mold design, refining injection parameters, and investing in training and maintenance, companies can significantly reduce the occurrence of short shots. As technology advances, embracing simulation tools and alternative techniques will further enhance production capabilities, ensuring that short shots become a rare occurrence rather than a frequent challenge. The ongoing pursuit of excellence in injection molding will improve product quality and contribute to a more sustainable and efficient manufacturing landscape.
For more about the short shot injection molding: a comprehensive overview, you can pay a visit to Djmolding at https://www.djmolding.com/ for more info.