PVC Injection Molding: A Comprehensive Guide
PVC Injection Molding: A Comprehensive Guide
PVC (Polyvinyl Chloride) injection molding is a widely used manufacturing process for creating durable plastic products. With its versatility, cost-effectiveness, and unique properties, PVC has become a preferred material in various industries, including construction, automotive, and consumer goods. This article will explore the intricacies of PVC injection molding, including its benefits, applications, process details, and best practices for successful implementation.
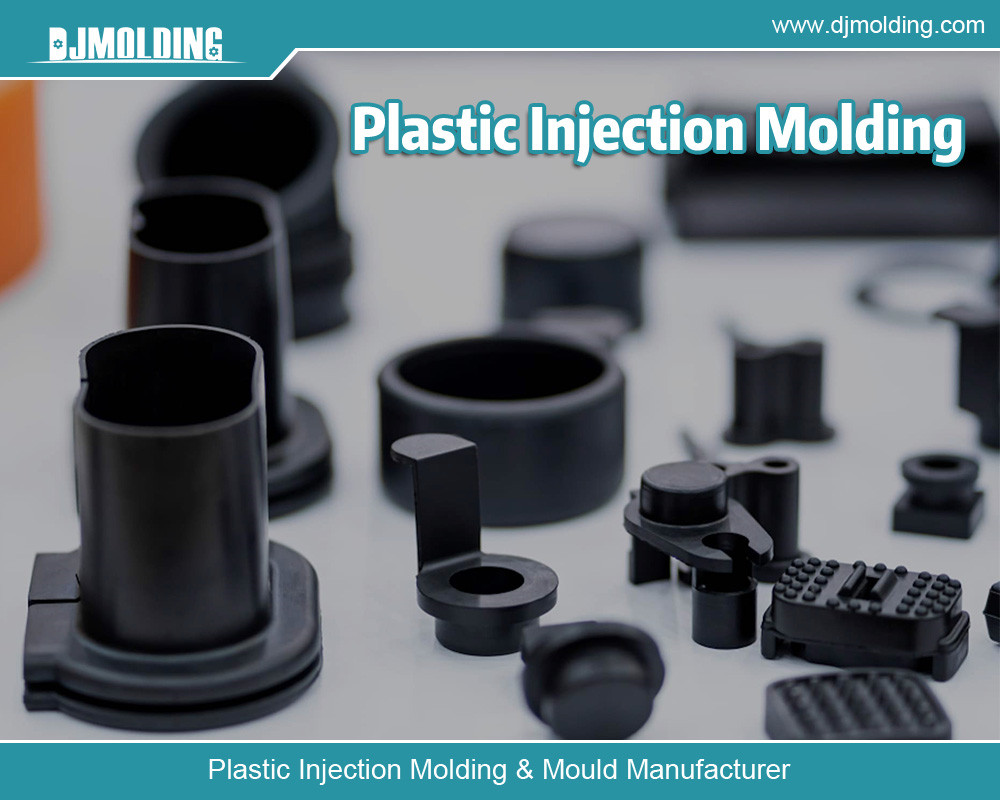
Understanding PVC Injection Molding
What is PVC Injection Molding?
PVC injection molding is a process that involves injecting molten PVC material into a mold cavity, where it cools and solidifies to form a desired shape. The process consists of several key steps:
- Material Preparation: PVC pellets are fed into the injection molding machine.
- Melting: The pellets are heated until they reach a molten state.
- Injection: The molten PVC is injected into the mold under high pressure.
- Cooling: The material is allowed to cool and solidify.
- Ejection: Once solidified, the part is ejected from the mold.
Advantages of PVC Injection Molding
PVC injection molding offers numerous benefits that make it a popular choice for manufacturers:
- Cost-Effectiveness: PVC is relatively inexpensive compared to other plastics, making it an economical option for large-scale production.
- Durability: PVC is resistant to chemicals, moisture, and UV light, enhancing the longevity of products.
- Versatility: The material can be easily formulated to achieve desired properties, such as flexibility or rigidity.
- Good Electrical Insulation: PVC provides excellent electrical insulation, making it suitable for electrical applications.
- Ease of Coloring: PVC can be easily colored, allowing for a wide range of aesthetic options.
Applications of PVC Injection Molding
1. Construction Industry
PVC is widely used in the construction industry due to its durability and resistance to environmental factors. Common applications include:
- Pipes and Fittings: Used for plumbing and drainage systems.
- Windows and Doors: PVC frames offer weather resistance and low maintenance.
- Flooring: Vinyl flooring, made from PVC, is famous for its durability and ease of installation.
2. Automotive Industry
In the automotive sector, PVC is utilized for its lightweight and durable properties. Applications include:
- Interior Trim: Dashboard components, door panels, and other interior features.
- Electrical Components: Insulation for wiring and connectors.
- Exterior Parts: Bumpers and trims that require resistance to weathering.
3. Consumer Goods
PVC injection molding is also prevalent in the production of various consumer products:
- Toys: Durable and safe materials for children’s toys.
- Packaging: Containers and bottles that require chemical resistance.
- Household Items: Kitchenware, storage solutions, and decorative items.
The PVC Injection Molding Process
Step-by-Step Breakdown
Understanding the PVC injection molding process is crucial for achieving high-quality products. Here’s a detailed breakdown:
Material Preparation
- Pellet Selection: Choose the appropriate grade of PVC pellets based on the application.
- Drying: PVC pellets may need to be dried to reduce moisture content, which can affect molding quality.
Melting
- Temperature Control: Set the appropriate barrel temperature to ensure the PVC melts uniformly. Typical temperatures range from 350°F to 450°F (177°C to 232°C).
- Screw Design: Use a screw design that promotes thorough mixing and uniform melting of the PVC.
Injection
- Injection Pressure: Maintain the proper injection pressure to ensure complete mold cavity filling.
- Injection Speed: Adjust the speed based on the complexity of the part to avoid defects.
Cooling
- Cooling Time: Allow sufficient cooling time to ensure the part solidifies properly without warping.
- Cooling Channels: Design molds with effective cooling channels to enhance cooling efficiency.
Ejection
- Ejector System: An effective ejector system releases the part from the mold without causing damage.
- Post-Ejection Inspection: Inspect the ejected parts for defects and quality assurance.
Challenges in PVC Injection Molding
Material Sensitivity
PVC can be sensitive to processing conditions, and improper handling may lead to:
- Degradation: Overheating can degrade PVC, leading to discoloration and loss of mechanical properties.
- Moisture Absorption: Improperly dried materials can cause flow and surface finish issues.
Mold Design Complexity
- Complex Geometries: Designing molds for complex parts can be challenging, requiring advanced simulation and testing.
- Ventilation: Inadequate venting can lead to air traps and incomplete filling.
Environmental Concerns
While PVC is durable, its production and disposal can raise environmental concerns:
- Recycling Issues: PVC is not as easily recyclable as other plastics.
- Additives: Some additives used in PVC formulations can pose health and environmental risks.
Best Practices for Successful PVC Injection Molding
Optimize Machine Settings
- Temperature Control: Monitor and adjust temperature settings to ensure optimal melting and processing.
- Pressure and Speed Adjustments: Fine-tune injection pressure and speed based on part complexity.
Quality Control Measures
- Regular Inspections: Implement routine inspections of molded parts to identify defects early.
- Testing: Conduct mechanical testing to ensure that parts meet the required specifications.
Employee Training
- Operator Training: Provide comprehensive training for operators on machine operation, troubleshooting, and maintenance.
- Safety Protocols: Ensure that all safety measures are in place to protect workers handling PVC materials.
Sustainable Practices
- Material Sourcing: Consider using recycled PVC materials where feasible.
- Waste Management: Implement strategies to reduce waste during the manufacturing process.
Innovations in PVC Injection Molding
As industries evolve, so do the technology and techniques used in PVC injection molding. Recent innovations are enhancing the process’s efficiency, quality, and sustainability. Here are some key innovations currently shaping the future of PVC injection molding:
Advanced Material Formulations
High-Performance PVC Blends: New formulations are being developed to enhance the mechanical properties of PVC, including flexibility and impact resistance.
Additive Technologies: Incorporating additives that improve UV stability, fire resistance, and antimicrobial properties is becoming more common. This leads to:
- Enhanced Durability: Products that can withstand harsh environments.
- Improved Safety: Reducing risks associated with material degradation.
Automation and Smart Manufacturing
Robotic Integration: Robots in the injection molding process are on the rise, streamlining operations and reducing labor costs. Key benefits include:
- Increased Precision: Robots can handle complex tasks with high accuracy.
- Reduced Cycle Times: Automation can speed up production rates significantly.
IoT and Data Analytics: The Internet of Things (IoT) is being leveraged to monitor machinery in real-time, enabling:
- Predictive Maintenance: Identifying potential machine failures before they occur, minimizing downtime.
- Process Optimization: Analyzing data to refine molding parameters for better quality and efficiency.
Eco-Friendly Practices
Sustainable Material Sourcing: Manufacturers increasingly use recycled PVC or bio-based alternatives to reduce environmental impact. This includes:
- Recyclability Initiatives: Developing products that can be more easily recycled at the end of their lifecycle.
- Waste Reduction Strategies: Implementing processes that minimize scrap and rework.
Energy-Efficient Technologies: Innovations in machinery are leading to energy-efficient injection molding processes, including:
- Hybrid Machines: Combining electric and hydraulic systems to reduce energy consumption.
- Heat Recovery Systems: Capturing and reusing heat from the process to lower energy costs.
Enhanced Mold Design Techniques
- 3D Printing for Prototyping: 3D printing to create mold prototypes allows for faster iterations and more complex designs without the costs associated with traditional mold manufacturing.
Simulation Software: Advanced simulation tools are helping engineers predict flow patterns and cooling rates, leading to:
- Better Mold Designs: Reducing issues such as short shots and warping.
- Optimized Cycle Times: Enhancing overall productivity by refining cooling and injection processes.
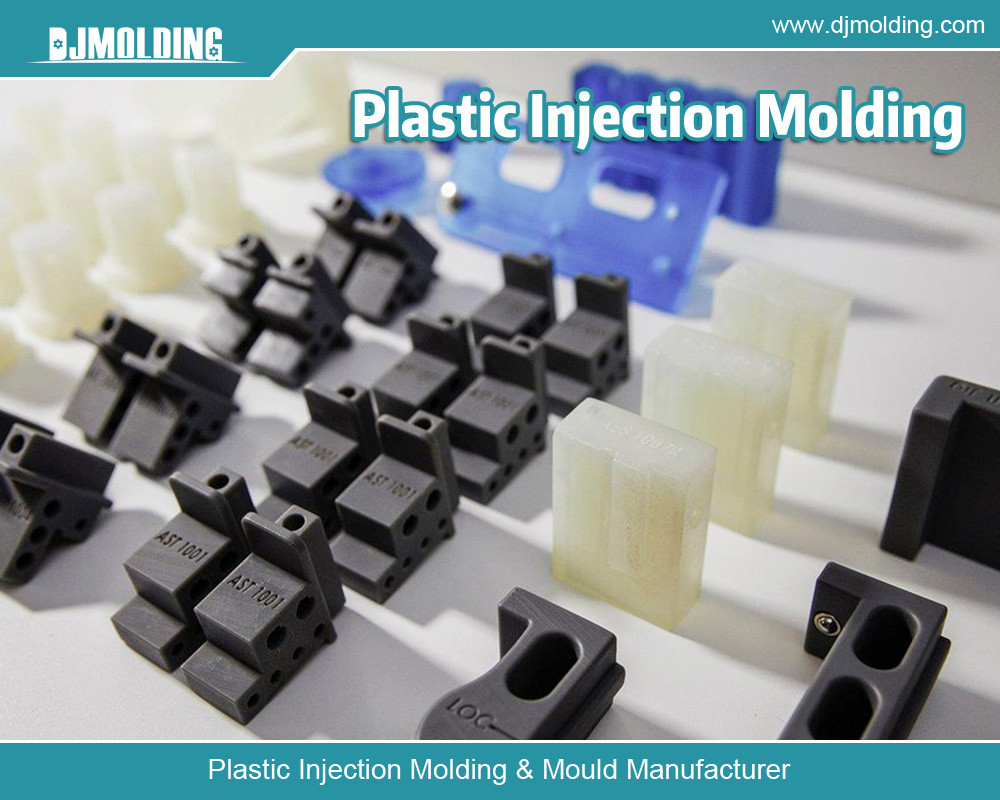
Conclusion
PVC injection molding is a vital process in modern manufacturing, offering a range of benefits and applications across various industries. By understanding the intricacies of the process and implementing best practices, manufacturers can harness the full potential of PVC to create high-quality products. While challenges exist, such as material sensitivity and environmental concerns, the advantages of PVC, including its durability and versatility, make it a compelling choice for many applications. As technology advances, the future of PVC injection molding looks promising, with opportunities for innovation and sustainable practices shaping the industry. Embracing these advancements will enable manufacturers to stay competitive and meet the evolving demands of consumers.
For more about pvc injection molding: a comprehensive guide, you can pay a visit to Djmolding at https://www.djmolding.com/complete-guide-to-pvc-injection-molding/ for more info.