Overmold Process In Injection Molding: A Comprehensive Guide
Overmold Process In Injection Molding: A Comprehensive Guide
Injection molding is a widely used manufacturing process in various industries, and one of its specialized techniques is over-molding. Overmolding, sometimes called two-shot molding or multi-material molding, combines two or more materials to create a single, integrated product. By fusing materials, over-molding enhances a product’s functionality, aesthetics, and durability. This guide explores the fundamentals, techniques, materials, applications, and advantages of the overmold process in injection molding.
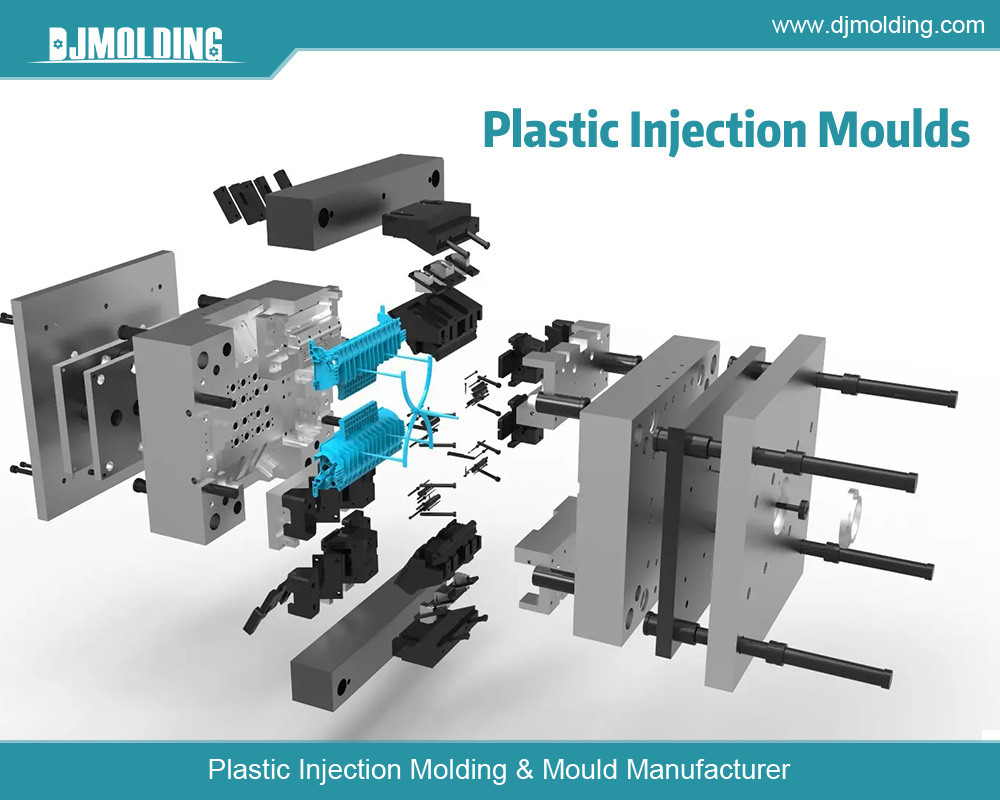
What is Overmolding?
Overmolding is an injection molding technique where one material is molded over another to create a single part. This process involves multiple injection steps, each adding a new material layer to the previously molded component. Overmolding provides flexibility in designing products with different physical, tactile, and functional attributes, often combining rigid and flexible materials.
The key concept of over-molding is effectively bonding dissimilar materials. A primary substrate (often a rigid thermoplastic) is molded initially, followed by a secondary layer of material molded over or around it. The goal is to strengthen the materials’ bond to enhance properties such as grip, aesthetics, insulation, and impact resistance.
Types of Overmolding:
- Insert Overmolding: In this type, a pre-fabricated part (metal or plastic) is inserted into the mold, and a different material is injected around it.
- Two-Shot (or Multi-Shot) Overmolding: This uses two or more injection cycles to create a bonded product with distinct layers of material. The mold is designed with two cavities for different materials, allowing each to be injected in sequence.
- The Overmolding Process: Step-by-Step
Understanding the over-molding process involves comprehending its key stages:
Step 1: Designing the Substrate Mold
The initial step in over-molding is designing the mold for the substrate material, which will form the core part of the final product. Engineers consider material compatibility, structural requirements, and mold orientation.
Step 2: First Injection
The substrate material, typically rigid plastic, is injected and molded into shape. It is later removed and placed into a second mold for over-molding. This substrate can stay in place when using multi-shot injection molding machines, moving automatically to the next cavity.
Step 3: Mold Transfer and Secondary Injection
Once the substrate cools and hardens, it’s placed in a second mold for the over-molding step, where the secondary material is injected. This step requires precision to ensure an even bond between the layers.
Step 4: Cooling and Final Product Ejection
After the second injection, the over-molded component cools to harden fully. Ejectors then remove the final product from the mold.
Equipment and Technology Involved:
Modern over-molding often employs specialized injection molding machines with multiple injection units, automatic transfer arms, and robotic systems that increase precision, efficiency, and repeatability.
Materials in Overmolding
Choosing compatible materials is critical for effective overmolding. Two primary material combinations are typically used: rigid/flexible and plastic/metal.
Thermoplastics
Commonly used as the substrate layer, thermoplastics provide structural support. Some popular choices include:
- Polypropylene (PP): Used for products requiring high flexibility.
- Polycarbonate (PC): Known for high impact resistance and strength.
- Acrylonitrile Butadiene Styrene (ABS): Excellent for consumer products needing durability.
- Polyethylene (PE): Lightweight and resistant to chemicals.
Elastomers and Thermoplastic Elastomers (TPEs)
These flexible materials are frequently used in over-molding to provide cushioning, grip, and ergonomic benefits. Examples include:
- Thermoplastic Polyurethane (TPU): Known for flexibility and chemical resistance.
- Silicone Rubber: Provides high-temperature resistance and flexibility.
- Thermoplastic Vulcanizates (TPVs): Blends rubber and plastic properties, making them suitable for automotive and medical applications.
Metal Inserts
Metal is sometimes used as an insert, typically in insert molding, to add strength, conductivity, or thermal properties to a plastic part.
Considerations for Material Compatibility:
Successful over-molding requires that the materials bond well without delamination. Compatibility testing often considers factors such as:
- Melting Point: Materials should have similar or compatible melting points.
- Chemical Compatibility: Materials must not degrade or chemically interact.
- Thermal Expansion Rates: Differing expansion rates can lead to cracking or deformation.
Applications of Overmolding in Different Industries
The versatility of over-molding makes it applicable across various industries. Here are some prominent applications:
Consumer Electronics
Overmolding is widely used in consumer electronics to improve aesthetics and functionality. For example, handheld devices often feature a soft TPE layer over a rigid plastic casing for better grip and impact resistance. Keyboards and phone cases also benefit from the dual-material design, which combines durability with user-friendly ergonomics.
Medical Devices
In the medical field, over-molding produces durable, easy-to-clean, and ergonomic devices. For instance, surgical instruments often incorporate rigid materials for structural support and elastomers for comfortable, non-slip grips. Overmolding ensures that medical devices remain functional under sterilization procedures and repeated use.
Automotive Industry
Automotive parts, such as buttons, grips, and interior panels, are commonly over-molded for aesthetic and functional purposes. For example, a steering wheel may incorporate a TPE layer over a hard plastic frame to enhance comfort and grip. Additionally, over-molding helps reduce noise by isolating metal parts with a flexible plastic layer.
Tooling and Industrial Equipment
Tools and equipment handles often incorporate over-molding for ergonomic benefits. Power tools, hand tools, and machinery controls typically have a soft layer over a rigid substrate, improving grip and minimizing user fatigue.
Household Goods and Personal Care Items
Household items such as toothbrushes, razors, and kitchen tools are often over-molded to combine functionality and aesthetics. For instance, a toothbrush’s soft grip areas provide comfort and a better grip, especially in wet conditions.
Advantages of the Overmold Process in Injection Molding
Over-molding is highly advantageous regarding product functionality, appearance, and durability. Here are some of its main benefits:
Enhanced Grip and Comfort
Adding a soft material layer to a rigid component improves grip and comfort. This is especially useful in handheld products requiring repeated handling, such as tools, medical instruments, and electronics.
Improved Product Durability
Overmolding adds an extra layer of protection, often making products more durable and resistant to impact, moisture, and chemical exposure. Overmolded components typically exhibit better longevity, even under harsh conditions.
Enhanced Aesthetic Appeal
Overmolding allows designers to combine multiple colors and textures, enhancing product aesthetics. Creating complex, multi-material designs provides a significant edge in consumer goods, where appearance and feel are crucial.
Cost Efficiency
Since over-molding combines two materials in a single process, it reduces the need for additional assembly or finishing processes. This can lead to reduced manufacturing costs, labor, and material waste.
Design Flexibility
Overmolding provides substantial design flexibility, enabling manufacturers to combine various materials and shapes within a single mold. This versatility is valuable in industries requiring customized or ergonomically designed products.
Challenges in Overmolding
While beneficial, the over-molding process has specific challenges that manufacturers must address:
Material Bonding
Achieving a solid bond between materials is essential. Poor bonding can result in delamination, where layers separate, compromising the product’s quality and durability.
Mold Design Complexity
Overmolding requires intricate mold designs, especially for multi-shot processes. The mold must accommodate multiple cavities for different materials and ensure precise alignment.
Temperature and Pressure Control
Since different materials may have varying melting points and expansion rates, carefully controlling temperature and pressure is critical to avoid warping or other defects.
Cycle Time and Production Cost
Due to the additional steps, over-molding can increase cycle time, leading to higher production costs. However, this can be offset by reduced post-processing and assembly needs.
Material Compatibility Testing
Extensive testing ensures materials bond well and perform under intended conditions. Unexpected interactions between materials can arise, causing compatibility issues.
Future Trends and Innovations in Overmolding
As technology and materials advance, over-molding continues to evolve with new possibilities:
Sustainable Materials and Processes
With the rise in environmental consciousness, there is a growing demand for sustainable materials in over-molding. Recyclable thermoplastics, biodegradable polymers, and bio-based elastomers are becoming more prominent in manufacturing processes.
Miniaturization in Electronics
As electronic devices shrink, the over-molding process adapts to produce smaller, more precise components. Innovations in micro-over-molding make it possible to encapsulate delicate electronic circuits, sensors, and microchips, enhancing durability without adding bulk.
Advancements in Automation
Robotic automation and AI are transforming the over-molding process, enabling more precise control and reducing errors. Automated systems now manage transfer, temperature control, and bonding strength, improving efficiency and consistency in production.
Customization and Personalization
Additive manufacturing (3D printing) and over-molding allow for highly customized products, especially in the medical, automotive, and consumer electronics industries. Hybrid manufacturing processes enable rapid prototyping and on-demand production.
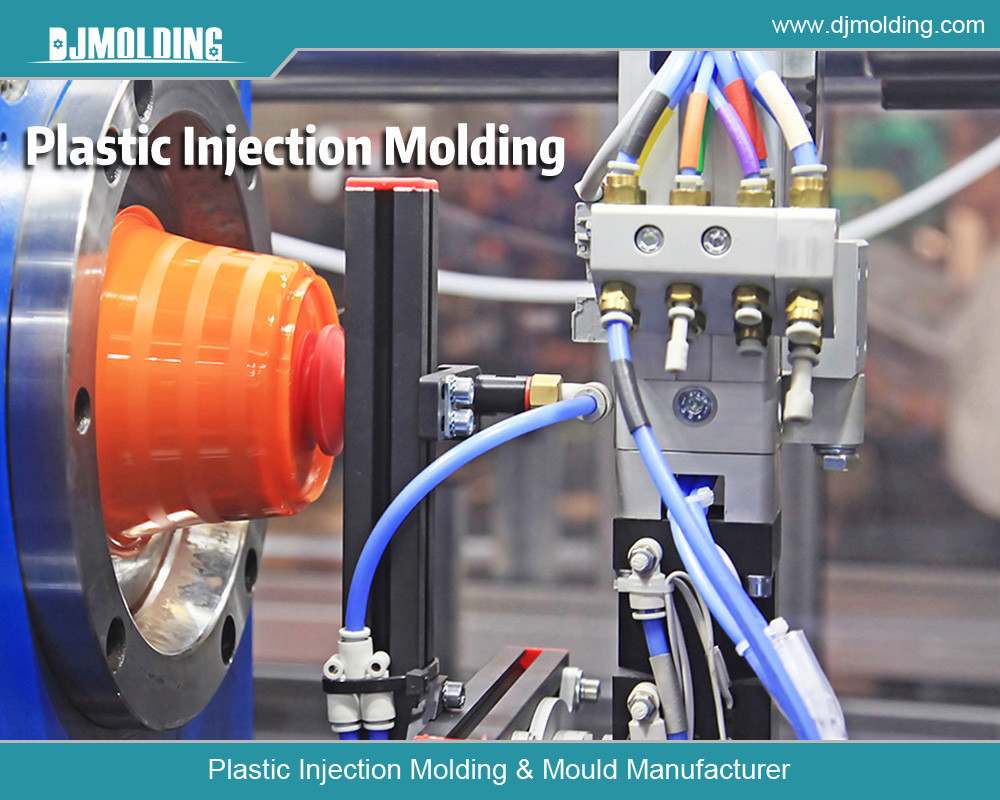
Conclusion
The over-mold process in injection molding is a versatile and highly beneficial manufacturing technique that caters to various industries. Overmolding enables the production of durable, ergonomic, and aesthetically appealing products, from consumer electronics to medical devices. However, carefully considering material compatibility, mold design, and bonding strength is required; over-molding offers unmatched functionality and cost-efficiency advantages.
With advancements in materials, automation, and sustainability, the over-molding process is poised to play an even more significant role in modern manufacturing. Overmolding will likely remain a pivotal process for creating high-quality, multi-functional products as industries continue to seek innovative ways to enhance product design.
For more about the overmold process in injection molding: a comprehensive guide, you can pay a visit to Djmolding at https://www.djmolding.com/overmolding/ for more info.