Complete Guide To HDPE Injection Molding
Complete Guide To HDPE Injection Molding
High-density polyethylene (HDPE) is one of the most commonly used plastics in the world. It is renowned for its strength, flexibility, and resistance to impact and chemicals. These properties make it ideal for a variety of applications, from household products to industrial components. This guide provides an in-depth look at HDPE injection molding, including its process, advantages, applications, and considerations for successful implementation.
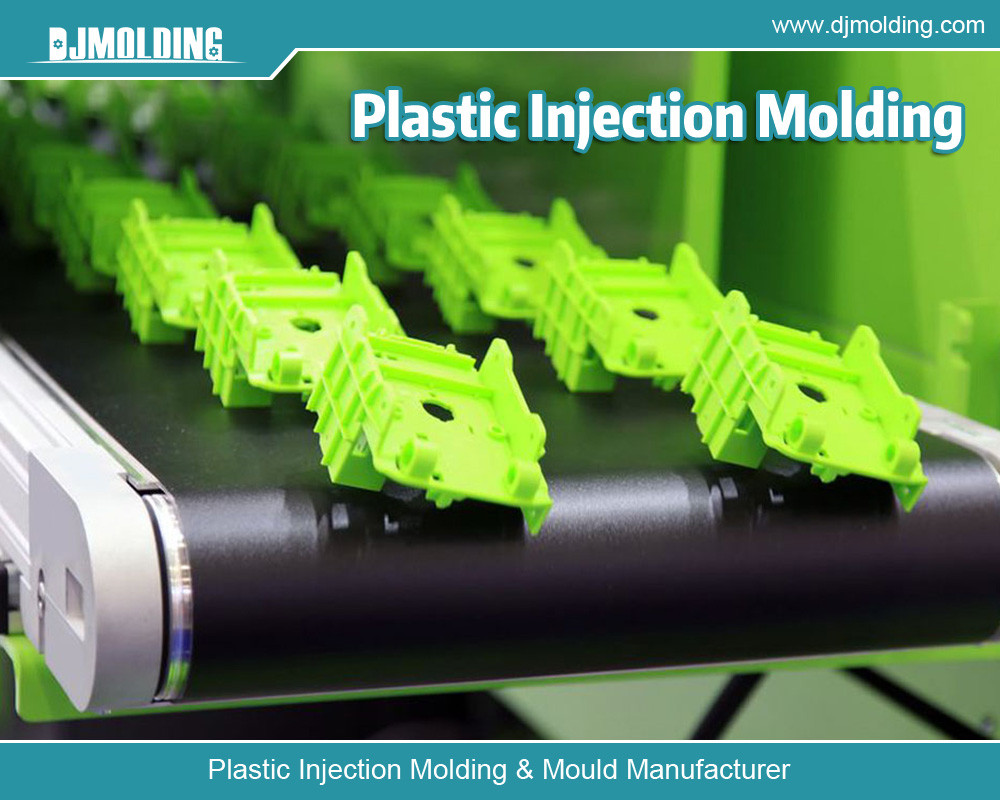
What is HDPE?
Characteristics of HDPE
HDPE is a thermoplastic polymer made from petroleum. It has several distinctive characteristics that contribute to its widespread use:
- High Strength-to-Density Ratio: HDPE is strong and lightweight, making it suitable for various applications.
- Chemical Resistance: It is resistant to many chemicals, making it a preferred choice for containers and piping in chemical processing industries.
- Low Moisture Absorption: This characteristic makes HDPE suitable for outdoor applications, as it resists degradation from moisture.
- UV Resistance: HDPE can withstand exposure to UV rays without significant degradation, making it ideal for outdoor use.
- Recyclability: HDPE is recyclable, which makes it an environmentally friendly option.
Common Applications of HDPE
Due to its favorable properties, HDPE is used in various applications, including:
- Packaging: HDPE is commonly used for bottles, containers, and plastic bags.
- Construction: It is utilized in piping systems, geomembranes, and plastic lumber.
- Automotive: HDPE is used in fuel tanks, bumpers, and interior parts.
- Consumer Goods: Items like toys, kitchenware, and furniture often incorporate HDPE.
The Injection Molding Process
Overview of Injection Molding
Injection molding is a manufacturing process that involves injecting molten plastic into a mold to create a specific shape. Due to its efficiency and repeatability, it is widely used for producing large quantities of parts.
Steps in the Injection Molding Process
- Material Preparation: HDPE pellets are dried to remove moisture, which can affect the quality of the final product.
- Injection Phase:
- Heating: The HDPE is heated to its melting point (approximately 180-220°C) in a barrel.
- Injection: The molten HDPE is injected into the mold at high pressure.
- Cooling Phase: The material cools and solidifies in the mold, taking on its shape.
- Ejection Phase: Once cooled, the mold opens, and the finished part is ejected.
- Post-processing may include trimming, surface finishing, or additional assembly steps.
Types of Injection Molding
Several types of injection molding processes can be used for HDPE:
- Conventional Injection Molding: The standard method used for most HDPE products.
- Gas-Assisted Injection Molding: Uses gas to create hollow sections in parts, reducing weight and material usage.
- Multi-Shot Injection Molding: Involves injecting two or more materials or colors into the same mold to create multi-material products.
Advantages of HDPE Injection Molding
Cost Efficiency
HDPE injection molding is cost-effective for large production runs due to its low material costs and minimal waste. The process also reduces labor costs since it is highly automated.
Versatility in Design
Injection molding allows for complex shapes and intricate designs that would be difficult or impossible to achieve with other manufacturing processes. HDPE’s flexibility means it can be molded into a wide range of products.
High Production Speed
The speed of the injection molding process enables manufacturers to produce large quantities of parts quickly. This is particularly advantageous for industries that require rapid production cycles.
Consistent Quality
Injection molding provides high precision and uniformity in the production of parts, ensuring consistent quality across large production runs. This minimizes defects and reduces waste.
Considerations for HDPE Injection Molding
Mold Design
The design of the mold is critical for successful injection molding. Key considerations include:
- Draft Angles: Incorporating draft angles helps with the easy ejection of parts from the mold.
- Cooling Channels: Properly designed cooling channels ensure uniform cooling and minimize cycle times.
- Gate Design: The location and size of the gate (where the plastic enters the mold) can affect the quality and appearance of the final product.
Processing Conditions
The following processing conditions should be monitored:
- Temperature: Maintaining the correct temperature for melting and molding is crucial to achieving the desired properties.
- Injection Speed: The speed at which the material is injected can affect the part’s final properties, including strength and appearance.
- Cooling Time: Adequate cooling time is necessary to ensure the part is fully solidified before ejection.
Material Selection
Choosing the correct grade of HDPE is essential for achieving the desired properties of the final product. Different grades offer varying levels of strength, flexibility, and chemical resistance. Factors to consider include:
- Impact Resistance: A high-impact resistance grade should be selected for products that will undergo stress or impact.
- Processing Conditions: Some grades may require different processing temperatures or conditions.
Environmental Considerations
While HDPE is recyclable, proper waste management practices should be in place. Implementing recycling programs for HDPE waste generated during production can enhance sustainability efforts.
Applications of HDPE Injection Molding
Packaging
HDPE is widely used in the packaging industry for products such as:
- Bottles: Milk, detergent, and other liquid products are commonly packaged in HDPE bottles due to their durability and chemical resistance.
- Containers: Food storage containers made from HDPE are famous for their moisture barrier properties.
Automotive Components
The automotive industry utilizes HDPE for various components, including:
- Fuel Tanks: HDPE’s chemical resistance makes it suitable for storing fuel safely.
- Interior Parts: Panels, trim, and other components benefit from HDPE’s lightweight and durable characteristics.
Consumer Products
HDPE is prevalent in consumer goods, including:
- Toys: The safety and durability of HDPE make it an ideal choice for children’s toys.
- Kitchenware: Cutting boards, utensils, and storage containers are often made from HDPE due to their ease of cleaning and resistance to bacteria.
Industrial Applications
In industrial settings, HDPE injection molding is used for:
- Piping Systems: HDPE pipes are used in water distribution and drainage systems due to their strength and resistance to corrosion.
- Geomembranes: HDPE geomembranes provide excellent impermeability in landfills and environmental protection applications.
Challenges in HDPE Injection Molding
Material Shrinkage
HDPE tends to shrink during cooling, which can lead to dimensional inaccuracies in the final product. Proper mold design and processing conditions must be established to minimize this issue.
Warping and Deformation
Parts may warp or deform if cooling is not uniform or the part design is not optimized. To prevent this, it is essential to ensure the mold is designed to allow for even cooling.
Color and Finish Consistency
Achieving consistent color and surface finish can be challenging, especially when using recycled HDPE or when different batches are processed. Manufacturers should establish stringent quality control measures to ensure uniformity.
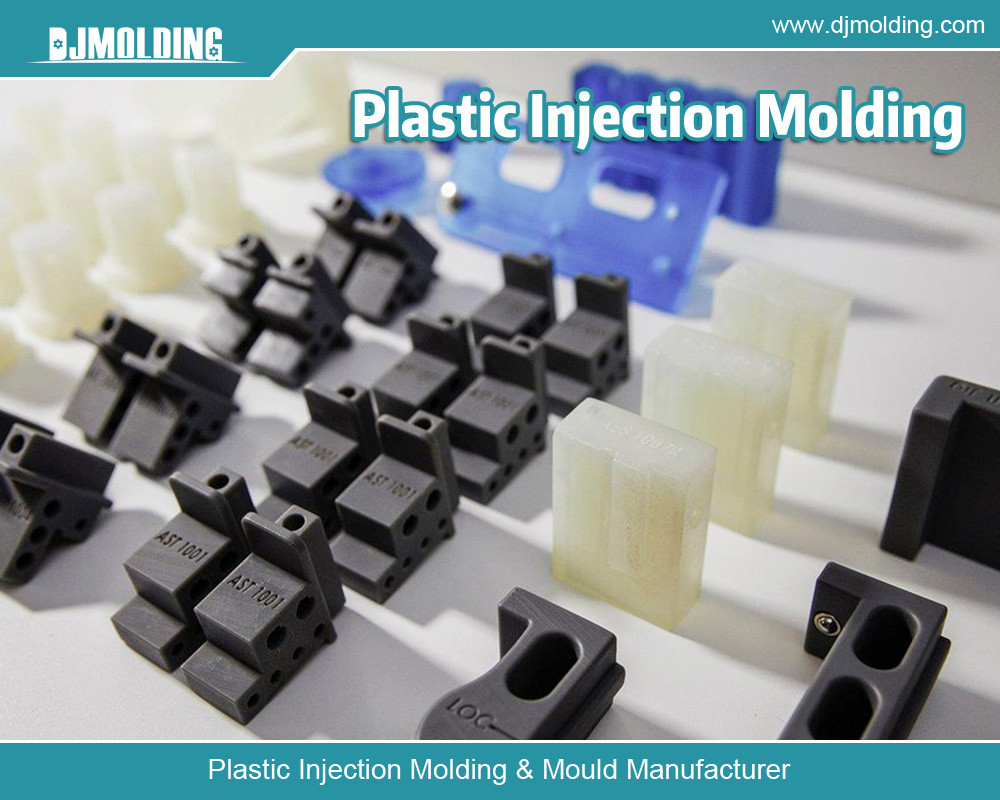
Conclusion
HDPE injection molding is a versatile and efficient manufacturing process that offers numerous benefits, including cost-effectiveness, design flexibility, and consistent quality. With its wide range of applications across industries, HDPE remains a preferred choice for manufacturers. However, to achieve optimal results, it is crucial to consider factors such as mold design, processing conditions, and material selection. By understanding these elements, manufacturers can successfully leverage HDPE injection molding to produce high-quality products that meet customers’ demands.
By harnessing HDPE’s full potential and the injection molding process, businesses can innovate and create various products that meet market needs and contribute to a sustainable future.
For more about the complete guide to hdpe injection molding, you can pay a visit to Djmolding at https://www.djmolding.com/ for more info.