Different Types Mold Textures In Plastic Injection Molding
Different Types Mold Textures In Plastic Injection Molding
Plastic injection molding is a process that shapes raw plastic into various forms and is widely used in industries ranging from automotive to consumer goods. Mold texturing plays a crucial role in its techniques, influencing the aesthetics and functionality of the molded parts. Mold textures can mimic a variety of surfaces, from smooth to intricate patterns, which adds value by enhancing a product’s tactile and visual experience. This article dives into the significance, types, applications, benefits, and challenges associated with mold textures in plastic injection molding.
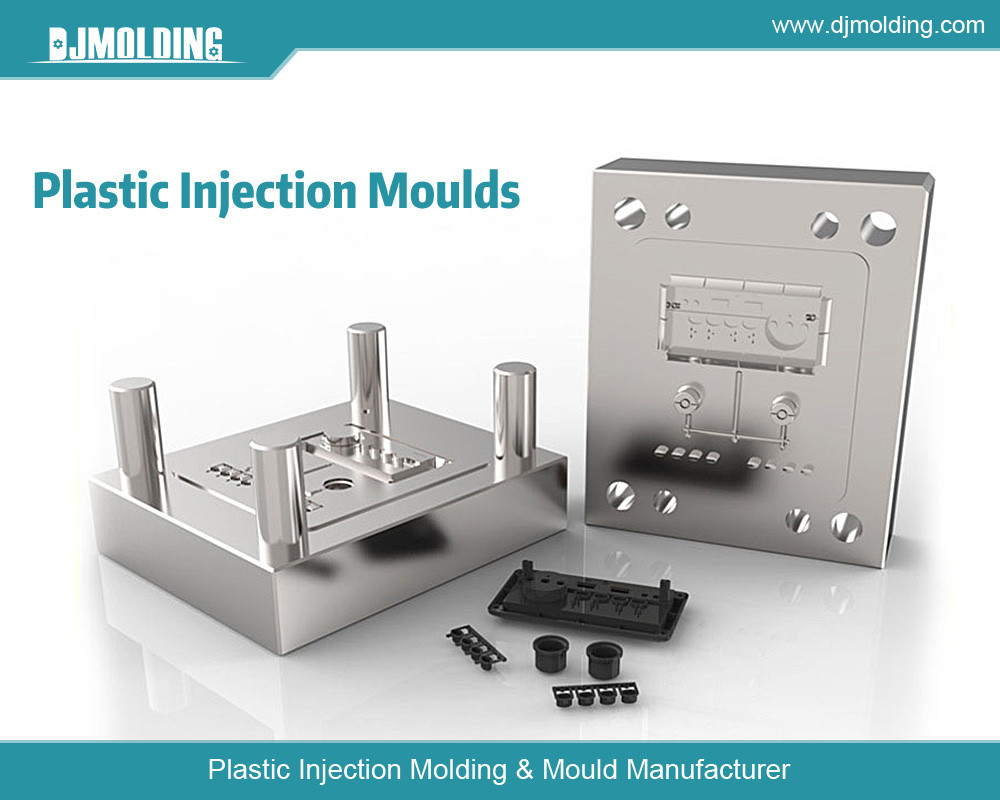
Importance of Mold Textures in Plastic Injection Molding
Mold textures are created through different methods, which we will explore. These methods have evolved to accommodate modern needs in plastic molding. The texture affects the appearance and performance of a molded component, often making it more desirable to end-users.
Aesthetic Appeal:
Mold textures enhance a product’s aesthetic by introducing patterns that mimic wood, leather, or metal. This can help give a product a more polished or unique look. Textures also add color depth to plastics, making them appear more sophisticated and expensive than they might otherwise be in their raw form.
Functional Advantages:
Mold textures impact more than just appearance; they can also improve a part’s functionality. For example, some textures reduce gloss and reflection, an essential feature for products exposed to sunlight, such as automotive dashboards. Additionally, textures improve grip on products like tool handles and smartphone cases by introducing friction to prevent slippage.
Durability and Concealment of Imperfections:
Textures can help mask minor imperfections, such as scratches or scuffs, which are inevitable in daily use. By masking these imperfections, the product retains a newer look for longer, which benefits customer-facing industries.
Types of Mold Textures in Plastic Injection Molding
Various mold textures are available in plastic injection molding, each suited for different applications and desired effects. Below are some common categories:
- Glossy/Smooth Textures:
These are often created through high polishing techniques and provide a mirror-like finish. High-gloss finishes are commonly used in automotive, electronics, and medical applications, where smooth surfaces are essential. However, they may show fingerprints and scratches more readily.
- Matte and Satin Finishes:
Matte textures are non-reflective and offer a softer appearance. They’re widely used in consumer goods like electronic housings and household items, as they have an understated elegance and are less likely to show wear over time.
- Textured Patterns:
These patterns include fine to coarse grains, cross-hatching, and intricate designs that mimic natural materials (like leather or wood) or add a unique appearance to the plastic part. These patterns can help a product stand out visually while adding functionality, such as improved grip.
- Functional Textures:
Some textures are engineered for specific purposes, like reducing friction or enhancing a part’s grip. These textures are typical in industrial and medical applications, where functionality is critical. For example, tool handles may feature textured surfaces to ensure a secure grip even in slippery conditions.
- Decorative Textures:
These textures aim to add artistic or aesthetic value to the molded part. They may feature logos, intricate designs, or brand elements. Decorative textures are widely used in high-end consumer goods and fashion accessories.
Methods for Creating Mold Textures
Adding texture to a mold requires specialized techniques, and several methods are commonly used, depending on the desired finish and the material of the mold. Here are the most prevalent methods:
- Chemical Etching:
Chemical etching is one of the most popular methods for texturing molds. The mold surface is coated with resistant material in this process, and specific areas are exposed to acid or other etching agents. The result is a uniform pattern or texture. This technique is particularly suitable for intricate designs and delicate textures, making it widely used for creating grained or matte finishes.
- EDM (Electrical Discharge Machining):
EDM involves using electrical discharges to erode the mold’s surface in a controlled manner. This technique helps create deep textures and complex patterns that would be challenging to achieve with other methods. EDM is often used to create textures that require high precision and consistency across multiple parts.
- Laser Engraving:
Laser engraving has gained popularity due to its precision and versatility. It uses a laser to etch patterns directly onto the mold surface, allowing for intricate and highly detailed designs. Laser engraving offers quick adjustments, making it ideal for prototyping and customization.
- Sandblasting and Shot Blasting:
These abrasive techniques involve blasting the mold surface with small particles, creating a consistent rough texture. While unsuitable for intricate patterns, sandblasting efficiently achieves matte finishes and enhances grip on plastic parts.
- Hand Engraving:
Though labor-intensive, hand engraving offers a personalized touch ideal for unique or low-volume parts. Skilled engravers can create custom designs that may be difficult to replicate with automated techniques.
Applications of Mold Textures Across Industries
Mold textures play a vital role in various industries, offering both functional and aesthetic benefits tailored to specific applications:
Automotive Industry:
In automotive manufacturing, mold textures are crucial for interior and exterior components. The interior dashboard, for instance, often uses a matte texture to reduce glare and reflection. Additionally, door panels, seat trims, and control knobs may feature patterns that simulate leather or other premium materials, providing a tactile experience for the user.
Consumer Electronics:
Electronics, especially handheld devices like smartphones, tablets, and remote controls, benefit from textured surfaces. These textures can help prevent fingerprint marks on the surface and improve grip. For instance, a matte texture on a phone case or remote control can offer an elegant look while making the product comfortable.
Household Goods:
Kitchen utensils, storage containers, and other household goods frequently employ mold textures. Textures enhance functionality by providing slip resistance or improving the visual appeal of products like plastic cups, trays, or appliance parts.
Medical Devices:
In the medical field, textured molds are used for devices and tools that can be easily gripped without slipping, particularly in surgical and diagnostic equipment. Textures also enhance the aesthetic appearance of prosthetics and patient-specific products.
Industrial and Tooling Equipment:
Textured mold finishes are applied to industrial tools and equipment where grip and durability are critical. For instance, tool handles or grips often feature textured patterns to improve functionality and reduce wear over time, which is vital for heavy-duty applications.
Benefits of Mold Textures in Plastic Injection Molding
Incorporating mold textures into plastic injection molding offers numerous benefits, ranging from improved aesthetics to enhanced product performance:
Enhanced Product Appeal:
Textures can transform a simple plastic part into a high-quality product that appeals to consumers. A well-chosen texture can elevate a product’s look, making it more appealing and marketable.
Improved Functionality:
Textures can reduce glare, add friction, or provide slip resistance, making them essential for products in challenging environments. This functionality extends a product’s usability, especially in applications like automotive interiors or industrial tools.
Durability and Scratch Resistance:
Textures can help conceal minor scratches and imperfections during usage, which is advantageous for consumer products and industrial tools. By masking these blemishes, the product maintains a newer appearance for longer.
Reduced Maintenance:
Textures are often easier to maintain, as they do not show fingerprints, smudges, or minor scratches as prominently as smooth surfaces. For instance, matte finishes in automotive interiors require less frequent cleaning, adding convenience for end-users.
Cost-Effective Customization:
With advancements in laser engraving and other texturing technologies, molds can be customized relatively quickly and affordably. This means that manufacturers can produce unique designs without significantly increasing production costs, making mold texturing a versatile and cost-effective option.
Challenges and Considerations in Mold Texturing
While mold texturing offers many benefits, there are challenges and considerations manufacturers must address:
Precision in Texture Application:
Achieving consistent texture across multiple parts can be challenging, particularly with intricate designs. Minor deviations can result in visual or functional inconsistencies. Therefore, selecting the appropriate method (such as laser engraving or EDM) and skilled operators is essential for high precision.
Material Selection:
Different plastic materials respond differently to mold textures. For example, some materials may be more prone to shrinkage or warping when exposed to certain textures. Choosing a material that complements the desired texture is essential to achieve optimal results.
Tool Maintenance:
Textured molds require regular maintenance, as textures can wear down over time. This is especially true for high-volume production. Abrasive surfaces can accumulate residue, leading to a loss of detail in the texture, so regular cleaning and refurbishment are necessary to maintain the mold’s performance.
Higher Initial Costs:
Creating molds with textures and incredibly complex patterns can involve higher initial costs due to specialized equipment and skilled labor. However, these costs can be offset by the added value the textures bring to the product.
Mold Release Issues:
Textured molds may sometimes create challenges during demolding. Certain textures can cause the plastic part to stick more readily, leading to possible surface damage. To prevent this, mold release agents or specialized mold designs may be needed.
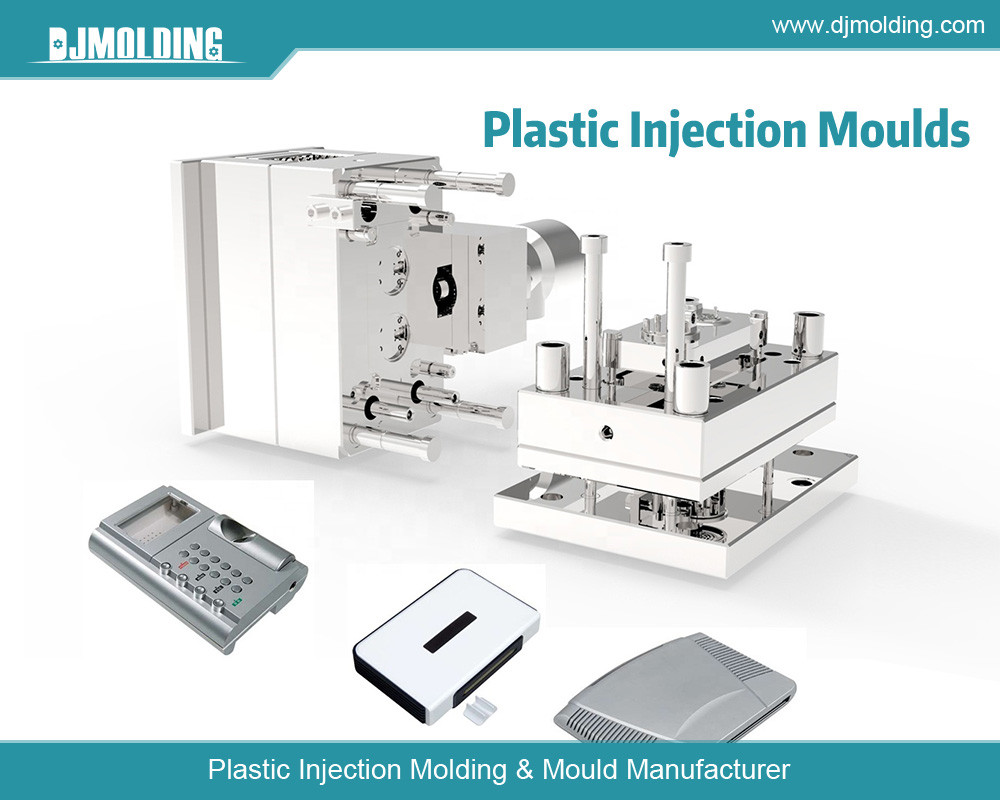
Conclusion
Mold textures in plastic injection molding are a powerful tool manufacturers use to enhance their products’ appearance, functionality, and longevity. With options ranging from smooth, glossy finishes to intricate, functional patterns, mold texturing techniques are versatile and adaptable across industries. However, the process requires careful consideration, from choosing the proper texturing method and material compatibility to managing tool maintenance and costs.
By balancing aesthetics and practicality, mold textures offer a valuable means to meet consumer demands and create products that stand out in a competitive market. As technology advances, so will the possibilities of mold texturing, enabling even more sophisticated designs and applications across diverse industries.
For more about the different types mold textures in plastic injection molding, you can pay a visit to Djmolding at https://www.djmolding.com/ for more info.