Complete Guide To Thermoplastic Elastomers (TPE) for Injection Molding
Complete Guide To Thermoplastic Elastomers (TPE) for Injection Molding
Thermoplastic Elastomers, or TPEs, are a simple combination of polymers with thermoplastic and elastomers elements. In commercial sectors, they were introduced in 1960. TPEs are polymers according to their characteristics. The melted thermoplastic material is injected into a mold cavity to form a unique shape in this injection molding manufacturing process. TPEs are a unique type of polymer with both plastic and rubber properties, which makes them suitable for any application that needs both flexibility and strength. After the molding process, the molded part may have a wide range of physical and mechanical properties, which depend on the specific TPE material used and the molding conditions. So many industries, such as automotive, consumer goods, and medical devices, use injection molding in the TPE manufacturing process.
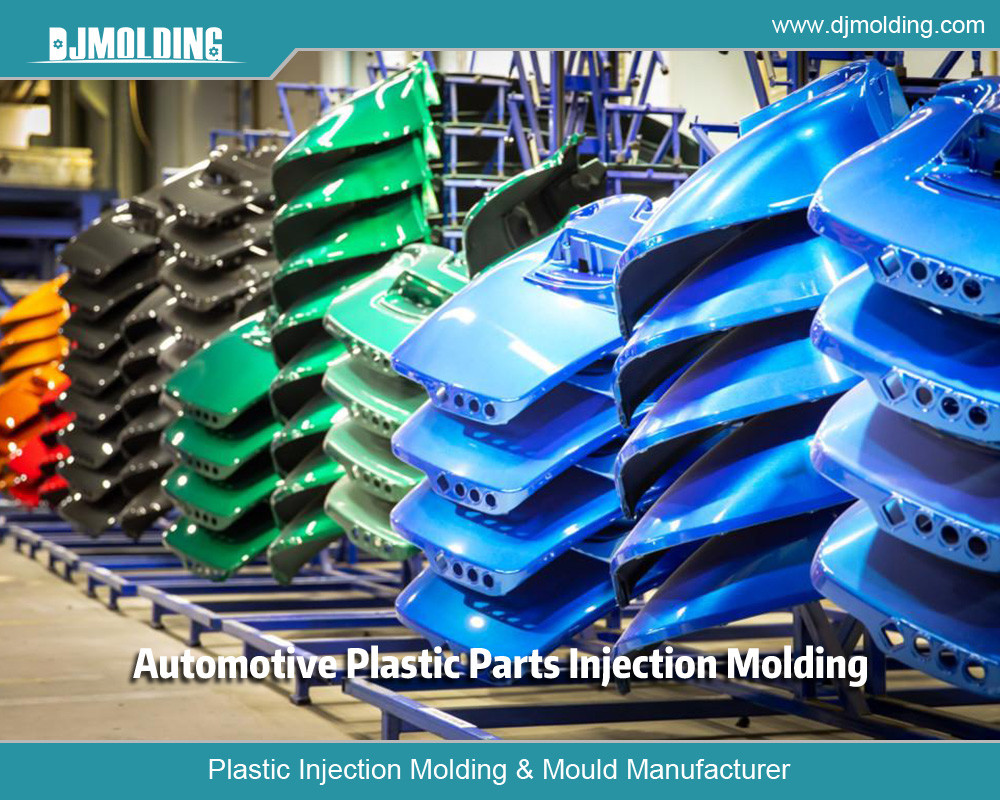
Key Features of Thermoplastic Elastomers (TPE) :
According to its unique characteristics, Thermoplastic Elastomers (TPEs) are a perfect manufacturing process for injection molding. It is a Dynamic class of polymers that includes rubber characteristics and plastics’ process ability, Making the injection molding applications ideal for every process. Here, we will discuss the main features of TPEs and mention their significance and benefits among various manufacturing processes:
- Flexibility and Elasticity: TPEs, like rubber, have exceptional flexibility and elasticity. This allows them to be used in various applications, from seals and gaskets to soft-touch grips. TPEs can return to their original shapes after deformation, which makes them suitable for maintaining products requiring resilience and durability.
- Processability: Compared to traditional elastomers, TPEs are easily produced using standard plastic molding methods, such as injection molding. Because of this processing ease, complex forms and high-precision components can be produced efficiently.
- Recyclability: TPEs are completely recyclable, which is in line with escalating environmental laws and eco-friendly activities. This quality allows for material reuse, which promotes a circular economy and reduces waste.
- Thermal Stability: TPEs provide stability in high- and low-temperature situations by maintaining their characteristics throughout a broad temperature range. Applications subjected to a range of temperature environments depend on this thermal durability.
- Chemical Resistance: Many TPEs are resistant to solvents, oils, and chemicals, making them appropriate for use in harsh conditions where regular exposure to these substances is expected.
- Aesthetic Versatility: TPEs are flexible. They can be easily colored and customized for product design and aesthetics, allowing manufacturers to create visually appealing products while maintaining the material’s functional properties.
Key Characteristics of TPE
- Elasticity: TPEs exhibit high elasticity, allowing them to stretch and return to their original shape.
- Processability: They can be processed using standard plastic manufacturing techniques such as injection molding, extrusion, and blow molding.
- Recyclability: TPEs can be remelted and reprocessed, making them more environmentally friendly than traditional rubber.
- Chemical Resistance: TPEs offer good resistance to chemicals, oils, and weathering, making them suitable for various applications.
- Soft Touch: The soft and flexible nature of TPEs makes them ideal for products that require a comfortable grip or contact surface.
Types of Thermoplastic Elastomers
TPEs are classified into several types based on their chemical composition and structure. Each type has its unique properties, making it suitable for specific applications.
Styrenic Block Copolymers (TPE-S or TPS)
- TPE-S is one of the most commonly used types of TPE. It consists of rigid styrene and soft elastomeric blocks, balancing rigidity and elasticity. TPE-S is often used in consumer products, automotive parts, and packaging materials.
Thermoplastic Polyolefins (TPE-O or TPO)
- TPE-O is a blend of polypropylene (PP) and elastomeric materials. This type of TPE offers excellent impact resistance, making it ideal for automotive applications, particularly in bumper systems and interior components.
Thermoplastic Vulcanizates (TPE-V or TPV)
- TPE-V is a blend of thermoplastic and cross-linked rubber. This type is known for its superior heat resistance and durability. TPE-V is commonly used in automotive seals, hoses, and other applications where long-term performance is critical.
Thermoplastic Polyurethanes (TPE-U or TPU)
- TPE-U is known for its exceptional abrasion resistance and flexibility. It is often used in applications that require high wear resistance, such as footwear, cables, and sporting goods.
Thermoplastic Copolyester (TPE-E or TPC)
- TPE-E offers excellent chemical resistance and mechanical properties. It is commonly used in demanding applications such as automotive components, industrial belts, and hoses.
Thermoplastic Polyamides (TPE-A or TPA)
- TPE-A, also known as thermoplastic elastomer amides, combines the flexibility of rubber with the strength and rigidity of nylon. It is widely used in automotive, electrical, and industrial applications requiring high performance.
Advantages of Using TPE in Injection Molding
TPEs offer numerous advantages when used in injection molding processes, making them a preferred choice for many manufacturers across various industries.
Design Flexibility
- TPEs allow for intricate designs with complex geometries, which can be challenging to achieve with traditional rubber. The material’s flowability during injection molding enables precise and detailed molding.
Cost-Effective Production
- The reprocessability of TPEs reduces material waste, leading to cost savings in production. Additionally, using the same molds for multiple production runs further enhances cost efficiency.
Shorter Cycle Times
- TPEs typically have shorter cycle times than thermoset rubbers, as they do not require curing. It reduces overall production time, increasing manufacturing throughput.
Material Versatility
- The wide range of TPE types allows manufacturers to select the most suitable material for their specific application. A TPE fits the bill, whether it’s high abrasion resistance, chemical resistance, or softness.
Enhanced Product Performance
- Products made from TPE often exhibit superior performance characteristics, such as improved grip, flexibility, and durability. This makes them ideal for consumer products that require a soft touch or ergonomic design.
Environmental Benefits
- TPEs are recyclable and can be reprocessed without significant loss of material properties. It contributes to sustainability efforts by reducing waste and promoting circularity in manufacturing.
Best Practices for Injection Molding with TPE
It is essential to follow best practices that consider the material’s unique properties to achieve optimal results when using TPEs in injection molding.
Material Selection
- Choosing the right TPE type is critical to achieving the desired product performance. When selecting the appropriate TPE, consider factors such as elasticity, chemical resistance, temperature resistance, and hardness.
Mold Design
- The mold design should accommodate the flow characteristics of TPEs. Ensure that the mold has appropriate venting to prevent air traps and that the gate design allows for even material distribution.
Processing Conditions
- TPEs typically require lower processing temperatures compared to traditional thermoplastics. Monitor the processing temperature, injection pressure, and cooling time to prevent defects such as warping or sink marks.
Tooling Maintenance
- Regular maintenance of the injection molding equipment is crucial to prevent contamination and ensure consistent product quality. Clean the mold cavities and tooling surfaces to avoid residue buildup that could affect the molding process.
Quality Control
- Implementing strict quality control measures ensures the final product meets the required specifications. Regularly inspect the molded parts for flashing, warping, or incomplete filling defects.
Reprocessing and Recycling
- TPEs can be reprocessed and recycled, making them a sustainable option for injection molding. Collect and reprocess scrap material to reduce waste and improve overall material efficiency.
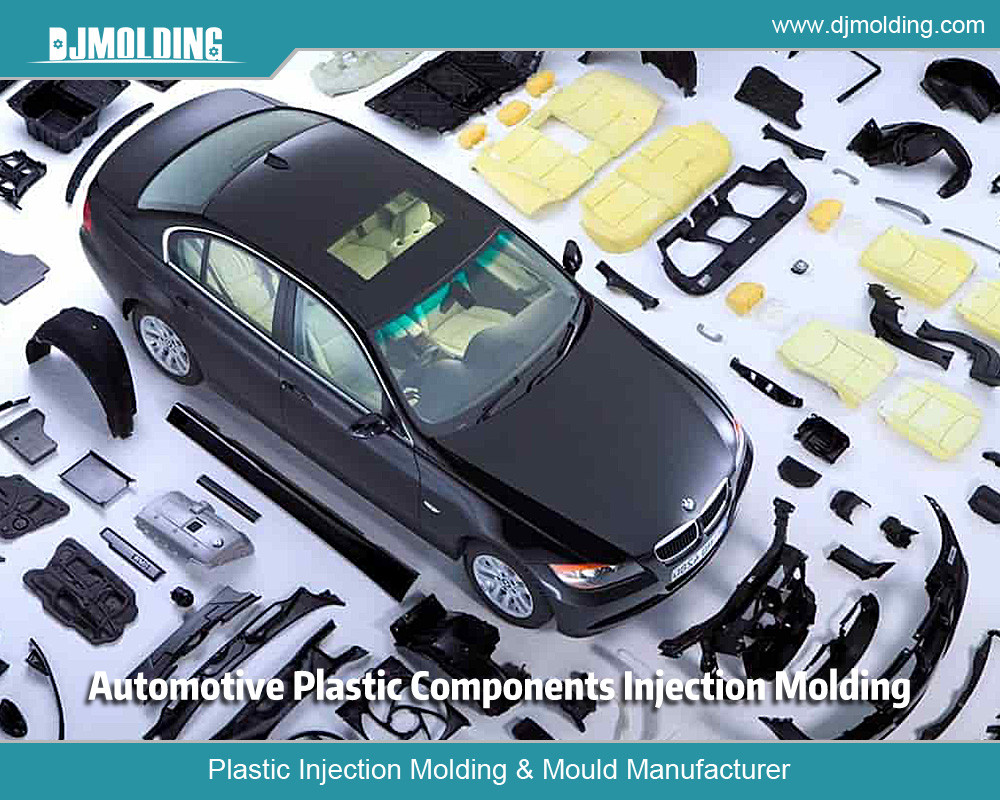
Conclusion
Thermoplastic Elastomers (TPE) are an incredibly versatile and valuable material for injection molding, offering a unique combination of flexibility, durability, and processability. Their ability to be molded into complex shapes and their environmental benefits make them an increasingly popular choice across various industries. Manufacturers can optimize their processes and produce high-quality, cost-effective products by understanding the different types of TPEs, their advantages, and best practices for injection molding.
For more about the complete guide to thermoplastic elastomers (tpe) for injection molding, you can pay a visit to Djmolding at https://www.djmolding.com/who-are-thermoplastic-elastomers-tpe-injection-molding-manufacturers/ for more info.