Complete Guide To PVC Injection Molding
Complete Guide To PVC Injection Molding
PVC injection molding is an essential method in the manufacturing sector. It is renowned for creating plastic parts with efficiency and adaptability. This article describes the intricacies of PVC injection molding, from the primary process to advanced considerations, applications, and emerging trends. When you are a newcomer to this field, knowing how to maximize PVC injection molding for your project and explore future trends is helpful.
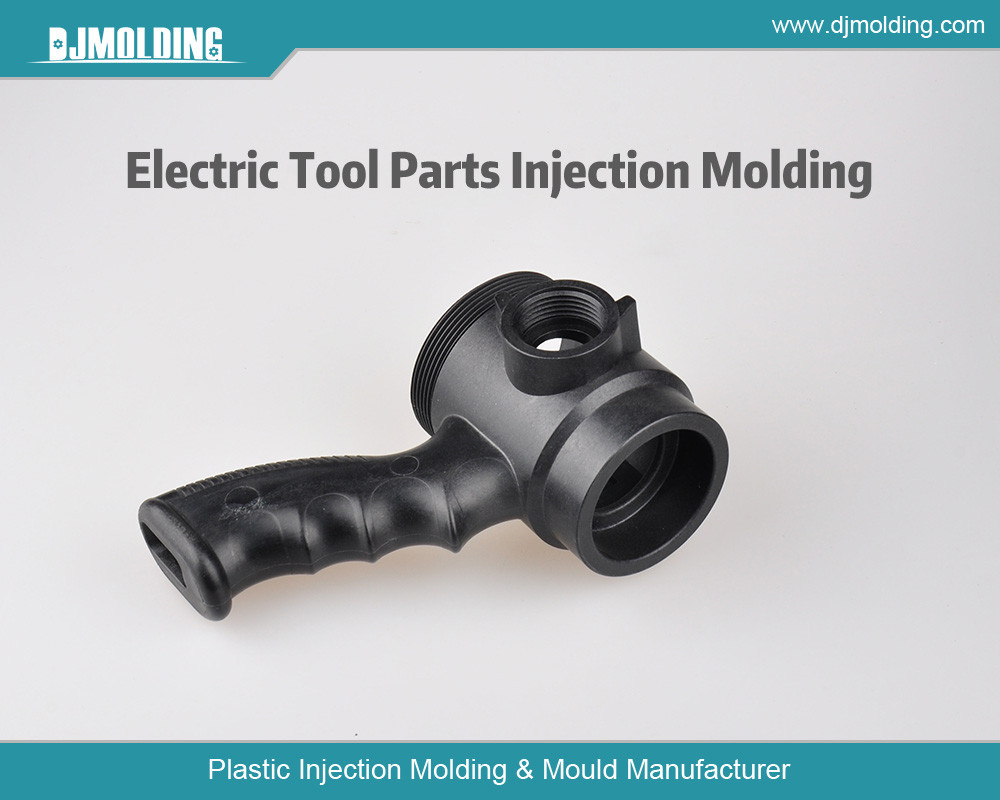
What is PVC Injection Molding?
PVC injection molding is a widely used manufacturing process that creates precise and intricate plastic components. The operator places PVC (polyvinyl chloride) pellets into an injection molding machine to begin the procedure. These pellets are heated inside the machine, which makes them easier to move around. After that, molten PVC is compressed under intense pressure into a specially created mold. The mold’s precise engineering ensures high precision and reliability when forming the finished product into the correct shape.
After the PVC has filled the mold cavity, it is cooled and solidified, assuming the mold’s shape. The part’s size and detail affect how long it takes to cool. Once it has cooled, the mold opens to release the completed part. This procedure makes high-volume manufacture of parts with specifics and reliable quality possible.
PVC injection molding is preferred due to its affordability and adaptability. PVC is a thermoplastic plastic that may be treated with different chemicals to give it particular qualities like strength, softness, or capacity to UV and chemical attack. PVC is widely utilized because of its versatility and the injection molding technique’s effectiveness in several industries.
Advantages of PVC Injection Molding
PVC injection molding offers several important advantages, making it a popular choice for manufacturing a wide range of plastic components.
- Suitable and Consistency: It is ideal for producing high-quality parts. Large production runs of the same part can be made consistently since each injection cycle can copy it with little to no variance.
- Effectiveness: PVC injection molding is highly effective and fast in producing large numbers of parts. Due to fast cycle durations and automation capabilities, production time is lower, and total output is increased.
- Variety: The varieties of PVC allow different additions to change its characteristics. Because of its various uses, heat retardancy, impact resistance, and UV stability, PVC can be used in multiple applications, from building supplies to medical devices.
- Affordability: PVC injection molding is economical due to its efficiency and minimal material waste. It is needed explicitly for high-volume production, where economies of scale can be realized.
- Quality and Durability: PVC components are well known for their quality and resistance to outside factors like UV radiation, chemicals, and moisture. This durability ensures long-lasting performance in various applications, including outdoor and industrial settings.
Applications of PVC Injection Molding
Since PVC injection molding is flexible and long-lasting, it is used in many sectors.
- Construction: PVC pipes, fittings, and profiles are widely used in construction because they are durable and resistant to corrosion.
- Automotive: It is used for manufacturing components such as dashboards, trim pieces, and engine covers.
- Medical: PVC injection molding creates medical devices and components due to its hygienic properties and precision.
- Consumer Goods: The process produces household items, toys, and various consumer products.
Critical Considerations for PVC Injection Molding
Several critical factors must be carefully managed to ensure optimal results when undertaking PVC injection molding projects.
- Mold Design: The mold design is fundamental to the success of the injection molding process. It must be meticulously engineered to accommodate the PVC material’s flow characteristics and to achieve the desired part geometry. Proper mold design minimizes defects and ensures the part meets dimensional specifications.
- Material Selection: Choosing the correct type of PVC resin is crucial. Different formulations offer various properties, such as rigidity, flexibility, and resistance to chemicals and UV light. Selecting the appropriate resin based on the intended application ensures the final product performs as required.
- Machine Calibration: The injection molding machine must be accurately calibrated to maintain consistent temperature and pressure during the molding process. Proper calibration prevents incomplete filling or warping issues and ensures uniformity across production runs.
- Cooling and Cycle Time: Effective cooling is essential for solidifying the PVC and achieving the correct part dimensions. The cooling time must be optimized to balance production speed with part quality. Improper cooling can lead to defects such as warping or shrinkage.
- Maintenance: Regular maintenance of both the injection molding machine and the molds is necessary to avoid production disruptions and defects. Well-maintained equipment ensures smooth operation and extends the lifespan of the machinery.
Addressing these considerations helps achieve high-quality, consistent results in PVC injection molding, making the process efficient and cost-effective.
Future Trends in PVC Injection Molding
The future of PVC injection molding is poised for significant advancements driven by evolving technologies and growing environmental awareness.
- Technological Integration: Advances in automation and robotics are expected to enhance the precision and efficiency of PVC injection molding. Automated systems can improve cycle times, reduce labor costs, and increase production consistency.
- Sustainability: There is a strong push towards more sustainable manufacturing practices. This includes developing recyclable PVC materials and reducing the environmental impact of production processes. Innovations in recycling technologies and the use of eco-friendly additives are anticipated to play a crucial role.
- Manufacturing: The integration of IoT (Internet of Things) technologies is set to transform PVC injection molding. Real-time monitoring and data analysis made possible by IoT will lead to smarter manufacturing processes. Predictive maintenance and process optimization through data-driven insights will become the norm, improving quality and reducing downtime.
- Advanced PVC Formulations: Research into new PVC formulations is expected to bring about materials with significantly improved properties. These materials will boast greater durability, enhanced flexibility, and better resistance to environmental factors. As a result, the range of applications for PVC injection molding is set to expand.
- Customization and Complexity: As manufacturing technologies advance, the ability to produce more complex and customized parts will increase. Innovations in mold design and injection techniques will allow for greater design freedom and customization options.
These trends indicate a future in which PVC injection molding will become even more efficient, sustainable, and adaptable, meeting the evolving demands of various industries.
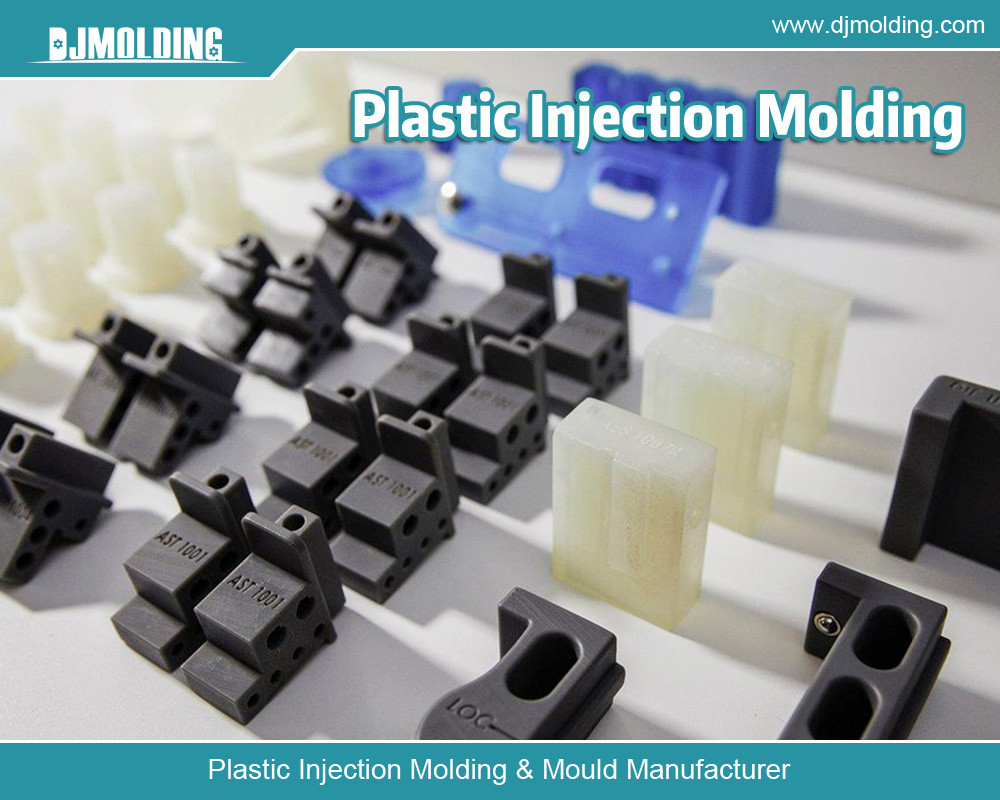
Conclusion
PVC injection molding is still a vital industrial technology because of its accuracy, effectiveness, and adaptability. Manufacturers can maximize their use of PVC injection molding to satisfy their production goals by comprehending the basic procedure, benefits, applications, and important factors. The benefits and applications of PVC injection molding will be further enhanced as the industry innovates, embracing new technology and sustainable practices to ensure its continued relevance and effectiveness.
For more about complete guide to pvc injection molding, you can pay a visit to Djmolding at https://www.djmolding.com/best-top-10-plastic-injection-molding-manufacturers-and-companies-in-india/ for more info.