Troubleshooting Injection Molding Weld Lines: A Comprehensive Guide
Troubleshooting Injection Molding Weld Lines: A Comprehensive Guide
Injection molding is a widely used manufacturing process for producing complex plastic parts with high precision and efficiency. However, one common defect encountered during this process is forming weld lines, also known as knit lines. These lines occur when two or more flow fronts of molten plastic meet and fail to merge fully, leading to visible lines or weak spots in the final product. Weld lines can affect the appearance and structural integrity of molded parts, making it crucial to understand how to troubleshoot and minimize them. This article will delve into the causes of weld lines, their impact on molded parts, and strategies for troubleshooting and preventing them.
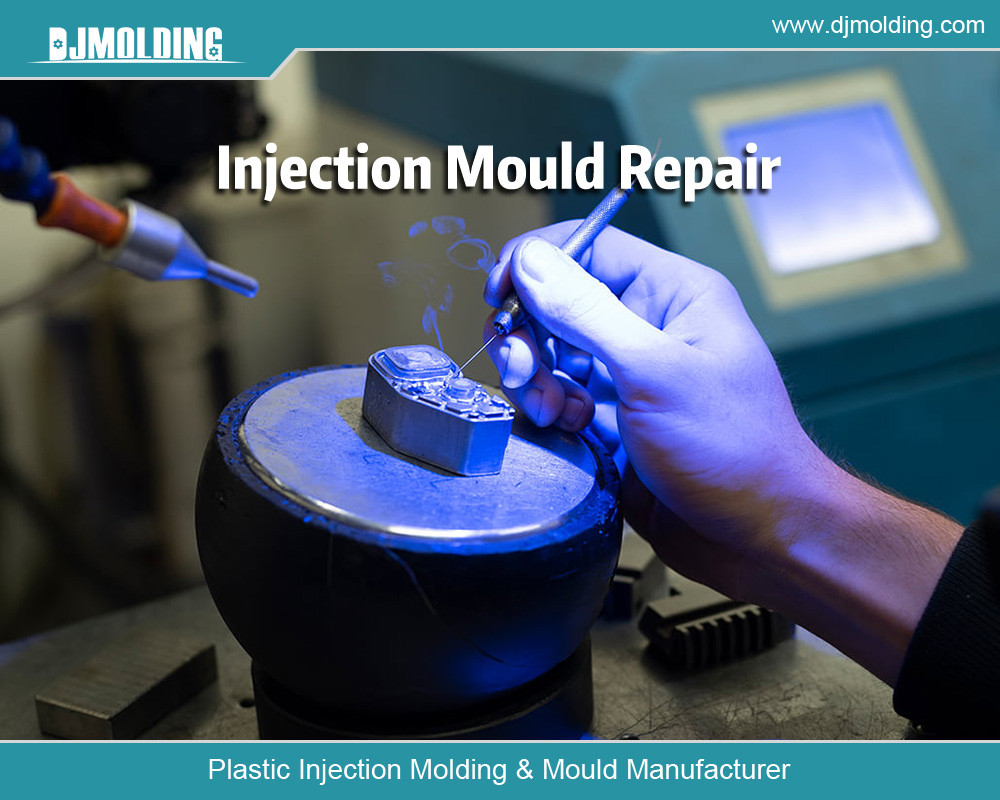
1. Understanding Weld Lines in Injection Molding
1.1 What Are Weld Lines?
Weld lines, also called knit lines, form when multiple flow fronts of molten plastic meet within a mold cavity. These flow fronts may come from different gates or the plastic flow splitting due to obstacles such as cores, inserts, or holes in the mold. When these flow fronts converge, they may not fully meld together, resulting in a line often visible on the part’s surface. Weld lines can appear from faint lines to more pronounced grooves, depending on material type, mold design, and processing conditions.
1.2 Causes of Weld Lines
Weld lines can be caused by several factors related to the injection molding process, including:
- Material Properties: Different materials have varying viscosities and flow characteristics. Materials with high viscosity may flow slowly, leading to incomplete merging of flow fronts and the formation of weld lines.
- Mold Design: The design of the mold plays a significant role in the formation of weld lines. Features such as sharp corners, thin walls, and complex geometries can disrupt flow, leading to multiple flow fronts that may not fully merge.
- Processing Parameters: Injection speed, pressure, and temperature are critical parameters that influence the flow of molten plastic. Inadequate pressure or speed may result in insufficient force to push the flow fronts together. At the same time, improper temperature settings can affect the material’s viscosity and ability to merge at the weld line.
- Gate Location: The placement of gates in the mold can significantly impact the flow pattern of the molten plastic. Poor gate placement can create uneven flow fronts, leading to the formation of weld lines.
2. The Impact of Weld Lines on Molded Parts
2.1 Aesthetic Concerns
Weld lines can significantly impact the visual appearance of molded parts. They may appear as visible lines or color changes on the part’s surface, which can be particularly problematic for products that require a high-quality finish, such as consumer electronics or automotive components. In some cases, the presence of weld lines can lead to product rejections or the need for additional finishing processes, increasing production costs and time.
2.2 Structural Integrity
Beyond aesthetics, weld lines can also compromise the structural integrity of molded parts. Since weld lines are areas where the flow fronts have not fully merged, they can create weak spots more prone to cracking or breaking under stress. This is especially concerning for parts subjected to mechanical loads or environmental conditions that may exacerbate these weaknesses. In critical applications like medical devices or aerospace components, weld lines can be a severe safety concern.
2.3 Material Properties
The presence of weld lines can also affect the material properties of the molded part. For example, the part’s mechanical strength, impact resistance, and fatigue life may be reduced in the area of the weld line. This is because the molecular orientation and bonding at the weld line often differ from those in the rest of the part, leading to localized weaknesses. Additionally, weld lines can affect the part’s ability to undergo secondary operations, such as painting, plating, or bonding, as these processes may not adhere well to the weld line area.
3. Troubleshooting Weld Lines in Injection Molding
3.1 Material Selection and Preparation
One of the first steps in troubleshooting weld lines is carefully considering the material used for the injection molding process. Different materials have different flow characteristics, which can influence the formation of weld lines. When selecting a material, it’s essential to consider factors such as viscosity, melting temperature, and the material’s ability to flow and merge at weld lines.
- Material Viscosity: Low-viscosity materials flow more quickly and are less likely to form weld lines. If weld lines are a persistent issue, switching to a material with a lower viscosity may help improve flow and reduce the formation of weld lines.
- Material Additives: Certain additives, such as lubricants or plasticizers, can be added to the material to improve flow and reduce the likelihood of weld lines. However, it’s essential to carefully evaluate these additives’ impact on the part’s overall performance.
- Drying: Proper material drying is essential to prevent the formation of weld lines. Moisture in the material can lead to steam pockets or other flow disruptions that contribute to weld line formation. Ensuring the material is adequately dried before molding can help minimize these issues.
3.2 Mold Design Considerations
The design of the mold itself is a critical factor in preventing weld lines. Optimizing mold design can reduce the likelihood of weld line formation and improve the overall quality of the molded part.
- Gate Placement: Proper gate placement is essential for minimizing weld lines. The gates should be positioned to ensure a uniform material flow into the mold cavity, minimizing the formation of multiple flow fronts. In some cases, various gates may achieve a more balanced flow and reduce weld lines.
- Flow Channels: The design of the flow channels within the mold can also impact weld lines. Smooth, gradual transitions in the flow channels can help maintain a uniform flow of material and reduce the likelihood of flow disruptions that can lead to weld lines.
- Ventilation: Proper ventilation allows trapped air to escape from the mold cavity. Trapped air can create flow disruptions and contribute to the formation of weld lines. Ensuring the mold is vented correctly can help reduce the likelihood of these issues.
- Cooling System: The cooling system within the mold can also impact weld lines. Uneven cooling can lead to differential shrinkage and flow disruptions, which can contribute to the formation of weld lines. Ensuring that the mold is cooled correctly can help reduce these issues.
3.3 Optimizing Processing Parameters
In addition to material selection and mold design, the processing parameters used during injection molding can significantly impact weld line formation. By optimizing these parameters, we can reduce the likelihood of weld lines and improve the overall quality of the molded part.
- Injection Speed and Pressure: Increasing the injection speed and pressure can help push the flow fronts together more forcefully, reducing the likelihood of weld lines. However, balancing these parameters is essential to avoid defects like flash or warping.
- Melt Temperature: The temperature of the molten material plays a critical role in its flow characteristics. Increasing the melt temperature can reduce viscosity and improve flow, helping to minimize weld lines. However, ensuring the temperature is not too high is essential, as this can lead to material degradation.
- Mold Temperature: The temperature of the mold itself can also impact weld line formation. Higher mold temperatures can help maintain the material flow and reduce the likelihood of weld lines. However, it’s essential to carefully control mold temperature to avoid other issues, such as prolonged cycle times or material shrinkage.
- Hold and Pack Pressure: Proper and pack pressure can help ensure the flow fronts are fully merged at the weld line. Increasing hold and pack pressure can reduce the likelihood of weld lines, but avoiding excessive pressure can lead to other defects, such as sink marks or flash.
3.4 Advanced Techniques and Technologies
Advanced techniques and technologies can further reduce or eliminate weld lines for more challenging cases where weld lines persist despite optimizing material selection, mold design, and processing parameters.
- Mold Flow Simulation: Mold flow simulation software can analyze the flow of material within the mold cavity and identify potential areas where weld lines may form. By simulating different scenarios and adjusting mold design or processing parameters, the process can be optimized and the likelihood of weld lines reduced.
- Gas-Assisted Injection Molding: In gas-assisted injection molding, gas is injected into the mold cavity along with the molten material, helping to push the flow fronts together and reduce the likelihood of weld lines. This technique is beneficial for thick-walled parts or parts with complex geometries.
- Sequential Valve Gating: Sequential valve gating is a technique where the gates in the mold are opened and closed in a specific sequence to control the flow of material and reduce the likelihood of weld lines. This technique is beneficial for large or complex parts with multiple gates.
- Vacuum-Assisted Molding: Vacuum-assisted molding involves applying a vacuum to the mold cavity to remove trapped air and reduce the likelihood of flow disruptions that can lead to weld lines. This technique can be beneficial for parts with deep cavities or intricate details.
4. Case Studies and Real-World Examples
To better understand the practical application of these troubleshooting techniques, let’s explore a few case studies where weld lines were successfully minimized or eliminated.
4.1 Case Study 1: Automotive Dashboard
An automotive manufacturer was experiencing issues with weld lines on a significant, complex dashboard component. The weld lines were affecting the aesthetic quality of the part and leading to customer complaints. After conducting a mold flow analysis, it was determined that the weld lines were forming due to the gates’ placement and the material’s flow characteristics.
The manufacturer implemented several changes to address the issue:
- The gate placement was optimized to create a more uniform flow pattern within the mold cavity.
- The injection speed and pressure were increased to help push the flow fronts together more forcefully.
- The mold temperature was increased to improve the flow of the material.
These changes significantly reduced the visibility of weld lines, improved the overall quality of the dashboard component, and reduced customer complaints.
4.2 Case Study 2: Medical Device Housing
A medical device manufacturer was producing a housing component requiring high structural integrity and a flawless surface finish. However, weld lines formed in critical areas of the part, leading to concerns about its aesthetic quality and strength.
The manufacturer conducted a detailed analysis of the material properties, mold design, and processing parameters. It was determined that the material being used had a high viscosity, contributing to the formation of weld lines. The material was switched to a lower-viscosity alternative, which improved flow and reduced the likelihood of weld lines.
In addition, the gate placement was optimized to create a more balanced flow pattern, and the mold temperature was increased to help maintain the flow of the material. These changes significantly reduced weld lines, ensuring that the housing component met the required quality standards.
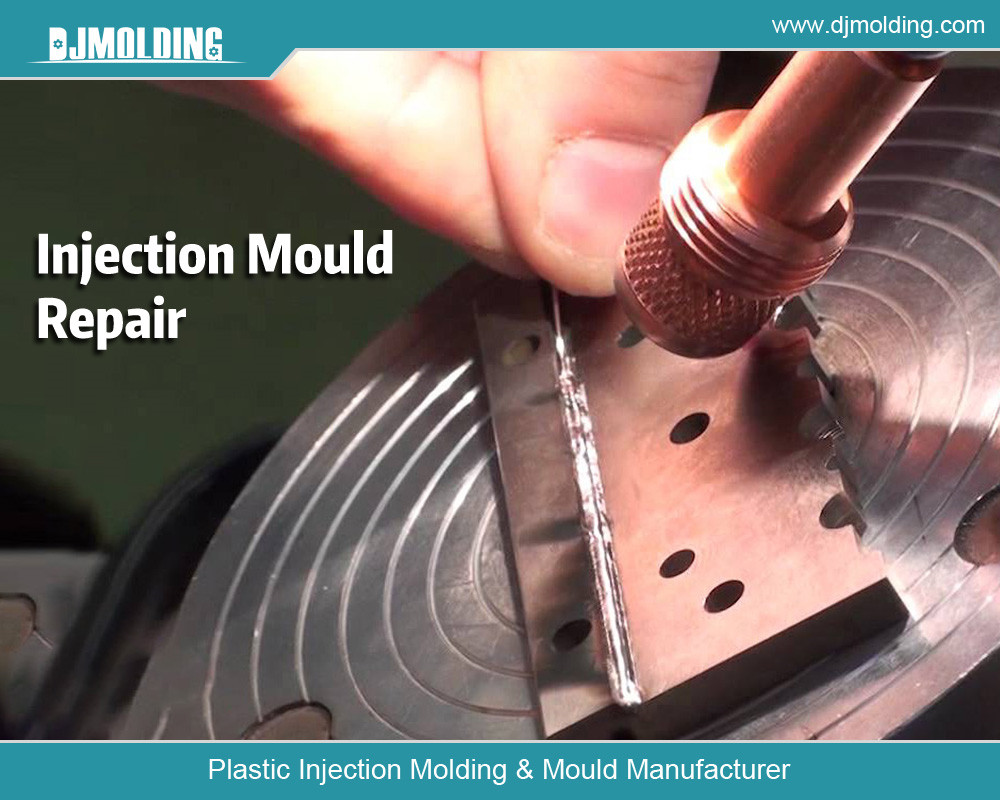
Conclusion
Weld lines are a common issue in injection molding that can impact the aesthetic quality, structural integrity, and material properties of molded parts. By understanding the causes of weld lines and implementing effective troubleshooting strategies, manufacturers can minimize their impact and produce high-quality parts that meet customer expectations.
Critical strategies for troubleshooting weld lines include selecting the appropriate material, optimizing mold design, and carefully controlling processing parameters. For more challenging cases, advanced techniques such as mold flow simulation, gas-assisted injection molding, and sequential valve gating can be employed to reduce further or eliminate weld lines.
By taking a comprehensive approach to troubleshooting weld lines, manufacturers can improve the quality of their injection-molded parts, reduce production costs, and enhance customer satisfaction.
For more about troubleshooting injection molding weld lines: a comprehensive guide, you can pay a visit to Djmolding at https://www.djmolding.com/mould-service/ for more info.