Types Of Ejection System In Injection Molding
Types Of Ejection System In Injection Molding
Injection molding is a profoundly effective and flexible assembly process used to create many parts in different enterprises, including auto, shopper merchandise, and clinical gadgets. An essential part of this interaction is the discharge framework, which is liable for eliminating the shaped part from the shape cavity whenever it has cooled and hardened. The launch framework should guarantee that the part is taken out without causing harm, bending, or excessive weight on the form. This article will investigate the various kinds of discharge frameworks utilized in injection shaping, their standards of activity, and their benefits and burdens.
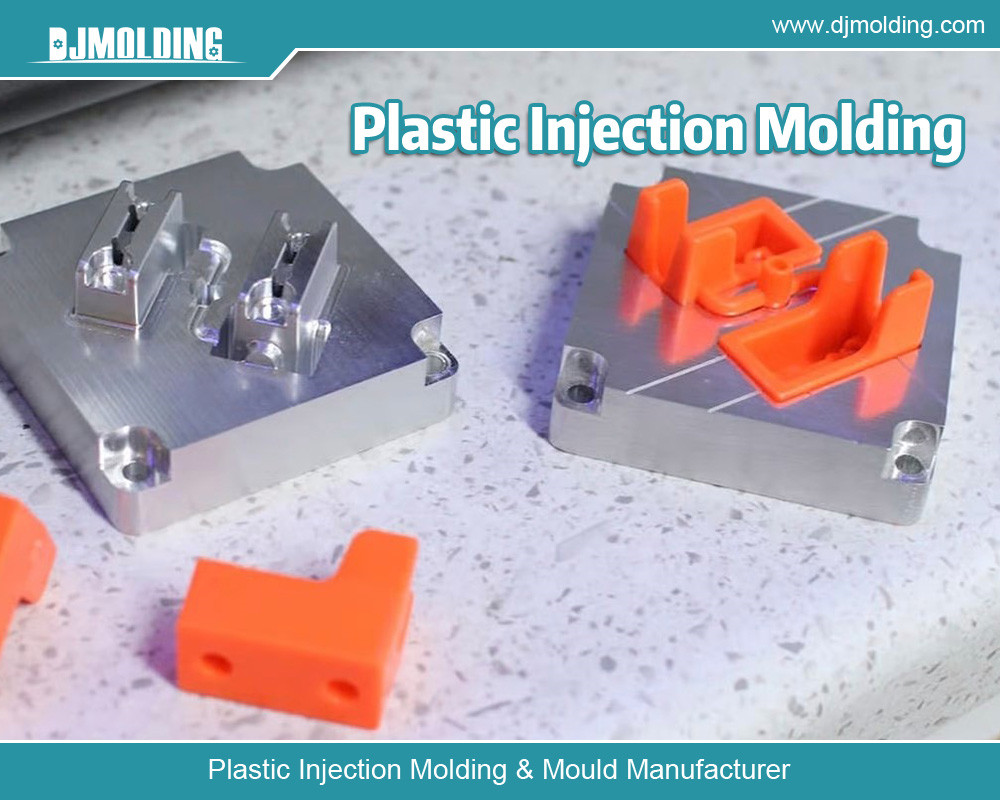
Mechanical Launch Frameworks
Mechanical launch frameworks are the discharge frameworks most ordinarily involved in injection shaping. These frameworks depend on actual instruments to push or haul the shaped part out of the form cavity. The principal types of mechanical launch frameworks include:
Push-Pull Discharge Framework
The push-pull discharge framework uses back-and-forth powers to launch the shaped part. This framework uses ejector pins or plates to push the part out of the form hole. When the ejector pins are initiated, they stretch through the shape and move the part toward the form opening. In particular plans, a draw force is applied to withdraw the part from the shape pit.
Advantages:
- Basic and precise plan.
- Dependable and practical.
- Reasonable for many part calculations and sizes.
Disadvantages:
- Restricted discharge force contrasted with different frameworks.
- It may not be appropriate for perplexing or sensitive parts.
- Potential for mileage on ejector pins.
Ejector Pin Framework
The ejector pin framework is a generally utilized mechanical launch framework with a progression of pins organized inside the form. These pins are driven by an instrument (typically a water-powered or pneumatic framework) to push the formed part out of the pit. Ejector pins blend with different parts, such as ejector plates or sleeves, to guarantee a powerful launch.
Advantages:
- Gives exact command over launch power and development.
- It can be effectively tweaked to suit different part calculations.
- Insignificant gamble of part contortion or harm.
Disadvantages:
- Requires cautious arrangement and support.
- It could be restricted in its capacity to deal with high-volume creation.
Ejector Plate Framework
The ejector plate framework comprises at least one plate outfitted with ejector pins or edges. These plates are mounted on a mobile piece of the shape and pushed or pulled to launch the formed part. The framework can be worked physically or naturally, contingent upon the intricacy of the embellishment interaction.
Advantages:
- Appropriate for high-volume creation and complex part calculations.
- Gives a steady and solid launch.
- Takes into consideration simple substitution and upkeep of ejector parts.
Disadvantages:
- Higher beginning expense and intricacy contrasted with more straightforward frameworks.
- Requires exact arrangement and adjustment.
Pressure-driven Launch Frameworks
Water-powered launch frameworks utilize pressure-driven strain to drive the discharge interaction. These frameworks are often used in applications requiring high discharge powers or exact command over the launch cycle, which is fundamental. Pressure-driven discharge frameworks can be arranged into two primary sorts:
Water-driven Ejector Pin Framework
The water-powered ejector pin framework uses water-driven chambers to drive the ejector sticks that push the formed part out of the shape hole. This framework considers exact command over the launch power and development, making it appropriate for intricate and high-accuracy parts.
Advantages:
- Gives high discharge powers and exact control.
- Reasonable for high-accuracy and complex parts.
- Takes into consideration smooth and predictable discharge.
Disadvantages:
- More significant expense and intricacy contrasted with mechanical frameworks.
- It requires ordinary support and checking of water-driven parts.
Water-powered Ejector Plate Framework
The water-driven ejector plate framework utilizes pressure-driven strain to move at least one ejector plate, which pushes the formed part out of shape. This framework is conducive for massive or weighty parts that require critical discharge force.
Advantages:
- We are equipped to take care of enormous and weighty parts.
- Gives steady and solid discharge.
- Consider a simple change of discharge force.
Disadvantages:
- It requires a water-driven power unit and related parts.
- Higher beginning expense and intricacy.
Pneumatic Discharge Frameworks
Pneumatic discharge frameworks use compacted air to drive the launch cycle. These frameworks are usually utilized in applications where moderate discharge powers are required or where a fast and productive launch is fundamental. Pneumatic launch frameworks can be grouped into two principal types:
Pneumatic Ejector Pin Framework
The pneumatic ejector pin framework utilizes pneumatic chambers to drive the ejector sticks, which push the formed part out of the shape cavity. This framework provides fast and effective discharge and is often utilized in high-velocity creation conditions.
Advantages:
- Gives a speedy and effective launch.
- Appropriate for moderate discharge powers and rapid creation.
- It requires less support than pressure-driven frameworks.
Disadvantages:
- Restricted launch force contrasted with pressure-driven frameworks.
- Requires a compacted air supply.
Pneumatic Ejector Plate Framework
The pneumatic ejector plate framework utilizes pneumatic strain to move at least one ejector plate, which pushes the formed part out of shape. This framework is great for applications where moderate launch powers are required and where space imperatives are considered.
Advantages:
- Gives a fast and effective launch.
- Reasonable for moderate discharge powers and space-obliged conditions.
- Water-driven frameworks require more support.
Disadvantages:
- Restricted discharge force contrasted with pressure-driven frameworks.
- Requires a compacted air supply.
Mixture Launch Frameworks
Cross-breed discharge frameworks consolidate components of mechanical, water-driven, and pneumatic launch frameworks to give a tweaked launch arrangement. These frameworks are intended to exploit the qualities of each sort of discharge framework while alleviating their limitations.
Mechanical-Water powered Half and half Framework
The mechanical-water-powered half-breed framework consolidates mechanical discharge parts (for example, ejector pins or plates) with pressure-driven actuators to improve launch power and control. This framework is appropriate for applications requiring high launch force and exact control.
Advantages:
- Gives high discharge force and exact control.
- Joins the qualities of mechanical and water-driven frameworks.
- Reasonable for intricate and high-accuracy parts.
Disadvantages:
- More significant expense and intricacy.
- Requires cautious joining and upkeep.
Mechanical-Pneumatic Half-breed Framework
The mechanical-pneumatic half-breed framework joins mechanical launch parts with pneumatic actuators to provide speedy and proficient discharge. This framework is appropriate for applications requiring moderate discharge powers and high-velocity creation.
Advantages:
- Gives speedy and effective discharge.
- Consolidates the qualities of mechanical and pneumatic frameworks.
- Appropriate for high-velocity creation conditions.
Disadvantages:
- Restricted discharge force contrasted with water-driven frameworks.
- Requires a compacted air supply.
Contemplations for Picking a Discharge Framework
While choosing a discharge framework for an injection shaping application, a few variables should be considered to guarantee ideal execution and effectiveness:
Part Calculation and Intricacy
The math and intricacy of the shaped part play a massive part in deciding the most reasonable discharge framework. Leaves behind many-sided plans or tight resilience might require water-driven or half-and-half frameworks to guarantee exact and reliable discharge.
Launch Power Necessities
The expected discharge force relies upon elements such as part size, material properties, and shape plan. Higher discharge powers might require water-driven or half-breed frameworks, while mechanical or pneumatic frameworks can handle moderate powers.
Creation Volume and Speed
Pneumatic or mixture launch frameworks that offer fast and productive discharge might benefit high-volume and high-velocity creation conditions. Water-driven or mechanical frameworks might be more appropriate for lower-volume or more complicated applications.
Support and Dependability
The support necessities and dependability of the discharge framework are significant considerations. Mechanical frameworks generally require less support yet might be less strong than water-driven or pneumatic frameworks, which offer higher discharge powers yet require standard observation and upkeep.
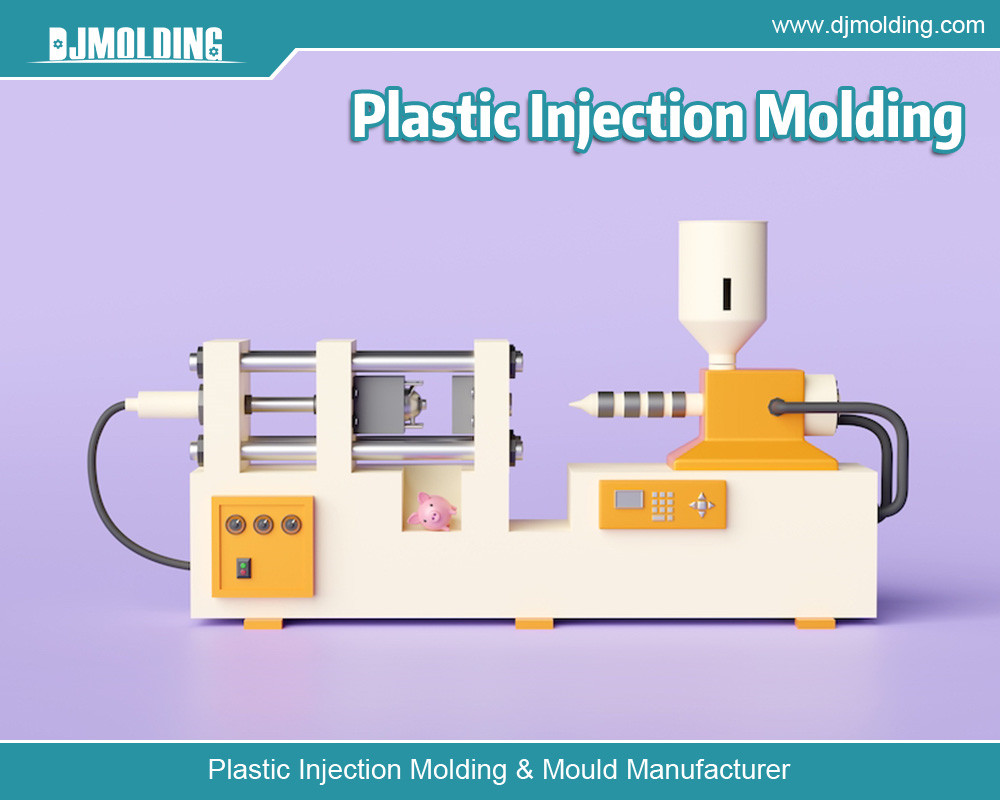
Conclusion
The launch framework is an indispensable part of the injection shaping interaction, liable for eliminating the shaped part from the form hole productively and without harm. Different sorts of launch frameworks, including mechanical, pressure-driven, pneumatic, and half-and-half frameworks, offer various benefits and detriments relying upon the particular necessities of the application. By understanding the standards of each kind of discharge framework and considering factors, for example, part calculation, launch force necessities, creation volume, and upkeep needs, producers can choose the most reasonable launch framework to guarantee ideal execution and quality in their injection shaping cycles.
For more about types of ejection system in injection molding, you can pay a visit to Djmolding at https://www.djmolding.com/types-of-gating-system-for-plastic-injection-mold-design/ for more info.