Plastic Injection Mold Cooling System Design
Plastic Injection Mold Cooling System Design
Injection molding is a critical process in manufacturing plastic products, where molten plastic is injected into a mold to form specific shapes. One of the most essential aspects of injection molding is the cooling system, as it significantly impacts the production process’s cycle time, product quality, and overall efficiency. This article delves into the intricacies of injection mold cooling system design, highlighting its importance, key components, design considerations, and best practices.
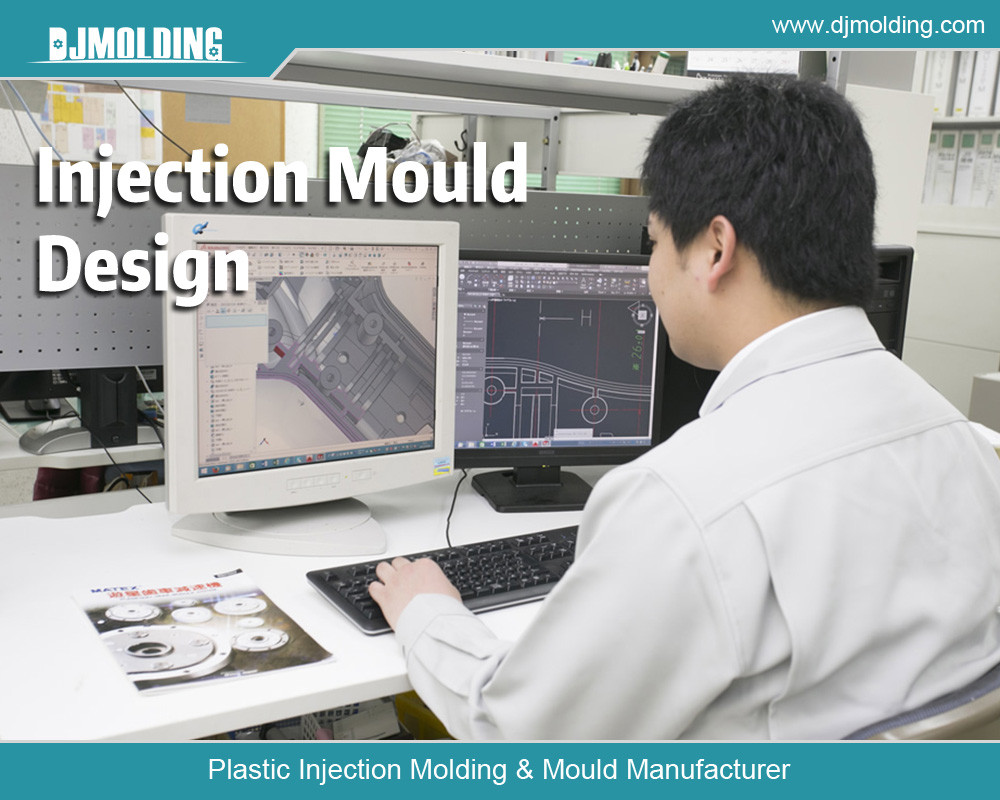
Importance of Cooling in Injection Molding
Cooling is a crucial phase in the injection molding cycle. It typically accounts for more than half of the cycle time, making it a significant factor in determining the overall productivity of the molding process. Effective cooling ensures the following:
- Reduced Cycle Time: Efficient cooling systems shorten the time required for the plastic to solidify, reducing the overall cycle time and increasing production throughput.
- Improved Product Quality: Proper cooling helps achieve uniform temperature distribution and minimize internal stresses, warping, and shrinkage, which leads to better dimensional stability and surface finish of the molded parts.
- Energy Efficiency: Optimized cooling systems can significantly reduce energy consumption by maintaining the mold temperature within the desired range more efficiently.
Critical Components of Injection Mold Cooling Systems
A well-designed injection mold cooling system comprises several critical components, each playing a vital role in the process:
Cooling Channels
Cooling channels are pathways designed within the mold through which a cooling medium (usually water) flows to remove heat from the molten plastic. These channels’ design, layout, and placement are crucial for effective cooling.
Cooling Medium
Water is the most commonly used cooling medium due to its high thermal conductivity and availability. However, other fluids like oil or air can be used in specific applications where water is unsuitable.
Pumps and Chillers
Pumps circulate the cooling medium through the system, while chillers remove the heat absorbed by the cooling medium and maintain it at the desired temperature.
Temperature Controllers
Temperature controllers regulate the temperature of the cooling medium to ensure consistent cooling throughout the molding process.
Design Considerations for Injection Mold Cooling Systems
Designing an effective cooling system for injection molds involves several critical considerations for optimal performance. These include:
Mold Material and Thermal Conductivity
The mold’s material significantly affects its thermal conductivity. Materials with high thermal conductivity, such as aluminum and beryllium copper alloys, enhance cooling efficiency but may be more expensive than standard mold steels.
Cooling Channel Design and Placement
The design and placement of cooling channels are crucial for uniform cooling. Key factors to consider include:
- Channel Geometry: Circular channels are common due to their ease of manufacturing and efficient flow characteristics. However, conformal cooling channels, which follow the contour of the mold cavity, provide more uniform cooling but are more complex and expensive to produce.
- Channel Diameter and Spacing: Larger diameter channels offer better flow rates and cooling efficiency but may compromise mold strength. Proper spacing ensures uniform cooling and prevents hot spots.
- Proximity to Mold Cavity: Channels should be placed as close to the mold cavity as possible without compromising the structural integrity of the mold.
Cooling Medium Flow Rate and Temperature
The flow rate and temperature of the cooling medium directly affect the heat removal rate. Higher flow rates and lower temperatures enhance cooling efficiency but may increase energy consumption and operational costs. Balancing these factors is crucial for an optimal cooling system design.
Heat Transfer Analysis
Conducting a thorough heat transfer analysis helps understand the mold’s thermal behavior and identify potential hot spots. Computational tools like Finite Element Analysis (FEA) can simulate the cooling process and provide valuable insights for optimizing the cooling system design.
Mold Complexity and Part Geometry
The complexity of the mold and the geometry of the part being produced also influence the cooling system design. Complex molds with intricate geometries may require advanced techniques such as conformal cooling or baffles and bubblers to ensure uniform cooling.
Advanced Cooling Techniques
As injection molding technology advances, several innovative cooling techniques have been developed to enhance cooling efficiency and reduce cycle times. Some of these techniques include:
Conformal Cooling
Conformal cooling channels are designed to follow the contour of the mold cavity, providing uniform cooling across the entire part. This technique is made possible by advanced manufacturing methods like 3D printing and Direct Metal Laser Sintering (DMLS), which allow for the creation of complex channel geometries that are impossible with traditional machining methods.
High-Performance Heat Transfer Fluids
High-performance heat transfer fluids with better thermal conductivity than water can improve cooling efficiency. Although more expensive, these fluids can significantly reduce cycle times and enhance product quality.
Dynamic Mold Temperature Control
Dynamic mold temperature control involves varying the mold temperature during the injection molding cycle to optimize cooling and minimize defects. This technique uses advanced temperature controllers and sensors to adjust the cooling medium temperature dynamically, ensuring optimal cooling conditions throughout the cycle.
Heat Pipes and Thermal Conductive Inserts
Heat pipes and thermal conductive inserts can enhance heat transfer in critical areas of the mold. Heat pipes are sealed tubes filled with a working fluid that transfers heat through a phase change. At the same time, thermal conductive inserts are materials with high thermal conductivity placed strategically to improve cooling efficiency.
Best Practices for Injection Mold Cooling System Design
Designing an effective injection mold cooling system requires theoretical knowledge, practical experience, and adherence to best practices. Here are some essential best practices to consider:
Early Involvement of Cooling System Design
Integrating cooling system design early in the mold design process ensures that cooling considerations are addressed from the outset. This proactive approach helps identify potential issues and optimize the design for better cooling performance.
Collaboration with Mold Makers and Material Suppliers
Collaborating with mold makers and material suppliers can provide valuable insights into the best cooling system design practices. These experts can recommend mold materials, cooling channel designs, and advanced cooling techniques based on their experience and expertise.
Regular Maintenance and Monitoring
Regular maintenance and monitoring of the cooling system are essential for ensuring its optimal performance. This includes checking for leaks, cleaning cooling channels, and calibrating temperature controllers to maintain consistent cooling efficiency.
Use of Simulation Tools
Simulation tools like FEA and moldflow analysis can provide valuable insights into the mold’s thermal behavior and help optimize the cooling system design. These tools can simulate the cooling process, identify potential hot spots, and evaluate design options for improved cooling performance.
Continuous Improvement and Optimization
Continuous improvement and optimization of the cooling system are essential for maintaining high productivity and product quality. This involves regularly reviewing the cooling system performance, identifying areas for improvement, and implementing changes to enhance cooling efficiency.
Case Studies and Real-world Applications
To illustrate the importance and effectiveness of well-designed injection mold cooling systems, here are a few case studies and real-world applications:
Case Study 1: Automotive Component Manufacturer
An automotive component manufacturer faced long cycle times and inconsistent product quality issues. By redesigning the cooling system with conformal cooling channels and high-performance heat transfer fluids, they achieved a 30% reduction in cycle time and significant improvements in product quality and dimensional stability.
Case Study 2: Consumer Electronics Manufacturer
A consumer electronics manufacturer experienced high scrap rates due to warping and internal stresses in its molded parts. By implementing dynamic mold temperature control and using thermal conductive inserts in critical areas, it reduced scrap rates by 40% and improved the overall quality of its products.
Case Study 3: Medical Device Manufacturer
A medical device manufacturer needed to produce high-precision components with tight tolerances. By collaborating with mold makers and using advanced simulation tools to optimize the cooling system design, they achieved their products’ required precision and consistency while maintaining high production throughput.
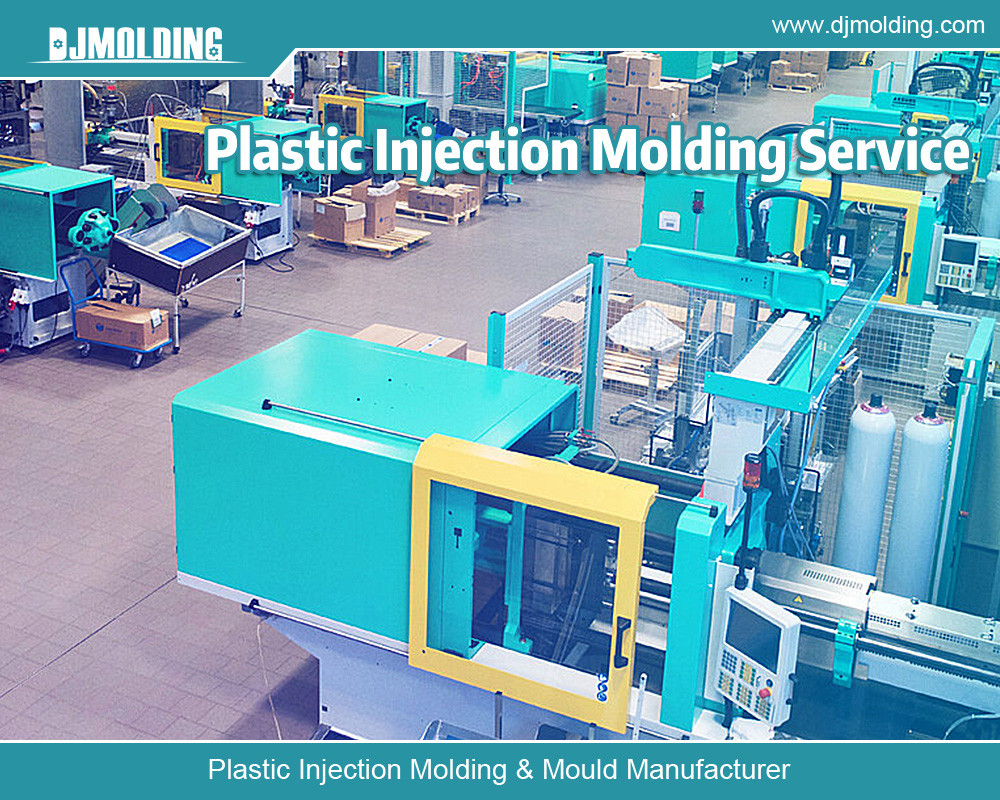
Conclusion
Injection mold cooling system design is a critical aspect of the injection molding process, directly impacting cycle time, product quality, and overall efficiency. By understanding the importance of cooling, the essential components involved, and the design considerations, manufacturers can optimize their cooling systems for improved performance. Advanced cooling techniques, best practices, and continuous improvement efforts further enhance cooling efficiency, ensuring high productivity and product quality in injection molding operations. With the right approach and tools, manufacturers can achieve significant gains in efficiency, cost savings, and competitive advantage in the market.
For more about the plastic injection mold cooling system design,you can pay a visit to Djmolding at https://www.djmolding.com/types-of-gating-system-for-plastic-injection-mold-design/ for more info.