What Is The Injection Molding Process?
What Is The Injection Molding Process?
Injection molding is a manufacturing process that produces parts by injecting molten material into a mold. It is one of the world’s most widely used manufacturing processes due to its ability to produce large quantities of complex parts with high precision and repeatability. This article explores the various aspects of the injection molding process, including its history, the materials used, the equipment involved, the steps of the process, and its applications.
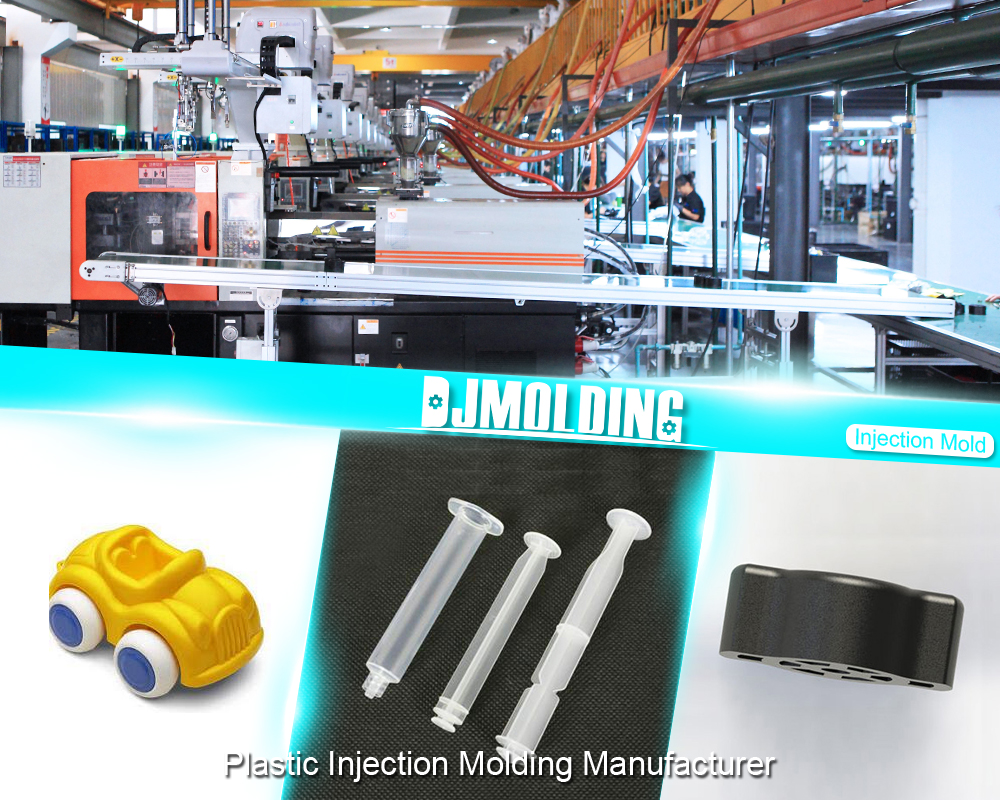
History of Injection Molding
Early Developments
The injection molding process was first developed in the late 19th century. 1872, John Wesley Hyatt and his brother Isaiah patented the first injection molding machine. The machine was relatively simple compared to modern standards, and it was used to mold celluloid, an early form of plastic. The process gradually evolved as new materials and technologies were introduced.
Advances in Technology
Significant advancements in injection molding came in the 1940s with the development of new thermoplastics. These materials allowed for greater flexibility and durability in molded parts. During World War II, the demand for mass-produced plastic parts increased, driving further innovation in injection molding. By the 1950s, injection molding had become a mainstream manufacturing process.
Materials Used in Injection Molding
Types of Materials
Various materials can be used in the injection molding process, each with unique properties. The primary categories include thermoplastics, thermosetting plastics, and elastomers.
- Thermoplastics: These are the most common materials used in injection molding. They include polyethylene, polypropylene, polystyrene, and polyvinyl chloride (PVC). Thermoplastics are favored for their ability to be melted and re-melted multiple times without significant degradation.
- Thermosetting Plastics: These materials, such as epoxy and phenolic resins, undergo a chemical change when heated, which sets them permanently. They cannot be re-melted after being set, making them ideal for high-heat applications.
- Elastomers: These materials, like rubber, have elastic properties and are used for parts that require flexibility and resilience.
Selection Criteria
The choice of material for injection molding depends on various factors, including the intended use of the part, mechanical properties, thermal properties, and cost. Engineers must carefully select the material to ensure the final product meets the desired specifications and performance requirements.
Equipment Used in Injection Molding
Injection Molding Machine
The injection molding machine is the heart of the process. It consists of several key components:
- Injection Unit: This machine part is responsible for melting and injecting the material into the mold. It includes a hopper, where the raw material is fed, a barrel, where the material is heated, and a screw or plunger that pushes the molten material into the mold.
- Clamping Unit: This unit holds the mold in place and applies the necessary pressure to keep it closed during injection. It comprises a fixed platen, a movable platen, and a clamping mechanism.
- Control System: Modern injection molding machines have computerized control systems that regulate temperature, pressure, and timing to ensure consistent quality.
Molds
The mold is a critical component of the injection molding process. It determines the shape and features of the final part. Molds are typically made from steel or aluminum and can be designed to produce single or multiple parts per cycle. The mold consists of two halves: the cavity (female) and the core (male). The design and manufacturing of molds require high precision and are often the most expensive aspects of the injection molding process.
The Injection Molding Process
Step 1: Clamping
The process begins by clamping the two halves of the mold together. The injection molding machine’s clamping unit exerts force to keep the mold closed during the injection phase. The clamping force required depends on the size and complexity of the part being produced.
Step 2: Injection
In the injection phase, the raw material is fed into the injection unit’s hopper and heated until it reaches a molten state. The screw or plunger then pushes the molten material into the mold cavity through a nozzle. The material fills the cavity, taking on its shape. The injection pressure and speed must be carefully controlled to ensure the material flows smoothly and fills the mold.
Step 3: Cooling
Once the mold cavity is filled, the material begins to cool and solidify. The cooling time depends on the material’s properties and the part’s thickness. Proper cooling is crucial to prevent defects such as warping or shrinkage. Some molds have cooling channels to speed up the process and maintain consistent quality.
Step 4: Ejection
After the part has sufficiently cooled and solidified, the mold opens, and the ejection system pushes the part out. Ejector pins or plates are typically used to remove the part from the mold without damaging it. The mold then closes, and the cycle repeats.
Step 5: Finishing
Once the part is ejected, additional finishing processes may be required. These processes include trimming excess material, sanding, painting, or assembly. The extent of finishing required depends on the part’s application and quality requirements.
Advantages of Injection Molding
High Efficiency
Injection molding is known for its high efficiency in producing large quantities of parts. Once the initial setup is complete, the process can run continuously with minimal human intervention, making thousands of parts per hour.
Consistency and Precision
The injection molding process offers exceptional consistency and precision. Modern machines and molds can produce parts with tight tolerances and complex geometries, making injection molding ideal for applications where accuracy is critical, such as in the automotive and medical industries.
Material Versatility
Injection molding is compatible with various materials, allowing manufacturers to choose the best material for their specific application. This versatility extends to the ability to use colorants and additives to enhance the properties of the final product.
Cost-Effectiveness
For high-volume production, injection molding is highly cost-effective. The per-unit cost of parts decreases significantly as production volumes increase. Additionally, the process generates minimal waste, as excess material can often be recycled and reused.
Challenges of Injection Molding
High Initial Costs
One of the main challenges of injection molding is the high initial cost of equipment and molds. Designing and manufacturing molds require significant investment, making the process less viable for low-volume production runs.
Design Limitations
While injection molding is versatile, it does have some design limitations. Parts with complex geometries or undercuts can be challenging to mold and may require additional tooling or secondary operations. Engineers must consider these limitations during the design phase.
Material Constraints
Not all materials are suitable for injection molding. Some materials may degrade at high temperatures or have poor flow properties, making them challenging to mold. Additionally, certain materials may require specialized equipment or processing conditions.
Applications of Injection Molding
Automotive Industry
The automotive industry is one of the most significant users of injection molding. The process produces many parts, including dashboards, bumpers, and interior components. Injection molding allows for making lightweight, durable parts that meet the industry’s strict quality standards.
Medical Industry
Injection molding is used in the medical industry to produce various components, such as syringes, IV components, and surgical instruments. The process ensures that parts meet stringent hygiene and precision requirements, making it ideal for medical applications.
Consumer Goods
Injection molding is widely used in producing consumer goods, including toys, kitchenware, and electronics. The process’s ability to deliver high-quality, aesthetically pleasing parts makes it a popular choice for products that require an excellent appearance and durability.
Packaging
Packaging relies heavily on injection molding to produce containers, caps, and closures. Injection molding allows for the creation of complex shapes and designs essential for packaging products effectively and attractively.
Innovations in Injection Molding
Advanced Materials
Developing advanced materials, such as biodegradable plastics and high-performance polymers, is driving innovation in injection molding. These materials offer improved properties and environmental benefits, expanding the range of applications for injection molding.
Process Automation
Automation is significantly improving the efficiency and consistency of the injection molding process. Automated systems can handle material handling, part inspection, and assembly tasks, reducing labor costs and minimizing human error.
Additive Manufacturing Integration
Integrating additive manufacturing (3D printing) with injection molding is another area of innovation. Additive manufacturing can create complex molds and prototypes quickly and cost-effectively, speeding up the development process and allowing for greater design flexibility.
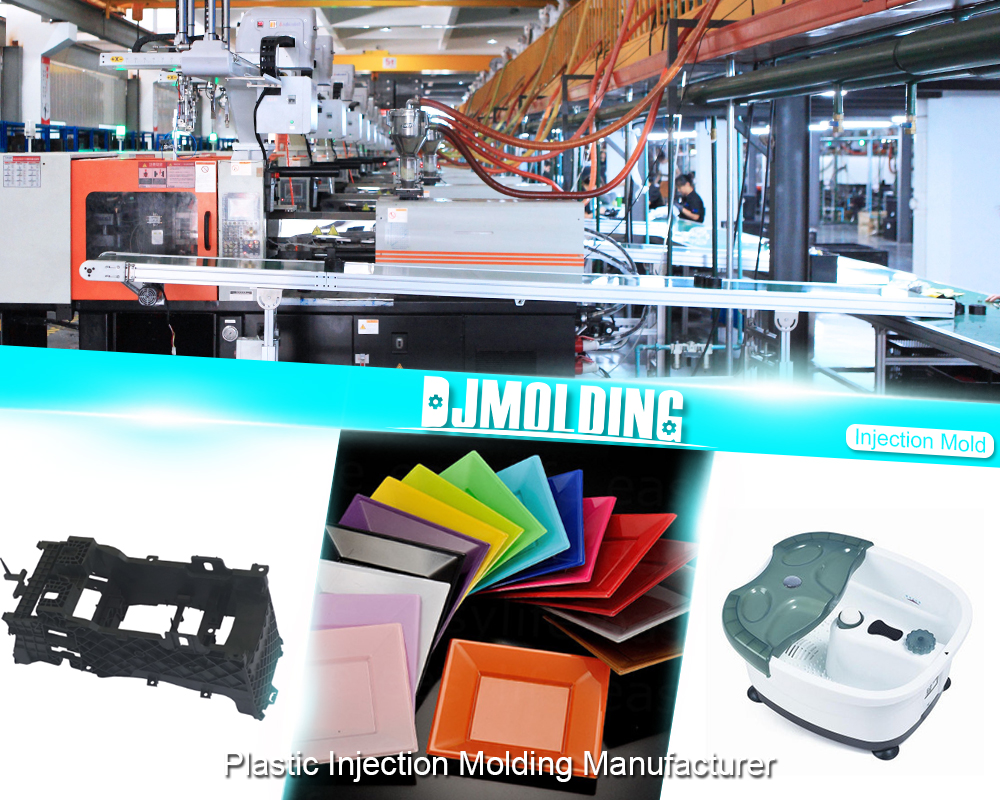
Conclusion
Injection molding is a versatile and efficient manufacturing process crucial in producing a wide range of parts and products. Its ability to deliver high-quality, consistent parts in large quantities makes it a preferred choice for many industries. Despite its challenges, ongoing innovations in materials, automation, and additive manufacturing are continually expanding the capabilities and applications of injection molding. As technology advances, injection molding will remain a fundamental process in the manufacturing world, driving the production of everything from everyday consumer goods to critical medical devices.
For more about what is the injection molding process,you can pay a visit to Djmolding at https://www.djmolding.com/a-step-by-step-manufacturing-guide-to-plastic-injection-molding-process/ for more info.