What Is Aluminum Rapid Tooling For Plastic Injection Molding?
What Is Aluminum Rapid Tooling For Plastic Injection Molding?
Plastic injection molding is a widely used way of manufacturing, pumping out plenty of plastic parts in one go. It works by melting the plastic and forcing it into moulds, which are then cooled to give you the desired shape. But for this process to occur, tooling made from materials like aluminum is essential – aluminum is especially favored due to its long list of benefits over alternative options.
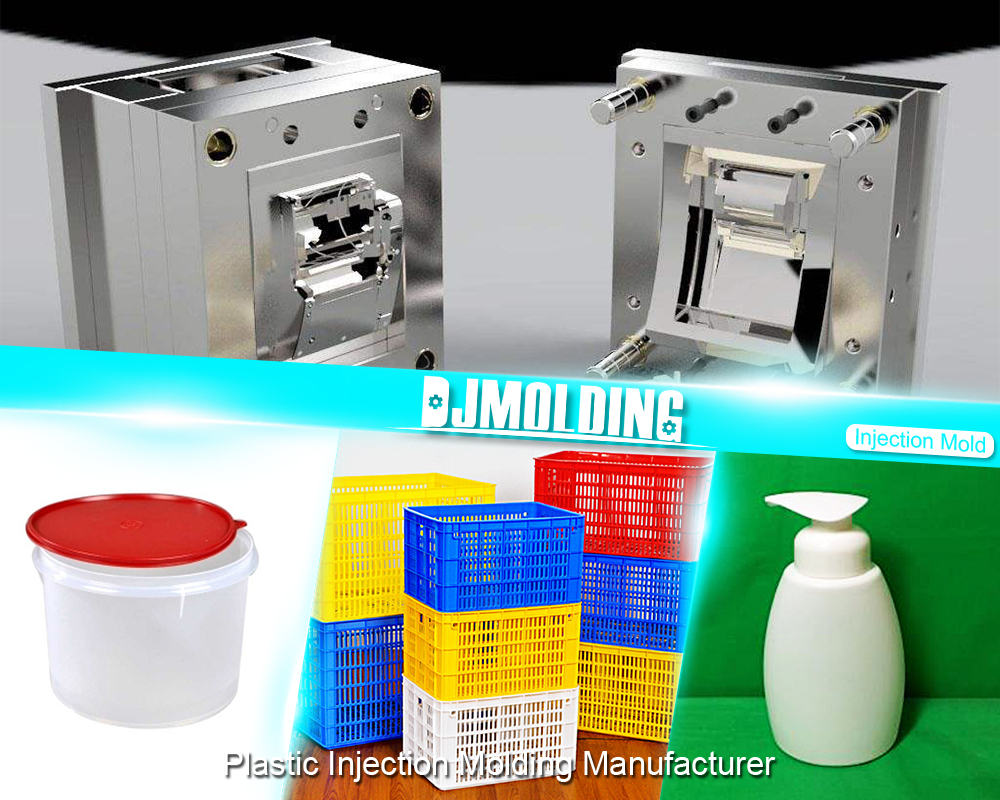
Advantages of Using Aluminum Tooling for Plastic Injection Molding
The primal perk of using aluminum for plastic injection molding is that it delivers lightning-fast results. Aluminum molds are considerably speedier to whittle than solids like steel, leading to reduced lead times and enhanced production rates.
Plus, since aluminum is generally less costly than steel, it’s an economical option for tooling, too—not to mention the machining procedure, for it is way simpler, requiring far fewer moves and cutting costs even further.
Not only do you save time and money with this lightweight material, but its ability to withstand any wear and tear during transportation makes it a more convenient choice – saving labor and worry in the long run.
Importantly, this metal consists of excellent thermal conductivity, which aids in the cooling down of plastics during molding, consequently hastening cycles and making manufacturing more efficient.
To top it off, aluminum propagates fantastic surface grades on all your finished parts, meaning there is no need for extra finishing methods.
How Aluminum Tooling is Made for Plastic Injection Molding
Crafting aluminum tooling for plastic injection molding isn’t exactly straightforward. First, a design outfitted with the desired shape and features of the final product has to be drawn up using some savvy CAD software.
Those specs are then transferred to CAM software, which maps out all the tool paths- that guide the cutters in shaping your aluminum mold! Once it’s programmed, CNC milling machines remove material from that block to create our litter cavity.
Then comes some polishing touch-ups, which produce smooth surfaces for high-quality parts like nobody’s business! Aluminum tooling has perks: faster production rates than steel molds mean shorter lead times.
Also, machining complexity and times are reduced slightly thanks to its overall ease of use compared to steel tooling’s durability – but remember, not every situation is an ideal fit.
Types of Aluminum Used in Tooling for Plastic Injection Molding
Several types of aluminum are commonly used in tooling for plastic injection molding. Each type has its unique properties and benefits.
6061 Aluminum
6061 Aluminum is an incredibly popular alloy of choice for various projects. From creating everyday objects to intricate machinery parts, you can rely on this aluminum staple for a reliable composition with smooth machining while offering unparalleled dimensional stability.
7075 Aluminum
With its superior strength and remarkable resistance to wear, 7075 Aluminum is the ideal alloy for any tooling application requiring durability and dependability. Its lauded mechanical make-up has been tested under intense heat – so you know it’s durable.
5083 Aluminum
Known for its fantastic corrosion resistance and weldability, it’s often used in tooling applications to guard against moisture and corrosive environments. So basically, it’s the knight in shining armor when things threaten to get a bit dicey.
2024 Aluminum
2024 Aluminum is the strong stuff. It’s used widely in aerospace applications – needed to stay hot and travel through space, you know? Machining isn’t a walk in the park, but you can make it work with some elbow grease.
Design Considerations for Aluminum Tooling in Plastic Injection Molding
As you create molds for plastic injection molding with aluminum tooling, several crucial things must be considered. Let’s look at some of them below:
Wall thickness
Just right’s the key! Designing your mold with an appropriate wall thickness is critical for successful plastic injection. It’s too thin, and you’ll end up with distorted parts, not to mention a warped outcome. Conversely, too thick means extending cycle times & wasting material – not worth it! It would help if you struck that happy medium so everything works perfectly in the long run.
Draft angles
Draft angles make it effortless to take out plastic parts cooked in molds, ensuring that neither the molds nor casted pieces get damaged. The ideal draft angle is conditional on the kind of material you’re using and how complex your part turned out. All in all, they are a must for molding if you want super smooth results.
Gate location
Placing the gate at just the right spot – where the molten plastic oozes into the mold cavity – is key for ensuring it’s spread evenly and avoiding blemishes. It must be carefully calculated, assessing what position will ensure that no part of your castings will suffer from pockets or gaps.
Ejection system
Crafting the ejection system is crucial for the uncomplicated and effective expulsion of the plastic pieces from the mold. Structuring it right helps reduce the strain on the die and ensures none of those bits get roughed up when scrapped.
Cost Comparison: Aluminum vs. Steel Tooling for Plastic Injection Molding
Regarding costs, steel tooling for plastic injection molding isn’t always the best option. Sure, aluminum tooling is pricier upfront, but it beats out steel in the long run for companies. After all, aluminum is a much cheaper material and requires fewer steps when machined for molds – making an excellent bang for your buck with lower initial costs!
But that doesn’t mean aluminum will last as long. It has a softer composition, which means more wear over time — especially during production runs at high volumes. Companies may need to swap their molds out sooner than expected, increasing overall expenses.
Despite potential added future fees, aluminum still prevails thanks to its superfast production rate and less heavy initial cost tag – benefitting manufacturers through those lead times and yields being cut down significantly without breaking their bank accounts first.
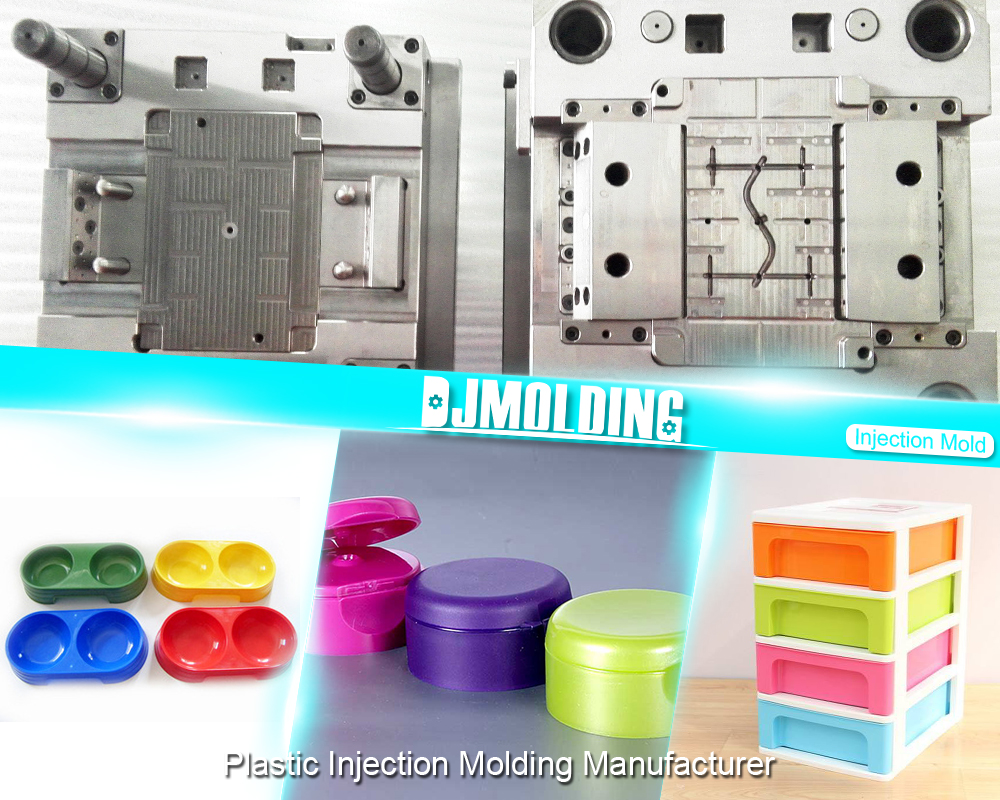
Conclusion
To sum it up, aluminum tooling offers some great perks regarding plastic injection molding. Not only is production time faster and the cost lower, but its lightweight nature makes handling a breeze. Plus, you can count on high thermal conductivity and excellent surface finish that’ll leave you looking good.
It all starts with designing the mold – when you’ve got that down pat, machining and polishing an aluminum block will follow. Certain kinds of aluminum suit different tasks better than others; they treat you right with their unique properties, so be sure to factor them into your decisions! Last but not least – wall thickness, draft angles, gate location, and ejection system.
For more about what is aluminum rapid tooling for plastic injection molding,you can pay a visit to Djmolding at https://www.djmolding.com/what-is-rapid-tooling-injection-molding-for-plastic-parts-manufacturing/ for more info.