Low Volume Injection Molding: Cost-Effective Solutions For Small Scale Plastic Manufacturing
Low Volume Injection Molding: Cost-Effective Solutions For Small Scale Plastic Manufacturing
Low volume injection molding offers a cost-effective solution for small-scale production, revolutionizing the manufacturing industry. With its ability to provide reduced costs, shorter lead times, and increased flexibility, low volume injection molding has gained significant importance in various sectors. In this blog post, we will explore the concept of low volume injection molding, its advantages over traditional manufacturing methods, suitable use cases, materials and design considerations, the process involved, cost considerations, and the factors to consider when choosing a low volume injection molding provider.
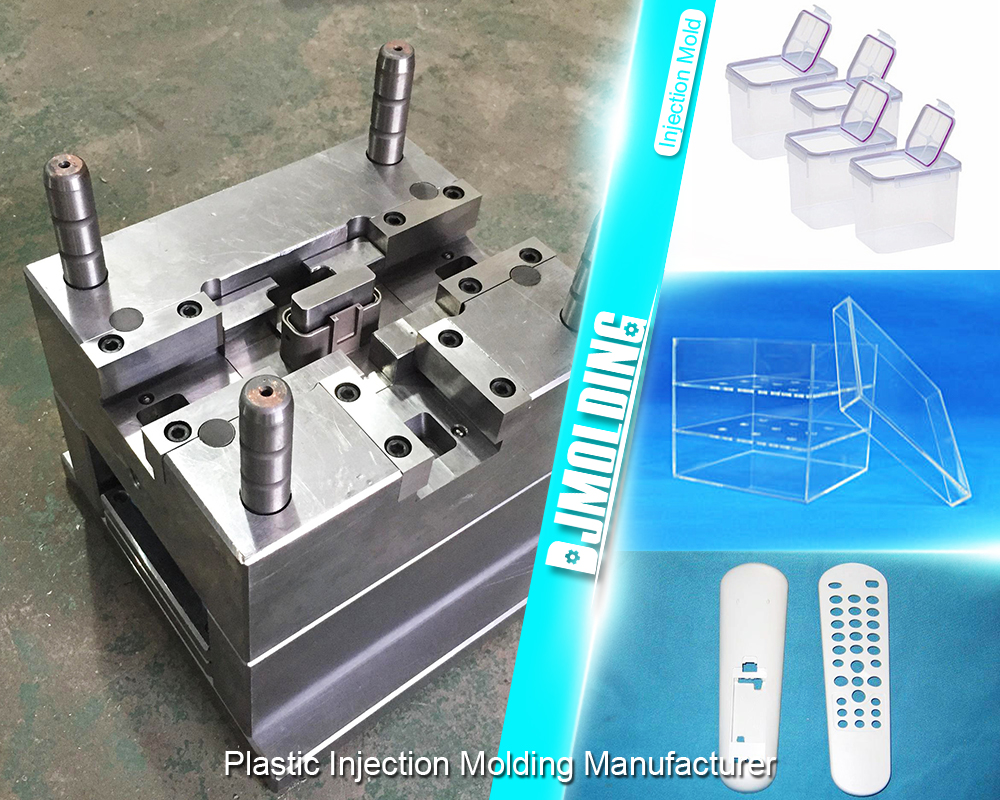
Understanding Low Volume Injection Molding
Definition and Key Features
Low volume injection molding is a manufacturing technique that involves producing small parts using injection molding processes. It combines the benefits of rapid prototyping and traditional injection molding, allowing for efficient production with reduced tooling costs and lead times.
Advantages of Traditional Manufacturing
Low volume injection molding offers several advantages over traditional manufacturing methods. It saves costs by eliminating the need for expensive tooling and minimizing material waste. The shorter lead times facilitate faster product iterations and market entry. Low volume injection molding also supports various industries, including prototyping, niche markets, and limited production runs.
Appropriate Use Cases
Low volume injection molding finds applications in diverse industries. It benefits prototyping, allowing for iterative design improvements before full-scale production. Niche markets benefit from the flexibility of low volume production, enabling customized products for specific customer segments. Furthermore, low volume injection molding caters to limited production runs, addressing demand fluctuations and reducing inventory costs.
Materials and Design Considerations
Low volume injection molding supports various materials, including thermoplastics, elastomers, and engineering-grade resins. Design considerations play a crucial role in achieving optimal results. Factors such as part complexity, undercuts, draft angles, and wall thickness need careful consideration. Manufacturers can make mold modifications to accommodate specific design requirements.
Process of Low Volume Injection Molding
Mold Creation
The process of low volume injection molding begins with mold creation. Mold design involves translating the part’s innovation into a 3D mold, considering factors like part ejection, gating, and cooling. Various mold fabrication methods, such as CNC machining or additive manufacturing, can be employed based on the project requirements.
Injection Molding Process
Once the mold is ready, the injection molding process begins. It comprises several steps, starting with material selection, where the appropriate resin is chosen based on the desired properties of the final part. The material is then heated and injected into the mold cavity, following which it undergoes a cooling phase. Finally, someone opens the mold and ejects the finished part.
Quality Control and Testing
Quality control is paramount in low volume injection molding to ensure the production of high-quality parts. Inspection techniques, such as dimensional analysis, visual inspection, and functional testing, verify the part’s conformance to specifications. Testing procedures, including mechanical, thermal, and chemical testing, further validate the part’s performance.
Cost Considerations and Benefits
Regarding cost considerations, low volume injection molding offers significant advantages over traditional manufacturing methods. Let’s delve into some key points:
- Reduced Tooling Costs: One of the considerable cost benefits of low volume injection molding is the substantial reduction in tooling expenses. Traditional manufacturing often requires expensive molds and tooling equipment, hindering small-scale production. With low volume injection molding, businesses with limited budgets can significantly reduce the tooling cost, making it more accessible and affordable.
- Minimal Material Waste: Traditional manufacturing methods often result in significant material waste, especially during the initial setup and testing phases, and this can lead to increased costs and environmental concerns. Low volume injection molding minimizes material waste by precisely controlling the amount of material injected into the mold, and this not only reduces costs and aligns with sustainable manufacturing practices.
- Faster Time-to-Market: Time is money in the competitive business landscape. Low volume injection molding enables faster time-to-market by lowering lead times compared to traditional manufacturing. The streamlined process allows quicker iterations and adjustments, from mold creation to production. This rapid turnaround time is especially advantageous for businesses in rapidly evolving industries or those responding to changing customer demands.
- Customization and Flexibility: Low volume injection molding offers high customization and flexibility. Companies can easily modify designs and make adjustments to meet specific customer requirements. This level of customization minimizes the need for costly post-production modifications or rework, resulting in cost savings and improved customer satisfaction.
- Cost Savings for Small Production Runs: Low-volume injection molding is particularly cost-effective for limited production runs or niche market products. Instead of investing in large-scale production infrastructure, businesses can produce small quantities on demand. By adopting this approach, you can avoid holding extra inventory, lower storage expenses, and decrease the chances of making too much.
- Scalability and Risk Reduction: Low volume injection molding allows businesses to scale their production gradually, allowing them to test the market and validate product demand before committing to large-scale production. This scalability reduces the financial risks associated with mass production, as businesses can adjust production volumes based on market response and request.
- Improved Profit Margins: Low volume injection molding can improve profit margins by reducing tooling expenses, minimizing material waste, and allowing for faster time-to-market. Businesses can optimize manufacturing processes, reduce costs, and increase efficiency, improving financial outcomes.
Choosing the Right Low Volume Injection Molding Provider
Choosing the right low volume injection molding provider can be daunting, as businesses must consider many factors. Here are some key points to help you make the right decision:
- Experience: Look for a provider with a solid track record of success in low volume injection molding. An experienced provider will likely have the expertise and knowledge to deliver high-quality products.
- Quality Control: Quality control is critical in injection molding, as even minor defects can result in significant production delays and costs. Ensure the provider has a robust quality control system to ensure the final product meets your specifications.
- Customization: Injection molding can create various products, from small components to large parts. Look for a provider that can customize their services to meet your needs, including material selection, mold design, and production volume.
- Communication: Good communication is key to a successful injection molding project. Look for a provider that is responsive and easy to communicate with and who keeps you informed throughout the production process.
- Cost: Cost is always a consideration but should not be the only factor. Look for a provider that offers competitive pricing while still delivering high-quality products and excellent customer service.
- Environmental Responsibility: As environmental concerns become more critical, choosing a provider committed to sustainable manufacturing practices is essential. Look for a provider that uses eco-friendly materials and processes and recycles waste materials.
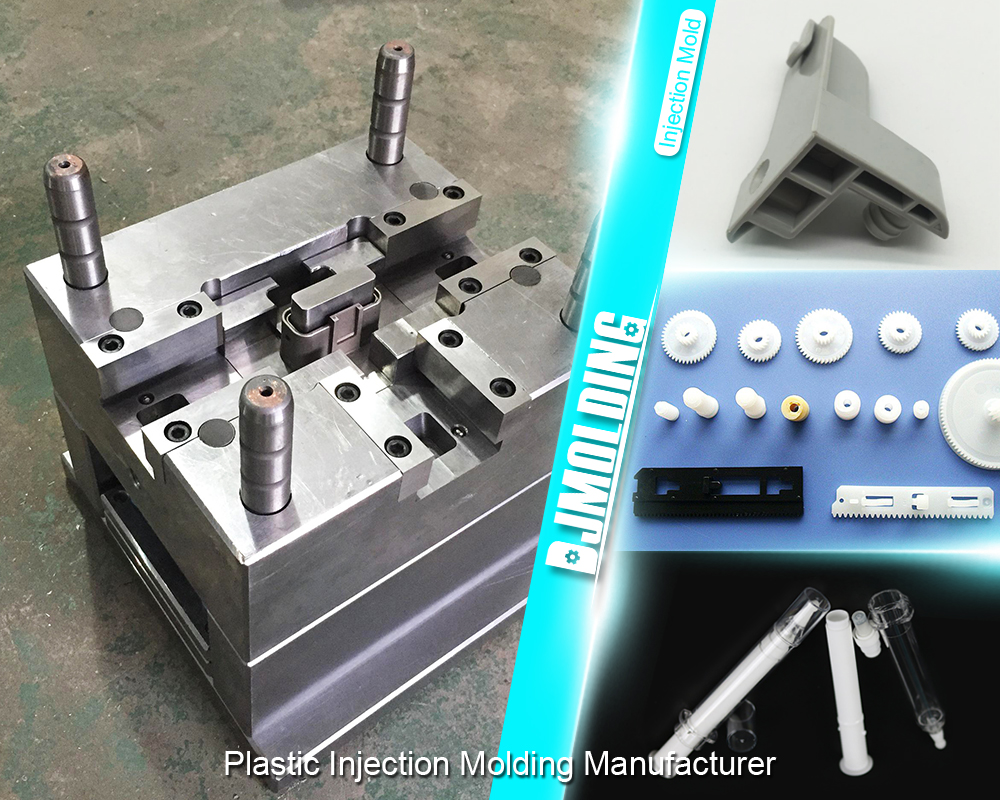
Conclusion
Low volume injection molding presents a cost-effective and efficient solution for small-scale production. Its advantages over traditional manufacturing methods, such as reduced costs, shorter lead times, and increased flexibility, have become a valuable option for various industries. By understanding the process, considering materials and design aspects, and selecting the right provider, businesses can leverage low volume injection molding to optimize their production strategies and achieve success in the market.
For more about low volume injection molding: cost-effective solutions for small scale plastic manufacturing,you can pay a visit to Djmolding at https://www.djmolding.com/low-volume-injection-molding/ for more info.