Tips And Tricks Of Maximizing Low Volume Injection Molding Cost For Small Batch Plastic Parts Manufacturer
Tips And Tricks Of Maximizing Low Volume Injection Molding Cost For Small Batch Plastic Parts Manufacturer
If you’re looking to produce small quantities of parts through injection molding, low-volume molding can be an ideal solution. However, the cost of low-volume injection molding can be higher per unit compared to high-volume molding. So, how can you maximize your investment? In this blog post, we’ll share some tried-and-true tips and tricks for minimizing costs and maximizing efficiency when it comes to low-volume injection molding. From selecting the right materials to optimizing your design, we’ve got you covered. Let’s dive in.
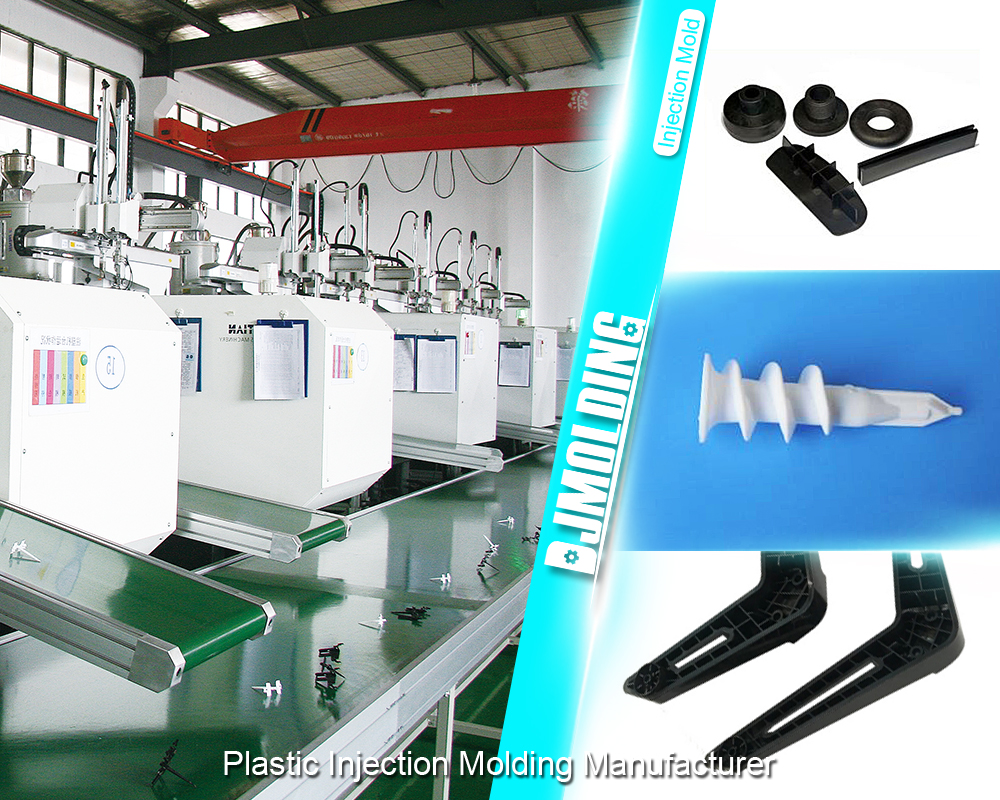
Factors affecting the cost of low-volume injection molding
Several factors can affect the cost of low-volume injection molding, including material selection, mold design and complexity, cycle time, and post-processing and finishing.
Material selection is a critical factor in the cost of low-volume injection molding. Different materials have different properties and requirements, and some materials are more expensive than others. Companies must consider the cost-effectiveness of materials when selecting them for their parts.
Mold design and complexity can also affect the cost of low-volume injection molding. More complex molds require more time and resources to produce, which can increase the cost of production. Additionally, molds with more cavities can produce more parts per cycle, reducing the overall cost per part.
Cycle time is another critical factor in the cost of low-volume injection molding. Longer cycle times can increase the cost of production, as they require more time and resources to produce each part. Companies must optimize their injection molding parameters to reduce cycle time and increase efficiency.
Tricks for optimizing mold design for low-volume injection molding
Optimizing mold design is another critical factor in cost optimization for low-volume injection molding. Companies can optimize their mold design by simplifying part design, reducing the complexity of mold design, and using multi-cavity molds.
Simplifying part design can help reduce the complexity of the mold and reduce production costs. By reducing the number of features and details in the part design, companies can produce parts more quickly and cost-effectively.
Reducing the complexity of mold design can also help reduce production costs. By simplifying the mold design, companies can reduce the time and resources required to produce each part.
Using multi-cavity molds can also help reduce production costs by producing more parts per cycle. Multi-cavity molds can produce multiple parts simultaneously, reducing the overall cost per part.
Strategies for selecting the right material for low-volume injection molding
Selecting the right material is critical to the success of low-volume injection molding. Companies must consider the material properties and requirements, cost-effectiveness of materials, and availability and lead time of materials when selecting materials for their parts.
Material properties and requirements are essential considerations when selecting materials for low-volume injection molding. Different materials have different properties, such as strength, flexibility, and durability, and companies must select materials that meet the requirements of their parts.
Cost-effectiveness is another critical consideration when selecting materials for low-volume injection molding. Some materials are more expensive than others, and companies must consider the cost-effectiveness of materials when selecting them for their parts.
Availability and lead time of materials are also important considerations when selecting materials for low-volume injection molding. Some materials may be in short supply or have long lead times, which can affect production schedules and costs.
Techniques for minimizing cycle time in low-volume injection molding
Minimizing cycle time is essential to cost optimization in low-volume injection molding. Companies can minimize cycle time by optimizing injection molding parameters, using hot runners and other advanced molding technologies, and properly maintaining equipment.
Optimizing injection molding parameters can help reduce cycle time and increase efficiency. Companies can optimize parameters such as injection speed, pressure, and temperature to produce parts more quickly and cost-effectively.
Using hot runners and other advanced molding technologies can also help reduce cycle time and increase efficiency. Hot runners are a type of injection molding system that uses heated channels to keep the plastic material in a molten state, reducing the time required to heat the material during each cycle.
Proper maintenance of equipment is also essential to minimizing cycle time and increasing efficiency. Regular maintenance and cleaning of equipment can help prevent downtime and ensure that equipment is operating at peak efficiency.
Best Practices For Post-Processing And Finishing Low-Volume Injection Molded Parts
Post-processing and finishing are critical steps in producing high-quality parts in low-volume injection molding. Companies can ensure the quality of their parts by properly trimming and deburring, using surface finishing techniques, and implementing quality control and inspection processes.
Proper trimming and deburring can help remove excess material and smooth out rough edges, ensuring that parts meet the required specifications. Surface finishing techniques, such as polishing and painting, can also help improve the appearance and functionality of parts.
Quality control and inspection processes are essential to ensuring the quality of parts in low-volume injection molding. Companies must implement processes to inspect and test parts for defects, such as cracks, warping, and dimensional accuracy.
Ways to Leverage Technology To Reduce Low-Volume Injection Molding Costs
Leveraging automation and technology is another way to reduce costs in low-volume injection molding. Companies can use robotics and automation in production, implement digital design and simulation tools, and integrate data analytics and process monitoring to increase efficiency and reduce costs.
Using robotics and automation in production can help reduce labor costs and increase efficiency. Robots can perform repetitive tasks, such as part removal and packaging, more quickly and accurately than humans.
Implementing digital design and simulation tools can help reduce the time and resources required to produce parts. These tools allow companies to design and test parts virtually, reducing the need for physical prototypes and tooling changes.
Integrating data analytics and process monitoring can help companies identify areas for improvement and optimize their production processes. By analyzing data on production performance, companies can identify inefficiencies and implement changes to increase efficiency and reduce costs.
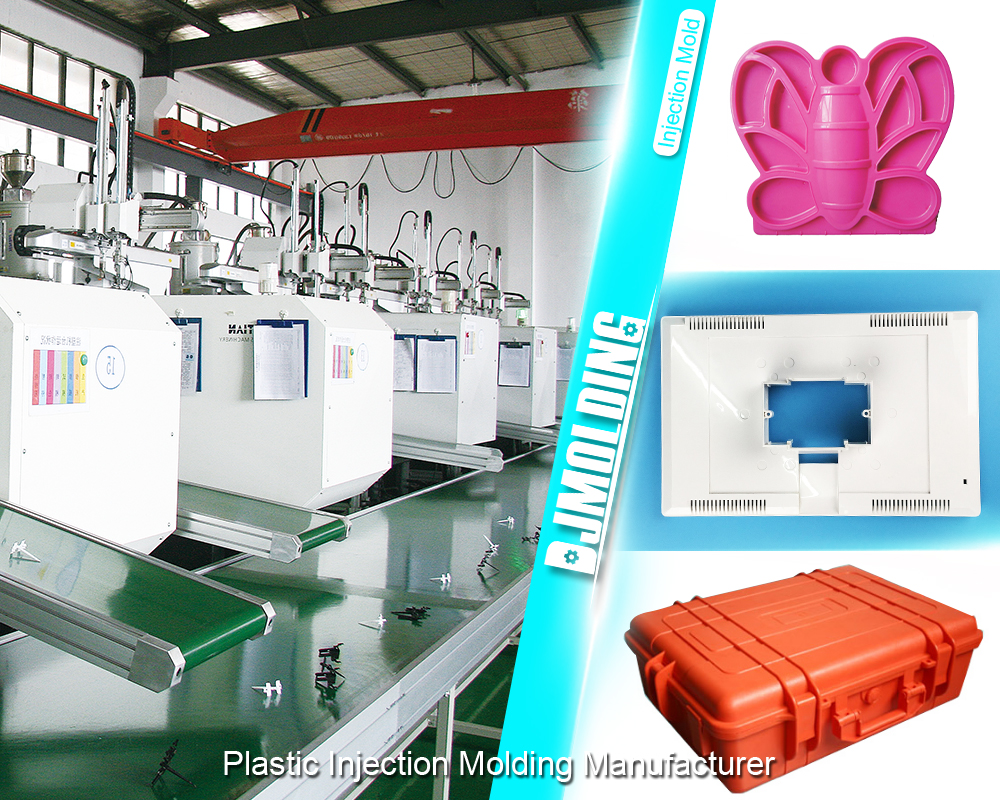
Final Thoughts On Maximizing Low-Volume Injection Molding Cost
In conclusion, low-volume injection molding is an essential part of product development, allowing companies to produce small quantities of high-quality parts quickly and cost-effectively. By optimizing their production processes and leveraging automation and technology, companies can reduce costs and increase efficiency in low-volume injection molding.
For more about tips and tricks of maximizing low volume injection molding cost for small batch plastic parts manufacturer,you can pay a visit to Djmolding at https://www.djmolding.com/low-volume-injection-molding/ for more info.