Custom Plastic Injection Molding
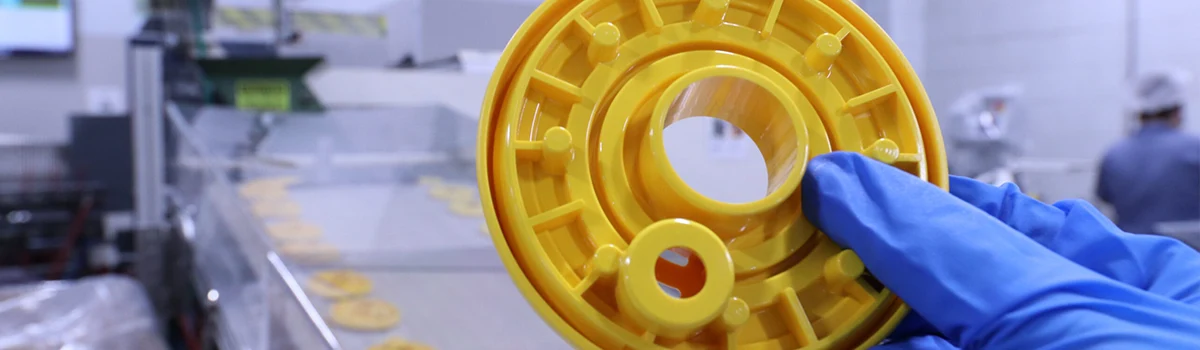
Custom injection molding is ideal for plastic parts where success relies on achieving specific mechanical or aesthetic features. DJmolding plastic injection molding is driven by the fundamental goal of helping customers produce the best plastic parts. No stranger to complexity, design challenges really stoke our desire to innovate for you. Involving us early enables us add value in the design process.
Benefits of Plastic Injection Molding
Detailed Features
Consider aesthetic or functional details to enhance your brand: imprinted text, cosmetic or textured surfaces, in-mold decorating, snap fits, flexible hinges, varied hardness.
High Efficiency
The efficiency of plastic injection molding is unmatched. We engineer unnecessary costs out of your part and tool. Our long-tenured design engineers and master molders really excel at this.
Enhanced Performance
We work hard to understand the intended function of your part and meet your key objectives by application of material science, design principles, analytical tools, and process controls.
Material Variety
Choose from more than 200 materials, commodity and engineering resins. We’ll help you balance performance and price and identify alternative material equivalents to reduce costs.
Injection Molding Process
Plastic injection molding is one of the oldest methods of manufacturing plastics and a critical step in the development of parts for product manufacturers. It’s also a great solution for manufacturers looking to convert heavy metal parts to plastic. Explained in its simplest form, the process uses polymers or plastic resins that when heated, melted and injected under high pressure into a custom mold, will produce plastic parts to be utilized in product manufacturing.
While that process seems straightforward, it can actually be quite complex and requires a high level of experience from an injection molder partner that can cater to your unique industry needs, specifications, end-uses and time / budget constraints. The best place to start is by gaining basic knowledge of the plastic molding process and design best practices.
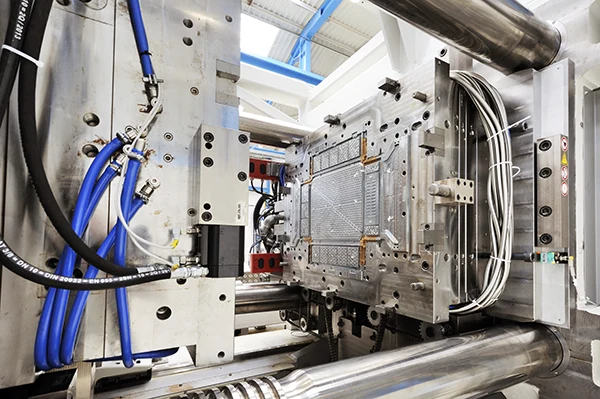
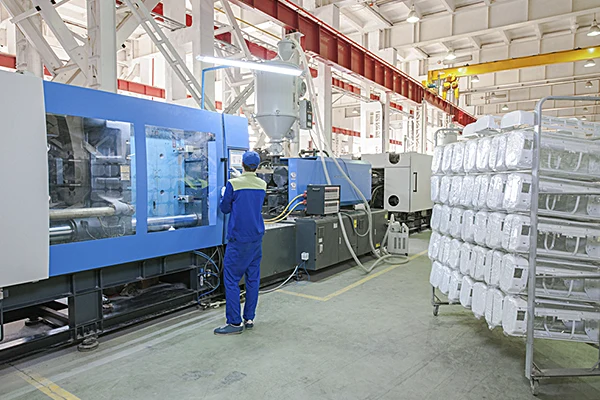
Scientific Molding
A scientific molding approach benefits the production of critical parts that demand specific performance and high precision. Our advanced molding technology ensures repeatability and consistency. That means the product we make for you today, is the product we make for you tomorrow.
Scientific injection molding begins during tooling development. Factors such as pressure, temperature, cavity fill time are optimized so that the mold design minimizes opportunities for variation. Mold flow analysis shows the last areas of the part to fill, how the material will orient with the mold, and exposes potential warp and stress points. It’s a proactive step that provides engineering predictive analysis and measurement and allows for easy determination of the success or failure of a part or project.
Robust production processes further utilize a scientific approach through monitoring and automated process controls which reduces scrap and processing time. Should a variation or malfunction occur, it is rapidly identified and isolated before nonconforming parts are made.
Overmolding
Two (or more) materials can be combined into a single part with overmolding. This process is often used for a distinct tactile surface, such as a softer grip area. Overmolding can be plastic over plastic substrate or rubber over plastic substrate, typically accomplished by a two-shot injection molding process. Resin formulation and colors can vary. The aesthetic advantages of overmolding are easy to notice, but they also eliminate secondary operations. Overmolding is perfect for tools with handgrips, hand-held objects, robotics where rubber grips are needed, or simply to enhance the appearance of a part with distinct colors.
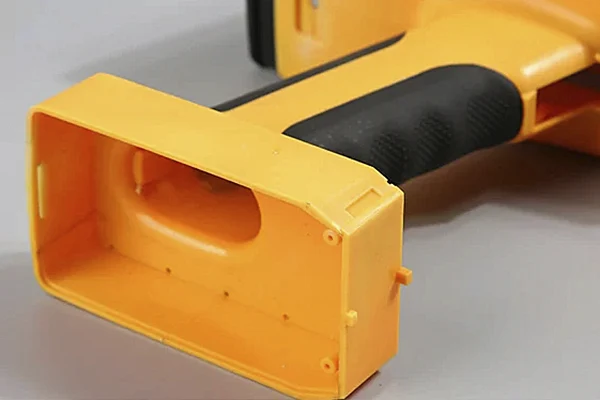
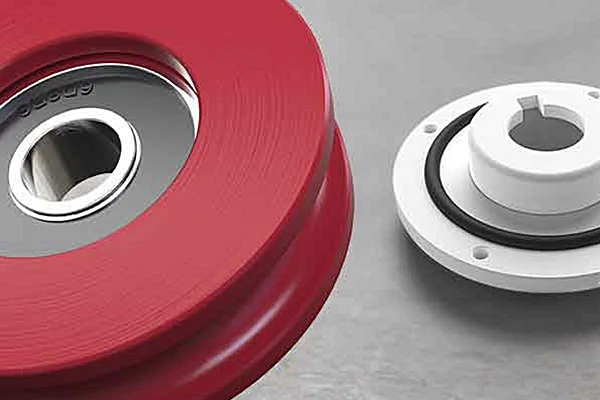
Insert Molding
Insert molding is similar to overmolding but incorporates an object that is placed within a mold cavity. Insert molding bonds plastic to inserts, typically metal or plastic. Threaded inserts are common. This eliminates labor when used as an alternative to fasteners, adhesives, or heat-staking. Inserts also strengthen the part. Inserts are loaded manually or with robotic automation.
Part Decorating and Labeling
In-mold decoration (IMD) and in-mold labeling (IML) are used to create a visually remarkable appearance with graphics or labels. Facilitated by robotics and electrostatic or vacuum grip, a printed film overlay is added to the mold cavity prior to the injection of molten plastic resin. This process creates a permanent bond between the label and the finished part, usually eliminating any need for post-processing operations. A wide range of texture, color, and surface coating choices leaves the door open for creative possibilities. We encourage you to talk to your project manager about options to enhance your brand.
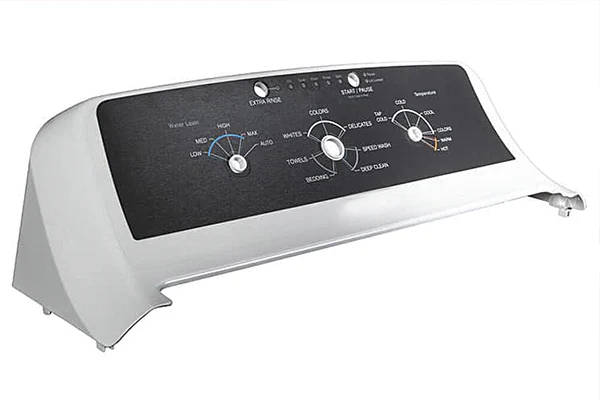
Custom Plastic Injection Molding Service China
DJmolding Operating since 2010 | AFAQ ISO/TS 16949, UL and ISO certifications,mainly supplying to many 3D Printing Company In the World Now.
At Djmolding we specialize in producing high-quality plastic injection molded parts and mold tools. We mainly supply our plastic injection manufacturing for many 3D print companies in the world. We have 55 machines for robotics and automatic plastic injection manufacturing.We offer all machining and finishing services to make tools from a variety of materials, and can produce 100 to 200k+ finished parts in all major plastics. What truly sets us apart is our advanced material verification, inspection and testing to ensure your parts meet and exceed your highest expectations. Contact our international injection molding experts for a free quote today.
DJmolding Plastic Injection Molding Process
Once your plastic injection mold tools are ready, the molding process consists of the following basic steps:
Step 1. The plastic resin comes in raw pellets. These are dried to the right moisture content, and then if necessary they can be blended with pigments or master batch colorants.
Step 2. The dried pellets are poured into the hopper of the molding machine. A reciprocating screw inside the barrel of the machine will transport these pellets towards the mold.
Step 3. Within the barrel, the pellets are mixed and heated until fully molten, forming the liquid resin.
Step 4. The heated mold closes automatically and resin, under great pressure, is injected through a gate and into the mold cavity.
Step 5. The mold is cooled to solidify the part inside.
Step 6. The mold opens and the part is ejected to begin a new cycle.
Plastic Injection Molding Tolerances
All plastic material will expand and contract under the influence of heat and moisture. Our tolerance guide will give more general information on the characteristics of most common resin types for typical part features.
We will work closely with you to optimize your designs for manufacturing. We will indicate any areas where poor design may produce thermal stress, shrinkage, warping, etc. Consult our design guide for more information on common defects and how to avoid them.
Unless otherwise specified, we comply with the DIN 16742 standard tolerances for plastic injection moldings. Read about the visual quality standards that we apply to injection molded parts.
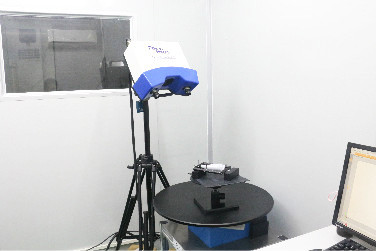
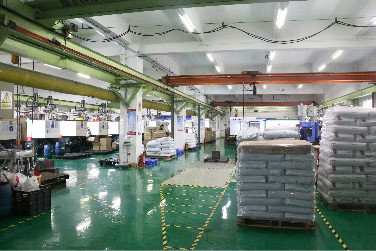
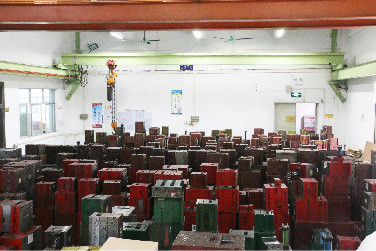
Plastic Injection Molding Materials
Djmolding make injection molding tools and dies from Aluminum 7075, P20 and NAK80 semi-hardened steels and H13 fully-hardened steel. Additionally, we offer standard SPI finishes, EDM texturing and a range of etched textures.
Each of these material types will have distinct advantages for certain applications. *Considerations include:
*Cost of the raw material
*Durability and resistance to corrosion or abrasion
*Machinability
*Ability to take a high surface polish
*Time required for heat treatment
*Expected tool life
Contact our technical specialists to learn more about which one is right for you.
Plastic Injected Parts
There are thousands of thermoforming and thermosetting plastics to choose from for your project. In addition, mechanical and chemical characteristics can also be enhanced with additives like glass fibers, UV stabilizers and lubricants. Our materials sheet will give you more detailed information about the standard types and the tolerances to expect with each.
Your choice of resins may depend upon one or more of the following considerations:
*UV, chemical, abrasion and impact resistance
*Cost of raw material
*Mechanical strength
*Weight and density
*Flexibility
*Transparency
*Recyclability
Contact one of our technical specialists to learn more about material properties.
DJmolding injection shop:
Leading plastic injection mold and rapid prototyping service manufacturer
Djmolding is one of the more well-knowm plastic injection molding companies in China. Our injection molding shop is equipped with 50 sets of high precision injection molding machines, ranging from 30 tons to 800 tons, They are mostly imported from Taiwan and Japan,our injection shop run 24 hours a day, 7 days a week ,and provide production services.
We are experienced with various plastic products for many industrial,including :automotive, medical, lighting, sports equipment, home appliances, and agriculture. Djmolding have pass AFAQ ISO/TS 16949, UL and ISO 9001 Certifications since 2010,We also have 15 IPQC people constantly watch our production and check part quality,This ensures our production maintains a highest level of quality. In the last 9 years,Djmolding has established a strong reputation of producing high quality tool and part at a resonable price.We maintain strong business relationships with appx. 50 customers,mainly from the USA and Europe.
Custom Plastic Injection Molding
Custom plastic injection molding is an innovative and efficient way of producing high-quality plastic parts. This manufacturing process uses a mold to shape plastic materials into complex shapes and sizes, making it an ideal solution for various industries. This blog post will dive deep into custom plastic injection molding and explore its benefits, applications, and best practices.
Understanding the custom injection molding process
Custom injection molding is a manufacturing process used to produce plastic parts in large volumes. It involves melting plastic pellets or granules and injecting them into a mold under high pressure, where they cool and solidify to form a desired shape. Here’s how the injection molding process works:
- Clamping: The two halves of the mold, called the “tool,” are clamped together with enough force to withstand the injection pressure.
- Injection: The plastic pellets are melted in a heated barrel and injected into the mold through a runner system under high pressure. The plastic fills the mold cavity and takes the shape of the mold.
- Cooling: The plastic can cool and solidify inside the mold to maintain the desired shape.
- Ejection: The mold opens once the plastic has cooled and the finished part is ejected.
- Repeat: The process is then repeated to create multiple identical parts.
Injection molding produces plastic products, from small components to large items like automotive parts and home appliances. The process is highly efficient and can produce parts with complex geometries and tight tolerances, and it’s also exact, with minimal waste and low scrap rates.
The process requires specialized equipment, including a mold, injection molding machine, and a control system to ensure accurate and consistent results. The mold is typically made of steel and can be designed to produce multiple parts using multi-cavity molding.
Injection molding can also be used with various materials, including thermoplastics, thermosets, and elastomers. Each material has unique properties and can be tailored to specific applications.
Overall, injection molding is a highly versatile and efficient manufacturing process widely used in many industries.
Advantages of custom plastic injection molding
Custom plastic injection molding is a manufacturing process used to create custom plastic parts in large volumes. Here are some of the advantages of this process:
High efficiency and productivity: Custom plastic injection molding is a highly efficient process that can produce large volumes of identical parts quickly and consistently. This makes it an ideal choice for the mass production of plastic parts.
Versatility: The process can be used with a wide range of plastic materials, including thermoplastics, thermosets, and elastomers. This allows for a wide variety of part designs and applications.
Consistency and precision: Injection molding provides consistent and precise results, with tight tolerances and minimal variation between parts. This ensures that each piece is identical to the next, which is essential for many applications.
Cost-effective: Custom plastic injection molding can be cost-effective for high-volume production runs. The initial tooling costs can be high, but the cost per part decreases as the volume increases.
Complexity: Injection molding can produce parts with complex shapes and geometries, including thin walls and intricate features. This allows for greater design flexibility and enables the production of factors that would be difficult or impossible to produce using other methods.
Minimal waste: Injection molding generates minimal waste compared to other manufacturing processes, as any excess plastic can be recycled and reused.
Surface finish: Injection molding can produce parts with a high-quality surface finish without additional post-processing or finishing operations. This makes it a cost-effective solution for creating pieces with a smooth and polished appearance.
Automation: Injection molding can be easily automated, with robots loading and unloading parts from the mold and inspecting and sorting features. This reduces the need for manual labor and increases efficiency.
Custom plastic injection molding is a highly versatile and efficient manufacturing process offering many advantages over other methods. Its ability to quickly and accurately produce large volumes of identical parts makes it ideal for many industries, including automotive, aerospace, medical, and consumer goods.
Applications of injection molding
Injection molding is a widely used manufacturing process to create various industrial plastic products. Here are some of the most common applications of injection molding:
- Automotive industry: Injection molding produces various automotive parts, including interior and exterior trim, dashboard components, door handles, and engine parts. It is preferred because it can have features with high strength and dimensional accuracy.
- Consumer goods: Injection molding creates various consumer products, including toys, household appliances, and electronic devices. It allows for producing complex shapes and geometries and high-quality surface finishes.
- Medical devices: Injection molding is used to produce a variety of medical devices, including syringes, IV components, and diagnostic equipment. It offers high precision, clean manufacturing, and the ability to produce parts with complex geometries, which are essential in the medical industry.
- Packaging industry: Injection molding produces packaging materials, including bottles, jars, and lids. It allows for creating lightweight and durable containers and customizing colors, textures, and shapes.
- Aerospace industry: Injection molding is used to produce various components of aerospace parts, including structural elements and interior fittings. It allows for creation of high-performance materials that can withstand extreme temperatures and pressures.
- Construction industry: Injection molding produces various construction materials, including PVC pipes, gutter systems, and roofing materials. It offers high durability, resistance to weather and chemicals, and the ability to produce parts in large volumes.
- Electronics industry: Injection molding produces various electronic components, including housing, connectors, and switches. It offers high precision, uniformity, and the ability to produce parts with complex geometries, which is essential in the electronics industry.
Overall, injection molding is a versatile manufacturing process that can produce many plastic parts for many industries. Its ability to produce parts with complex geometries, high precision, and consistent quality makes it a popular choice for many manufacturers.
Types of materials used in injection molding
Injection molding is a manufacturing process that involves injecting molten plastic into a mold cavity to create a specific shape. Different materials can be used in injection molding, depending on the desired properties of the final product. Here are some of the most common types of materials used in injection molding:
- Thermoplastics: These are the most commonly used materials in injection molding. They are a type of plastic that becomes soft and moldable when heated and hardens when cooled. Thermoplastics can be molded and remolded multiple times without losing their properties. Common thermoplastics used in injection molding include polypropylene, polyethylene, polystyrene, and nylon.
- Thermosets: These are plastics that can only be molded once. They are heated and developed into a specific shape, and once they harden, they cannot be remolded. Thermosets are used for applications where high strength and durability are required. Common thermosets used in injection molding include epoxy, melamine, and phenolic resins.
- Elastomers: These materials have elastic properties and can stretch and return to their original shape. Elastomers are used for applications where flexibility and shock absorption are required. Standard elastomers used in injection molding include rubber, silicone, and polyurethane.
- Biodegradable materials: These can break down naturally in the environment without leaving harmful residues. They are used for applications where environmental sustainability is a concern. Common biodegradable materials used in injection molding include polylactic acid (PLA) and polyhydroxyalkanoates (PHAs).
- Composites are materials made by combining two or more different materials to create a new material with specific properties. Composites are used for applications where high strength and stiffness are required. Standard composites used in injection molding include glass fiber-reinforced plastics (GRP) and carbon fiber-reinforced plastics (CFRP).
- Metal-filled plastics are plastics infused with metal particles to create materials with high electrical and thermal conductivity and other specific properties. Metal-filled plastics are used for applications with necessary electrical or thermal conductivity. Common metal-filled plastics used in injection molding include copper-filled plastics and nickel-filled plastics.
Overall, the choice of injection molding material depends on the final product’s specific requirements, including strength, flexibility, conductivity, and durability. Manufacturers often select materials based on cost, availability, ease of processing, and the properties required for the final product.
Factors to consider when selecting an injection molding material
Selecting a suitable material is crucial when it comes to injection molding, as it can affect the properties and performance of the final product. Here are some of the factors to consider when selecting an injection molding material:
- Mechanical properties: One of the most important factors to consider when selecting a material is its mechanical properties. This includes its strength, stiffness, toughness, and resistance to wear and tear. The mechanical properties required for the final product will depend on the application and the stresses to which the product will be exposed.
- Thermal properties: The thermal properties of a material are also important, especially if the final product will be exposed to high temperatures or thermal cycling. This includes the material’s melting point, thermal conductivity, and coefficient of thermal expansion.
- Chemical resistance: If the final product is exposed to chemicals, selecting a material that can resist chemical degradation is essential. The material should withstand exposure to acids, bases, solvents, and other chemicals without breaking down or losing its properties.
- Environmental factors: Environmental factors, such as humidity and UV exposure, can also affect the properties and performance of a material. It’s essential to consider the final product’s environmental conditions and select a material that can withstand them.
- Cost: The cost of the material is also an important consideration, especially for high-volume production runs. The cost of the material should be weighed against its performance and properties to ensure that it is a cost-effective choice for the final product.
- Processing requirements: The processing requirements for a material can also affect the selection process. Some materials may require specific processing equipment or techniques, and some may be more difficult to process. The processing requirements should be considered to ensure the material can be successfully used in the injection molding process.
- Regulatory compliance: Finally, it’s essential to consider any regulatory requirements that the final product must meet. Some industries, such as the medical and food industries, have specific regulations for the materials used in their products. Selecting a material that meets these regulatory requirements is essential to ensure the final product is safe and compliant.
Overall, selecting the suitable material for injection molding requires careful consideration of various factors, including mechanical and thermal properties, chemical resistance, environmental factors, cost, processing requirements, and regulatory compliance. Manufacturers must weigh these factors against each other to select the material that is the best fit for the final product.
The importance of mold design in injection molding
Mold design is a critical aspect of the injection molding process. The design of the mold can affect the quality of the final product, as well as the efficiency and cost-effectiveness of the manufacturing process. Here are some of the reasons why mold design is essential in injection molding:
- Product quality: The mold’s design can affect the final product’s quality. If the mold is not designed properly, it can result in defects such as warping, sink marks, and flash. These defects can make the final product unusable, reduce performance, and increase scrap rates and production costs.
- Manufacturing efficiency: The design of the mold can also affect the efficiency of the manufacturing process. If the mold is not designed for optimal flow and cooling, it can result in longer cycle times, increased energy consumption, and reduced throughput. An optimized mold design can improve efficiency and reduce production costs.
- Cost-effectiveness: Mold design can also affect the cost-effectiveness of the injection molding process. A well-designed mold can reduce material waste, improve part quality, and increase throughput, reducing production costs. Additionally, a mold designed for high-volume production can reduce the cost per part and increase the return on investment.
- Customization: Mold design also plays a vital role in the customization of the final product. By designing the mold for specific shapes and features, manufacturers can create products tailored to their customers’ needs. This allows for greater flexibility and differentiation in the market, leading to increased customer satisfaction and loyalty.
- Material selection: The mold design can also influence the choice of the material used in injection molding. The molding method can affect the material flow and cooling, which can impact the mechanical and thermal properties of the final product. By selecting the right mold design, manufacturers can optimize the material selection and ensure that the final product meets the desired performance requirements.
Overall, mold design is a critical factor in the injection molding process. A well-designed mold can improve product quality, manufacturing efficiency, cost-effectiveness, customization, and material selection. Manufacturers must invest time and resources into designing optimized molds for their specific needs to achieve the best possible results in the injection molding process.
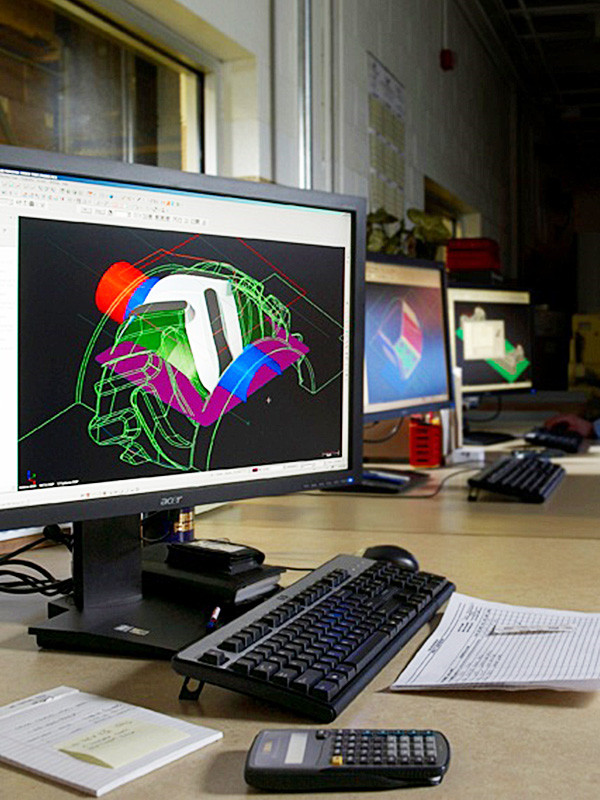
Different types of molds used in injection molding
Injection molding is a versatile manufacturing process that can produce various plastic products. One critical factor determining the quality and efficiency of injection molding is the type of mold used. Here are some of the different types of molds used in injection molding:
- Two-plate mold: Two-plate molds are the most common mold used in injection molding. They consist of two plates that are separated by a mold cavity. The plastic material is injected into the cavity, combining the two plates to form the final product.
- Three-plate mold: Three-plate molds are similar to two-plate molds but have an additional plate separating the runner system from the molded part. This allows for easier ejection of the part and can reduce cycle time.
- Hot runner mold: Hot runner molds are used for high-volume production runs, as they can reduce cycle time and material waste. The mold contains a heated runner system that delivers molten plastic directly to the mold cavity, eliminating the need for a cold runner.
- Cold runner mold: Cold runner molds are the most basic type of mold and consist of a sprue, runners, and a mold cavity. The molten plastic is injected into the sprue, which feeds the plastic into the runners and then into the mold cavity.
- Family mold: Family molds produce multiple parts in a single cycle. The mold contains multiple cavities, each of which has a different part. Family molds are often used for small, high-volume components.
- Stack mold: Stack molds produce multiple layers of plastic in a single cycle. The mold contains numerous layers of cavities, which are stacked on top of each other. The plastic is injected into the holes, and the layers are then brought together to form a single, multi-layered product.
- Insert mold: Insert molds are used to insert metal or plastic components into the molded part during the molding process. The insert is placed into the mold cavity before the plastic is injected, and the plastic then surrounds the insert.
Overall, the type of mold used in injection molding depends on the specific requirements of the product being produced. By selecting the correct type of mold, manufacturers can optimize the injection molding process’s efficiency, quality, and cost-effectiveness.
Best practices for injection molding
Injection molding is a complex manufacturing process that requires careful planning and execution to achieve the desired results. Here are some best practices for injection molding that can help ensure optimal quality, efficiency, and cost-effectiveness:
- Design for manufacturability: The product’s design should be optimized for injection molding. This includes minimizing the number of parts, ensuring uniform wall thickness, and avoiding undercuts and other features that complicate molding.
- Material selection: The material used in injection molding should be selected based on the product’s requirements. Factors such as mechanical properties, thermal properties, and environmental resistance should be considered.
- Mold design: The mold design should be optimized for the specific product. This includes ensuring proper cooling, venting, and gating, as well as selecting the appropriate type of mold.
- Injection parameters: The injection parameters, such as injection pressure, temperature, and speed, should be carefully controlled and monitored to ensure optimal quality and consistency.
- Maintenance: Regular injection molding machine and mold maintenance are critical to ensuring optimal performance and preventing downtime.
- Quality control: Quality control should be implemented throughout the injection molding process, from incoming material inspection to final product inspection. This includes monitoring defects such as warpage, sink marks, and flash.
- Process optimization: Continuous process improvement should be a key focus of injection molding operations. This includes monitoring process performance metrics such as cycle time, scrap rate, and machine utilization and making adjustments as necessary to optimize efficiency and quality.
Overall, injection molding requires careful attention to detail and a focus on continuous improvement. By following best practices for injection molding, manufacturers can ensure optimal quality, efficiency, and cost-effectiveness and produce high-quality plastic products that meet the needs of their customers.
Quality control measures for injection molding
Quality control is critical to injection molding, as it ensures that the final product meets the required specifications and standards. Here are some quality control measures for injection molding:
- Incoming material inspection: The quality control process should begin with a review of the raw material used for injection molding. This includes verifying that the material is the correct type, grade, and color and meets the required mechanical and thermal properties specifications.
- In-process inspection: During injection molding, quality control personnel should regularly inspect the product to ensure it is being molded correctly. This includes monitoring for defects such as sink marks, warping, and flash and verifying that the product meets the required dimensional tolerances.
- Final product inspection: Once the injection molding process is complete, the final product should be inspected to ensure it meets the required specifications and standards. This includes verifying that the product is free from defects, such as cracks, bubbles, and voids and meets the required dimensional tolerances.
- Statistical process control: Statistical process control (SPC) is a method of monitoring and controlling a process to ensure that it produces consistently high-quality results. SPC involves collecting data on critical process parameters, such as injection pressure and temperature, and using statistical analysis to identify trends and patterns that indicate process variability.
- Continuous improvement: Quality control should be an ongoing process of constant improvement. This includes analyzing data on process performance, identifying areas for improvement, and making changes to the process to optimize quality and efficiency.
- Documentation and traceability: Quality control personnel should maintain detailed documentation of the injection molding process, including process parameters, inspection results, and corrective actions. This documentation provides traceability and helps ensure that any quality issues can be identified and corrected quickly.
Overall, quality control is a critical aspect of injection molding and should be integrated into every aspect of the manufacturing process. By implementing these quality control measures, manufacturers can produce high-quality plastic products that meet the needs of their customers.
Common defects in injection molding and how to prevent them
Injection molding is a complex process that can result in defects if improperly executed. Here are some common defects in injection molding and how to prevent them:
- Sink marks are depressions or dents on the product’s surface. They are caused by uneven cooling or insufficient packing pressure. Ensure the mold design includes uniform wall thickness and sufficient draft angles to prevent sink marks. Adjusting the packing pressure and cooling time can also help prevent sink marks.
- Warpage: Warpage is the distortion of the product after it has been removed from the mold. It is caused by uneven cooling or internal stresses in the product. To prevent warpage, ensure the mold design includes uniform wall thickness and sufficient cooling time. Avoid sharp corners or sudden changes in the product geometry, which can create stress points.
- Flash: Flash is excess plastic that extends beyond the product boundaries, typically occurring around the edges of the mold. It is caused by excessive injection pressure, insufficient clamping force, or a worn mold. To prevent flash, adjust the injection pressure and clamping force and regularly inspect the mold for signs of wear.
- Short shots: Short shots occur when the mold is partially filled with plastic. This can be caused by insufficient injection pressure or temperature or a blocked or restricted flow channel. To prevent short shots, adjust the injection pressure and temperature, and ensure the flow channel is clear and unobstructed.
- Burn marks: Burn marks are dark discolorations on the product’s surface caused by overheating or excessive friction in the mold. To prevent burn marks, ensure the mold is adequately cooled and lubricated, and adjust the injection speed and pressure as necessary.
- Voids and bubbles: Voids and bubbles are product areas missing material or containing air pockets. They are caused by trapped air or gas in the mold or insufficient material flow. To prevent voids and bubbles, ensure that the mold is vented correctly and that the injection speed and pressure are sufficient to ensure uniform material flow.
Maintenance tips for injection molding equipment
Injection molding equipment is a significant investment for manufacturers, and proper maintenance is essential to ensure optimal performance and longevity. Here are some maintenance tips for injection molding equipment:
- Conduct regular inspections: Inspect the equipment regularly to identify any wear and tear, damage, or other issues. Inspect the hydraulic hoses, seals, and other critical components to ensure they are in good condition.
- Clean and lubricate the equipment: Clean and lubricate the equipment regularly to prevent corrosion and wear. Use the recommended cleaning and lubrication products, and follow the manufacturer’s instructions.
- Monitor and maintain hydraulic oil: Monitor it regularly to ensure it is clean and at the correct viscosity. Change the oil as needed, and use the recommended oil type.
- Maintain the heater bands: Check them regularly to ensure they are in good condition and heating correctly. Replace any damaged or worn heater bands immediately.
- Monitor and maintain the cooling system: It is critical to the injection molding, as it prevents overheating and warpage. Monitor the cooling system regularly to ensure it functions correctly, and clean the cooling channels as needed.
- Train operators: Train operators on proper equipment operation and maintenance procedures to prevent damage and ensure optimal performance.
- Schedule regular maintenance: Establish a maintenance schedule and stick to it. Schedule routine maintenance tasks, such as lubrication and oil changes, and document all maintenance activities.
- Keep spare parts on hand: Provide spare parts, such as hydraulic hoses, seals, and heater bands. This will quickly replace damaged or worn parts and minimize downtime.
Proper maintenance of injection molding equipment is essential to ensure that it operates efficiently, produces high-quality products, and has a long lifespan. By following these maintenance tips, manufacturers can keep their equipment in top condition and minimize downtime and repair costs.
How to choose the proper injection molding manufacturer
Choosing the proper injection molding manufacturer is an important decision that can significantly impact the quality and cost of your products. Here are some factors to consider when choosing an injection molding manufacturer:
- Experience and expertise: Look for a manufacturer with extensive experience and expertise in injection molding. Ask about their manufacturing processes, quality control measures, and certifications.
- Technology and equipment: Look for a manufacturer that uses modern technology and equipment. This can help ensure consistent quality, shorter lead times, and cost-effectiveness.
- Materials and capabilities: Consider the types of materials the manufacturer can work with and their abilities. Look for a manufacturer that can handle a wide range of materials, including specialized materials, and can produce a variety of product sizes and shapes.
- Quality control measures: Look for a manufacturer that strongly focuses on quality control. Ask about their quality control measures, such as inspection and testing procedures, and any certifications they may have.
- Customer service: Look for a manufacturer that provides excellent customer service. Consider responsiveness, communication, and willingness to work with you to meet your specific needs.
- Cost and lead time: Consider the manufacturer’s cost and lead time for your project. Look for a manufacturer that offers competitive pricing and realistic lead times that meet your requirements.
- References and reviews: Ask for references and check online reviews of the manufacturer. This can help you get a better sense of their reputation and the experiences of other customers.
You can choose the proper injection molding manufacturer for your project by considering these factors and conducting thorough research. A reputable manufacturer with the right experience, capabilities, and commitment to quality can help ensure that your products are produced efficiently, cost-effectively, and to your exact specifications.
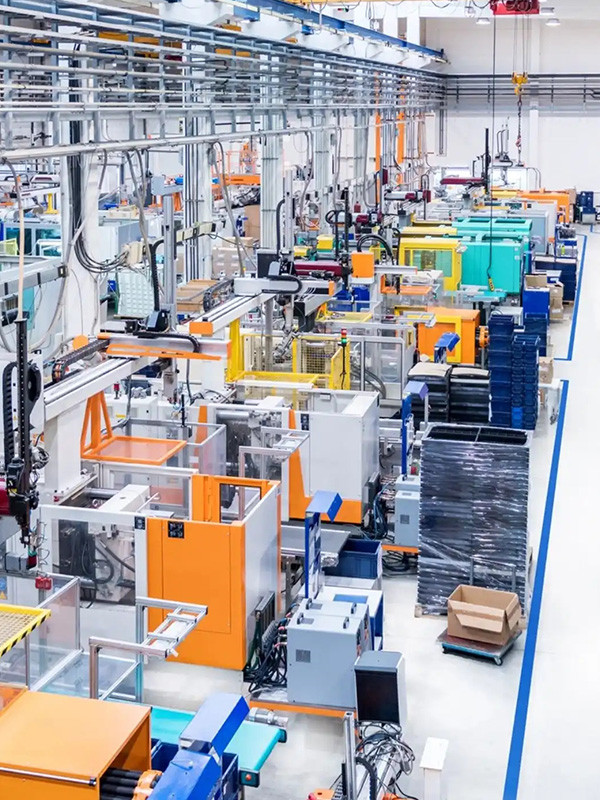
Cost Considerations in custom plastic injection molding
Custom plastic injection molding is a highly versatile manufacturing process that can produce complex, high-quality parts at scale. However, cost considerations are a critical factor in using this manufacturing process. Here are some key cost considerations in custom plastic injection molding:
- Material costs: The type and quantity of material used in the injection molding process will affect the price. Some materials, such as high-performance engineering plastics, are more expensive than others. The cost of materials can also be affected by supply chain disruptions, market demand, and price fluctuations.
- Tooling costs: The cost of tooling, or the molds used to produce the parts, is a significant expense in custom plastic injection molding. The part’s complexity, the number of cavities in the mold, and the material used to create the mold will all affect the tooling cost. Tooling can be expensive upfront but can help lower unit costs over time by increasing production efficiency.
- Production volume: The volume of parts produced will impact the injection molding cost. High-volume production can help reduce unit costs, while low-volume production may have higher unit costs due to the need for more tooling and setup time.
- Labor costs: Labor costs are a significant factor in injection molding, especially for more complex parts that require more manual labor. The skill level of the operators and the complexity of the part will affect the delivery cost.
- Quality control costs: Maintaining quality control is essential to ensure the parts’ integrity. The price of quality control can include inspection equipment, testing, and labor.
- Shipping costs: Shipping the parts to the customer or other locations can be a significant expense, especially for large or heavy details.
Manufacturers can produce high-quality parts at a lower cost by considering these cost factors and optimizing the injection molding process. This can be achieved by reducing material waste, increasing production efficiency, and minimizing setup and changeover times. Working with an experienced and knowledgeable injection molding manufacturer can also help optimize the process and reduce costs.
Trends and innovations in injection molding technology
Injection molding technology has been around for many years, but there are still many innovations and trends shaping this manufacturing process’s future. Here are some of the top trends and innovations in injection molding technology:
- 3D printing and additive manufacturing: 3D printing and additive manufacturing are becoming increasingly popular in the injection molding industry. This technology allows for creation of complex shapes and geometries that are difficult or impossible to achieve with traditional injection molding.
- Multi-material injection molding: Multi-material injection molding allows for creation of parts with multiple materials or colors in a single shot. This process can reduce manufacturing time and costs and create functions with unique properties and appearances.
- Automation and Industry 4.0: Automation and Industry 4.0 technologies, such as IoT sensors and robotics, are being integrated into injection molding machines and processes. This can improve production efficiency, reduce labor costs, and improve quality control.
- Sustainable materials and processes: As companies seek to reduce their environmental impact, sustainable materials and methods are becoming more important in the injection molding industry. This includes using biodegradable or recycled materials and processes that minimize waste and energy consumption.
- Smart manufacturing and predictive maintenance: Smart manufacturing technologies, such as machine learning and predictive maintenance, are being used to optimize injection molding processes and reduce downtime. This can improve overall efficiency and reduce maintenance costs.
- High-performance materials: New high-performance materials are being developed for injection molding, including materials with improved strength, durability, and heat resistance. These materials can be used in various applications, from automotive parts to medical devices.
By staying up-to-date on these trends and innovations, injection molding manufacturers can remain competitive and continue to provide high-quality parts to their customers. As new technologies and materials are developed, the injection molding industry will continue to evolve and adapt to meet the changing needs of consumers and businesses.
Sustainability in injection molding: reducing waste and energy consumption
Sustainability is becoming increasingly important in the injection molding industry as companies seek to reduce their environmental impact and meet the growing demand for eco-friendly products. Here are some ways that injection molding manufacturers can reduce waste and energy consumption:
- Use sustainable materials: The choice of material is a critical factor in sustainability. Injection molding manufacturers can use biodegradable or recycled materials to reduce environmental impact. Biodegradable plastics, for example, can break down naturally over time and reduce the amount of waste in landfills. Recycled materials, such as post-consumer recycled plastics, can also help reduce waste and energy consumption.
- Reduce material waste: Injection molding manufacturers can also reduce material waste by optimizing the design of the part and the mold. This includes reducing the amount of excess material used, minimizing the number of cavities in the mold, and reducing the overall weight of the part. By reducing material waste, manufacturers can save on material costs and reduce their environmental impact.
- Optimize production efficiency: Injection molding manufacturers can optimize their production processes to reduce energy consumption. This includes using high-efficiency injection molding machines, optimizing the molding process parameters, and minimizing downtime. By reducing energy consumption, manufacturers can save on energy costs and reduce their carbon footprint.
- Implement sustainable practices: Injection molding manufacturers can also implement sustainable practices in their operations, such as recycling and waste reduction programs, using renewable energy sources, and promoting sustainability among their employees and suppliers. By promoting sustainable practices throughout the supply chain, manufacturers can help create a more sustainable industry overall.
- Use sustainable packaging: Finally, injection molding manufacturers can use sustainable packaging materials and designs to reduce waste and environmental impact. This includes using biodegradable or recyclable packaging materials, minimizing packaging waste, and designing reusable or refillable packaging.
By implementing these sustainable practices, injection molding manufacturers can reduce their environmental impact and create a more sustainable industry overall. As sustainability becomes increasingly important for consumers and businesses, injection molding manufacturers prioritizing sustainability will be well-positioned to meet the growing demand for eco-friendly products.
How custom plastic injection molding compares to other manufacturing processes
Custom plastic injection molding is a popular manufacturing process for producing high-quality plastic parts in large quantities. However, several other manufacturing processes can be used to make plastic parts, each with advantages and disadvantages. Here is a comparison of custom plastic injection molding with other manufacturing processes:
- 3D Printing: 3D printing is a rapidly growing technology that allows for creation of complex shapes and geometries. While 3D printing can be used for small-scale production, injection molding is generally less cost-effective and efficient than injection molding for producing large parts.
- Blow Molding: Blow molding is a manufacturing process that creates hollow plastic parts, such as bottles and containers. While blow molding is suitable for producing high volumes of features, injection molding is generally less precise than injection molding and may not be ideal for creating more complex shapes and geometries.
- CNC Machining: CNC machining is a subtractive manufacturing process that involves cutting and shaping parts from a solid block of material. While CNC machining is suitable for producing high-precision parts in small quantities, it is generally not as cost-effective or efficient as injection molding.
- Rotational Molding: Rotational molding is a manufacturing process that involves rotating a mold around two perpendicular axes while heating it. While rotational molding can produce large parts with complex geometries, injection molding is generally less precise than injection molding and may not be suitable for making smaller parts.
- Thermoforming: Thermoforming is a manufacturing process that involves heating a plastic sheet and then shaping it over a mold. While thermoforming can produce large parts with simple geometries, injection molding is generally less precise than injection molding and may not be suitable for creating more complex shapes and geometries.
Custom plastic injection molding is a highly versatile and cost-effective manufacturing process for producing high-quality plastic parts in large quantities. While other manufacturing processes may be better suited for specific applications or production volumes, injection molding is generally the preferred choice for many manufacturers due to its speed, precision, and cost-effectiveness. Ultimately, the choice of manufacturing process will depend on various factors, including the part design, production volume, and budget.
Pros and cons of outsourcing injection molding
Outsourcing injection molding is a common practice for companies looking to produce plastic parts without investing in their own injection molding equipment or expertise. While outsourcing can offer several benefits, it also has some potential drawbacks. Here are some pros and cons of outsourcing injection molding:
Pros:
- Cost Savings: Outsourcing injection molding is often more cost-effective than setting up an in-house production facility. This is especially true for small to medium-sized companies that need more money or volume to justify investing in expensive equipment and personnel.
- Expertise: Injection molding companies specialize in manufacturing and have the expertise to ensure that parts are produced to a high-quality standard. By outsourcing injection molding, companies can benefit from the expertise of experienced professionals.
- Capacity: Injection molding companies can produce large quantities of parts quickly and efficiently. This is especially beneficial for companies that must regularly make large volumes of features.
- Flexibility: Outsourcing injection molding allows companies to be more flexible in their production schedules. Companies can adjust their production volumes or switch to different parts without worrying about the capital costs of changing equipment and molds.
Cons:
- Communication: Outsourcing injection molding can create communication challenges between the customer and the company. Misunderstandings or delays in communication can result in mistakes or delays in production.
- Quality Control: Outsourcing injection molding means relying on an outside company to produce parts to the required quality standards. Quality control can be challenging when working with an outside company, and there is always the risk of receiving features that must meet the required specifications.
- Dependence: Outsourcing injection molding means depending on an outside production company. This can create risks regarding the supplier’s reliability, stability, and delivery times.
- Intellectual Property: Outsourcing injection molding can create risks for protecting intellectual property. Companies need to ensure that their designs and technology are protected by appropriate legal measures.
Future prospects for custom plastic injection molding
Custom plastic injection molding has been a reliable and versatile manufacturing process for several decades. In recent years, advancements in technology and materials have continued to enhance the capabilities and potential of injection molding. Here are some future prospects for custom plastic injection molding:
- Adoption of Industry 4.0 technologies: The integration of Industry 4.0 technologies, such as artificial intelligence, machine learning, and the Internet of Things (IoT), is expected to increase automation, improve quality control, and optimize production processes in injection molding.
- Increasing use of biodegradable materials: Environmental concerns drive the adoption of biodegradable materials in injection molding. Biodegradable materials offer a sustainable alternative to traditional plastics and can help reduce waste and environmental impact.
- Growing demand for medical device manufacturing: The need for medical devices is increasing due to the aging population and advancements in medical technology. Injection molding is a popular manufacturing process for medical devices due to its precision, speed, and cost-effectiveness.
- Expansion of 3D printing capabilities: The development of 3D printing technology has enabled the production of complex and intricate parts that were previously impossible to manufacture using injection molding. However, 3D printing is still relatively slow and expensive compared to injection molding, and the two technologies will likely continue to complement each other rather than replace one another.
- Increasing multi-material injection molding: Multi-material injection molding involves using two or more different materials in a single injection molding process. This technology offers several benefits, including improved part performance, reduced weight, and cost savings.
- Advancements in tooling technology: The development of new tooling materials and designs is expected to increase the speed, efficiency, and precision of injection molding. For example, conformal cooling channels in tooling can improve cycle times and reduce energy consumption.
Conclusion:
Custom plastic injection molding is a robust manufacturing process that enables the production of high-quality plastic parts with great precision and efficiency. By understanding the injection molding process, selecting suitable materials and mold designs, and implementing best practices for quality control and equipment maintenance, businesses can optimize their injection molding operations and achieve tremendous success. As new trends and innovations emerge in the industry, staying up-to-date and exploring new opportunities to enhance the sustainability, efficiency, and profitability of custom plastic injection molding is essential.