Liquid Silicone Rubber(LSR) Injection Molding Suppliers: A Comprehensive Guide
Liquid Silicone Rubber(LSR) Injection Molding Suppliers: A Comprehensive Guide
This blog post provides a comprehensive guide to Liquid Silicone Rubber(LSR) Injection Molding, covering the basics of LSR injection molding, its benefits, the injection molding process, applications, and the future of LSR.
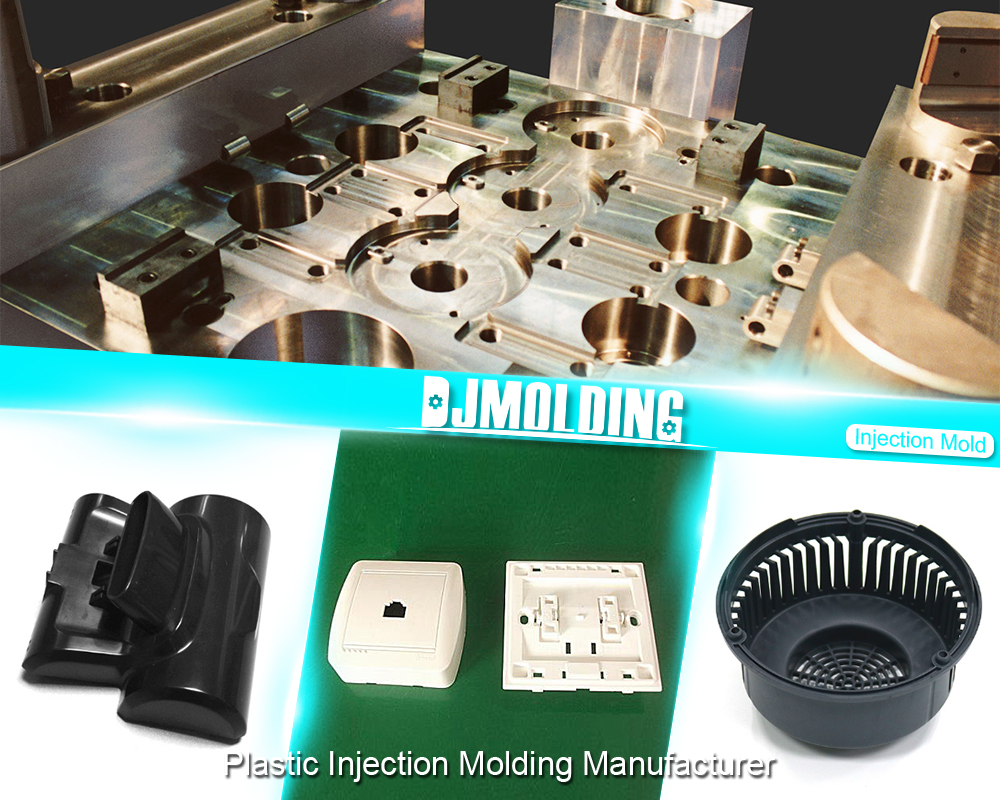
INTRODUCTION
Injection molding is an essential manufacturing process that has transformed various industries by enabling the mass production of high-quality and complex parts. Liquid Silicone Rubber(LSR) injection molding is a specialized type of injection molding that uses liquid silicone rubber as the raw material. This blog post aims to provide a comprehensive guide to LSR injection molding, discussing its benefits, injection molding process, applications, and prospects.
What is LSR Injection Molding?
Definition of LSR Injection Molding
LSR injection molding is a specialized process that uses liquid silicone rubber as the raw material. LSR has unique properties, including high-temperature resistance, biocompatibility, and good elasticity, making it ideal for various applications.
Types of LSR Injection Molding
There are two main types of LSR injection molding: Cold Runner and Hot Runner. The cold runner system suits low to medium production volumes, while manufacturers utilize the hot runner system for high-volume production.
Advantages of using LSR Injection Molding
The use of LSR injection molding offers several advantages, including:
- Reduced waste: LSR injection molding generates less waste than traditional injection molding.
- Better part quality: LSR injection molding produces parts with excellent surface finish, dimensional accuracy, and consistency.
- High productivity: LSR injection molding machines have high-speed capabilities and can quickly produce high volumes of parts.
- Enhanced product design: LSR injection molding allows for creation of intricate and complex part designs with high precision and accuracy.
Injection Molding Process
Step-by-step process of LSR Injection Molding
LSR injection molding is a process that involves injecting liquid silicone into a mold to create a specific shape or design. Here is a step-by-step process of LSR injection molding:
- Mold Preparation: The first step involves preparing the mold for injection. Thoroughly cleaning the mold is vital for guaranteeing the quality of the end product, as it helps remove any debris or contaminants that may impact it.
- Injection of LSR Material: A specialized injection molding machine injects the LSR material into the mold after preparing it. This machine uses a screw or plunger to move the LSR material through a heated barrel, which is mixed and injected into the mold.
- Curing: After injecting the LSR material into the mold, we let it cure for a specific period. The curing process involves heating the mold to a particular temperature, which causes the LSR material to solidify and take on the shape of the mold.
- Removal of Finished Product: Once we complete the curing process, we open the mold and remove the finished product.
Machines and Equipment Used in LSR Injection Molding
To produce high-quality LSR products, specialized machines, and equipment are used in the injection molding process. These include:
- Injection Molding Machine: This machine mixes and injects the LSR material into the mold.
- Heating and Cooling Systems: These systems heat the mold to the required temperature during the curing process and cool it down after forming the product.
- Mold Release Agent: This agent prevents the LSR material from sticking to the mold during curing.
Factors Affecting the Quality of LSR Injection Molding
Several factors can affect the quality of LSR injection molding, including:
- Material Selection: The quality of the LSR material used in the injection molding process is crucial in determining the final product’s quality.
- Mold Design: The design of the mold used in the injection molding process can affect the final product’s quality.
- Process Control: The temperature, pressure, and time used in the injection molding process can affect the final product’s quality.
Applications of LSR Injection Molding
Medical Industry
The medical industry uses LSR injection molding to create high-quality medical devices such as catheters, seals, and valves. We use LSR materials because they are biocompatible, easy to sterilize, and can withstand extreme temperatures and pressures.
Automotive Industry
The automotive industry uses LSR injection molding to create high-quality parts such as seals, gaskets, and wiring harnesses. We use LSR materials because they resist extreme temperatures and chemicals and can withstand wear and tear.
Consumer Electronics Industry
The consumer electronics industry uses LSR injection molding to create high-quality parts such as keypads, connectors, and gaskets. We use LSR materials because they possess durability, heat resistance, and the ability to withstand exposure to harsh chemicals.
Aerospace Industry
The aerospace industry uses LSR injection molding to create high-quality parts such as seals, gaskets, and tubing. LSR materials are used because they are lightweight, can withstand extreme temperatures and pressures, and have excellent chemical resistance.
Future of LSR Injection Molding
We expect a promising future for LSR injection molding as we develop new advancements and technologies to enhance the process and broaden its applications. Here are some of the key developments to look out for:
Advancements in LSR Injection Molding
- It increased automation and robotics for improved efficiency and quality.
- We offer high-quality materials that can improve the durability and performance of your products.
- It improved mold design for more complex shapes and geometries.
- We have improved the software to offer better control and monitoring of the process.
New Technologies in LSR Injection Molding
- Our company specializes in micro molding to produce small, high-precision parts.
- 3D printing is a valuable tool for creating intricate shapes and structures.
- Enhance functionality by integrating with other technologies, like sensors and electronics.
Opportunities and Challenges in LSR Injection Molding
- Opportunities: LSR injection molding has potential applications in various industries, such as medical, automotive, and consumer electronics.
- Challenges: LSR material is expensive, making it difficult for some applications. LSR injection molding also requires specialized equipment and expertise, which can limit its adoption.
Overall, the future of LSR injection molding looks bright, with new advancements and technologies expanding its applications and improving its efficiency and quality. However, there are also challenges to consider, such as the cost of the material and the specialized expertise required for the process.
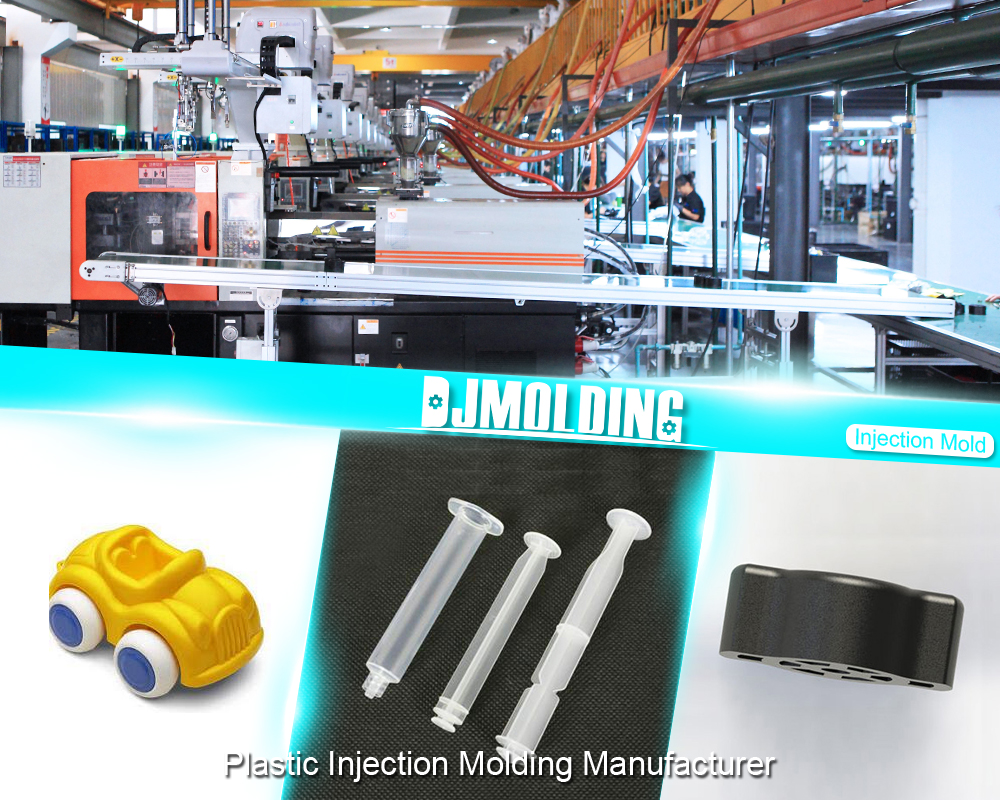
CONCLUSION
In conclusion, LSR injection molding is a highly versatile and efficient manufacturing process that offers many benefits. It is used in various industries, including medical, automotive, consumer electronics, and aerospace, and is known for its high-quality, precision, and durability. As advancements in LSR injection molding continue, the opportunities for its use will only grow, making it an essential technology for the manufacturing industry.
For more about liquid silicone rubber(lsr) injection molding suppliers,you can pay a visit to Djmolding at https://www.djmolding.com/liquid-silicone-rubberlsr-injection-molding/ for more info.