Injection Molding FAQ
What is Cushion & why do I need to hold it
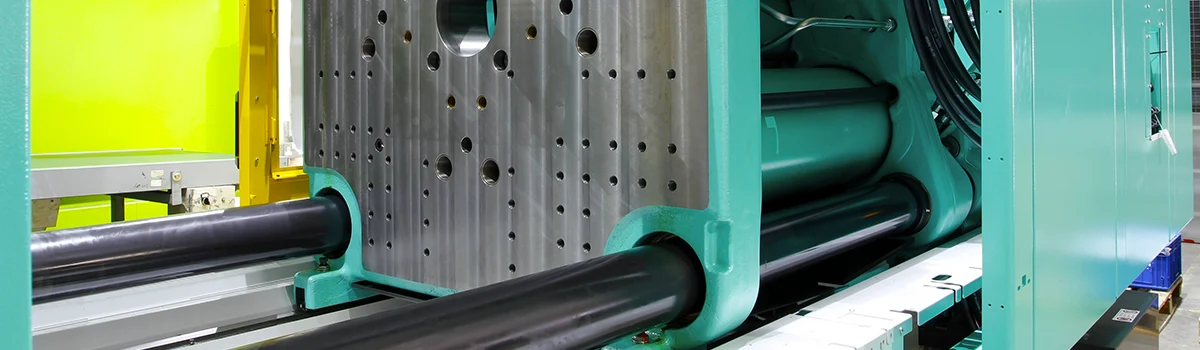
Injection Molding has a lot of strange sounding terms. Fill time, back pressure, shot size, cushion. For people new to plastics or injection molding, some of these terms might feel overwhelming or make you feel unprepared. One of the goals of our blog is to help newer processors have the tools they need to succeed. Today we will take a look at cushion. What is it, and why is it important to “hold it?”
To understand cushion, you need a working knowledge of molding machines, specifically injection units.
The injection unit of a molding press consists of an electrically heated barrel (a long cylindrical tube) that surrounds a reciprocating screw. Plastic pellets are fed into one end of the barrel and conveyed down its length by the screw as it turns. On the plastic’s journey down the length of the screw and barrel it is melted, compressed and forced through a non-return valve (check ring, ball check). As the molten plastic is forced across the non-return valve and conveyed in front of the screw tip the screw is forced back in the barrel. This mass of material in front of the screw is called the “shot”. This is the amount of material that will be injected out of the barrel if the screw is moved all the way forward.
The molding technician can adjust shot size by adjusting the stroke of the screw. The screw of a molding press is said to be on “bottom” if the screw is in the full forward position. If the screw is in the full back position it is said to be at full stroke or max shot size. This is usually measured on a linear scale in inches or centimeters but can also be measured volumetrically using inchesᶟ or centimetersᶟ.
The molding technician determines how much of the shot capacity is needed for the mold that is being ran. For example, if the amount of plastic needed to fill the mold cavity and produce an acceptable part is 2 pounds, then the technician would set the stroke of the screw to the position that would yield a slightly larger shot size. Say 3.5 inches of stroke or shot size. Good molding practices dictate that you use a slightly larger shot than needed so that you can maintain a cushion. Finally, we get to cushion.
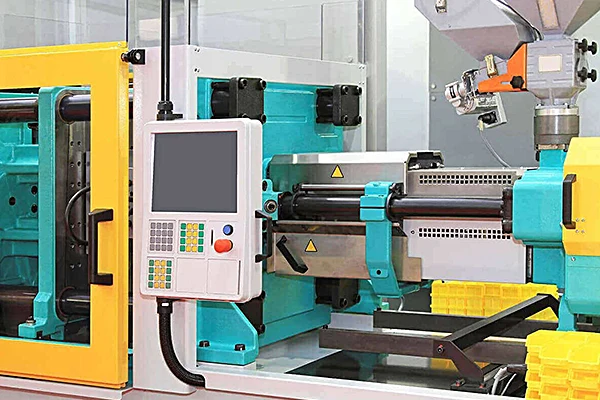
Scientific molding theory recommends that a mold be filled with molten plastic as fast as possible to 90-95% of the total part weight, slow the velocity down as the remainder of the part is filled, and transfer to fixed pressure “hold” phase just as the part is filled and starts to pack. This hold phase is a very important part of the process. This when the final packing of the part occurs and when much of the heat is transferred out of the molded part and into the mold steel. In order for the part to be packed out, there must be enough molten plastic remaining in front of the screw to be able to transfer the Hold Pressure through the runner system and through the molded part.
The intent is to hold pressure against the part until it has cooled sufficiently to keep part dimensions and appearance when ejected from the mold. This can only be achieved with a cushion of plastic in front of the screw. Ideally you want your cushion small to minimize the amount of material left in the barrel after each cycle of the machine. Any remaining material is subject to the constant heat in the barrel and could potentially degrade causing processing issues or loss of mechanical properties.
Monitoring cushion is an excellent way to see potential problems with your equipment. A cushion that continues to decrease as pressure is applied to a full part can indicate problems with the repeatability of your process. There could be excessive wear on the barrel or screw. There could be some form of contamination that prevents the non-return valve from seating properly. Any of these will cause unwanted variation to your molded parts. These variations could result in parts with shorts, sinks or other appearance issues. They could also be out of tolerance dimensionally due to under packing or insufficient cooling.
So, remember, pay attention to your cushion. It will tell you how healthy your process is.