Overmolding
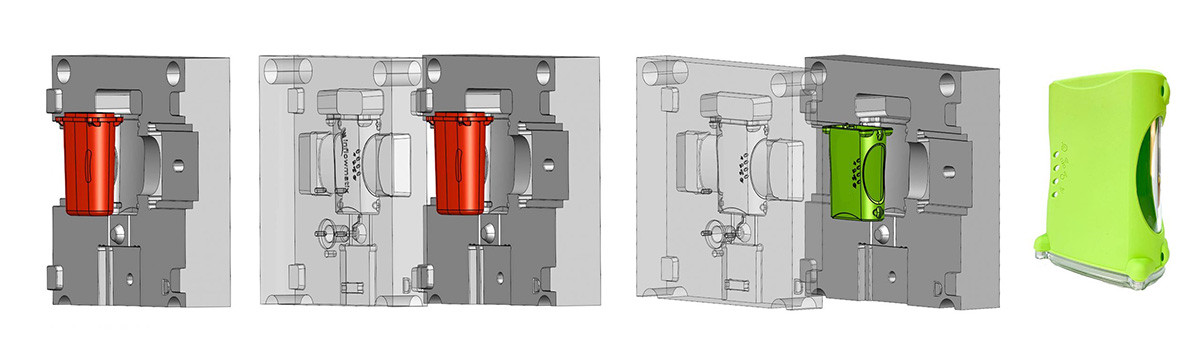
Overmolding is a manufacturing process in which a substrate or a base component is combined with one or more materials to create a final product with improved functionality, durability, and aesthetics. This process has gained popularity in recent years due to its ability to enhance the quality and performance of products while reducing costs and simplifying the assembly process. Overmolding finds applications in various industries, such as automotive, electronics, medical devices, and consumer products. To comprehensively understand this process, this article will delve into the multiple aspects of overmolding, including its techniques, materials, and applications.
Definition and Principles of Overmolding
Overmolding is molding one material over another, typically using thermoplastic elastomers (TPE) or thermoset rubber. This process creates a single component with two or more materials, each with unique properties that serve a specific purpose.
Principles of Overmolding
There are three primary principles of overmolding that manufacturers must consider:
- Material Compatibility:The materials used in overmolding must be compatible, and the materials must be able to bond to create a robust and cohesive component. The adhesion between the materials is critical to ensure that the element has the desired properties.
- Design for Overmolding:Before overmolding, one must carefully consider the component’s method. The design should facilitate molding the second material over the first one without interference. The design of the parting line, where the two materials meet, must carefully ensure no gaps or voids between the two materials.
- Manufacturing Process:Overmolding requires a specialized manufacturing process that involves molding one material over another. The method utilizes two or more molds, where the first mold develops the first material, and the second mold produces the second material over the first. Then, we join the two molds together to create a single component.
Benefits of Overmolding
Overmolding offers several benefits that make it a popular choice for many manufacturers, including:
- Enhanced Durability:Overmolding can improve the durability of a component by adding a protective layer that can resist wear and tear.
- Improved Aesthetics: Overmolding can improve the aesthetics of a component by adding color or texture to the surface.
- Enhanced Functionality:Overmolding can improve the functionality of a component by adding features such as grip, buttons, or switches.
Applications of Overmolding
Manufacturers commonly use overmolding to produce electronic products like mobile phones, remote controls, and computer peripherals. It also has medical devices, automotive components, and consumer products.
Injection Molding vs. Overmolding: What’s the Difference?
Injection molding and overmolding are commonly used manufacturing processes in plastic parts. While both methods involve molding plastic, they have distinct differences. This blog post will discuss the differences between injection molding and overmolding.
Injection Molding
Injection molding is a manufacturing process that involves melting plastic pellets and injecting the molten plastic into a mold cavity. The plastic is then cooled and ejected from the mold, resulting in a solid plastic part. Manufacturers use injection molding as an exact and efficient process to produce high volumes of plastic parts. Some key features of injection molding include:
Produces a single material part
- One injects the material into the mold cavity in a single step.
- The process finds application in producing high volumes of parts.
- The cost per part decreases as the volume of production increases.
Overmolding
Overmolding is a manufacturing process that involves molding one material over another material. The process typically adds a soft, rubber-like material over a rigid plastic part to enhance its durability and aesthetics. Some key features of overmolding include:
Produces a two-material component
- First, we mold the first material, and then the second material over the first.
- The process enhances the durability and aesthetics of the element.
- The cost per part is higher than injection molding due to the added technique of molding the second over the first.
- Differences between Injection Molding and Overmolding
The primary differences between injection molding and overmolding are:
- Number of Materials:Injection molding produces a single material part, while overmolding produces a two-material component.
- Process:Injection molding injects the molten plastic into a mold cavity in one step, while overmolding involves molding the first material first and then molding the second material over the first material.
- Purpose: Manufacturers use injection molding to produce high volumes of plastic parts, while they employ overmolding to enhance the durability and aesthetics of a plastic piece.
- Cost: Injection molding is typically less expensive per part than overmolding, due to the added process of molding the second material over the first.
Applications of Injection Molding and Overmolding
Manufacturers commonly use injection molding to produce consumer goods, automotive components, and medical devices. They also typically employ overmolding to enhance durability and aesthetics in electronic products like mobile phones and remote controls.
Two-Shot Overmolding: A Popular Technique
Two-shot overmolding, also known as two-shot molding or multi-shot molding, is a popular technique used in producing plastic parts. This process involves molding two materials onto each other to create a finished product. This blog post will discuss the basics of two-shot overmolding and its benefits.
Benefits of Two-Shot Overmolding
Two-shot overmolding offers several benefits over traditional overmolding techniques, including:
- Enhanced Aesthetics: Two-shot overmolding allows for the creation complex parts with multiple colors or textures. Using various materials can lead to a final product that is more visually attractive than one made from a single material.
- Improved Functionality: Two-shot overmolding can also enhance the functionality of a product. For example, a soft-touch grip over a rigid plastic base can improve a product’s ergonomics and user experience.
- Reduced Costs:Two-shot overmolding can help reduce costs by eliminating the need for secondary operations such as painting or coating. Implementing this can lead to a quicker manufacturing procedure and decrease expenses.
- Increased Durability: Two-shot overmolding can also improve the durability of a product. By using a rigid plastic base with a soft-touch grip, for example, the product is less likely to crack or break when dropped.
Applications of Two-Shot Overmolding
A variety of industries commonly use two-shot overmolding, including:
- Automotive: Two-shot overmolding produces automotive parts, such as dashboard components and interior trim pieces.
- Consumer Goods:Two-shot overmolding produces toothbrushes, razors, and electronic devices.
- Medical Devices:Two-shot overmolding produces medical devices such as surgical instruments and drug delivery devices.
Insert Molding: Combining Two Different Components
Insert molding is a manufacturing process that involves molding a plastic component around a pre-existing insert or substrate. The insert is typically made of metal or plastic and can be a threaded insert, a wire, or a printed circuit board. This blog post will discuss the basics of insert molding and its benefits.
How Does Insert Molding Work?
Insert molding is a two-step process that involves the following:
- We place the insert into a mold.
- Plastic is injected around the insert, creating a molded plastic component that is firmly attached to the insert.
- The insert adds strength and stability to the finished part, making it suitable for various applications.
Benefits of Insert Molding
Insert molding offers several benefits over traditional molding techniques, including:
- Improved Strength: Insert molding creates a more robust and stable finished product, as the insert is firmly attached to the plastic component. Improving the durability and lifespan of the product is possible with this.
- Reduced Assembly Time: Insert molding helps minimize assembly time and labor costs by combining multiple components into a single molded part.
- Increased Design Flexibility:Insert molding enables the creation of complex parts with multiple materials, textures, and colors, resulting in a better-looking final result.
- Enhanced Functionality: By using insert molding, manufacturers can improve the functionality of a product by incorporating features like threaded inserts or electrical contacts.
Applications of Insert Molding
Insert molding is commonly used in a variety of industries, including:
- Automotive: Insert molding produces automotive parts such as connectors, sensors, and switches.
- Electronics: Insert molding produces electronic components such as connectors, housings, and switches.
- Medical Devices:Insert molding produces catheters, connectors, and sensors.
Soft Overmolding: Improving Grip and Comfort
Soft overmolding is a process used in manufacturing to add a soft, flexible material onto a rigid base material. The technique allows for adding a layer of comfort and grip to a product, thereby improving its functionality and aesthetics. This blog post will discuss the basics of soft overmolding and its benefits.
How Does Soft Overmolding Work?
Soft overmolding is a two-step process that involves the following:
- We mold the rigid base material.
- A soft, flexible material is injected around the molded base material, creating a comfortable and tactile surface.
- Typically, manufacturers make the soft material from thermoplastic elastomers (TPE) or silicone. The resulting product has a smooth, comfortable surface that provides a better grip and improves handling.
Benefits of Soft Overmolding
Soft overmolding offers several benefits over traditional molding techniques, including:
- Improved Comfort: Soft overmolding provides a comfortable surface that enhances the user’s experience. The soft material conforms to the shape of the user’s hand, reducing pressure points and improving grip.
- Enhanced Grip: The soft material used in soft overmolding provides a better grip, reducing the likelihood of dropping or losing the product. Improving safety measures can reduce the risk of product damage.
- Aesthetically Pleasing: Soft overmolding can improve the appearance of a product, making it more aesthetically pleasing. The soft material can be customized to match the color and texture of the product, creating a cohesive look.
- Durable: Soft overmolding creates a durable product that can withstand regular use and wear. The soft material provides added protection against impacts and scratches, reducing the likelihood of damage to the product.
Applications of Soft Overmolding
A variety of industries commonly use soft overmolding, including:
- Consumer Electronics: Soft overmolding produces electronic devices such as remote controls, headphones, and gaming controllers.
- Sporting Goods: Manufacturers use soft overmolding to produce sporting goods such as grips for golf clubs, tennis rackets, and bicycle handles.
- Medical Devices: Soft overmolding produces medical devices such as surgical instruments and hearing aids.
Hard Overmolding: Adding Protection and Durability
Hard overmolding adds a rigid plastic layer over existing material, such as rubber or silicone, to create a more durable and protective surface. The result is a product that can withstand harsh environments, resist abrasion, and endure repetitive use.
Here are some of the benefits of using hard overmolding in product design:
- Increased durability: Hard overmolding provides an added layer of protection that can increase the lifespan of a product. Protecting the underlying material from wear and tear makes effects less likely to break or fail.
- Improved grip:By adding a tricky plastic layer to a soft material, such as rubber or silicone, manufacturers can create a better grip for users. It is crucial to consider this factor, particularly for products utilized in wet or slippery surroundings.
- Resistance to environmental factors:Hard overmolding can protect products from exposure to sunlight, chemicals, and other environmental factors that can cause damage over time. This enhancement improves the product’s ability to adapt and withstand various environments.
- Aesthetic appeal: Hard overmolding can also improve the appearance of a product. By adding a tricky plastic layer, manufacturers can create a sleek, polished look that is impossible with a single material.
- Customization: By employing hard overmolding, companies can customize their products by adding logos, colors, and other design elements to the surface. This branding strategy helps increase visibility in the marketplace.
Manufacturers use hard overmolding in various products, ranging from industrial equipment to consumer electronics. Here are a few examples:
- Handheld devices: Many handheld devices, such as cell phones and tablets, use hard overmolding to create a protective layer around the device. This feature helps to safeguard the device from damage caused by drops and impacts.
- Power tools:Power tools frequently encounter harsh environments, such as dust and debris. Employing hard overmolding can protect these tools from damage and extend their lifespan.
- Medical devices: Medical devices require high durability and resistance to environmental factors. Hard overmolding can protect these devices and ensure they function correctly.
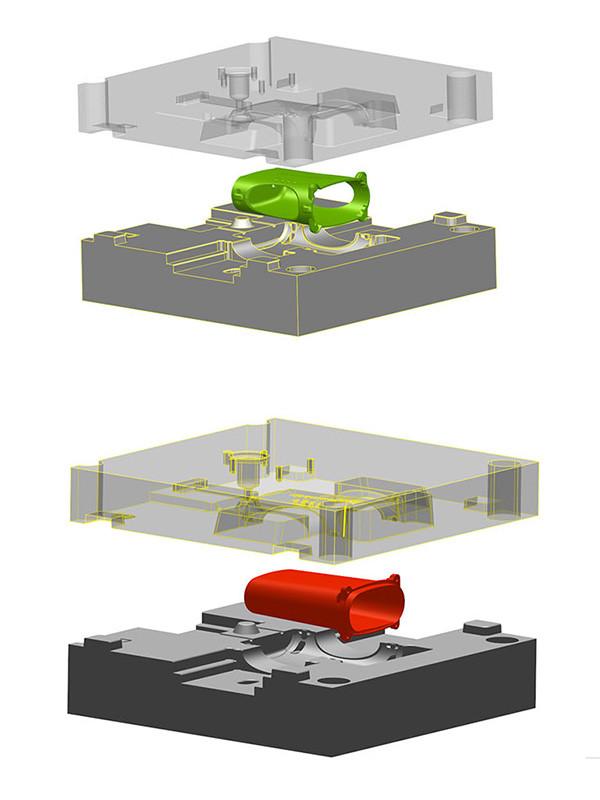
Thermoplastic Elastomers (TPEs): The Preferred Material for Overmolding
When it comes to overmolding, there are many materials to choose from, but none are more popular than Thermoplastic Elastomers (TPEs). TPEs are versatile materials that offer many benefits when it comes to overmolding. Here are some of the reasons why TPEs are the preferred material for overmolding:
- Versatility:Manufacturers can use TPEs to overmold various materials, including metals, plastics, and rubbers. Manufacturers can use them in various products made from different materials, making them a flexible option.
- Softness and flexibility: TPEs have a soft and flexible texture, making them ideal for overmolding products requiring a comfortable grip. They can also create products that need to bend or flex without breaking.
- Resistance to chemicals and UV radiation:TPEs are highly resistant to chemicals and UV radiation, making them ideal for products exposed to harsh environments.
- Durability: TPEs are highly durable and resistant to wear and tear, making them ideal for products used frequently or subjected to heavy use.
- Cost-effective: TPEs are cost-effective compared to other materials used for overmolding, making them an affordable option for manufacturers.
- Easy to process:TPEs can be quickly processed using injection molding, making them a popular choice for manufacturers who need to create large quantities of products promptly and efficiently.
Some examples of products that use TPEs for overmolding include:
- Grips for hand tools: Manufacturers often use TPEs to overmold grips for hand tools, such as pliers and screwdrivers. TPEs’ soft and flexible texture makes them ideal for creating a comfortable grip that won’t slip.
- Sports equipment: Manufacturers commonly use TPEs to overmold sports equipment, such as golf club grips and tennis racket handles. TPEs’ soft and flexible texture makes them ideal for creating a comfortable grip that won’t slip.
- Electronic devices: TPEs often overmold electronic gadgets like remote controls and cell phones. TPEs’ soft and flexible texture makes them ideal for creating a protective layer around the device that won’t scratch or damage the surface.
Silicone Overmolding: Ideal for Medical Devices and Consumer Products
Silicone overmolding is a process that involves the injection of a liquid silicone material over a substrate material. This process can create various products for various industries but is particularly useful for medical devices and consumer products. This blog post will explore the advantages of silicone overmolding for these industries.
Advantages of Silicone Overmolding for Medical Devices
- Biocompatibility:Medical devices that come into contact with human tissue require safe materials for the body. Silicone is a biocompatible material that is not toxic or harmful to living tissue. Using this material in medical devices is highly advantageous.
- Sterilization: Medical devices must be sterilized before use to ensure they are free from bacteria and other harmful contaminants. Healthcare professionals can use various methods to fix silicone, including steam, radiation, and chemical sterilization. Medical devices can benefit from the versatility of this material.
- Flexibility: Silicone’s high flexibility allows molding it into various shapes and sizes. The material’s ability to conform to the body’s shape makes it perfect for medical devices.
- Durability: Silicone is a highly durable material that can withstand repeated use and exposure to harsh chemicals. Its durability and ability to withstand repeated use and cleaning make it a suitable material for medical devices.
Advantages of Silicone Overmolding for Consumer Products
- Comfort: Silicone is a soft and flexible material that is comfortable to wear against the skin. Consumer products in contact with the body, like earbuds, watches, and fitness trackers, are perfect for materials like this.
- Water Resistance: Silicone is a water-resistant material that can withstand exposure to moisture without deteriorating or losing shape. Consumer products used in wet environments, such as swimming goggles and waterproof speakers, are ideally made from this material.
- Design Flexibility: Silicone can be molded into various shapes and sizes, allowing designers to create unique and innovative products. This property makes silicone ideal for consumer products requiring complex shapes and designs.
- Durability:Silicone is a highly durable material that can withstand exposure to UV radiation, extreme temperatures, and harsh chemicals. This feature makes it ideal for consumer products that require durability and can withstand various weather conditions.
Polyurethane Overmolding: Versatile and Durable
Polyurethane overmolding is a manufacturing process that has recently gained popularity due to its versatility and durability. This process involves applying a layer of polyurethane material over an existing substrate, creating a seamless, protective coating that enhances the original part’s strength, durability, and functionality.
Overmolding with polyurethane offers many benefits, making it an attractive option for manufacturers across various industries. Here are some of the key advantages:
Versatility
Manufacturers can use the highly versatile process of polyurethane overmolding with many substrates, including plastics, metals, and composites.
This versatility makes polyurethane overmolding an ideal solution for applications that require combining different materials into a single part.
Durability
Polyurethane is a highly durable material that can withstand various environmental conditions, including extreme temperatures, harsh chemicals, and heavy wear and tear. Applications that require stable performance and protection can benefit from choosing this as their ideal option.
Customization
Manufacturers can achieve a high degree of customization with polyurethane overmolding, allowing them to create complex shapes and designs. This feature makes it a perfect choice for items needing a unique appearance or practical layout.
Cost-Effective
Polyurethane overmolding can be a cost-effective solution compared to other manufacturing methods, such as injection molding or machining. It can also reduce the number of parts required for a given application, reducing assembly time and costs.
Improved Grip and Comfort
Polyurethane overmolding can enhance the grip and comfort of products, such as tools and handles, by providing a non-slip surface that is easy to grip and comfortable to hold.
Polyurethane overmolding can be used in a wide range of applications, including:
- Automotive:for interior and exterior parts, such as door handles, dashboard components, and trim pieces.
- Electronics:for protecting sensitive electronic components from environmental damage.
- Medical: for creating durable and hygienic medical equipment, such as handles for surgical instruments.
- Consumer Goods: for creating custom products with unique designs and enhanced functionality, such as sporting goods and home appliances.
Overmolding for Automotive Applications: Enhancing Aesthetics and Functionality
In the automotive industry, overmolding has become increasingly popular for improving the aesthetics and functionality of vehicle components. This manufacturing process creates various automotive parts, such as handles, grips, and knobs. Here, we will discuss how overmolding is used in automotive applications to enhance aesthetics and functionality.
Improving Aesthetics
One of the primary benefits of overmolding in the automotive industry is its ability to improve aesthetics. Overmolding allows designers to create complex shapes and designs that would be difficult to achieve with traditional manufacturing processes. Here are some ways overmolding enhances the aesthetic appeal of automotive components:
- Customization: Overmolding allows for customization, making it easy to create parts with unique designs and color combinations that match the vehicle’s interior or exterior.
- Texture: Overmolding can create a variety of surfaces, from soft-touch to high-grip, improving the part’s overall feel.
- Branding:Manufacturers can use overmolding to incorporate branding elements, such as logos or brand names, into the design.
- Quality: Overmolding produces high-quality parts with a consistent finish, improving the overall look and feel.
Enhancing Functionality
In addition to improving aesthetics, overmolding can enhance automotive components’ functionality. Here are some ways in which manufacturers use overmolding to enhance functionality:
- Grip: Overmolding can create a non-slip surface that improves grip, making parts easier to use and safer for drivers and passengers.
- Durability: Overmolding can increase the durability of parts by protecting them from wear and tear and exposure to harsh environmental conditions.
- Noise reduction: Overmolding can reduce noise by creating a dampening effect that reduces vibrations and absorbs sound.
- Protection:Overmolding can protect parts from damage caused by impacts or abrasion, which helps extend their lifespan.
Applications of Overmolding in the Automotive Industry
Manufacturers use overmolding in a variety of automotive applications, including:
- Interior components:Overmolding creates knobs, switches, and handles for internal features such as dashboards, door panels, and armrests.
- Exterior components: Overmolding creates external features such as grill inserts, headlight surrounds, and mirror covers.
- Under the hood: Overmolding creates parts such as engine mounts, sensors, and brackets that must withstand high temperatures and harsh conditions.
Overmolding for Electronics: Improving Performance and Reliability
In the electronics industry, overmolding has become increasingly popular for its ability to improve the performance and reliability of electronic components. Here, we will discuss how overmolding is used in electronics to enhance performance and reliability.
Improving Performance
One of the primary benefits of overmolding in the electronics industry is its ability to improve performance. Overmolding can enhance the performance of electronic components in several ways:
- Waterproofing:Overmolding enables the waterproofing of electronic components, making it essential for applications where the part may come into contact with moisture or other liquids.
- Vibration Resistance: Overmolding can create a barrier that helps electronic components resist vibration, which is critical in applications where the part may be subject to shock or vibration.
- Thermal Management: Overmolding helps dissipate heat away from electronic components, thereby enhancing their performance and prolonging their lifespan.
- Electrical Insulation:Overmolding can create an insulating layer that protects electronic components from electrical interference, which can help improve their performance.
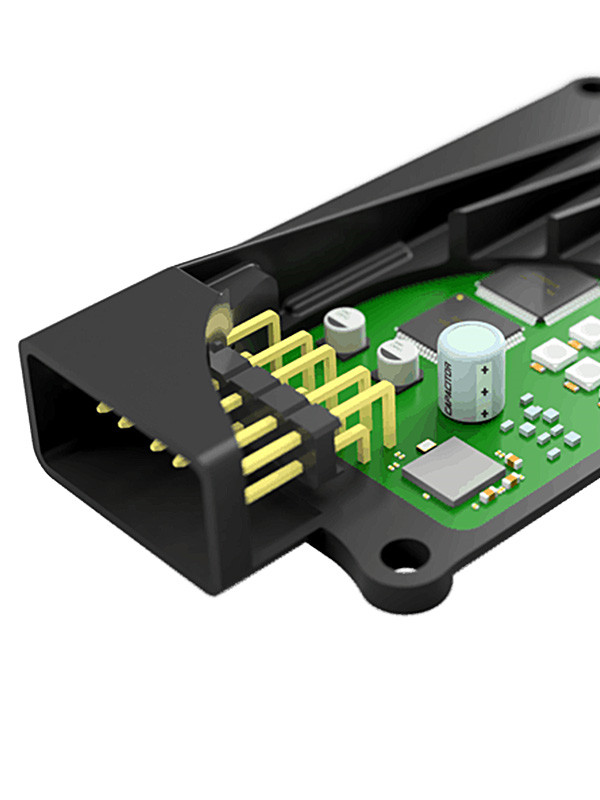
Improving Reliability
In addition to improving performance, overmolding can also enhance the reliability of electronic components. Here are some ways in which overmolding improves reliability:
- Protection from Damage: Overmolding can protect electronic components from physical damage, such as impact or abrasion, which can help extend their lifespan.
- Chemical Resistance:Overmolding can protect electronic components from chemicals that can cause corrosion or other damage, which can help improve their reliability.
- Reduced Risk of Failure: Overmolding can help reduce the risk of failure by protecting electronic components from environmental factors such as moisture, vibration, and temperature extremes.
Applications of Overmolding in the Electronics Industry
A variety of electronic applications utilize overmolding, including:
- Connectors:Overmolding creates waterproof and vibration-resistant connectors that find applications in various electronic devices.
- Circuit Boards:Overmolding can protect circuit boards from moisture, vibration, and other environmental factors that can cause damage or failure.
- Sensors: Overmolding can protect sensors from damage caused by exposure to harsh chemicals or other environmental factors.
- Handheld Devices:Overmolding creates durable and waterproof cases for handheld devices, such as mobile phones, cameras, and GPS devices.
Overmolding for Medical Devices: Ensuring Safety and Comfort
Overmolding has become increasingly popular in the medical industry for improving the safety and comfort of medical devices. Here, we will discuss how overmolding is used in medical devices to ensure safety and comfort.
Ensuring Safety
One of the primary benefits of overmolding in the medical industry is its ability to ensure safety. Overmolding can enhance the security of medical devices in several ways:
- Biocompatibility: Overmolding enables the creation of biocompatible medical devices, ensuring their safety for use in the human body without causing adverse reactions.
- Sterilization: Overmolding can create easy medical devices to sterilize, which is essential for preventing the spread of infections in healthcare settings.
- Ergonomics: Overmolding enables the creation of ergonomically designed medical devices, which can help reduce the risk of repetitive stress injuries and other musculoskeletal disorders among healthcare workers.
- Durability: Overmolding can create medical devices that are more durable, which can help reduce the risk of failure or malfunction during use.
Ensuring Comfort
In addition to ensuring safety, overmolding can also enhance the comfort of medical devices. Here are some ways in which overmolding provides comfort:
- Texture: Overmolding can create medical devices with a textured surface that provides a better grip and improves comfort.
- Flexibility: Overmolding can create medical devices that are more flexible, which can help improve comfort and reduce the risk of injury or discomfort during use.
- Customization: Overmolding allows customization of the shape and design of medical devices to suit the unique needs of individual patients better, enhancing comfort and minimizing the risk of complications.
Applications of Overmolding in the Medical Industry
A variety of medical applications utilize overmolding, including:
- Surgical Instruments: Overmolding can create surgical instruments with a more comfortable grip, better ergonomics, and improved durability.
- Implants:Overmolding can create biocompatible implants that are more comfortable for patients and less likely to cause complications.
- Diagnostic Devices: Overmolding can create diagnostic devices that are easier to handle, more durable, and more comfortable for patients.
- Wearables: Overmolding enables the creation of wearable medical devices that offer enhanced comfort and flexibility, making them easier for patients to wear and use.
Overmolding for Consumer Products: Adding Value and Appeal
Here, we will discuss how overmolding is used in consumer products to add value and appeal.
Improving Aesthetics
One of the primary benefits of overmolding in the consumer product industry is its ability to improve aesthetics. Overmolding can enhance the look and feel of consumer products in several ways:
- Design Flexibility:Overmolding allows for greater design flexibility, making creating products with unique shapes and textures easier.
- Color Customization: Overmolding enables multiple colors in a single product, creating eye-catching designs that stand out on the shelf.
- Soft-Touch Feel:Overmolding can create products with a soft-touch feel, improving the overall user experience and appeal.
Adding Functionality
In addition to improving aesthetics, overmolding can also add functionality to consumer products. Here are some ways in which overmolding adds value:
- Improved Grip: Overmolding allows the creation of products with a better grip, enhancing the ease of use and comfort when holding them.
- Enhanced Durability:Overmolding can create more durable products, improving their lifespan and overall value.
- Waterproofing: Overmolding enables the creation of waterproof products, increasing their versatility and appeal to consumers.
Applications of Overmolding in the Consumer Product Industry
A variety of consumer product applications utilize overmolding, including:
Electronics: Overmolding can create stylish and durable cases for electronic devices like phones and tablets.
Sports Equipment: Overmolding can create equipment with improved grip and durability, such as bike handles and tennis racket grips.
Kitchenware: Overmolding can create kitchenware with a soft-touch feel and improved grip, such as cooking utensils and handles for pots and pans.
Personal Care Products: Overmolding can create personal care products with a unique look and feel, such as toothbrushes and razors.
Overmolding Design Considerations: From Prototyping to Production
Overmolding involves injecting a second material over a pre-formed component, creating a unified product. Overmolding can provide significant benefits, such as improved aesthetics, added functionality, and enhanced durability. However, designing and manufacturing overmolded parts requires careful consideration to ensure success.
Here are some essential design considerations for overmolded parts:
Material compatibility: The materials used in overmolding must be compatible to ensure a strong bond. The adhesion between the two materials is critical to the performance of the part. Materials with similar properties and melt temperatures are ideal for overmolding.
Part design: The design of the pre-formed component should consider the size, shape, and location of the overmolded area. A well-designed part will have a uniform wall thickness and no undercuts to ensure a smooth transition between the materials.
Tooling design: The tooling for overmolding is more complex than traditional injection molding. The tool design should hold the pre-formed component in place during the overmolding process, allowing the second material to flow around and over the part.
The designer must also design the tooling to minimize flashing and ensure a consistent bond between the materials.
Process optimization: The overmolding process involves multiple stages, including molding the pre-formed component, cooling, and then injecting the second material. The engineer must optimize the process to ensure the best possible bond between the two materials and minimize defects such as warping or sink marks.
When moving from prototyping to production, there are additional considerations to keep in mind:
Volume and cost: Overmolding can be more expensive than traditional injection molding due to the complexity of the process and the cost of tooling. As volume increases, the cost per part can decrease, making overmolding more cost-effective for larger production runs.
Quality control: Overmolding requires strict measures to ensure consistent part quality and prevent defects. The quality control team should perform inspection and testing at every stage of the manufacturing process to ensure the part meets specifications.
Supplier selection: Choosing the right supplier for overmolding is critical to the project’s success. Look for a supplier with experience in overmolding and a track record of producing high-quality parts. The supplier should also be able to provide design assistance, process optimization, and quality control measures.
Cost-Effective Manufacturing with Overmolding
Overmolding is a manufacturing process that involves injecting a second material over a pre-formed component to create a single unified product. This process can provide significant benefits, such as improved aesthetics, added functionality, and enhanced durability. Overmolding can also be a cost-effective solution for specific products.
Here are some ways that overmolding can help reduce manufacturing costs:
Reduced assembly time: Overmolding can eliminate the need for separate components and the time-consuming process of assembling them. Overmolding can reduce assembly time and labor costs by creating a unified product.
Reduced material waste: Traditional injection molding often generates significant material waste due to the sprues and runners necessary to fill the mold. Overmolding can minimize waste by using the pre-formed component as the core and injecting the second material only where needed.
Improved part performance: Overmolding can improve part performance and durability, reducing the need for frequent replacements or repairs. Reducing downtime and maintenance costs can result in significant long-term savings.
Reduced tooling costs: Overmolding can be more expensive than traditional injection molding due to the complexity of the process and the cost of tooling. However, in some cases, overmolding can reduce tooling costs by eliminating the need for separate molds for each component. Overmolding can simplify the manufacturing process, especially for small and complex parts.
Reduced transportation costs: Overmolding lowers transportation costs by eliminating the need to transport and assemble separate components later. By implementing this, there will be a reduction in the risk of damage during transportation, leading to a decrease in rejected parts and waste.
When considering overmolding for cost-effective manufacturing, it’s essential to keep the following factors in mind:
Material selection: The materials used in overmolding must be compatible to ensure a strong bond. Materials with similar properties and melt temperatures are ideal for overmolding. Choosing suitable materials can also impact long-term cost savings by improving part performance and reducing maintenance costs.
Process optimization: The overmolding process involves multiple stages, including molding the pre-formed component, cooling, and then injecting the second material. The process optimization team must optimize the process to ensure the best possible bond between the two materials and minimize defects such as warping or sink marks. Optimizing the process can also result in faster cycle times and increased efficiency, reducing manufacturing costs.
Supplier selection: Choosing the right supplier for overmolding is critical to the project’s success. Look for a supplier with experience in overmolding and a track record of producing high-quality parts. The supplier should also be able to provide design assistance, process optimization, and quality control measures.
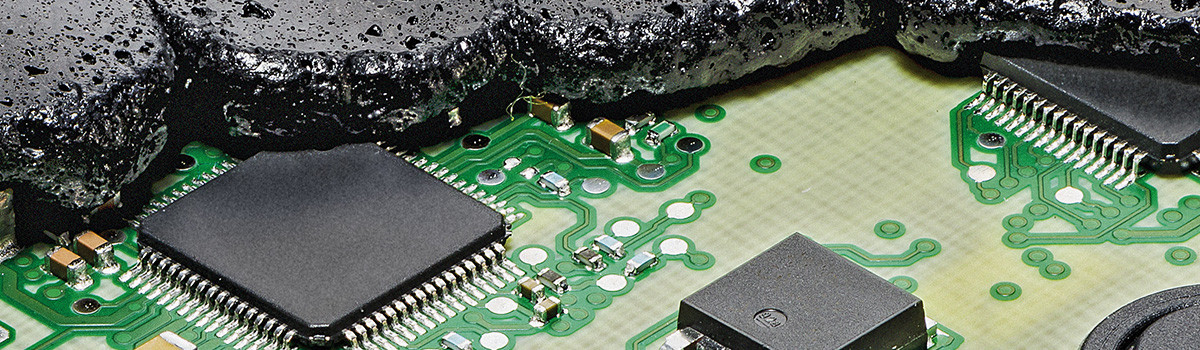
Environmental Sustainability and Overmolding
Overmolding is a popular manufacturing process that involves molding one material over another to create a single product. This process offers a range of benefits, including improved aesthetics, added functionality, and increased durability. But what about its impact on the environment? Is overmolding an environmentally sustainable manufacturing process?
Here are some ways that overmolding can be an environmentally sustainable manufacturing process:
Reduced material waste: Overmolding can minimize waste by using the pre-formed component as the core and injecting the second material only where needed. Using less material in production reduces the amount of waste generated overall.
Reduced energy consumption: Overmolding can be more energy-efficient than traditional manufacturing processes because molding a single product requires less energy than manufacturing separate components and assembling them later.
Use of recycled materials: Many overmolding materials can be recycled, reducing waste in landfills. Using recycled materials can also reduce the need for virgin materials, conserving natural resources and reducing energy consumption.
Longer product lifespan: Overmolding can improve part performance and durability, resulting in products that last longer and require fewer replacements. Reducing waste generated over the product’s lifetime can significantly lessen its environmental impact.
Reduced transportation: By eliminating the need for separate transit and later assembly of components, overmolding can reduce transportation costs. Reducing the amount of fuel used in the vehicle can decrease the environmental impact and lower associated emissions.
However, it’s important to note that overmolding is not always an environmentally sustainable manufacturing process. Here are some considerations to keep in mind:
Material selection: The materials used in overmolding must be carefully selected to ensure they are environmentally friendly. For example, some materials may be challenging to recycle or may require significant energy consumption to produce.
Process optimization: Overmolding must be optimized to reduce energy consumption and waste. One way to minimize material waste is by upgrading machinery or refining the molding process for greater efficiency.
End-of-life considerations: When considering the end of a product’s life, individuals or organizations must contemplate how they will dispose of it. Overmolded products may be more challenging to recycle or may require more energy to dispose of than traditional products.
Overmolding and Industry 4.0: Innovations and Opportunities
Overmolding is a manufacturing process that involves molding a material onto another material or substrate. The automotive, medical, and electronics industries widely use it. With the advent of Industry 4.0, overmolding has become even more innovative and efficient. Here, we will explore the innovations and opportunities of overmolding in the Industry 4.0 era.
Innovations in Overmolding
Integrating Industry 4.0 technologies such as automation, artificial intelligence, and the Internet of Things (IoT), has revolutionized the overmolding process. Here are some of the innovations that have emerged:
- Smart Molds: These molds are equipped with sensors and can communicate with the machines to adjust the molding process. They can also detect defects and notify operators to take corrective action.
- Robotics:Using robots in overmolding has increased efficiency and reduced labor costs. Robots can handle repetitive tasks such as loading and unloading materials, reducing human error risk.
- 3D Printing:3D printing has created complex molds that were previously impossible to produce. The increased design flexibility has led to reduced lead times.
- Predictive Maintenance:Predictive maintenance is a technique that uses data analysis to predict when machines will require maintenance. This technique can help prevent downtime and reduce maintenance costs.
Opportunities in Overmolding
Overmolding has numerous opportunities in Industry 4.0, including:
- Lightweighting:Overmolding can create lightweight parts by molding a thin layer of material onto a light substrate. Reducing the weight of the final product improves fuel efficiency and reduces emissions.
- Customization: Overmolding allows for the customization of parts by using different materials and colors. In the medical and consumer electronics industries, looks matter a lot, and it’s crucial to consider this factor.
- Sustainability:Overmolding can help reduce waste by using recycled materials as substrates. By reducing the environmental impact of manufacturing, companies can not only improve their brand image and contribute towards a sustainable future.
- Cost Savings: Automation, robotics, and predictive maintenance can reduce labor costs and increase efficiency, leading to manufacturer cost savings.
Overmolding Challenges and Solutions
However, overmolding poses some challenges that manufacturers must overcome to produce high-quality overmolded parts. In this article, we explore some of the overmolding difficulties and solutions.
Challenges
- Adhesion: Overmolding requires that the two materials used adhere to each other, and poor adhesion leads to delamination, cracking, or detachment of the overmolded material.
- Warping:During the overmolding process, the substrate can deform due to the high heat and pressure applied. Warping adversely affects the overall quality of the part.
- Material compatibility:The materials used in overmolding must be compatible to ensure good adhesion and prevent warping. Mismatched materials can lead to poor bonding and material failure.
- Parting line: The parting line is where the two materials meet. Poor parting line design can lead to weak points in the finished product and reduced durability.
- Material flow: The overmolding process requires the second material to flow around the substrate, filling every crevice. Poor material flow can lead to incomplete coverage, voids, or weak points.
Solutions
- Surface preparation: Preparing the substrate surface is crucial to achieving good adhesion. The surface must be clean, dry, and free of contaminants such as oils and debris. Pre-treating the substrate with adhesion promoters can also improve bonding.
- Proper tooling design: The design must consider the materials used and the part geometry to prevent warping and ensure good material flow. Using specialized tooling, such as insert molding, can also improve the part’s durability and strength.
- Material selection: The materials used in overmolding must be compatible with achieving good bonding and preventing warping. Using materials with similar thermal expansion coefficients can reduce the part’s stress during molding.
- Parting line design: When designing a product, it’s crucial to consider the parting line to ensure its strength carefully. Using rounded parting lines is highly recommended to prevent stress concentration.
- Injection molding process optimization: Optimizing the process can improve material flow and prevent voids or weak points. Controlling temperature, pressure, and injection speed is crucial for achieving good results.
Future Directions of Overmolding: Emerging Trends and Technologies
Overmolding, a process that involves molding one material onto another, has been a popular method in the manufacturing industry for decades. However, with advancements in technology and a greater focus on sustainability, overmolding is now experiencing a surge in popularity. Here, we will discuss the future directions of overmolding, including emerging trends and technologies.
Trends in Overmolding:
Sustainability: Sustainability is a top priority for many companies, and overmolding can help to reduce waste and improve efficiency in manufacturing processes. Using recycled materials and biodegradable polymers in overmolding is becoming more prevalent, reducing environmental impact.
Miniaturization: As technology evolves, the demand for smaller, lighter, and more intricate products is increasing. Overmolding allows for creation of smaller, more complex parts that are durable and efficient, making it an ideal choice for the miniaturization trend.
Customization: Consumers are demanding more personalized products, and overmolding provides the ability to customize products with different colors, textures, and materials. As customization becomes more accessible and affordable, we expect this trend to grow.
Technologies in Overmolding:
In-Mold Decoration (IMD): In-Mold Decoration is a technology that creates a decorated surface during overmolding. This technology enables the creation of products with intricate designs and patterns, making it ideal for the customization trend.
Insert Molding: Insert molding involves overmolding a pre-existing part or component. This technology is perfect for miniaturization since it produces smaller, more complex features.
Multi-Shot Overmolding: Multi-shot overmolding involves using multiple materials to create a single part or product. This technology allows for the creation products with different textures, colors, and materials, making it ideal for the customization trend.
Co-Injection Molding: Co-injection molding involves injecting two or more materials into a single mold. This technology allows for creation of products with a combination of properties, such as strength and flexibility.
Benefits of Overmolding:
Reduced Waste: Overmolding eliminates the need for separate parts and components, leading to a more efficient and sustainable manufacturing process.
Improved Durability: Overmolding provides increased durability and strength to products, making them more resistant to wear and tear.
Cost-Effective: Overmolding can be a cost-effective alternative to traditional manufacturing methods, mainly when producing smaller, more intricate parts.
Overmolding Services and Providers: Choosing the Right Partner
However, finding the right overmolding service provider can be challenging, particularly given the wide variety of providers and services available. Here, we will discuss the key factors to consider when choosing an overmolding service provider.
Factors to Consider:
Experience: Look for a service provider with a proven track record in overmolding. Check the provider’s portfolio to see if they have experience working on projects similar to yours.
Capabilities: Ensure that the provider can meet your specific needs, including material selection, customization options, and production volume.
Quality: Quality is critical in overmolding, as even minor defects can lead to product failure. Look for a provider with a robust quality control system certified by relevant regulatory bodies.
Cost: Overmolding can be expensive, so choosing a competitive pricing provider without compromising quality is essential.
Communication: Look for a provider that values clear and transparent communication. The provider should be responsive to your inquiries and keep you informed throughout the production process.
Lead Time: Consider the provider’s lead time, as delays can impact your production schedule. Ensure that the provider can meet your required deadlines.
Location: Choosing a provider geographically close to your business can reduce transportation costs and lead times.
Customer Service: Choose a provider that values customer service and will work with you to solve any issues.
Service Providers:
Injection Molding Companies: Many injection molding companies offer overmolding services as an additional offering. These companies have the advantage of experience in injection molding and can provide a full range of services, including material selection and customization options.
Contract Manufacturing Companies: Contract manufacturing companies provide manufacturing services for various industries. These companies often have extensive experience in overmolding and can offer cost-effective solutions for large volume production runs.
Specialty Providers: Specialty providers focus on specific aspects of overmolding, such as tooling or material selection. These providers can offer specialized expertise that may be valuable for complex or unique projects.
Conclusion
Overmolding is a versatile and practical process that can enhance product functionality, durability, and aesthetics across different industries. With a range of materials, techniques, and applications, overmolding offers many possibilities for manufacturers to create high-quality products that meet the needs and preferences of consumers. Manufacturers can make informed decisions and stay competitive in today’s market by considering the design, cost, sustainability, and innovation aspects of overmolding. Whether you are a product designer, engineer, or business owner, understanding the concept of overmolding can help you take your products to the next level.