Insert Injection Molding
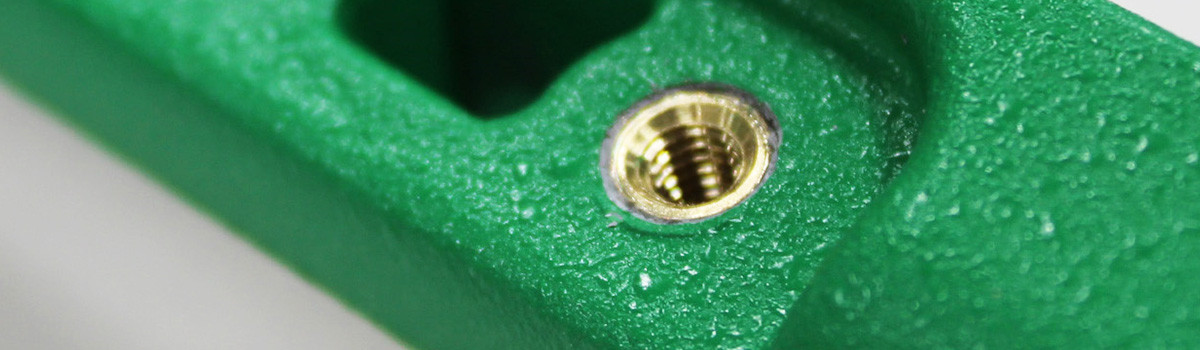
Insert injection molding is a widely used manufacturing process in producing complex plastic parts with embedded components. This technique involves inserting metal or plastic parts into the mold cavity before the injection molding process. The molten material then flows around the inserted element, creating a solid bond between the two materials. Insert injection molding offers several advantages, including improved design flexibility, reduced assembly time, and enhanced part functionality. This comprehensive guide will explore the different techniques, benefits, and applications of insert injection molding.
What is Insert Injection Molding?
Injection molding is a manufacturing process used to create a variety of parts and products. Insert injection molding is a type of injection molding that allows for the insertion of preformed elements, or inserts, into the mold before the molding process begins. This technique allows the creation of parts that require specific features that traditional injection molding methods cannot achieve.
Insert injection molding works by placing a preformed insert into the mold cavity before the molding process begins. The insert can contain various materials, including metal, plastic, and ceramics. The molding process begins as usual, with molten plastic injected into the mold cavity. As the plastic cools and solidifies, it fuses with the insert, creating a single, integrated part.
There are several advantages to using insert injection molding. One of the main advantages of this technique is that it allows for the creation of parts with specific features that traditional injection molding methods cannot achieve. For example, insert injection molding can be used if a function requires a threaded insert or a metal component for reinforcement. This technique also allows for the creation of parts with a combination of materials, such as a plastic part with a metal insert.
Another advantage of insert injection molding is saving time and money. Instead of assembling multiple components, insert injection molding creates a single, integrated piece. By doing so, companies can reduce the time and costs required for assembly.
Insert injection molding is also helpful for creating complex parts. Because the insert can be placed in the mold cavity before the molding process begins, it is possible to produce parts with complex geometries and features that would be difficult to achieve through traditional injection molding methods.
How Does Insert Injection Molding Work?
It is a type of injection molding process that allows for the insertion of preformed parts, or inserts, into a mold before the molding process begins. This technique allows for creating pieces with specific features that traditional injection molding methods cannot achieve and is especially useful for creating complex parts. Here we will discuss how to insert injection molding works.
The insert injection molding process involves the following steps:
- Insert Placement:The first step in the insert injection molding process is to place the preformed insert into the mold cavity. Manufacturers can produce this insert from various materials, such as metal, plastic, or ceramics.
- Mold Clamping:The mold is closed and clamped shut once the insert is in place. The goal is to keep the insert in place during the molding process.
- Injection of Molten Plastic:The injection molding process injects molten plastic into the mold cavity. Manufacturers typically heat the plastic to a temperature between 200 and 300 degrees Celsius, determining it based on the specific plastic used.
- Cooling and Solidification: As the plastic cools and solidifies, it fuses with the insert, creating a single, integrated part. The cooling and solidification time depends on the specific plastic used and the complexity of producing the piece.
- Mold Opening and Ejection: Once the part has cooled and solidified, the operator opens the mold and ejects the item. The piece can then be finished and prepared for use.
There are several advantages to using insert injection molding. Some of these advantages include:
- The ability to create parts with specific features that traditional injection molding methods cannot achieve
- Elements can be made as a single, integrated piece, resulting in reduced assembly time and costs
- Ability to create complex parts with complex geometries and features
- Ability to use a variety of materials, including metal, plastic, and ceramics
- Injection molding is a highly efficient and repeatable process that can produce large quantities of parts with high precision and accuracy.
Types of Inserts Used in Injection Molding
Manufacturers can use various materials, including metal, plastic, and ceramics, to make inserts. These inserts enable the creation of parts with specific features that traditional injection molding methods cannot achieve. Here we will discuss the different types of inserts used in injection molding.
- Metal Inserts:Metal inserts are commonly used in injection molding to provide additional strength and stability to plastic parts. They are typically made from brass, steel, or aluminum and can be threaded or unthreaded, depending on the application. Manufacturers can use metal inserts to create parts with complex geometries and factors that require high strength and durability.
- Plastic Inserts: Plastic inserts are often used in injection molding to support and reinforce plastic parts. They are typically made from nylon, ABS, or polycarbonate materials and can create pieces with specific features such as snap-fit connections or threaded holes. Manufacturers value plastic inserts for their ability to offer lightweight, cost-effective solutions and mold easily into various shapes and sizes.
- Ceramic Inserts: Ceramic inserts are used in injection molding to create parts that require high strength and resistance to wear and tear. They are typically made from materials such as zirconia or alumina and can be used to produce parts for the automotive, aerospace, and medical industries. Ceramic inserts are highly resistant to high temperatures, corrosion, and abrasion, making them ideal for harsh environments.
- Composite Inserts: Manufacturers combine two or more materials, such as metal and plastic, and mold them to create composite inserts, resulting in a single, integrated part. Manufacturers can utilize blended inserts to develop pieces with specific features that traditional injection molding methods cannot achieve. Furthermore, they can highly customize these inserts to meet the unique needs of particular applications.
- Overmolded Inserts: During the injection molding process, manufacturers mold inserts into a plastic part, resulting in what is known as over-molded inserts. This process involves developing a first shot of plastic around the insert and then setting a second over the first shot to create a single, integrated part. Manufacturers often use over-molded inserts to create pieces that combine materials, such as incorporating a metal insert into a plastic component.
Metal Inserts vs. Plastic Inserts
The process involves using preformed parts, or inserts, placed into a mold before the plastic injection molding process begins. Manufacturers can make inserts from various materials, including metal and plastic, and each type presents its unique advantages and disadvantages. This article will compare metal and plastic inserts and help you determine the best option for your application.
Metal Inserts
Manufacturers commonly use metal inserts in molding because of their high strength and durability. They are typically made from brass, steel, or aluminum and can be threaded or unthreaded, depending on the application. Metal inserts are often used in injection molding to provide additional strength and stability to plastic parts.
Advantages of Metal Inserts
- High strength and durability
- Resistant to wear and tear
- It can offer additional functionality through threading
- Ideal for parts with high-stress or load-bearing requirements
Disadvantages of Metal Inserts
- Higher cost than plastic inserts
- More challenging to mold than plastic inserts
- Heavy, which may be a concern in specific applications
Plastic Inserts
Plastic inserts are popular for molding due to their versatility and cost-effectiveness. Manufacturers typically make them from materials such as nylon, ABS, or polycarbonate, and they can easily mold them into various shapes and sizes. Plastic inserts are lightweight and can create parts with specific features, such as snap-fit connections or threaded holes.
Advantages of Plastic Inserts
- Cost-effective
- Lightweight
- Easily molded into a variety of shapes and sizes
- Ideal for parts with lower stress or load-bearing requirements
Disadvantages of Plastic Inserts
- Less durable than metal inserts
- Not ideal for parts with high-stress or load-bearing requirements
- It can be more susceptible to wear and tear over time
When to Choose Metal Inserts
Metal inserts excel in parts that demand high strength and durability, as they resist wear and tear and provide the added functionality of being threaded. Metal inserts are also ideal for functions with high-stress or load-bearing requirements. However, they are more expensive than plastic inserts and may be more difficult to mold.
Applications that may require metal inserts include
- Automotive and aerospace components
- Medical devices
- Industrial equipment
- Consumer electronics
When to Choose Plastic Inserts
Plastic inserts are cost-effective and versatile for parts with lower stress or load-bearing requirements. They exhibit lightweight characteristics; manufacturers can mold them into various shapes and sizes. Plastic inserts are also ideal for positions that require specific features such as snap-fit connections or threaded holes. However, they may need to be more suitable for details with high-stress or load-bearing requirements.
Applications that may require plastic inserts included
- Consumer goods
- Household appliances
- Toys and games
- Electronics
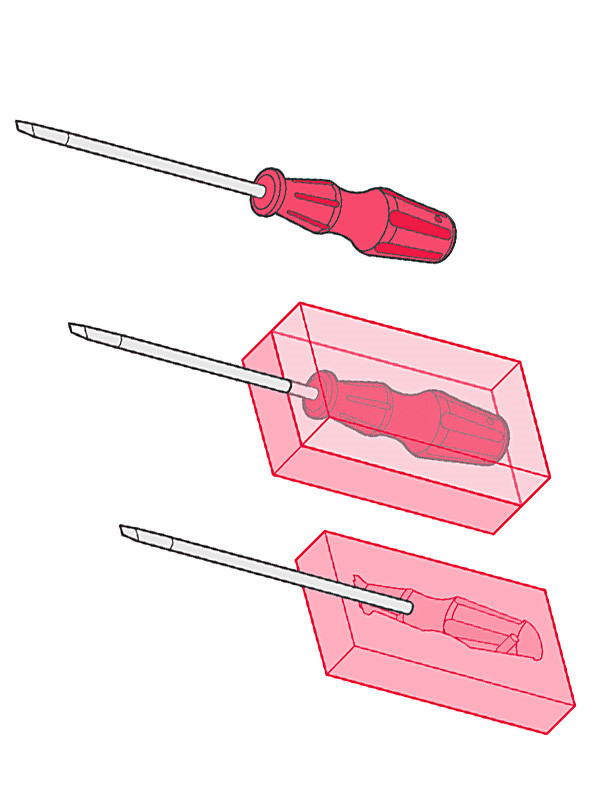
Benefits of Insert Injection Molding
Insert injection molding is a popular manufacturing process involving preformed parts or inserts placed into a mold before the plastic injection molding process begins. This technique offers numerous benefits over traditional molding methods, making it a popular choice for various applications. This article will discuss some of the main advantages of insert injection molding.
- Cost-effective: Insert injection molding can be a cost-effective manufacturing solution because it eliminates the need for post-molding assembly of separate parts. By integrating the inserts during molding, manufacturers can reduce labor and assembly costs while increasing production efficiency.
- Improved part strength: Insert injection molding can enhance the strength and durability of parts by using different materials in different areas of the piece. This feature can be particularly beneficial for applications that require details to endure high-stress or load-bearing demands.
- Increased design flexibility: Insert injection molding offers greater design flexibility, as it creates complex parts with multiple features and functions. This process is well-suited for intricate designs and geometry, making it an ideal choice for such details.
- Consistency and accuracy: Insert injection molding offers excellent consistency and accuracy in part production. We precisely position the preformed inserts into the mold, ensuring their exact placement according to the requirements of each part. As a result, we achieve uniform dimensions and exceptional quality control in the produced pieces.
- Reduced cycle time: Insert injection molding can reduce cycle time by combining multiple steps into a single process. This method can save time and enhance productivity, especially when dealing with high-volume production runs.
- Variety of materials: Insert injection molding can be used with various materials, including plastic, metal, and ceramic. Manufacturers can now select the most suitable material for any application by considering strength, durability, and cost.
- Environmental benefits: Insert injection molding can also offer environmental benefits by reducing waste and minimizing the use of materials. Because we precisely place the inserts into the mold, we experience less material waste than traditional molding methods. Implementing this can lead to a decrease in environmental impact and a reduction in manufacturing expenses.
Design Considerations for Insert Molding
Insert molding is a popular manufacturing process that involves the integration of preformed inserts into a plastic injection molding process. This technique offers numerous benefits, including improved part strength, reduced assembly costs, and increased design flexibility. However, designing parts for insert molding requires careful consideration of several factors to ensure successful and efficient production. This article will discuss some of the key design considerations for insert molding.
- Insert Placement: The placement of the insert within the mold is critical to the success of the insert molding process. The insert must be positioned precisely within the mold to ensure that the plastic material fully encapsulates it during the molding process. Designers must also ensure that the insert does not interfere with the flow of plastic material or cause any parting line issues.
- Material Compatibility: The selection of materials for both the insert and the plastic material is crucial to the success of the insert molding process. The materials must be compatible to prevent bonding issues or material incompatibilities. Designers must carefully consider the material properties, such as melting point, shrinkage, and coefficient of thermal expansion, to ensure successful insert molding.
- Part Geometry: The part’s geometry is another critical consideration for insert molding. The design must allow for proper filling and packing of the plastic material around the insert to ensure it fully encapsulates it. The part geometry must also allow for adequate venting and cooling to prevent any issues with warping, shrinkage, or sink marks.
- Draft Angles and Undercuts: The presence of draft angles and undercuts can affect the moldability of a part in insert molding. Designers must carefully consider the placement and geometry of draft angles and undercuts to ensure that they can easily remove the insert from the mold without causing any damage to the part or mold.
- Tooling Considerations: The tooling required for insert molding can be more complex than traditional molding methods. Designers must carefully consider the mold design, including the placement and geometry of the insert, the gating and venting, and any necessary side actions. Additionally, the tooling must be capable of maintaining tight tolerances to ensure proper insert placement and prevent any issues with part quality.
Materials Used in Insert Injection Molding
Insert injection molding is a highly specialized process that produces complex parts precisely and consistently. This process involves using pre-manufactured features called inserts, inserted into a mold before injection molding occurs. These inserts can be made from various materials, each with unique properties and benefits. Here we will discuss the most common materials used in insert injection molding and their advantages.
Metals
Injection molding widely uses inserts made from metals such as steel, aluminum, and brass. These materials offer excellent strength and durability, making them ideal for parts requiring high wear and tear resistance. In addition, metal inserts can withstand high temperatures, making them suitable for use in demanding applications such as the aerospace and automotive industries. Some of the specific advantages of using metal inserts in injection molding include:
- High strength and durability
- Excellent heat resistance
- Corrosion resistance
- Ability to withstand high pressure and stress
Plastics
Plastic inserts are also commonly used in injection molding, with materials such as PEEK, PTFE, and UHMW being popular choices. These materials offer a high degree of temperature resistance, chemical resistance, and low friction properties. These components are well-suited for utilization in medical devices and semiconductor manufacturing due to their high precision and cleanliness, which are critical factors in those applications. Some of the specific advantages of using plastic inserts in injection molding include:
- High chemical resistance
- Excellent temperature resistance
- Low friction properties
- Easy to machine and shape
Ceramics
In injection molding, ceramic inserts find use due to their high strength, hardness, and wear resistance. These materials are ideal for use in applications where the part needs to withstand high temperatures or harsh environments. In addition, ceramic inserts offer excellent dimensional stability, making them suitable for precision engineering applications. Some of the specific advantages of using ceramic inserts in injection molding include:
- High strength and hardness
- Excellent wear resistance
- High temperature resistance
- Dimensional stability
Composites
Composite materials, such as carbon fiber or fiberglass, are used in injection molding for their high strength-to-weight ratio. The aerospace and automotive industries often use these materials where weight reduction is critical. Composite inserts offer high stiffness and strength, making them ideal for wind turbines and high-performance sports equipment applications. Some of the specific advantages of using composite inserts in injection molding include:
- High strength-to-weight ratio
- High stiffness and strength
- Good impact resistance
- Low thermal expansion coefficient
Rubber
Rubber materials, such as silicone or neoprene, are used in injection molding for their flexibility and sealing properties. These materials are commonly used in medical and automotive industries where sealing and cushioning are essential. Rubber inserts offer excellent resistance to chemicals and high temperatures, making them ideal for use in harsh environments. Some of the specific advantages of using rubber inserts in injection molding include:
- Excellent sealing properties
- High flexibility
- Chemical and temperature resistance
- Good vibration damping
Foam
Foam materials, such as polyurethane or polystyrene, are used in injection molding for their lightweight and shock-absorbing properties. These materials are often used in packaging and automotive industries where cushioning and impact resistance are essential. Foam inserts offer high insulation, making them ideal for temperature-sensitive applications. Some of the specific advantages of using foam inserts in injection molding include:
- Lightweight and flexible
- Excellent shock absorption
- Good insulation properties
- Its ability to mold into complex shapes
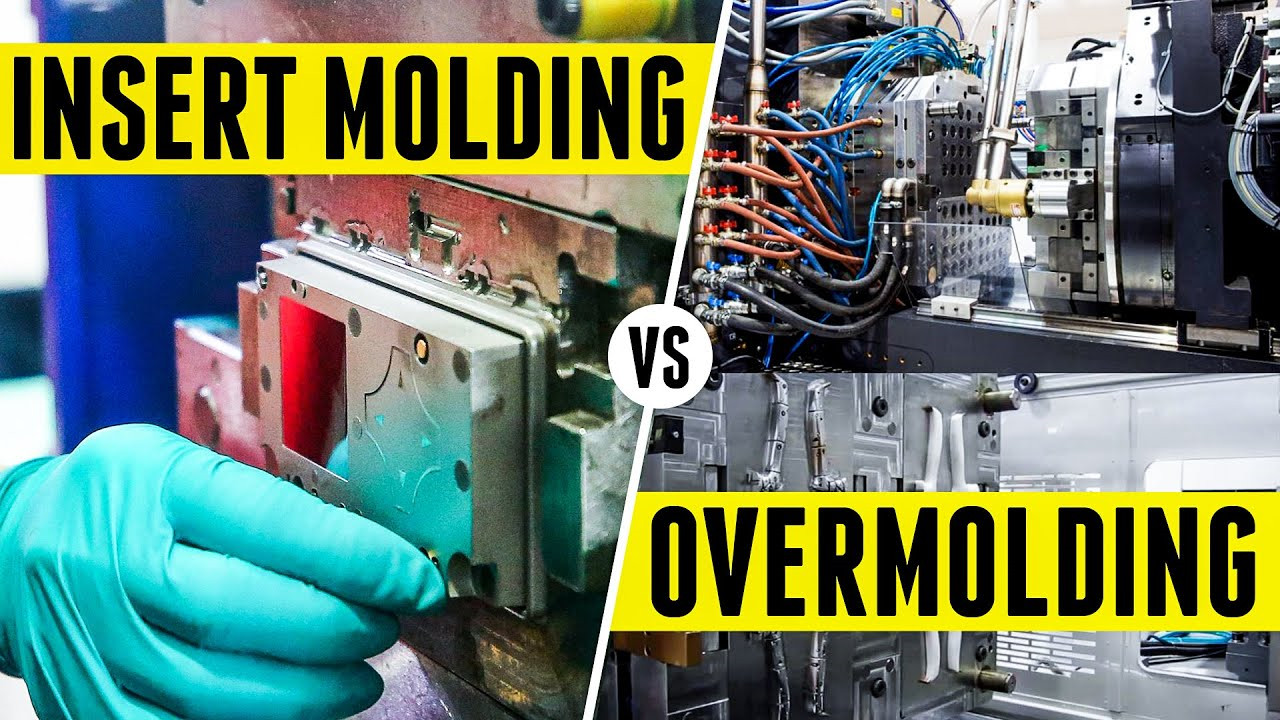
Insert Molding vs. Overmolding: What’s the Difference?
Insert molding and overmolding are two commonly used processes in injection molding involving multiple materials. While these processes may seem similar, they have some fundamental differences. Here we will discuss the differences between insert molding and over-molding.
Insert Molding
Insert molding is a process that involves the insertion of pre-fabricated parts, known as inserts, into a mold before the injection molding process takes place. The plastic material is then injected around the inserts, creating a finished product that combines the properties of the insert and the plastic material. This process is commonly used in the automotive, medical, and aerospace industries to create parts with a high degree of precision.
Advantages of insert molding
- High precision and accuracy
- Improved part strength and durability
- Reduced assembly time and cost
- Ability to combine materials with different properties
Overmolding
Overmolding is a process that involves the injection molding of a second material over a pre-existing part. Manufacturers use this process to create soft-touch handles, grips, and other consumer products. The over-molded material is typically soft and rubber-like, providing improved grip and comfort. Depending on the part’s complexity, we can perform over-molding in a single-shot or two-shot process.
Advantages of over-molding
- Improved ergonomics and aesthetics
- Improved grip and comfort
- Reduced assembly time and cost
- Ability to combine materials with different properties
Differences between insert molding and over-molding
- Insert molding involves the insertion of pre-fabricated parts, while overmolding consists of the injection molding of a second material over a pre-existing part.
- We utilize insert molding to create pieces with a high degree of precision, while we employ over-molding to enhance the ergonomics and aesthetics of a product.
- Insert molding involves combining materials with different properties, while over-molding involves using a soft, rubber-like material for the over-molded portion.
- Insert molding is often used in the automotive, medical, and aerospace industries, while over-molding is commonly used in consumer products such as tools, electronics, and personal care items.
Techniques for Insert Placement
Insert molding is a process where pre-made parts, or inserts, are placed into a mold before the injection molding process occurs. The plastic material is injected around the inserts to create a finished product. Placing the inserts is crucial to the success of the insert molding process. Here we will discuss some techniques for insert placement.
- Manual placement: An operator manually places the inserts into the mold in this technique. Manufacturers commonly use this technique for small or straightforward parts that require only a few inserts. However, it can be time-consuming and labor-intensive, and there is a higher risk of error due to manual placement.
- Automated placement: In this technique, the inserts are placed into the mold using a computerized system, such as a robot or a pick-and-place machine. This technique is faster and more accurate than manual placement, making it ideal for large production runs or complex parts. However, it requires an initial investment in equipment and may need to be more cost-effective for small-scale production.
- Insert molding over-molding: We place the inserts into a second, over-molded part and then position it into the primary mold. Manufacturers commonly use this technique for claims with complex geometries or hard-to-reach areas. It can also combine materials with different properties, such as a rigid plastic insert with a soft molded material.
- Adhesive-backed inserts:In this technique, we pre-coat the inserts with an adhesive backing, allowing us to place them in the mold without requiring manual or automated placement. The adhesive backing melts during the injection molding, bonding the insert to the plastic material. This technique is commonly used for small, simple parts and can reduce production time and cost.
- Threaded inserts: In this technique, threaded inserts are placed into the mold and are used to create threads in the finished product. Manufacturers commonly use this technique in manufacturing products that require inserting a screw or bolt, such as electronic devices or automotive parts.
Types of Insert Injection Molding Machines
One of the key components of the injection molding process is the injection molding machine. These machines come in various types, each with unique features and advantages. Here we’ll look at the different kinds of insert injection molding machines.
First, let’s define what an insert injection molding machine is. An insert injection molding machine is an injection molding machine that enables the insertion of preformed components, such as metal or plastic inserts, into the mold before injecting the plastic material. With this capability, it becomes feasible to manufacture complex parts that require additional features such as threaded openings or metal supports.
Here are the different types of insert injection molding machines:
- Vertical injection molding machines:These machines have a vertical orientation design, where they mount the mold vertically. They are ideal for insert molding because they allow easy insertion of the insert into the mold from the top. This type of machine also takes up less floor space and is better suited for smaller production runs.
- Horizontal injection molding machines:These machines have a flat orientation design, where they mount the mold horizontally. They offer the best suitability for larger production runs, and manufacturers typically use them for manufacturing more significant parts. With horizontal machines, inserts can be loaded from the side, making it more challenging to ensure proper alignment.
- Rotary table injection molding machines:These machines have a rotating table allowing multiple molds to be mounted and rotated into the injection unit for production. This type of machine is ideal for insert molding because it will enable various inserts into the mold, creating more complex parts.
- Shuttle injection molding machines: These machines have a shuttle that moves the mold back and forth between the injection unit and the molding area. They are best suited for small production runs and are ideal for insert molding because they allow for easy loading and unloading of inserts.
Process Parameters for Insert Molding
The resulting product has greater strength and durability compared to traditional injection molding. The process parameters for insert molding are critical in achieving high-quality and consistent results. Here we’ll look at the process parameters for insert molding.
- Material Selection: Material selection is an essential process parameter for insert molding. The plastic material must be compatible with the insert material and the application. Compatibility ensures that the insert and the plastic material adhere well, resulting in a strong and durable product.
- Temperature: Temperature plays a crucial role in the insert molding process. We must set the mold temperature correctly to ensure the plastic material flows uniformly and fills the cavity without voids or deformations. We must also consider the insert temperature to ensure the plastic material adheres well to the insert without causing thermal damage.
- Injection Pressure: The injection pressure is another essential parameter for insert molding. We must set the tension correctly to ensure we uniformly and quickly inject the plastic material into the mold cavity. A high injection pressure can result in the deformation of the insert or the mold, while a low injection pressure can lead to incomplete filling of the mold cavity.
- Injection Speed: The injection speed is also an essential parameter for insert molding. We must set the rate correctly to ensure the plastic material uniformly fills the mold cavity without voids or deformations. A high injection speed can lead to turbulence in the plastic material, resulting in defects in the finished product.
- Cooling Time: The cooling time is required for the plastic material to solidify and form the final product shape. We must set the cooling time correctly to ensure we achieve the desired shape and size for the finished product. A shorter cooling time can lead to deformation or shrinkage, while a longer cooling time can result in longer cycle times and reduced productivity.
- Ejection Time: We require the ejection time to eject the finished product from the mold. We must set the ejection time correctly to remove the finished product without causing any damage or deformation. A shorter ejection time can lead to incomplete ejection or damage to the product, while a longer ejection time can result in longer cycle times and reduced productivity.
Common Insert Molding Defects and How to Avoid Them
Insert molding is a popular manufacturing process that involves placing preformed components, such as metal or plastic inserts, into the mold before injecting the plastic material. This process results in more substantial and durable products than traditional injection molding. However, like any manufacturing process, insert molding can have defects that affect the quality and consistency of the final product. Here we’ll look closer at common insert molding defects and how to avoid them.
Flash: Flash is a defect that occurs when excess plastic material leaks out of the mold and forms a thin layer on the surface of the finished product. This defect can affect the appearance and function of the product. To avoid flash, you can take the following steps:
- Reduce the injection pressure
- Increase the mold clamping force
- Use a mold release agent
- Increase the cooling time
Short Shot: Short shot is a defect that occurs when the plastic material does not fill the mold cavity, resulting in an incomplete or undersized product. To avoid a short shot, you can take the following steps:
- Increase the injection pressure
- Increase the injection speed
- Increase the material temperature
- Increase the mold temperature
Warpage: Warpage is a defect when the finished product becomes deformed or twisted due to uneven cooling or shrinkage. To avoid Warpage, you can take the following steps:
- Increase the mold temperature
- Increase the cooling time
- Increase the packing pressure
- Use a balanced cooling system
Sink Marks: Sink marks are depressions or indentations that occur on the surface of the finished product due to uneven cooling or shrinkage. To avoid sink marks, you can take the following steps:
- Increase the mold temperature
- Increase the cooling time
- Increase the packing pressure
- Use thicker walls or ribbing to strengthen the product
Delamination: Delamination is a defect that occurs when the plastic material and the insert material do not bond properly, resulting in separation or peeling. To avoid delamination, you can take the following steps:
- Use a compatible plastic material and insert can material
- Increase the injection pressure and speed
- Increase the insert temperature
- Increase the mold temperature
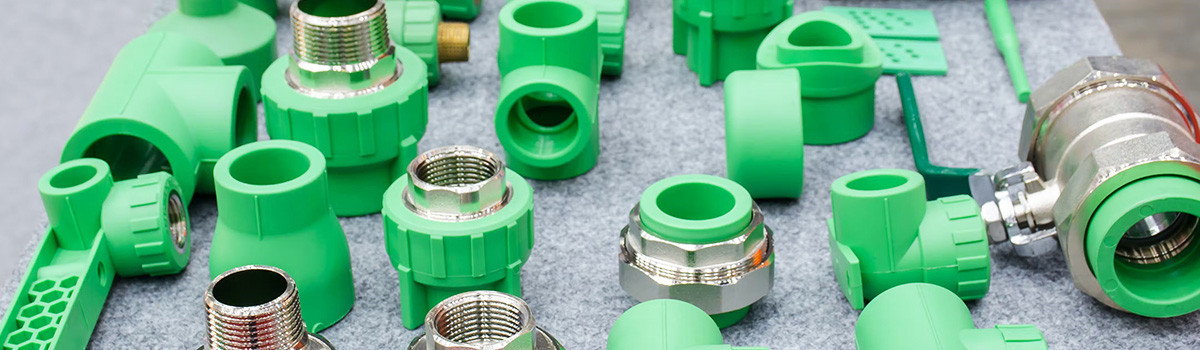
Post-Molding Operations for Insert Molding
However, after completing the insert molding process, we must perform several post-molding operations to ensure the final product meets the desired specifications. Here we’ll take a closer look at post-molding operations for insert molding.
- Deflashing:Deflashing is a process that removes any excess material, such as flash or burrs, from the finished product. This process can be performed manually or automatically, depending on the size and complexity of the product.
- Trimming:Trimming is a process that removes any excess material or protrusions from the finished product. This process can be performed using various cutting tools or methods, depending on the shape and size of the product.
- Cleaning: Cleaning is a process that removes any dirt, debris, or contaminants from the finished product. This process can be performed using a variety of cleaning agents or methods, depending on the type of material used in the insert molding process.
- Assembly:Assembly is a process that involves joining multiple components together to form a finished product. This process can be performed using various methods, such as ultrasonic welding, hot stamping, or adhesive bonding, depending on the type of material and the desired final product.
- Testing: Testing is a process that ensures the finished product meets the desired specifications and quality standards. This process can include a variety of tests, such as mechanical, electrical, or visual inspections, depending on the type of product and its intended use.
In addition to these post-molding operations, there are also several factors to consider when designing an insert molding process that will minimize the need for post-molding procedures. These include:
- Choosing the suitable materials for the insert and the molded part
- Ensuring the insert is appropriately positioned and held in place during the molding process
- Adjusting the molding parameters, such as temperature and pressure, to minimize defects and excess material
- Using high-quality molds and equipment to ensure consistency and accuracy in the finished product
Applications of Insert Injection Molding
Insert injection molding is a highly versatile manufacturing process used in many industries to produce high-quality, complex parts with greater strength and durability. Here we’ll take a closer look at the applications of insert injection molding and its benefits for different industries.
- Automotive Industry:The automotive industry is one of the most significant users of insert injection molding. It finds usage in producing various components, including airbag housings, seat belts, and engine components. The process allows for precise and accurate molding of parts that can withstand the harsh conditions of automotive use.
- Electronics Industry:The electronics industry also relies heavily on insert injection molding to produce components for devices such as smartphones, laptops, and other electronic devices. The process finds usage in creating elements such as connectors, switches, and housings for electronic components. The process is highly efficient and can produce high volumes of parts quickly and cost-effectively.
- Medical Industry: The medical industry also benefits significantly from insert injection molding. The process finds usage in producing various components, including surgical instruments, drug delivery devices, and medical implants. The method enables the precise molding of elements that can withstand the rigors of medical use and allows for the production of large volumes.
- Aerospace Industry: The aerospace industry is another industry that uses insert injection molding extensively. The process finds application in producing components such as air ducts, brackets, and housings for aircraft components. The process allows for the creation of high-strength components that can withstand the high stresses and extreme temperatures of aerospace use.
- Consumer Goods Industry: The consumer goods industry uses insert injection molding extensively to produce a wide range of products such as toys, household appliances, and sports equipment. The process allows for the creation of high-quality, durable, lightweight, and aesthetically pleasing components.
In addition to these industries, insert injection molding is also used in many other applications, including:
- Packaging Industry: for producing caps, closures, and other packaging components
- Construction Industry: for producing pipes, fittings, and other construction components
- Military Industry: for producing parts for military vehicles and equipment
Automotive Industry Applications
The automotive industry is one of the most significant users of plastic injection molding, as it is a cost-effective and efficient way to manufacture complex vehicle components. Here we’ll take a closer look at the various applications of plastic injection molding in the automotive industry.
- Interior Components: The interior of a vehicle consists of several plastic components essential for the overall aesthetics and functionality of the car. These components include a dashboard, door panels, air conditioning vents, and steering wheel components. Injection molding enables the production of these parts in high volumes quickly and cost-effectively while maintaining a high degree of accuracy.
- Exterior Components: The exterior of a vehicle consists of several plastic components, including bumper covers, headlamp assemblies, and taillight assemblies. Injection molding produces these components to high levels of accuracy, ensuring that they meet the strict safety and quality standards required in the automotive industry.
- Engine Components: Injection molding also finds use in producing several engine components, including air intake manifolds, engine covers, and oil filters. We must manufacture these components to strict tolerances and standards, and injection molding enables the production of high-quality ingredients that meet these requirements.
- Electrical Components: The electrical components in a vehicle, such as connectors, switches, and sensor housings, are also manufactured using injection molding. These components must be durable and withstand harsh operating conditions, and injection molding allows for producing high-quality ingredients that can withstand these conditions.
- HVAC Components:Injection molding produces several components used in the HVAC system of a vehicle, including air conditioning ducts and vents. These components must be manufactured to precise tolerances to ensure proper airflow and ventilation in the car.
In addition to these applications, manufacturers use injection molding to produce several other automotive components, including fuel, brake, and suspension systems.
The benefits of using injection molding in the automotive industry are numerous, including:
- High Efficiency:Injection molding allows for rapidly producing high-quality components in large volumes, reducing production times and costs.
- Precision:Injection molding allows for creating of components with high accuracy and consistency, ensuring they meet strict quality standards.
- Customization: Injection molding allows for the production of complex shapes and designs, allowing manufacturers to customize components to meet specific design requirements.
Medical Industry Applications
The medical industry is a field where precision and reliability are paramount, making plastic injection molding an ideal manufacturing process for producing medical components. Here we’ll take a closer look at the various applications of plastic injection molding in the medical industry.
- Surgical Instruments: Injection molding produces many surgical instruments, including forceps, clamps, and scalpels. Manufacturers must manufacture these components to strict tolerances and standards to ensure the highest accuracy and precision.
- Medical Devices:Manufacturers also use injection molding to produce medical devices, such as catheters and respiratory components. To guarantee the safety and dependability of patients, manufacturers must manufacture these components according to rigorous standards.
- Diagnostic Components: Manufacturers use injection molding to produce several components used in diagnostic equipment, such as pipettes, syringes, and test tubes. These components must be manufactured to precise tolerances to ensure accurate test results.
- Packaging: Injection molding produces packaging for medical products, such as sterile trays, containers, and packaging components. These components must be manufactured to strict standards to ensure the sterility and safety of medical products.
- Dental Components: Injection molding produces several dental components, including mouthguards, trays, and orthodontic pieces. These components must be manufactured to precise tolerances to ensure proper fit and comfort for the patient.
In addition to these applications, manufacturers use injection molding to produce several other medical components, including prosthetics, hearing aids, and laboratory equipment.
The benefits of using injection molding in the medical industry are numerous, including:
- High Precision:Injection molding allows for producing components with high levels of accuracy and consistency, ensuring that they meet strict quality standards.
- Customization:Injection molding allows for the production of complex shapes and designs, allowing manufacturers to customize components to meet specific design requirements.
- Cost-Effective: Injection molding is a cost-effective manufacturing process that produces high-quality components in large volumes, reducing production times and costs.
Electronic Industry Applications
The electronic industry is a field that relies heavily on precise and efficient manufacturing processes. Plastic injection molding is an ideal process for producing electronic components due to its accuracy, versatility, and speed. Here we’ll take a closer look at the various applications of plastic injection molding in the electronic industry.
- Connectors: Injection molding produces a wide range of connectors used in the electronic industry, including USB connectors, HDMI connectors, and audio jacks. These components must be manufactured to precise tolerances to ensure proper function and compatibility.
- Housings and Enclosures: Injection molding produces housings and enclosures for electronic devices, including cell phones, laptops, and other consumer electronics. Manufacturers must manufacture these components to precise specifications to ensure proper fit and function.
- Switches: Injection molding produces several types of controls used in electronic devices, including rocker switches, push-button switches, and slide switches. These components must be manufactured to precise tolerances to ensure reliable function.
- LED Components:Injection molding produces several components used in LED lighting, including lenses, reflectors, and diffusers. Manufacturers must manufacture these components to precise specifications to ensure proper light distribution and efficiency.
- Power Supply Components: Injection molding produces several components used in power supply units, including sockets, plugs, and cable connectors. These components must be manufactured to precise tolerances to ensure safe and reliable operation.
In addition to these applications, manufacturers use injection molding to produce several other electronic components, including keyboards, computer mice, and remote controls.
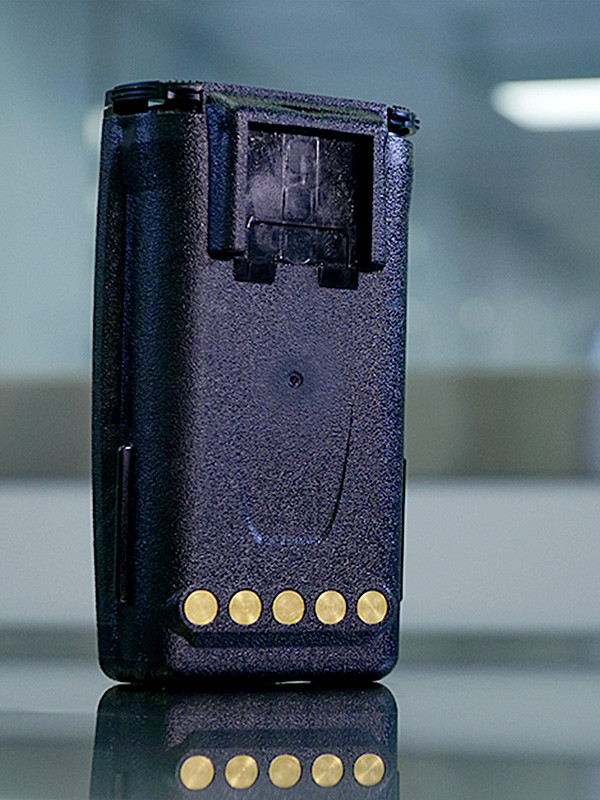
The benefits of using injection molding in the electronic industry are numerous, including:
- High Precision: Injection molding allows for producing components with high levels of accuracy and consistency, ensuring that they meet strict quality standards.
- Customization: Injection molding allows for the production of complex shapes and designs, allowing manufacturers to customize components to meet specific design requirements.
- Speed:Injection molding is a fast and efficient manufacturing process that allows for producing high-quality components in large volumes, reducing production times and costs.
Aerospace Industry Applications
The aerospace industry is a sector that requires the highest level of precision, accuracy, and durability in all its components. Plastic injection molding in the aerospace industry has become increasingly common due to its ability to produce complex geometries, reduce weight, and enhance structural integrity. Here we’ll take a closer look at the various applications of plastic injection molding in the aerospace industry.
- Interior Components: Injection molding produces a range of interior components for aircraft, including seat backs, tray tables, and overhead compartments. These components must be lightweight and durable, capable of withstanding high stress and wear and tear.
- Structural Components: Injection molding produces structural components for aircraft, including wingtips, fairings, and fuselage sections. These components must be lightweight, strong, and durable to ensure the safety and efficiency of the plane.
- Engine Components:Injection molding produces several components for aircraft engines, including turbine blades, fuel nozzles, and housings. These components must be manufactured to precise specifications to withstand high temperatures, pressures, and stresses.
- Electrical Components: Injection molding produces electrical components for aircraft, including connectors, switches, and wire harnesses. These components must be manufactured to precise tolerances to ensure proper function and reliability.
- Instrumentation Components:Injection molding produces instrumentation components for aircraft, including control panels and instrument housings. These components must be durable and withstand high temperatures, pressures, and vibrations.
In addition to these applications, manufacturers use injection molding to produce several other components for the aerospace industry, including brackets, fasteners, and gaskets.
The benefits of using injection molding in the aerospace industry are numerous, including:
- Weight Reduction: Injection molding allows for the production of lightweight components that reduce the aircraft’s weight, resulting in lower fuel consumption and increased efficiency.
- Precision:Injection molding allows for producing parts with high accuracy and consistency, ensuring they meet strict quality standards.
- Customization:Injection molding allows for the production of complex shapes and designs, allowing manufacturers to customize components to meet specific design requirements.
- Durability: Injection molding produces parts that are durable and able to withstand high levels of stress, temperature, and pressure, ensuring the safety and reliability of the aircraft.
Consumer Goods Industry Applications
The consumer goods industry is one of the most critical sectors of the global economy. Consumer goods are products that individuals use daily, including household items, electronics, toys, and personal care products. Plastic injection molding in the consumer goods industry has become increasingly popular due to its ability to produce high-quality components with precision and accuracy. Here we’ll take a closer look at the various applications of plastic injection molding in the consumer goods industry.
- Packaging: Injection molding is used extensively in producing packaging materials for consumer goods, including food packaging, beverage bottles, and cosmetic containers. Injection molding allows for the production of complex shapes and designs, ensuring that the packaging materials are functional and visually appealing.
- Household Items: Injection molding produces a range of household items, including kitchen utensils, storage containers, and cleaning supplies. These items must be durable, lightweight, and withstand daily use.
- Toys: Injection molding produces various toys, including action figures, dolls, and board games. These toys must be manufactured to precise specifications to ensure they are safe and durable.
- Personal Care Products: Injection molding produces unique care products, including toothbrushes, razors, and shampoo bottles. These products must be aesthetically pleasing, functional, and withstand frequent use.
- Electronics: Injection molding produces several components for electronic devices, including cases, buttons, and connectors. These components must be durable, lightweight, and withstand high temperatures and pressures.
In addition to these applications, manufacturers use injection molding to produce several other components for the consumer goods industry, including automotive parts, medical devices, and industrial equipment.
The benefits of using injection molding in the consumer goods industry are numerous, including:
- Cost-Effective:Injection molding allows for producing high-quality components at a lower cost than other manufacturing processes.
- Customization: Injection molding allows creating elements with complex shapes and designs, allowing manufacturers to customize features to meet specific design requirements.
- Precision: Injection molding has highly accurate and consistent details that meet strict quality standards.
- Durability: Injection molding makes parts durable and able to withstand high levels of stress, temperature, and pressure, ensuring the safety and reliability of the products.
Future Trends in Insert Injection Molding
As technology advances and consumer demands change, the insert injection molding industry constantly evolves. Manufacturers always look for ways to improve efficiency, reduce costs, and produce higher-quality products. Here we’ll look at some future trends in insert injection molding.
- Automation: Automation is becoming increasingly popular in the manufacturing industry, and insert injection molding is no exception. Automated systems can reduce labor costs, increase production speed, and improve quality control.
- Sustainability: With the growing environmental concern, manufacturers are looking for ways to reduce waste and improve sustainability. Using recycled materials and designing products that can be easily recycled or reused are just a few ways manufacturers address this issue.
- 3D Printing: Some aspects of insert injection molding already use 3D printing, but it has the potential to become even more prevalent in the future. The ability to quickly create prototypes and produce customized components is just one advantage of 3D printing.
- Advanced Materials: Researchers and manufacturers are developing new materials that withstand various temperatures, pressures, and stresses.
- Smart Manufacturing:Smart manufacturing involves using technology to gather and analyze data in real-time, allowing for faster decision-making and more efficient production. This technology can improve quality control, reduce downtime, and increase productivity.
Conclusion
Insert injection molding is a versatile and cost-effective manufacturing process that allows for the creation of complex parts with embedded components. Its advantages over traditional assembly methods make it popular in various industries, including automotive, medical, electronics, aerospace, and consumer goods. By understanding the different techniques, materials, and design considerations involved in insert injection molding, manufacturers can optimize their production processes and deliver high-quality products to their customers. As technology advances, we can expect to see even more innovative applications of insert injection molding.