6 Common Plastic Injection Molding Defects And Solutions
6 Common Plastic Injection Molding Defects And Solutions
It is common that when working with plastic injection molding many difficulties arise. However, you should not panic, most of these difficulties are quite common and easily resolved. Here we will put a list, with a varied number of solutions to take.
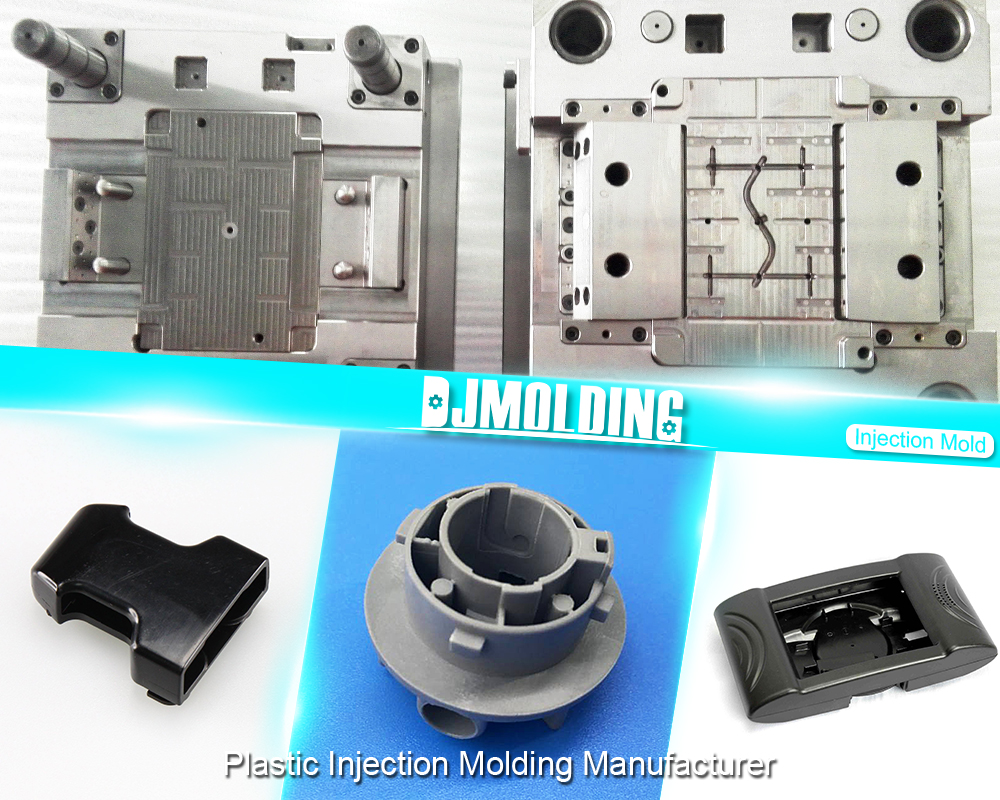
Problem # 1: Diesel Effect
First, what do we mean by the diesel effect?
It is when black marks or burns appear on the molded part.
This is difficult, in most cases, because the parts are not fully filled in those areas.
This effect is due to poor ventilation, the air cannot escape or does not move quickly towards the corners, leaving the temperature compressed and accelerated to very high levels.
Solution
Place vents in areas where burns vary and limit injection speed.
Problem # 2: Mold Fill Too Slow
It is of utmost importance that the pressure phase of accessories happens at the right time.
If it occurs too soon, the pressure affected, making it impossible to completely fill the cavity.
But, if it happens too fast, it results in a pressure spike that can damage the mold.
Solution
- Increase the temperature profile for the material.
- Increase the temperature of the nozzle.
- Increase or decrease the temperature of the mold.
- Increase injection pressure.
Problem # 3: Orange Peel
It is a problem caused by poor polishing of the mold.
It is called that because the surface of the plastic pieces acquires a texture similar to the peel of an orange.
It can create undesirable defects like ripples and pitting, affecting the quality of the final product.
Solution
- Correct mold polishing.
- If necessary, change the material so that it is suitable for the injected part.
Problem # 4: Sunken Marks and Gaps
Sunken marks are caused by solidification and contraction of the outer surface rather than the inner surface.
What do we mean by this?
Once the outer surface solidifies, an internal shrinkage of the material occurs, causing the shoreline to depress below the surface and causing subsidence.
The holes are also caused by the same phenomenon, but it manifests itself with an internal hole.
Solution
It can be solved using thinner sections and uniform thicknesses.
Problem # 5: The Mold Has A Defect In Finishing Or Design.
This happens when the mold has an error or deformity, causing the final result not to be as expected, causing problems and delayed production.
Solution
- Add a surface coating to the mold.
- Grind the surface of the mold.
- Change mold ultimately.
Problem # 6: There is poor coloration on the part.
The coloring of the pieces to be molded is a critical step, since the beauty of the piece, the identification and the optical functions depend on this process.
Therefore, if the color and its concentrate are not chosen correctly, the result will not be as expected, and therefore, the piece can be considered as a waste.
Solution
The dye may not be appropriate. Try to change the type of dye or concentration.
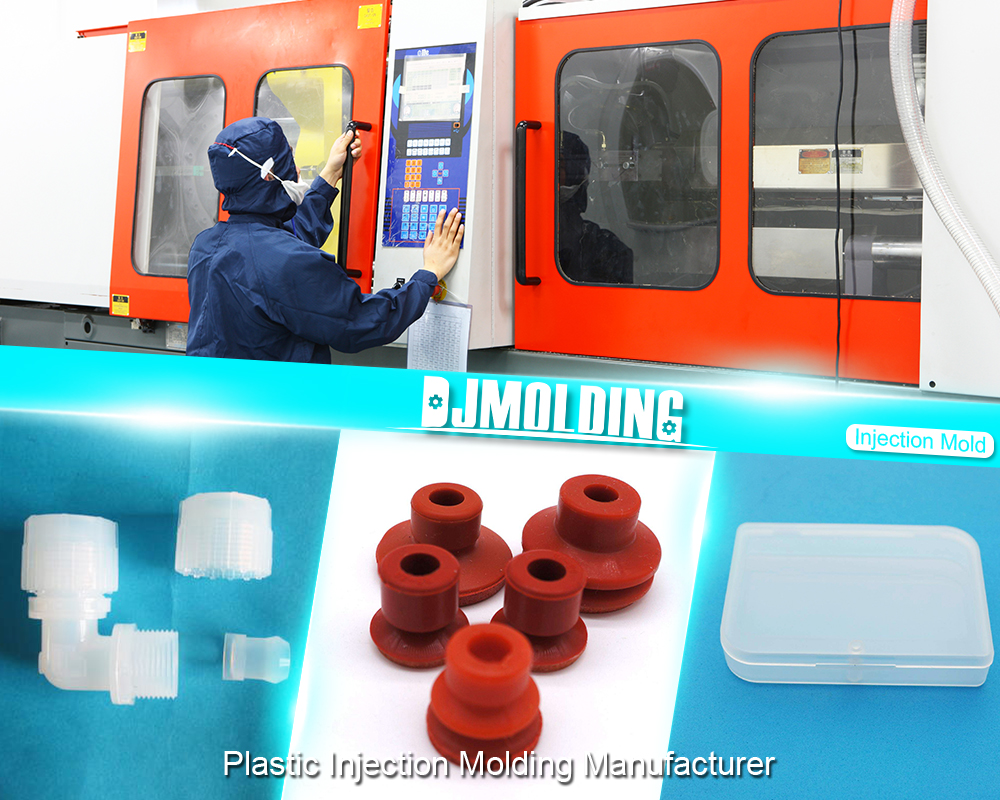
For more about the common plastic injection molding defects and solutions,you can pay a visit to Djmolding at https://www.djmolding.com/solutions-to-common-molding-defects-of-injection-molding/ for more info.