The Importance Of Mold Engineers In Plastic Injection Mold Design
The Importance Of Mold Engineers In Plastic Injection Mold Design
Plastic injection molding is a widely used manufacturing process involving injecting molding plastic into a mold to create various products. The success of this process depends heavily on the design and development of the mold, which is a critical component in determining the final product’s quality, efficiency, and cost-effectiveness. Mold engineers play a pivotal role in this process, bringing expertise and precision to ensure the molds are designed and manufactured to meet stringent requirements. This article explores the importance of mold engineers in plastic injection mold design, delving into their responsibilities, the challenges they face, and the value they add to the manufacturing process.
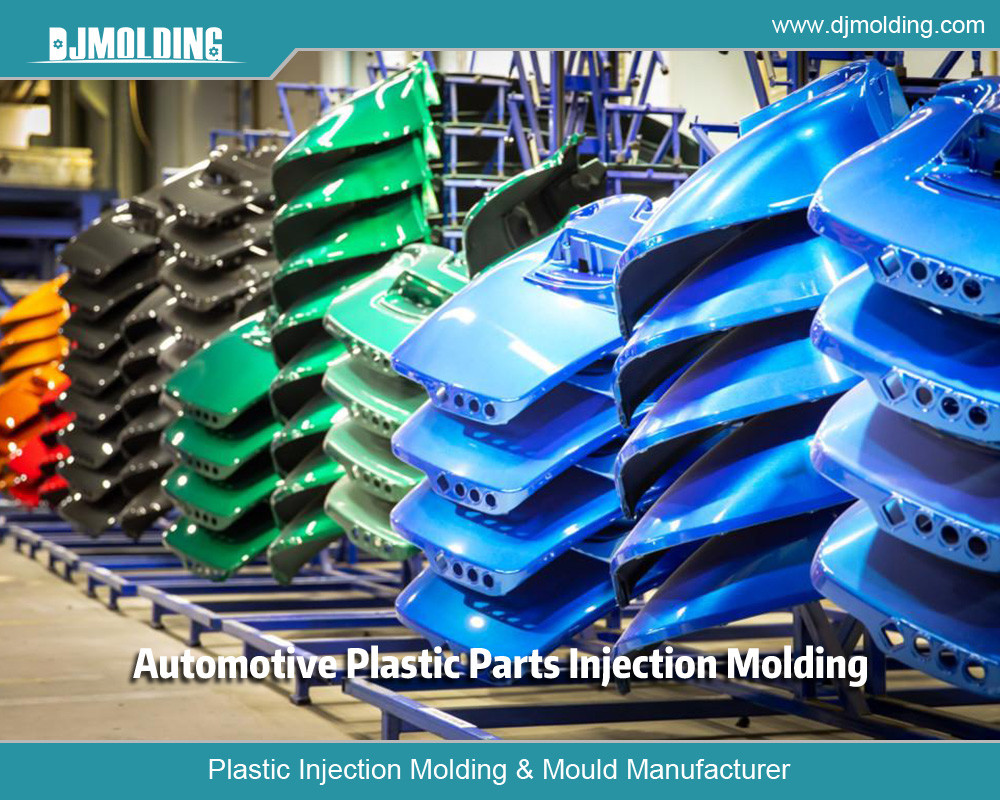
The Role of Mold Engineers in Plastic Injection Molding
Expertise in Material Selection
One of the primary responsibilities of mold engineers is to select the appropriate materials for the mold and the plastic product. This involves understanding the properties of various plastics, such as their melting points, tensile strength, and thermal expansion. Mold engineers must also consider the material’s compatibility with the product’s intended use, ensuring it meets all required specifications and standards.
Precision in Mold Design
Mold design requires high precision to ensure the final product meets the desired dimensions and tolerances. Mold engineers use advanced software and tools to create detailed designs that account for the molten plastic’s shrinkage, cooling rates, and flow characteristics. They must also ensure that the mold design allows for efficient manufacturing, minimizing waste and reducing cycle times.
Prototyping and Testing
Engineers often create prototypes before a mold is finalized to test the design and identify potential issues. This phase is crucial for ensuring the mold will perform as expected in production. Prototyping allows engineers to make necessary adjustments and improvements, leading to a more reliable and efficient mold design.
Collaboration with Other Teams
Mold engineers work closely with other teams, including product designers, manufacturing engineers, and quality control specialists. This collaboration ensures the mold design aligns with the product requirements and manufacturing capabilities. By working together, these teams can identify potential challenges early in the design process and develop solutions that enhance the final product’s quality and performance.
Challenges Faced by Mold Engineers
Complex Geometries
As product designs become more complex, mold engineers must develop innovative solutions to create molds that can produce intricate shapes and features. This often involves advanced techniques such as multi-cavity molds, insert molding, and over-molding. Engineers must also consider the impact of these complexities on the manufacturing process, ensuring the molds are both feasible and cost-effective to produce.
Tight Tolerances
Many plastic products require tight tolerances to ensure proper fit and function. Achieving these tolerances can be challenging, mainly when dealing with variations in material properties and environmental conditions. Mold engineers must use precise machining and quality control processes to ensure the molds meet these stringent requirements.
Cost Constraints
Balancing cost and quality is a constant challenge in mold design. Engineers must find ways to create high-quality molds while minimizing production costs. This often involves optimizing the mold design to reduce material usage, improving manufacturing processes to increase efficiency, and selecting cost-effective materials that meet performance requirements.
Rapid Technological Advancements
Plastic injection molding constantly evolves, with new materials, technologies, and techniques emerging regularly. Mold engineers must stay up-to-date with these advancements to ensure their designs remain competitive and effective. This requires continuous learning and adaptation and a willingness to experiment with new approaches and tools.
The Value Added by Mold Engineers
Improved Product Quality
One of mold engineers’ most significant contributions is their ability to enhance product quality. Engineers help ensure the final products meet all required specifications and standards by designing molds that produce consistent, high-quality parts. This results in fewer defects, reduced waste, and increased customer satisfaction.
Increased Manufacturing Efficiency
Efficient mold design is crucial for optimizing the injection molding process. Mold engineers develop designs that minimize cycle times, reduce material waste, and improve production efficiency. This leads to lower manufacturing costs and faster time to market for new products, providing manufacturers with a competitive advantage.
Enhanced Innovation
Mold engineers are vital in driving innovation within the plastic injection molding industry. Their expertise allows them to develop new and improved mold designs that can produce more complex and sophisticated products. This innovation helps manufacturers stay ahead of the competition and meet the market’s ever-changing demands.
Cost Savings
Effective mold design can result in significant cost savings for manufacturers. By optimizing the use of materials, reducing waste, and improving manufacturing efficiency, mold engineers help lower production costs. These savings can be passed on to customers or reinvested in further innovation and development, creating a positive feedback loop that benefits the entire industry.
Case Studies: The Impact of Mold Engineers
Case Study 1: Automotive Industry
In the automotive industry, precision and reliability are paramount. Mold engineers are critical in designing molds for various plastic components, from dashboards to engine covers. For example, an automotive manufacturer needed a lightweight yet durable plastic component for a new vehicle model. Mold engineers selected a high-performance plastic material and designed a complex mold with multiple cavities to produce the part efficiently. The result was a high-quality component that met all performance requirements and contributed to the overall weight reduction of the vehicle.
Case Study 2: Medical Devices
The medical device industry demands exceptionally high standards for product quality and safety. Mold engineers are instrumental in designing molds for medical components, such as syringes and catheter tips, which require precise dimensions and smooth surfaces. In one case, a medical device manufacturer needed to produce a small, intricate component with tight tolerances. Mold engineers used advanced simulation software to design a mold that ensured consistent quality and reduced the risk of defects. This allowed the manufacturer to produce the component at scale while maintaining the highest quality and safety standards.
Case Study 3: Consumer Electronics
Consumer electronics products often feature complex designs and require high-volume production. Mold engineers are essential in designing molds that produce these components efficiently and cost-effectively. For instance, a smartphone manufacturer needed a durable yet lightweight plastic housing for a new device. Mold engineers designed a mold that optimized material usage and minimized cycle times, resulting in a high-quality housing that met the manufacturer’s specifications. This allowed the company to bring the new device to market quickly and competitively.
Future Trends in Mold Engineering
Advancements in Simulation Software
Simulation software has revolutionized mold design by allowing engineers to model and test their designs before creating physical prototypes. Future advancements in this technology will provide even more accurate and detailed simulations, helping engineers optimize their designs more effectively. This will further improve product quality, manufacturing efficiency, and cost savings.
Integration of AI and Machine Learning
Artificial intelligence (AI) and machine learning are set to play an increasingly important role in mold engineering. These technologies can analyze vast amounts of data to identify patterns and trends, helping engineers make more informed decisions about mold design and manufacturing processes. AI-driven tools can also automate certain aspects of the design process, reducing the time and effort required to develop high-quality molds.
Sustainable Materials and Practices
As environmental concerns become more prominent, mold engineers must focus on developing sustainable materials and practices. This includes designing molds that use recycled or bio-based plastics, optimizing processes to reduce energy consumption, and implementing strategies to minimize waste. By prioritizing sustainability, mold engineers can help the plastic injection molding industry reduce its environmental impact and meet evolving regulatory requirements.
Additive Manufacturing (3D Printing)
Additive manufacturing, or 3D Printing, is increasingly used in mold making. This technology allows for rapidly producing complex mold components that would be difficult or impossible to create using traditional methods. As 3D printing technology advances, mold engineers will be given new opportunities to innovate and improve their designs.
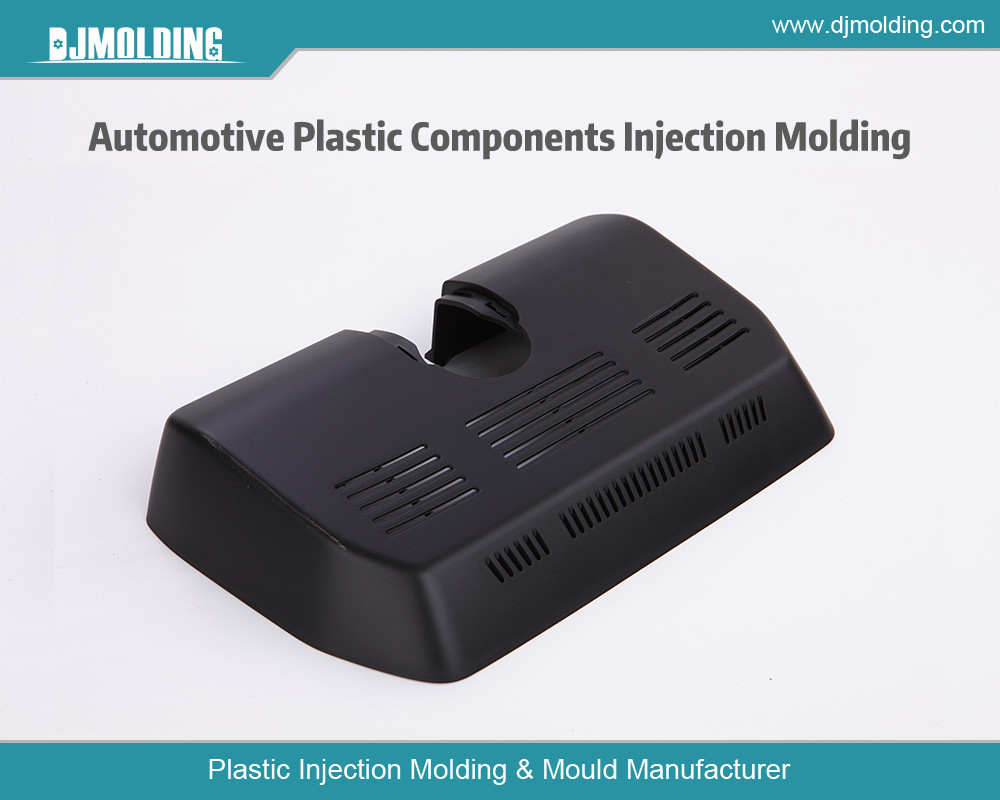
Conclusion
Mold engineers are indispensable to plastic injection molding, providing the expertise and precision necessary to design and develop high-quality molds. Their contributions enhance product quality, increase manufacturing efficiency, drive innovation, and deliver cost savings. Despite the challenges they face, mold engineers continue to play a vital role in advancing the field and meeting the market’s ever-changing demands. As technology and materials evolve, the importance of mold engineers will only grow, ensuring the continued success and competitiveness of the plastic injection molding industry.
For more about the importance of mold engineers in plastic injection mold design,you can pay a visit to Djmolding at https://www.djmolding.com/injection-mould-design/ for more info.