The Different Types Of Plastic Injection Moulding Machine – Pros and Cons
The Different Types Of Plastic Injection Moulding Machine – Pros and Cons
Injection molding happens to be a popular manufacturing process for creating a variety of products, particularly plastic items. Businesses and manufacturers prefer this method for its cost-effectiveness and ability to produce high-quality end products.machine
Injection molding employs a variety of machines to achieve quality processes and products. Understanding these machines is essential for a successful injection molding project, even though manufacturers can manage this aspect. Different types of injection molding machines offer unique advantages and capabilities.
Therefore, this article will be discussing the pros and cons of the 3 types of injection moulding machine – Electric Injection Moulding Machine, Hydraulic Injection Moulding Machine, and Hybrid Injection Moulding Machine.
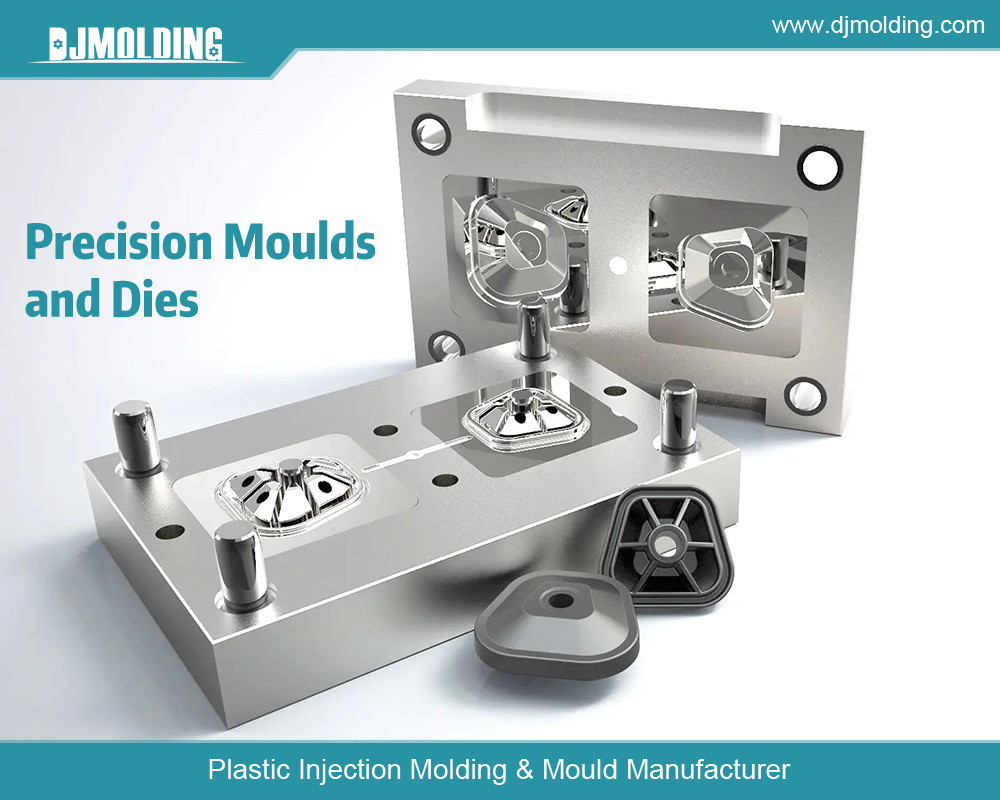
Hydraulic Injection Moulding Machine
The hydraulic injection molding machine, originally developed in the 1930s, continues to be utilized in various applications and product manufacturing. Its use depends on specific needs, such as personal preferences and electricity costs.
This machine is known for its straightforward mechanics and internal workings. Hydraulic cylinders, applying high pressure, are used to securely clamp the mold halves together during the injection molding process, ensuring precision and accuracy.
After melting the plastic pellets, they are forced into the mold’ cavity to take on the desired shape. The liquid plastic is then cooled to solidify within the mold. Once the product has cooled and solidified, it is removed, and the process is repeated. Maintaining optimal pressure is crucial to keep the mold closed and ensure the final product is free of defects.
The hydraulic injection molding machine typically applies significant clamp force for every square inch of thin walls. Advancements in technology have led to the evolution of these machines, allowing for the production of parts weighing over 50 pounds.
Modern hydraulic machines can now guarantee clamp forces in thousands of tons, making them suitable for manufacturing large and heavy parts. These machines are particularly useful in the automotive world. Hydraulic injection molding machines are basically liked for the following reasons;
Pros of Hydraulic Injection Molding Machines
- Injection rates are better.
- Bigger slot sizes.
- Enhanced injection capabilities.
- More clamping force for bigger parts.
- Requires less upfront payment for purchase.
- Reduced maintenance costs because bad parts can be replaced if need arises.
- Guarantees better control for big-sized projects.
Cons
Hydraulic injection molding machines have some drawbacks to consider:
- They tend to be noisier and less precise than other types of machines.
- Require more temperatures to mold and longer cooling times for the products to set.
- They consume more electricity compared to alternative injection molding machines.
Electric Injection Moulding Machine
Electric injection molding machines made their debut in Japan in the 1980s and rapidly gained popularity in the manufacturing sector. This innovative technology, featuring high-speed servo motor with digital control, provided enhanced speed and precision in the molding process.
Recognized for their efficiency, electric machines quickly captured a significant market share, constituting over half of injection molding machines sold in the United States. The seamless integration and superior performance of electric machines have made them a favored choice in the manufacturing industry.
Electric injection molding machines offer excellent repeatability, energy efficiency, and predictability in their operations. Their ability to consistently replicate successful manufacturing processes ensures a high-quality output and increased production volume. Furthermore, the use of these machines reduces labor costs as they can operate with minimal human intervention once programmed.
Pros of Electric Injection Moulding Machine
The electric injection molding machine offers several advantages:
- Provides a clean process with no risk of fluid leakage
- Lower downtime compared to hydraulic machines
- Energy savings of about 40 to 60%
- Quiet operations with a reduction in motor noise
- Faster rapid injection
- Reduced material waste and lower unit costs
- Improved precision and repeatability for efficient production
Cons
While the electric injection molding machine offers numerous advantages, it also has some drawbacks:
- High initial investment cost
- Certain components are prone to wear and could be costly to replace
- Limited clamping force compared to hydraulic machines, making them less suitable for manufacturing large products.
Hybrid Injection Molding Machines
Hybrid injection molding machines combine the strong clamp force of hydraulic systems with the energy efficiency, precision, and noise reduction of electric injection moulding machines. This results in enhanced performance for thin/thick walled part, making them a popular choice for manufacturers seeking efficiency and superior results.
Electric screw drives were sought after by molders four decades ago to achieve faster cycles, prioritizing speed over energy efficiency. Hybrid injection molding machines utilize a servo motor connected to a hydraulic pump to circulate oil for hydraulic pressure, activating machine components.
This setup allows continuous power adjustments, resulting in low emissions, reduced noise levels, and energy conservation. Servo motors, with quicker response times compared to standard hydraulic pumps, enable faster cycles and reduced cycle times. Encoders ensure precise control and consistency by tracking rotation position accurately.
Modern hybrid injection molding machines typically entail lower maintenance and experience fewer downtimes compared to all-hydraulic or all-electric machines. Furthermore, the price of hybrid machines falls between these two types, rendering them a cost-effective solution for medical device manufacturers.
Pros of Hybrid Injection Molding Machines:
- Enable versatility in product design
- Closed-loop process with rapid response times
- Enhanced efficiency leads to quicker returns on investment
- Lower operating temperature reduces cooling time
- Utilizes a two-clamp system instead of the toggle mechanism
- Allows for continuous adjustments thanks to the servo pump
Cons
Maintenance of hybrid injection molding machines, which combine hydraulic and electric components, can be challenging. A technician proficient in both electric and hydraulic machine mechanics is essential to address maintenance and repair issues effectively.
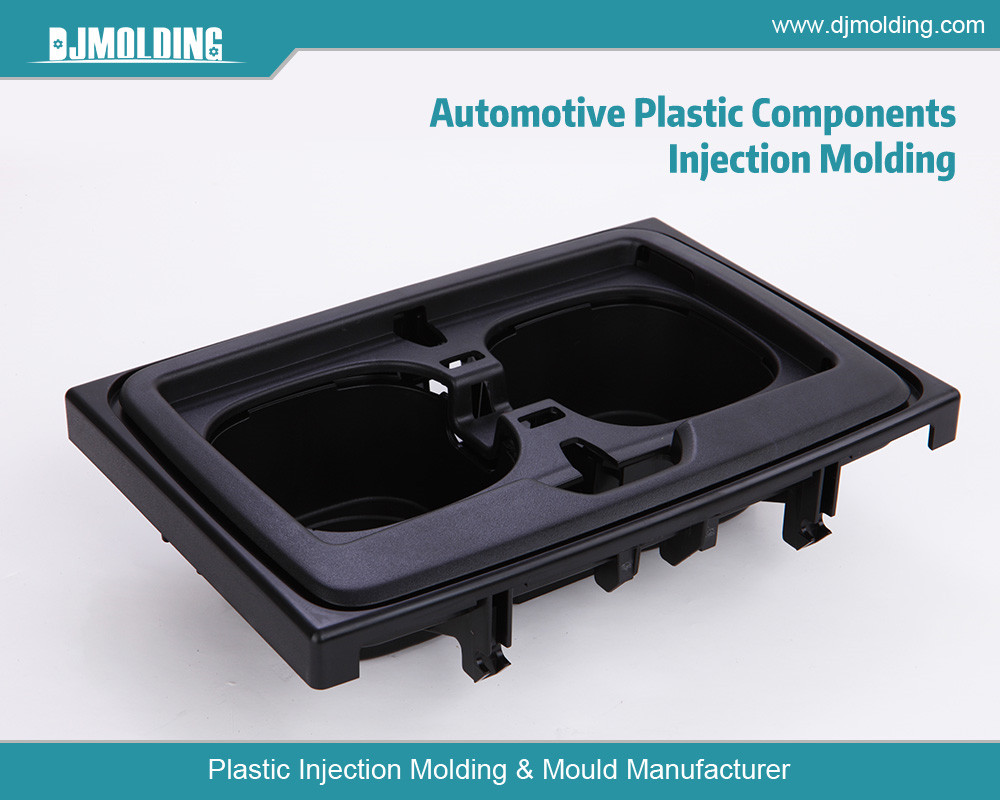
Final Thoughts
Injection molding is a valuable manufacturing process for producing quality products. Different types of injection molding machine are available, so it’s essential to determine which type best suits your needs.
Partnering with an experienced injection molding manufacturer can help you navigate this process effectively. Take the time to plan and develop your products carefully to achieve the desired outcomes and ensure successful manufacturing results.
For more about the different types of plastic injection moulding machine – pros and cons,you can pay a visit to Djmolding at https://www.djmolding.com/types-of-plastic-injection-molding-machines-used-in-plastic-parts-manufacturing-industry/ for more info.