Everything You Need To Know About Hot Runner Plastic Injection Molding
Everything You Need To Know About Hot Runner Plastic Injection Molding
Hot runner plastic injection molding is involves forcing molten plastic in a mold’ cavity to create a desired shape or product. Unlike traditional cold runner molding, hot runner molding utilizes a heated manifold system to deliver the plastic material directly to the mold cavity’, eliminating the need for a separate runner system. This results in several advantages, including reduced waste and scrap, improved part quality and consistency, faster cycle times, increased design flexibility, and cost savings in the long run.
The history of hot runner technology can be traced back to the 1960s when it was first introduced as a solution to address the limitations of cold runner molding. The initial designs were simple and consisted of heated nozzles that were attached directly to the mold.
Over the years, advancements in technology and materials have led to the development of more sophisticated hot runner systems that offer greater control and precision. Today, hot runner plastic injection molding is widely used in various industries for the production of high-quality plastic parts.
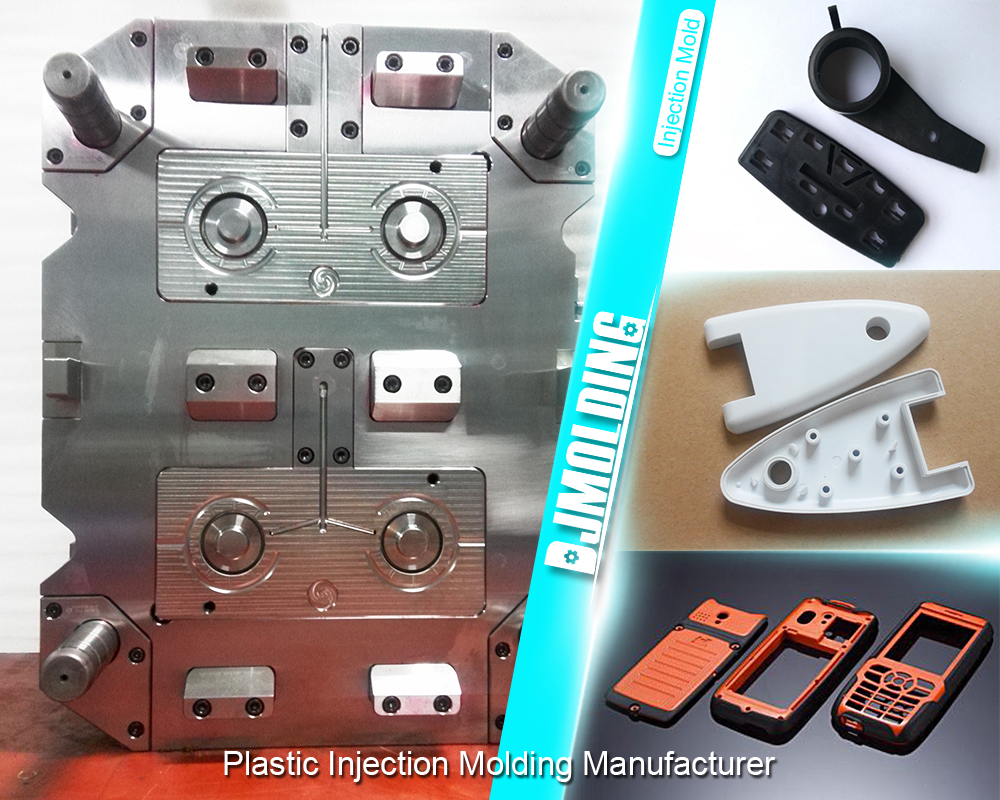
Advantages of Hot Runner Plastic injection molding
One of the key advantages of hot runner plastic injection molding is the significant reduction in waste and scrap. With traditional cold runner molding, the excess plastic material in the runner system is typically discarded after each cycle. In hot runner molding, however, there is no separate runner system, which means that there is no waste material to be discarded. This not only reduces material costs but also minimizes environmental impact.
Furthermore, hot runner molding offers improved part quality and consistency. The direct delivery of molten plastic to the mold cavity’ ensures that each part is filled uniformly, resulting in consistent dimensions and properties. This eliminates issues such as flow lines, sink marks, and warpage that are commonly associated with cold runner molding. The precise control over temperature and flow also allows for better control over part aesthetics, such as surface finish and color.
In addition to improved part quality, hot runner molding also offers faster cycle times compared to cold runner molding. The elimination of the runner system reduces the time required for material to flow from the injection unit to the mold cavity’, resulting in shorter cycle times. This increased efficiency translates into higher production rates and reduced lead times, making hot runner molding ideal for high-volume production.
Another advantage of hot runner plastic injection molding is increased design flexibility. The absence of a runner system allows for more complex and intricate part designs, as there are no limitations imposed by the need for a separate runner. This opens up possibilities for innovative and creative designs that would not be feasible with cold runner molding. Additionally, hot runner systems can be easily customized and adjusted to accommodate different part geometries and materials.
While the initial investment cost of hot runner systems may be higher compared to cold runner systems, the long-term cost savings make it a worthwhile investment. The reduction in waste material, improved part quality, faster cycle times, and increased design flexibility all contribute to overall cost savings in terms of material costs, labor costs, and production efficiency. Additionally, the ability to reuse or recycle the excess plastic material from hot runner systems further reduces costs and environmental impact.
Components of Hot Runner Plastic injection molding System
A hot runner plastic injection molding system consists of several key components that work together to deliver molten plastic to the mold cavity’. These components include the nozzle, manifold, hot runner controller, temperature sensors, thermocouples, and heaters.
The nozzle is responsible for delivering the molten plastic from the injection unit into the mold cavity’. It is designed to withstand high temperatures and pressures and is typically made from materials such as stainless steel or heat-resistant alloys. The nozzle is heated to maintain the plastic material in a molten state as it flows through the system.
The manifold is a distribution system that connects the nozzle to multiple mold cavities. It ensures that the molten plastic is evenly distributed to each cavity, allowing for consistent part filling. The manifold is also heated to maintain the desired temperature of the plastic material.
The hot runner controller is a device that controls and monitors the temperature of the hot runner system. It regulates the heating elements in the nozzle and manifold to ensure that the plastic material remains at the optimal temperature throughout the molding process. The controller also provides feedback on temperature variations and alerts the operator of any abnormalities.
Temperature sensors and thermocouples are used to measure and monitor the temperature of the hot runner system. They are strategically placed at various points along the system to ensure accurate temperature control. The data collected by these sensors is relayed to the hot runner controller for analysis and adjustment.
Types of Hot Runner Plastic injection molding Systems
There are several types of hot runner plastic injection molding systems available, each with its own unique features and advantages. The choice of system depends on factors such as part design, material requirements, production volume, and budget. Some of the commonly used types of hot runner systems include valve gate hot runners, open gate hot runners, insulated hot runners, and sequential valve gate hot runners.
Valve gate hot runners are widely used in applications where precise control over gate opening and closing is required. They consist of a valve pin that controls the flow of molten plastic into the mold cavity’. When the mold is closed, the valve pin seals the gate, preventing any plastic material from flowing. When the mold opens, the valve pin retracts, allowing the plastic material to flow into the cavity. This type of system offers excellent gate control, resulting in high-quality parts with minimal gate vestige.
Open gate hot runners are a simpler and more cost-effective option compared to valve gate hot runners. They consist of a single gate that is open throughout the molding process. The molten plastic flows directly from the nozzle into the mold cavity’ through the open gate. While open gate hot runners may not offer the same level of gate control as valve gate systems, they are suitable for applications where gate vestige is not a concern.
Insulated hot runners are designed to minimize heat loss and improve energy efficiency. They feature an insulating layer between the manifold and mold plate, which helps to maintain the desired temperature of the plastic material and reduce energy consumption. Insulated hot runners are particularly beneficial for applications that require precise temperature control or involve heat-sensitive materials.
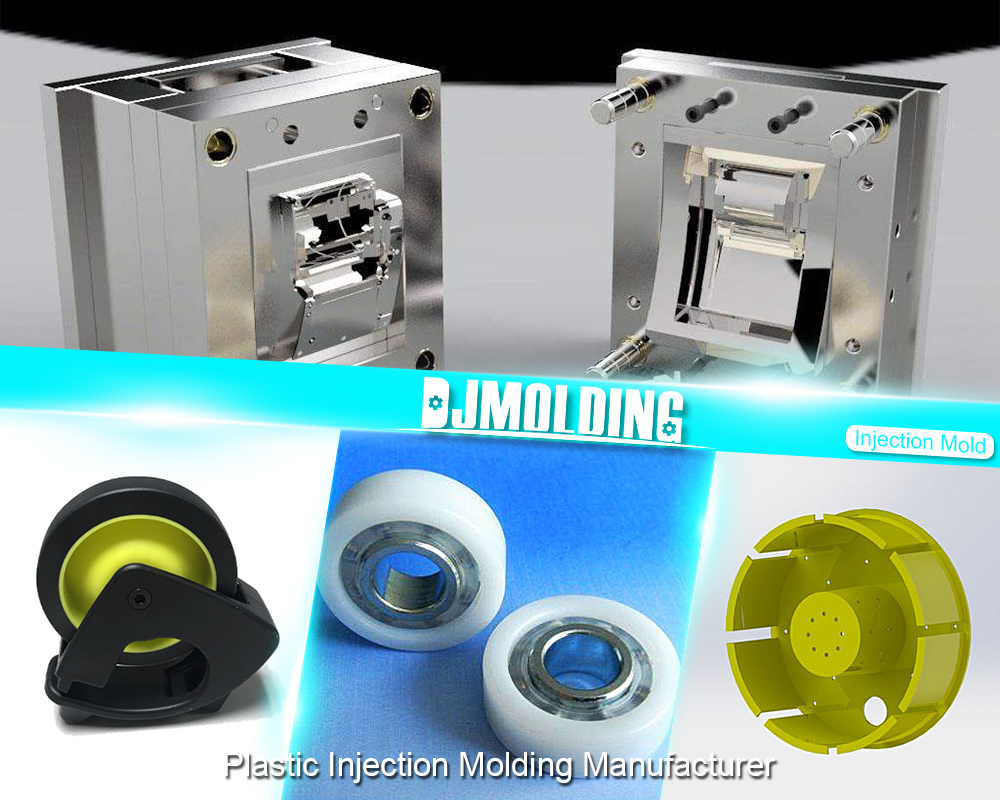
Final Words
When considering hot runner plastic injection molding for your project, it is important to evaluate the cost implications. While the initial investment cost of hot runner systems may be higher compared to cold runner systems, there are several long-term cost savings that make it a worthwhile investment.
The initial investment cost of hot runner systems includes the purchase of the system itself, as well as any customization or integration requirements. The cost can vary significantly depending on factors such as system complexity, brand reputation, and supplier capabilities. It is important to carefully evaluate the cost-benefit ratio and consider long-term cost savings when making a decision.
For more about everything you need to know about hot runner plastic injection molding,you can pay a visit to Djmolding at https://www.djmolding.com/about/ for more info.