7 Things Worth Knowing About Metal Insert Plastic Injection Molding
7 Things Worth Knowing About Metal Insert Plastic Injection Molding
Metal insert plastic injection molding combines the strength and durability of metal with the design flexibility and cost-effectiveness of plastic injection molding. It involves the insertion of metal components, such as threaded inserts or heat-staked inserts, into a plastic mold cavity before the injection molding process takes place. This allows for the creation of complex parts with integrated metal features, resulting in improved functionality and performance.
The history of metal insert plastic injection molding can be traced back to the early 20th century when the first attempts were made to combine metal and plastic in the manufacturing process. However, it wasn’t until the 1950s that significant advancements were made in this field. With the development of new materials and technologies, metal insert plastic injection molding has become a widely used technique in various industries, including automotive, electronics, medical devices, and consumer goods.
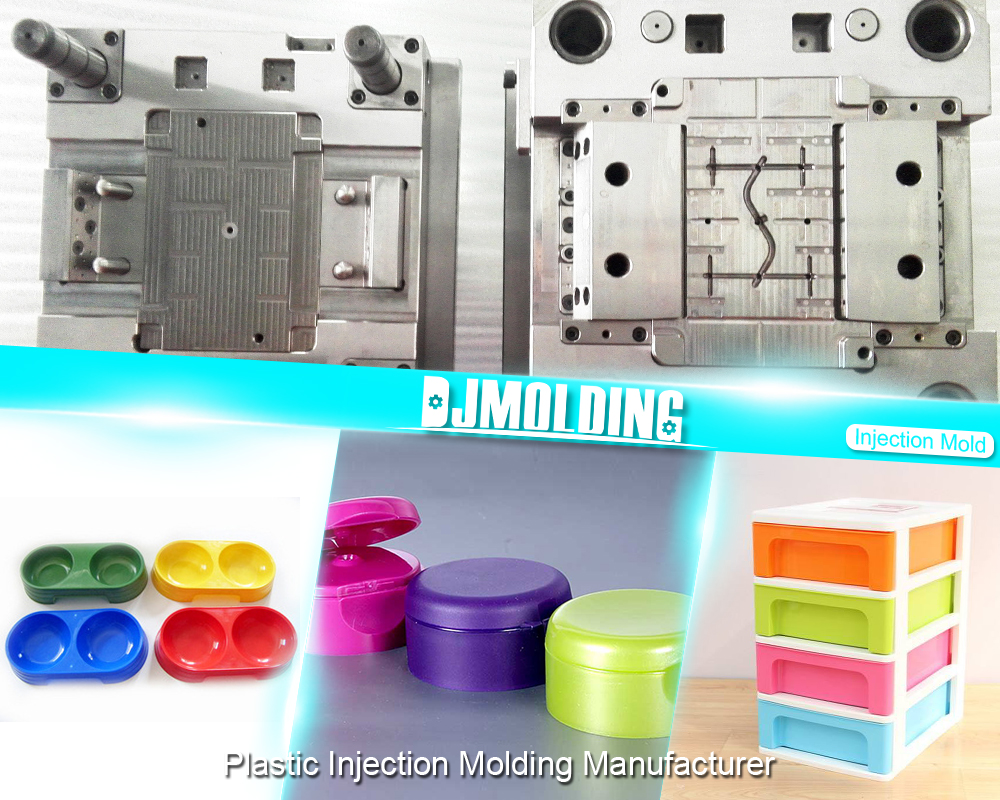
Types of Metal Inserts Used in Injection Molding
There are several types of metal inserts that can be used in metal insert plastic injection molding, depending on the specific requirements of the part and the application. Some common types include threaded inserts, heat-staked inserts, compression inserts, and expansion inserts.
Threaded inserts are commonly used when a plastic part needs to have threaded holes for screws or bolts. These inserts have external threads that allow them to be easily screwed into the plastic during the molding process, providing a secure and reliable connection.
Heat-staked inserts, on the other hand, are used when a plastic part needs to have metal features that are permanently attached. These inserts have a flange or head that is heated and pressed into the plastic, creating a strong bond between the metal and the plastic.
Compression inserts are used when a plastic part needs to have metal features that can be easily removed or replaced. These inserts have a compressible design that allows them to be inserted into the plastic during the molding process and then expanded to create a tight fit.
Design Considerations
When designing parts for metal insert plastic injection molding, there are several important considerations to keep in mind to ensure successful and efficient production.
One key consideration is wall thickness. It is important to maintain uniform wall thickness throughout the part to ensure proper flow of molten plastic during the injection molding process. Uneven wall thickness can result in defects such as sink marks or warpage.
Insert placement is another critical factor to consider. The location and orientation of metal inserts within the mold cavity can affect the overall strength and functionality of the part. Careful consideration should be given to the placement of inserts to ensure proper alignment and fit.
Undercuts are another design consideration for metal insert plastic injection molding. Undercuts are features that prevent the part from being easily ejected from the mold. Special design techniques, such as side actions or collapsible cores, may be required to accommodate undercuts in the part design.
Materials Used in Metal Insert Plastic Injection Molding
In metal insert plastic injection molding, a wide range of materials can be used, including thermoplastics, metals, and composites.
Thermoplastics are the most commonly used materials in metal insert plastic injection molding due to their excellent molding properties and versatility. They can be easily melted and molded into complex shapes, making them ideal for a wide range of applications. Some common thermoplastics used in metal insert plastic injection molding include ABS, polycarbonate, nylon, and polypropylene.
Metals can also be used as inserts in metal insert plastic injection molding. Metal inserts provide additional strength and durability to plastic parts, making them suitable for applications that require high mechanical performance. Common metals used as inserts include stainless steel, brass, and aluminum.
The Injection Molding Process for Metal Inserts
The metal insert plastic injection molding process involves several steps, including mold design and fabrication, insert placement and fixation, the injection molding process itself, and post-molding operations.
The first step in the process is mold design and fabrication. A mold is designed to accommodate the metal inserts and the desired plastic part geometry. The mold is then fabricated using precision machining techniques to ensure accuracy and quality.
Once the mold is ready, the metal inserts are placed and fixed in the mold cavity. This can be done manually or with the help of automation tools, depending on the complexity of the part and the production requirements.
The injection molding process begins with the heating and melting of the thermoplastic material. The molten plastic is then injected into the mold cavity under high pressure, filling all the cavities and creating the desired shape.
Quality Control Measures
Quality control is a critical aspect of metal insert plastic injection molding to ensure that parts meet the required specifications and performance standards. Several quality control measures can be implemented throughout the manufacturing process.
Statistical process control (SPC) techniques can also be used to monitor and control the injection molding process. SPC involves collecting data during production and analyzing it to identify any variations or trends that may affect product quality. By monitoring key process parameters, manufacturers can make adjustments in real-time to ensure consistent quality.
ISO certification is another quality control measure that manufacturers can obtain to demonstrate their commitment to quality management systems. ISO certification provides assurance that a company follows internationally recognized standards and practices, ensuring consistent quality and customer satisfaction.
Cost Considerations
When considering metal insert plastic injection molding for a project, several cost factors should be taken into account.
Tooling costs are one of the primary cost considerations. The design and fabrication of molds can be expensive, especially for complex parts or large production volumes. However, tooling costs can be offset by the benefits of metal insert plastic injection molding, such as improved strength and reduced assembly time.
Material costs are another important consideration. The choice of materials can significantly impact the overall cost of the project. Thermoplastics are generally more cost-effective than metals or composites, but the specific material selection should be based on the part’s requirements and performance needs.
Applications of Metal Insert Plastic Injection Molding
Metal insert plastic injection molding has a wide range of applications across various industries.
In the automotive industry, metal insert plastic injection molding is used to manufacture components such as interior trim panels, door handles, and dashboard controls. The integration of metal inserts provides enhanced strength and durability, ensuring long-lasting performance in demanding automotive environments.
In the electronics industry, metal insert plastic injection molding is used to produce parts such as connectors, switches, and housings for electronic devices. The ability to incorporate metal features directly into plastic parts allows for improved electrical conductivity and mechanical stability.
In the medical device industry, metal insert plastic injection molding is used to manufacture components such as surgical instruments, drug delivery devices, and implantable devices. The combination of metal and plastic allows for the creation of complex parts with integrated functionality, meeting the stringent requirements of the medical field.
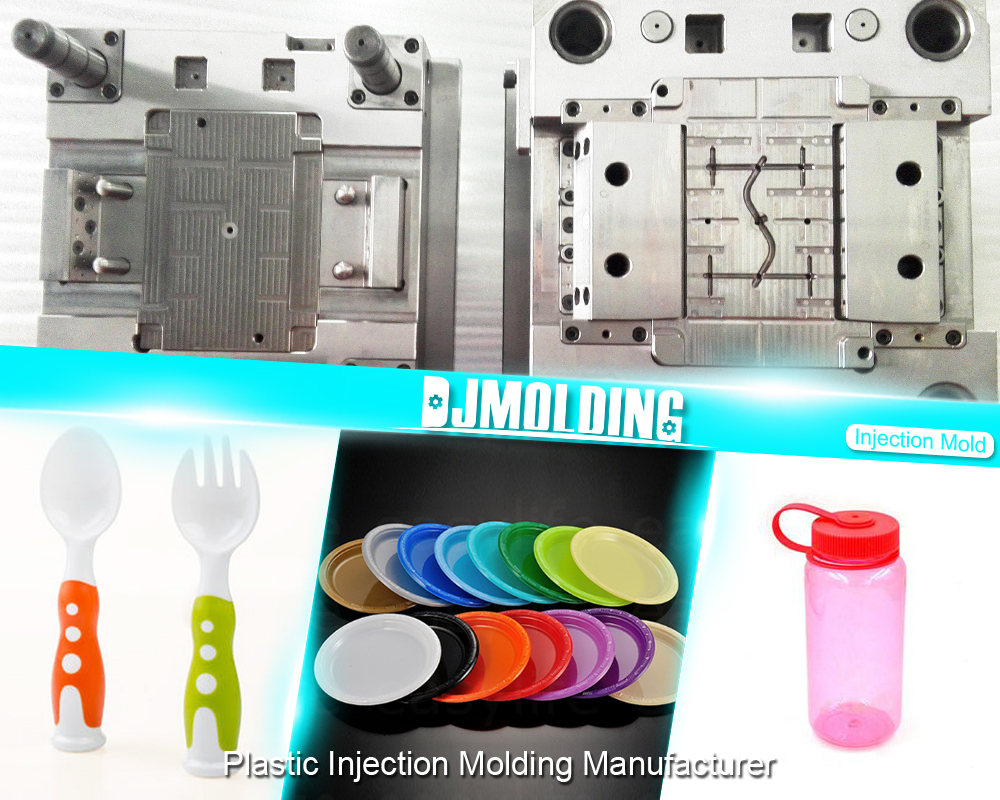
Is Metal Insert Plastic Injection Molding Right for Your Project?
In conclusion, metal insert plastic injection molding is a versatile and cost-effective manufacturing process that offers numerous advantages for a wide range of applications. By carefully considering the specific requirements of your project and weighing the benefits and limitations of metal insert plastic injection molding, you can make an informed decision on whether it is the right choice for your manufacturing needs.
For more about 7 things worth knowing about metal insert plastic injection molding,you can pay a visit to Djmolding at https://www.djmolding.com/insert-injection-molding/ for more info.